Introduction: Vintage Hoyle Official Game "X" Puzzler Recreation
Hi all, I’ve been collecting various puzzles over the years. Specifically wood puzzles. One particular series of wood puzzles, or Puzzlers as they were called, was released or issued by Hoyle back in 1964. My father had a couple of these that were passed on to me. To be honest I can’t remember which ones I had first. But I started searching and collecting these since around the early 1980s.
Mind you I didn’t go deep in search for them, just would buy one here or there when I found one. It wasn’t until Covid hit that I really went down the rabbit hole searching for others and trying to learn more about these unique and quite a few extremely rare puzzlers, not to mention impossibly hard to find. (See History) At some point I realized I can recreate the ones I am missing, or that have proven impossible to find. This Instructable will detail my efforts to recreate the missing “X” puzzle.
Supplies
- Wood (Walnut in this case)
- Lemon Oil w Beeswax*
- Rubber gloves
- Qtips
- Cheesecloth
- Sand paper (various grits)
- Miter saw
- Drill Press
- Digital Caliper
- Painters tape
- 32/64” Brad Point Drill bit
- Cone Shaped Dremel Sanding Stone
- Bench Sander
- Palm Sander
- Adobe Illustrator
LINSEED OIL(DON'T USE)
Step 1: Background Research & History
The history on these puzzlers is hard to come by. There is very little information about them on the internet, with the exception of a couple puzzle dedicated websites. The search for info is also hampered by the fact that two of the three companies that collaborated to make these puzzles are no longer in business (at least in the capacity for having any actual reference). The collection I have was published or released by Hoyle under the title of “Hoyle Official Games”.
There were two other companies involved with their manufacturing. Stancraft Products (who I assume but haven’t been able to verify) made the actual boards. Neither Hoyle or Stancraft Products are in business. Setko who made the metal pegs (in various finishes, Silver, Gold, Copper, Black) is out of Chicago area. As it turns out Setko founder and president Calvin O. Brown was the one responsible for designing, patenting, & copyrighting the majority of these puzzlers. Setko is still in business. I reached out to them, but they unfortunately had little information about the puzzles themselves. They only had a few actual puzzles they still in their inventory. I was actually able to help them with the info I had collected and work with them to recreate one of the puzzlers for their company (but more on that later).
Originally I had collected 11 of the Hoyle Puzzlers, thinking that was all there were. (CrissCross, Tri, Reversal, 3Square, Double Diamond, Bullseye, Kan-Yu, ZigZag, Mill Game, Why, Fore & Aft). But when I actually started examining them more closely I realized there were quite a few more, another 7 in fact. Setko had earlier versions of most of these that were released under the Setko name exclusively in smaller boxes. Some of the other puzzle titles they had were Bullseye II, “X”, Pyramid, Arrow, 8 Men on a Raft (Desk Pen Set), MatchHeads (no peg puzzle), Setko Scramble(Pegs with stamped S E T K O, that had to be rearranged to spell out the word properly). Also there were two puzzles designed and patented by Mr. Brown that were never actually made, deemed the Lost Puzzles. So quite a variety.
Step 2: Replicating the “X” Design Pattern
Taking measurements from one of my existing puzzles the game board is roughly 5.5” x 5.5” square and little over a 1/2” thick. Using these dimensions I laid out a grid in Illustrator to recreate the pattern. To accomplish this I found a existing pic of the puzzle board, then placing it on a base layer locking it down. I then drew a circle matching the width of existing pegs (1/4”). I then cloned the circle repositioning it over and over in the rough pic position of the pegs.
After having all the circles in place I used my alignment tool to get each row or column to line up evenly. As well as spacing out the holes to fit nicely on the board. After I was happy with the look, I selected all the holes which displays the actual center of each hole when selected. I then took a screen grab of the selection. Then placed the grabbed image in position over the original holes. By doing this it gives me an actual drill point for my drill bit.
Step 3: Cutting Wood and Drill Prep
I ended up using an old walnut table leaf that no longer has a table to be used in. The leaf was larger than I needed but perfect thickness. I cut the board down using my miter saw to be exactly 5.5” square. Once cut down I 80 grit sanded down the all sides using my bench sander. Next step drill the holes.
Before drilling I apply painters tape to the surface for cleaner drill holes. I then took my laser print out template for the “X” and using painters tape attached it to the surface of the board (choosing the side with the best wood grain look for the face of the puzzler). I first measured the depth of one of the pegs I have (.6mm).
I setup my drill press palette, then with the board on it I set my drill depth gauge to be deep enough that the pegs will comfortably seat in the drilled holes. I then carefully drilled each hole making sure the tip of my drill bit was striking the center of the hole indicated on the laser print. Now drill bit types can drastically affect the smoothness of the holes. I’ve found that brad point drill bit is best for the job.
Step 4: Board Clean Up and Finishing
After all the holes have been drilled, carefully remove template and painters tape. At this point I used my palm sander with a higher grit of 120 or 200 to go over the face to smooth off any burrs left after drilling. Now depending on the quality of your wood you may have some stubborn burrs that sanding won’t remove. I’ve found using a Dremel cone shaped sanding stone to spin in the openings by hand (not the actual Dremel tool) to smooth them out. I also used my palm sander to soften the sharp square edges of the entire wood puzzle block.
Once I was happy with the overall smoothness I applied a coat of lemon oil with beeswax to the entire board using cheese cloth. Let sit for about 30 mins then wipe off excess, again with cheese cloth (this prevents it from getting a gummy feeling). I let rest for 24 hours (at least or longer) then gave it another overall coat. I used a Qtips to swab the holes to make sure they were coated as well. Repeat wipe down process, let dry but this time I place face down on a couple paper towels to allow any excess in the holes to drain out.
Step 5: Essentially Done… However.
For all intensive purposes the puzzle is done. I used left over pegs from duplicate puzzles I had collected. I used my digital caliper to measure one of the existing pegs to create a 3D version. This way you can print your own pegs, since you probably won’t have access to extras like I do. It could be fun, especially doing different color combos, to create puzzle variations. I’ve included a Pegs.stl file for the pegs if you don’t have access to the original pegs.
Another history note: Setko, who was responsible for creating the solid metal pegs, is a screw fastener manufacturer and a lot of their earlier puzzles used just that, head screws of various types of heads (slotted, phillips, hex, etc). Some were threaded fasteners as well.
Attachments
Step 6: Has to Match My Existing Collection….
As I mentioned earlier, my original collection was just 11. It turns out each Puzzler had a unique model number issued by Stancraft Products (again assuming it was Stancraft who issued them as they appeared above their logo). The sequential numbers starting with Criss Cross was #8101 thru to the Mill Game #8109. Then I have two missing numbers with Fore & Aft #8112 being the last number I originally had. So at this point I’m making an educated guess that the “X” puzzle would be #8110 (but again I’ve been unable to confirm if that’s the case, or if Hoyle ever even produced the “X” puzzler). I only know Setko produced it. I have the Why puzzler in the original Hoyle case but no verification as to what its actual model number is since the instruction card was missing (So again my educated guess would be #8111). SO if anyone out there knows anything about these two puzzles and or others please let me know!!!!
Anyway, I decided to produce a box to match my other Hoyle Puzzler slipcases. I set about having my coworker help me design the structure. I replicated the art to match the existing designs. Rather than bore you with all the details for making the art and actual case, I’ll just share that I did the photography to match the look of the previous cartons which all have a staged photo of the puzzle being played. You’ll notice that the photos on each box all harken back to the 60s, which is understandable since the majority were released in 1964. My companies lobby is stuck in the 60s so it was the perfect setting to stage the cover pic. After having the board made and the pegs placed I simply had a coworker be my hand model for the shot.
The original slipcases had plastic inserts to hold the square puzzle boards in place in the slipcovers. I recreated a paperboard holder for my mine as well. I printed out the art and married it to the slipcase structure. I personally feel it is hard to distinguished that it doesn’t belong. After the success of doing this I was inspired to recreate two other extremely rare games from the Hoyle Collection, Odd or Even #8113, and Castile #8116. The last four in the know collection aren’t puzzles, but are games requiring two players. These 4 were created by design Sid Jackson and were released in the early 70s.
I also recreated the directions card which can usually be found with a lot of the original puzzlers that was printed on card stock.
I've included an EPS of the cad file for the slip case structure and insert.
Attachments
Step 7: Mass Production
It was because of my creation of this “X” puzzler I started creating puzzles for Setko who still owns the copyrights. After speaking with them to gather information about their puzzles, I mentioned and showed them my collection. They inquired if I'd be willing to recreate some of their puzzles for them. The first one I did for them is a recreation of the 3 Square puzzler #8104. They asked me to do 50 for them, plus laser engrave their logo on the front and sequentially number each 1/50 on the back (See Videos). They are using them as corporate incentive gifts, as well as Christmas gifts. It was a challenge to mass produce so many. Not to mention learning how to use a laser engraver. Plus a horrible lesson and consequence on using Linseed Oil instead of Lemon Oil with Beeswax. (See WARNING!!!)
Almost forgot I created a mini version with a smaller piece of scrap wood. And found smaller shelf pegs to use with it.
I hope you enjoyed this Instructable and that it inspires you to recreate something you love.
Step 8: WARNING!!!!
WARNING!!! I highly recommend NOT using Linseed oil, in that if not treated properly, or with extreme caution, can be quite hazardous. Rags, towels and even brushes that have been used with Linseed oil can and will spontaneously combust in to flames, if not disposed of properly, which I didn't resulting in a fire and damage in my basement.
So BE WARNED!! See pic of one of my Instructables Pumpkin lights that were lost, also lost my Floating Skull Specter Light destroyed in the fire. I was very very lucky, it could have been so much much worst. So now I'm faced with a $7K restoration project.
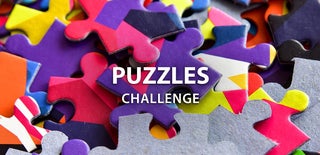
Second Prize in the
Puzzles Challenge