Introduction: Water Cool a 3D Printer Nozzle for Cheap and Easy!
On a 3D printer, the job of the nozzle is mainly to heat plastic. So why would you need to cool it?
Well, active cooling on a nozzle is essential, because if you indeed need to heat the plastic, you only want to melt it at the very spot where it goes out of the nozzle. If it stays hot too long after being extruded, then you'll end up with poor quality prints, but if it gets hot too far inside the nozzle, then there is a big chance that your nozzle will clog up at some point, ruining the beautiful print that you launched 20 hours ago, which is not good for your 3D printer's health because there is a pretty good chance that you'll want to smash it with a sledgehammer, running it over back and forth with your car and finishing it in your barbecue. So as you can see, it is obviously essential to have decent cooling, mainly to increase your printer's life time.
But why would it clog? well, this is a very good question, so I'll try to explain it:
-First, your extruder will push the filament down to your nozzle, through a tube
-While doing so, your nozzle heating block will do its job, which is to reach a sufficient temperature to melt the filament. So as you can understand, there is a spot where the filament goes from solid to semi liquid/liquid. Getting this spot right is the key. You don't want it too low in the nozzle, otherwise the plastic won't flow freely, but you absolutely don't want it too high, otherwise you'll end up with issues that will be explained here-under
-At this point, the plastic will flow through the nozzle, since it is continuously pushed by the hard part plastic coming behind it. If, like me, you are familiar with the use of hard drugs, you can think of a syringe here since it is basically the same principle**. The piston of the syringe here will be the spot where the filament turns from solid to liquid. This piston exists because at this spot the plastic oscillates permanently from liquid to solid, ensuring a both hermetic and solid fit.
-If you don't have enough cooling, what will happen is that this spot will progressively move up. and at some point, it will simply come out of the inner tube which directs it to the nozzle. Then, you can easily understand why it clogs up.
-What can happen also is that it will clog up during a retraction: when retracting, the extruder will pull the filament up, so the melted part will go up, and if it is not cooled fast enough, then it will progressively goes up and up in the nozzle. If you have several quick retractions in a brief amount of time, it might end up going out of the tube, and clog. As you can understand here, the likeliness of this issue to happen will largely depend on each print, as well as parameters like oustide weather conditions, prime/retract speeds and accelerations, extrusion overal speed, nozzle diameter, etc.
So, as you can see, this issue can be quite vicious, since it doesn't necessarily happen all the time, for instance, if you're running your printer in cold winter, you might never have this problem. But maybe you'll run the very same print in summer and be puzzled about "why the hell wouldn't it work anymore, I printed this part just fine few months ago, those 3D printers from China are crap, I want a full refund of the 50 bucks I paid for it"
**Don't do drugs, drugs are bad, M'kay?
Step 1: Step 2: Watercooling? That Sounds Expensive, Dude
Well, I would lie if I said that it is the same price as air cooling, obviously. But my method is so cheap that is is pretty much affordable by anyone.
The only "expensive" part will be the pump. And if you wish, you can find water pumps for less than a couple bucks. Depending on your cheapness, I believe that this system can be build for 10 american pesos, purchasing all the components. Kind of hard to do cheaper, right?
You'll need:
-An E3Dv6 nozzle or equivalent, but you probably already have one on your printer, no need to buy a new one since the mod is 100% reversible
-two O-rings, diameter 20
-about 4cm of 25 diameter silicon tubing. Mine came from a motorbike.
-a few air pressure quick release fittings (mine are 4mm diameter)
-a water pump. You don't want a crazy pump with a lot of pressure, just the most basic stuff. Too much pressure won't work anyway, you'll end up having leaks. basically, any el cheapo 12V water pump will do the trick. There is no need to have a lot of water flow actually, the water will barely get warm even at very low feed
-A water tank: at first I was simply using a plastic bottle. If you wish to get fancier, like I did, there are some water pumps which include water tanks designed for computer cooling, works perfectly
-Some pfte air pressure tubing
-A few cable ties
-Of course, beers.
My setup cost me 14 Dollars. The computer pump including the tank was 10 dollars, 1 dollar for the tubing and the rest for the fittings.
As you can see, the BOM is pretty simple and pretty cheap. Most of the cost will come from beers, as you really don't want to cut costs on this matter.
Step 2: Step 3: Install O-rings and Tube
First, remove your nozzle from your printer.
Cut the Silicon tube to the appropriate dimensions: it should go about one or two millimeters down the lowest point of the heatsink, and one or two millimeters above the heastink. So, basically, if my math is correct, you should cut it 2-4mm bigger in total (please chech this with your local math specialist).
Put one O-ring between the two lowest veins of the heatsink. Just put it there, you absolutely dont want to squish it inside or put any pressure to it.
Do the very same thing for the top.
Finally, put the heat sink in your silicon tube, but again, be careful not to apply pressure on your O-rings.
Step 3: Step 4: Finish the Nozzle Upgrade
Carefully drill two holes in your Silicon tube. For that, my method was to first use the drill with a 2mm drill bit, then heat a 2mm screwdriver and pass it through the hole to clean it a bit.
Screw directly your air pressure coupling fittings in these holes. It actually holds fine and will remain watertight. I didn't glue them or anything, I've just screwed them into the tube and it works perfectly on my machine for about half a year now. The inlet should be at the bottom, as the bottom is the part of the heat sink where you want maximum cooling efficiency. The outlet can then be put on top. You can drill the holes anywhere in the tube so that it is convenient for you to install on your machine and that it won't mess up your other part cooling fans, probes, etc.
Then, secure it in place with 2 zip ties, one on each O-ring. Here again, do not tighten the zip ties too much. This is not a contest about being the strongest man on Earth here, so just relax. Thing is, if you tighten the zip ties too much, the O-ring will get inside the heatsink and you'll end up having leaks.
Once done, I suggest that you put your nozzle aside and don't reinstall it on the printer right away, because you'll need to check for leaks first.
Step 4: Step 5: Build the Water Circulation System
Ok, so now you have your nozzle, you just have to feed it with water.
So, to do that, you'll need a pump and a tank. The tank has two purposes: store water, obviously, and act as a radiator/damping system. You actually don't need a real radiator, I tested my machine for hours and the tank never even got warm, so don't waste money on that and save it to write me a check instead.
First thing, find a nice spot for your pump and tank.
Once done, cut appropriate lengths of PFTE tubing. In some cases, you may need the tube to turn on a short radius, but PFTE tubing is a bit too rigid for that. The solution is to carefully heat it with a lighter, an air gun or a thermonuclear reactor, and to very slightly bend it. Repeat this operation many times until you end up with the appropriate angle. You absolutely don't want to do it in one time, otherwise there is a good chance that your tube internal diameter will be messed up, or that you'll heat it too much, in which case it will make tiny bubbles and won't be watertight anymore. So take your time here.
Install your coupler in the pump.
Then plug everything following this pattern: Pump out --> nozzle in --> nozzle out --> water tank in -->water tank out --> pump in.
This way, the water pump will receive the coolest possible water, which will increase its longevity.
So, now, connect your pump to your favorite 12V power supply and check if everything is watertight. If it isn't, it means that you probably screwed up somewhere, no need to put a chewing gum to try to fix the leak, just restart and do things properly.
First time I tried, I had a leak, it was coming from me having pushed the O-ring too tight. After re-installing the O-ring properly, I had another leak: one of my tubes coming from the nozzle to the tank was clogged, due to me having screwed up bending the tube like a moron, the pressure was building into the nozzle and it ended up leaking everywhere. I fixed this tube and then, all good!
If you've done things properly, it shouldn't leak at all. I know it seems unlikely due to the easy construction of this device, but after half a year of use I had no problem whatsoever. It only leaked once, but that was because the hot end smashed into another printed object because I made a mistake when creating the Gcode, it never leaked in normal condition.
Step 5: Step 4: Time to Print!
Ok, now just reinstall your nozzle. One important thing to keep in mind is that the two fittings that are screwed on the silicon tube cannot support much load. So you absolutely have to attach the tubes in a way that they will never apply efforts to the nozzle, no matter where the print head is. That's critical, because otherwise, if they detach, you'll end up having your 3D printer swimming, which is probably not the best thing.
Re-install your part cooling fans, re-plug everything.
Don't forget to plug your waterpump, you can plug it wherever the original fan was plugged, I recommend to plug it directly on your power supply unit if it is a 12V one, this way it is always on.
Now, try a a few print, you should'nt have any clogging issue anymore (well, as long as you keep using clean filaments)
Actually, at first, my idea was to build a cooling system out of metal. I wasn't sure at that time that watercooling would be effective to solve my issues, so I wanted to try a quick and dirty solution to see if this would be useful. I made this with the few things I had laying around in my shop and I thought I would replace it if this proved to be effective. Turns out, since it was both very effective and reliable, I never felt the need to build a more complicated system.
Step 6: Why Did I Decide to Do That and When Is Is Critical?
In my case, I had to do this because I was using a big nozzle to print giant things quickly.
So, in order to do that, I had to crank up the printing temperature, to keep a decent flow speed while allowing the extruder motor to keep up. So, the original fan was not enough and I ended up having clogging issues, especially during multiple retractions or very long travel distances.
For some materials, reaching very high temperatures is a must, in which case it is likely that the fan cooling system won't be able to keep up, compromising the parts that keep it in place. In which case watercooling becomes almost mandatory.
Generally, if you sometimes had your printer clog up and you didn't know why, it is possible that this was the cause. At least with a watercooled system you don't have to worry anymore about these kind of issues, as long as your filament stays clean (use a simple filament filter for this), you really shouldn't having clogging issues anymore.
For big nozzles, I think this is also a must if you want a reliable and fast setting. You can probably live without it if you print slowly, but them what's the point of having a big nozzle?
Anyways, this was a fun and easy project which made my printer way more reliable. I actually didn't have any failed print after installing this feature, while I had quite a bit before. So, yeah, it is possible to have a watercooled print head, without spending hundred of dollars or having incredible kung-fu master metal brazing skills to create a fancy heatsink, I hope this idea will inspire some of you and that it can be put to good use. I hereby decline any responsibility if anyone uses this technique for evil. Evil is bad.
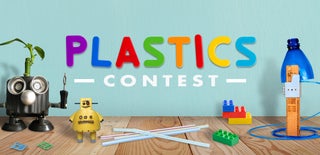
Participated in the
Plastics Contest
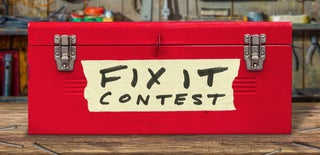
Participated in the
Fix It Contest
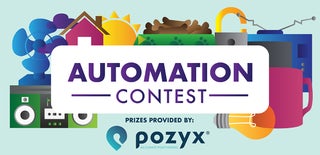
Participated in the
Automation Contest 2017