Introduction: What's Old Is New - Fixing an Old Wood Lathe With a Variable Frequency Drive
Cool story... about nine years ago a friend of mine decided to become a pastor, quick the wood working biz, and move to Tennessee. Okay, that's not really the cool part for me, although he still is enjoying his new profession. The cool part for me was that before he left he offered me a lathe that had been camping out in his garage for 20+ years. He told me that the lathe had some history behind it; it once belonged to Tage Frid when he worked at the Rhode Island School of Design. As the story goes, Mr. Frid had found an old metal working lathe at RISD that he wanted to convert into a wood turning lathe. My guess is that there was some reasoning for the conversion; maybe the gear-driven banjo, maybe the massive weight of the lathe to help damper large pieces, maybe it was just there and he wanted a lathe. Whatever the case, my friend, who apprenticed under Garrett Hack, inherited the lathe from Mr. Hack but never got it up and running in his shop, and that is how it ended up in my shop.
When I received the lathe it was in parts and pieces and the condition of the motor was unknown by my friend. The lathe is probably something from the 20s and had been modified to a certain extent so that it could be used as a woodturning lathe. Its tenure in the garage allowed it to develop a nice rusty patina and a frozen banjo (the part you will move to your work and your tools will rest on while cutting). The motor, a tri-clad 1-1/2 HP GE, looked to be in working order since its arbor wasn't seized and there were no odd noises when I turned it. So, with my flap wheels, sanders, wire brushes, and Rustoleum I set about restoring the lathe. I did not record this process, and there really wasn't much to it. Get rid of the rust, lube up the moving parts, and finish it with a nice "tool-gray" Rustoleum paint. Then, when I had everything cleaned up and and ready to roll (or spin), I went about running a new line for the motor, installing an ON/OFF toggle switch and wiring the motor. Lo and behold the ancient motor ran fantastic. The only problem I was running into was that it was really tough to change the speed the lathe was spinning. I ended up attaching a board to the shop floor and mounted the motor on to a large oak plank attached to the board by hinges. This allowed me to move the belt on the motor arbor and lathe headstock so that I could change speeds. This helped a bit, but with larger pieces the lathe was still prone to vibrating since I could not slow down the lathe enough. This led to my first big fix...
Step 1: The First VFD
After a lot of research I decided that there were two directions I could take:
1 - Find a DC motor and an inverter to run alternating current to the direct current motor
2 - Find a 3-phase motor and a variable frequency drive (VFD) and run single phase electricity to the VFD allowing it to convert it to three phase heading to the motor
I found that the DC motor route was way too cost prohibitive for what I was looking for and I ended up finding a great deal on a motor and VFD package at www.dealerselectric.com. I ended up sticking with a 1-1/2 HP motor and a compatible 2 HP VFD.
Set up was pretty easy. I mounted the new motor to the hinged board that my first motor was attached to and properly tensioned the belt on the lathe's headstock. I put the VFD in a somewhat vented tool box that I attached to a wall adjacent to the lathe. The manual that comes with the VFD was relatively straight forward and the basic gist of the it is to run a single phase 220v line to the VFD from the electrical box. That line then runs from the VFD to the motor but it is now a three phase frequency. From there I needed to run a couple of digital inputs for my switch, which is all "explained" in the manual. I'll go into more detail about digital inputs later on in this instructable.
All in all this set up worked great. I was able to control the speed of my lathe by turning a dial on the VFD and I could easily turn larger pieces without significant vibrations. What I was running into was that the swing for my lathe (the distance from the center of the headstock to the lathe bed) was too short to turn any pieces with a substantial diameter and I was going to need a more powerful motor and VFD to turn those pieces. I used the 1-1/2 HP motor and VFD set up for about three years but I knew it was time to upgrade since I was selling a number of my pieces and I wanted to turn larger salad bowls. The final decision came when I tried turning a 70 pound piece of oak that was freshly felled. Although, I was able to turn the bowl, the motor was prone to stalling out on me (the VFD has a number of parameters that protects both it and the motor). At the end of turning the bowl the motor was too hot to touch and my decision was made. I figured that while I was at it I could do some additional upgrades and fixes to help improve the flow of my turning experience. I thought that I would share the ways I outfitted and upgraded my lathe so that anyone else interested in taking an older non-variable speed lathe and making it variable speed could do it successfully.
Step 2: Making It Safe...r
As you can see in the first picture, my headstock's pulleys were fully exposed when I first refinished the lathe. This seemed to be the norm when the lathe was first reengineered to be a wood turning lathe and it is scary as all heck to have spinning pulleys right near your arm as you are trying to concentrate on the bowl or spindle you are turning. When I first installed the first 1-1/2 HP VFD I decided to prevent a significant and unsightly disaster by putting on a shield to prevent the pulleys from being exposed. A friend of mine worked at a auto body shop and said that he could quickly weld up some scrap steel to make a guard I could attach to the headstock. We took some measurements and made a cardboard template and he made that week. I painted it the same gray as the lathe and then drilled a hole in the top to line up with the lock bushing that I used to lock the headstock in place with a steel rod. I use a bunch of rare earth magnets on the guard to hold my calipers, rulers, and toggles for the scrolling three-jaw chucks I use to hold my work. I also added an old desk lamp that someone was throwing out as a flexible lighting source that I can focus on my work, especially as the walls of bowls get thinner.
Step 3: Increasing the Swing
I had mentioned earlier that I wanted to increase the swing of my lathe to allow me to turn larger pieces of work. Although, I was able to turn bowls with a decent diameter before (16") I wanted to turn bowls with a large enough diameter to set them apart from typical bowls. I do have an off board side to my headstock but need to find the proper faceplate adapters to use my chucks with the threads on that end... they are massive and I have yet to find a good fit.
A friend of mine works at a metal working shop and said that he would be more than happy to help me out. He said that there was a canceled job with some thick aluminum stock that he could use to make some risers for both my headstock and tailstock. As a bonus, my tailstock was WAY out of alignment with the headstock, like four millimeters out of alignment (sorry for the cringe factor for you turners out there). He was able to design the risers so that they realigned the tailstock and headstock neatly all the while giving me an additional 3-1/2" of swing. I can now turn bowls with a 22" diameter right on the bedside of my lathe and the tailstock and headstock are perfectly aligned!
Step 4: Breathing Clear - Getting Rid of the Dust
Another upgrade I made from my original lathe was adding a dust collection system to both collect dust while sanding and to collect the shavings that are tough to reach with the broom. I had already plumbed (is that the right word for this?) a dust collection system throughout my shop so I just extended the system to the lathe and at the end of it added a splitter so that I could have two different hoses. One hose is a flexible dryer hose that does a nice job holding its place while I am sanding (although it does rip and wear out over time). The other hose is a large vinyl hose that I use to collect the stuff on top of the lathe bed and on the floor. The system does a fantastic job collecting dust while I am sanding and I also run an air cleaner while I run the dust collector. Gotta keep those lungs healthy!
Step 5: Keeping Your Tools at Hand
With woodturning you end up using a lot of different tools, often for the same project. This holds true for turning bowls but it even holds more true for turning spindles with various ornamentation and designs. I have either purchased or inherited a number of turning tools and I like to keep them at hand and accessible while I am turning. My main tools I keep on a rack I built directly behind the lathe using a piece of angle iron connected to the lags holding the lathe to the concrete floor. I then attached a vertical piece of wood to the angle iron that has a perpendicular shelf attached to that with half circles to hold the handles of the tools. The shelf works great to hold my sharpening slipstones, wrench for my tailstock, and the remote for my dust collector.
The wall adjacent to my lathe holds the balance of my lathe tools. I use pieces of 1-1/2" PVC pipe drilled and screwed to the plywood wall to hold the tools neatly in place. Everything else has its place on the wall. Finally, when it comes down to sanding my work, I keep all of my grits of sandpaper in order (80 to 1200) in a wooden bowl. As I go through the grits I stack them up on top of each other (I don't usually start from 80, but typically 120 or 150). Additional tools that are used to remove the chucks and centers on my lather are stored in a small rack attached to the bottom of one of the pedestals.
Step 6: Keep Your Sharpening Stations Close By
With good turning comes good sharpening, and often! I have made it so my grinder is close by and accessible at all times. With just a couple of steps I am at the grinder and can quickly put a new edge on any of my tools. If I don't need to put a new edge on but just touch it up I use the water slipstones that I keep in a watertight plastic container on my tool stand. I have found that I am much less likely to sharpen my tools if they are too far away and there seriously isn't anything nicer than turning a bowl with a nice sharp gouge.
Step 7: Keep Your Stock Nearby... It's a Good Reminder to Turn Another Bowl!
I keep a good majority of my stock located directly near the grinding / sharpening station. This includes both rough blanks and currently drying twice-turned bowls. I think it is a great remainder to come on down and turn something, especially since it is right near the entrance to my shop. I have found that if the blanks are tucked away and you can't see them they are less likely to get turned. Often finding a forgotten blank isn't a bad thing, but since much of my wood is felled and then sealed with anchor seal on the ends it needs to be gotten to sooner rather than later to avoid drying issues (large checks and cracks) that might occur depending on the species.
Step 8: One VFD to Turn Them All!
As I had mentioned earlier, I was having trouble turning large pieces of wood with my 1-1/2 HP motor and VFD, but the results with my first set up were far superior to the initial non-variable speed motor. I was able to find a fantastic deal on a 5 HP three phase motor on Craigslist. I ended up paying $125 for a Lincoln TEFC (totally enclosed fan cooled) motor, which I believe is one heck of a bargain. The VFD I ended up purchasing on Amazon since it was near impossible to find a VFD that would run a 5 HP motor under $800. The VFD I purchased is a Lapond 4KW variable frequency drive and it was $200. It hooked up with my motor similarly to the other VFD and motor combo but this time I wanted to have some auxiliary switches and controls so that I could control the motor without having to access the VFD itself. The manual, and how it is written, is instrumental to programming the VFD so that you can easily have it turn the correct direction, reverse direction when needed, start and stop the lathe, and adjust the speed remotely. The Lapond VFD's manual was written pretty well overall. My motor was spinning counterclockwise once I hooked it up but there was a code that would "change motor direction" and it worked perfectly.
I did end up having to order a new pulley for my motor since its shaft diameter was so much larger than either of the other two motors. I decided to use a 5" pulley with a 1-1/8" bore since it would give me a good gear ratio with the smallest pulley on my headstock at 2-1/2" in diameter. It wasn't necessary to get the ratio perfect since the VFD can honestly compensate for all the speeds I need to turn at.
Step 9: VFD Accessories to Make the Lathe Safer and More Efficient
A Little Window: I was able to use the same old tool box I had used before as my VFD enclosure but since this VFD was so much bigger and generated more heat I had to come up with a better system to vent the box other than a couple of slanted vents. First I cut a square hole in the front of the box so that I could easily see the frequency of the VFD. Although, most lathes will have this shown in RPMs, you learn which frequency works best for each application (ie roughing out a 20" blank I would start at a frequency of 10Hz). I then cut out a small piece of plexiglas and hot glued it from the inside to make a neat little window.
Full of Hot Air: The VFD does generate some good heat and if I was to leave it boxed up in a relatively small space for long I am sure that I would burn it out. I found an old DC computer fan from a discarded computer tower that I thought would work perfectly cooling down the VFD by pulling out the hot air. The VFD has a few DC inputs and outputs but I didn't want to turn on a switch for the fan each time I planned on using the lathe. What I did instead is wired the fan between the 12V DC power supplied by the VFD and the remote switch I will be talking about next. This way when I run the lathe the fan kicks on automatically. To help prevent dust and debris from flying into the fan I used a piece of lightweight row cover (from our garden) and a bungee cord to act as a filter of sorts. Not the prettiest filter but it works great and is really easy to remove and clean.
Switch box: One of the things I was definitely missing from the last motor and VFD was the ability to change the speed of the motor remotely so that I didn't need to leave the box to the VFD open nor reach across the entire lathe to slow things down or speed them up. I was able to find a great switch box for about $28 and I already had a pile of potentiometers and knobs from other projects. I wired the switch box with an emergency stop switch (the big round red one) that will stop the motor almost at once if there is something seriously wrong. I also wired in a reverse-stop-forward rotator switch, which is the main switch for the lathe and the one the fan is connected to. The push-button green switch is for momentary rotation which is great for spinning the lathe just a bit to make pencil marks or look at other parts of the piece that I am turning. The final push-button is a momentary stop (the red one) that I can use to pause my turning or just slow it down (it's kind of like coast when using cruise control). Finally, I had to drill a small hole in the side of the switch box to install my potentiometer, which was wired to the AI or analog input and then programmed to be a remote pot to control the lathe's speed. I used some plastic conduit to keep the wires altogether and long enough so that I could pull the switch box over to where I was turning. I also hot glued some rare earth magnets (I love those things) to the bottom of the switch so that it can stay adhered to the lathe bed without a problem.
Everything at hand: A little but actually significant thing I did was add a little shelf directly behind the lathe on top of the motor mount. I keep my chucks and frequently used attachments on the shelve and it has been such a time saver. Little but really helpful.
Step 10: The Final Product!
All of the updates and fixes have resulted in an efficient, safe, and enjoyable lathe to use. The remote switch has really been a game changer for me and has allowed me to focus more on the turning of the wood instead of the turning of the potentiometer two arm lengths away. The dust collection has kept things cleaner in the shop and in my lungs. The larger motor has been able to handle anything I have thrown at it and I have turned 30 or so bowls with the new motor and VFD and it has not had any overheating issues with the fan built into the enclosure. I have been able to turn some really beautiful bowls just from the wood I have found on my own property and I am looking forward to many more years! If you have any questions do not hesitate to put them in the comments below. Happy turning!
Step 11: New Information and Future Plans
Thanks to comments from the instructables community I have additional ideas on how to add to the versatility of my lathe. As mentioned at the start of this instructable, I do not know the manufacturer of the lathe nor the year it was manufactured. I had originally guessed that it was something from the 1950's, but it seems that I was pretty far off based upon the comments and ideas of a good number of folks. Most seem to guess that it resembles a pattern makers lathe from the 1920's or earlier. I am still on the hunt for more information on the lathe and decided to post it at Old Woodworking Machinery to see if I can fish out even more information.
I have not effectively used the off board turning stand since I need to make some relatively simple modification to it. It is an extremely heavy cast iron stand that came with the lathe and will allow me to turn bowls much larger than my current 23" diameter. Since I increased the height of the headstock by 3-1/2", I need to now increase the height of my tool rest by some measure (I have yet to do the math on this one). This might be as simple as adding a wooden base to the off board tool rest and then using some lift away casters to help move it around more easily. Ultimately, when I do get it working I will have even more options with my turning.
Another future plant that I would like to complete is modifying the original metal working / pattern making tool holder so that it works with the newly lifted headstock and tailstock. This would allow me to create perfect cylinders on the lathe and even more effectively hollow out cylinders if I can design an auxiliary tool rest for the tool bit holder.
They'll happen when they happen, but nonetheless, I love figuring out problems and then coming up with a really cool, and useful, solution.
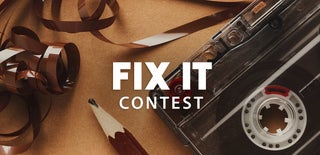
Second Prize in the
Fix It Contest