Introduction: Wicked Fast Dremel & Router Bit Organizers Using Dadoes (Instead of Holes)
With router and Dremel bits, I often don't know what I need until I see it.
After several iterations of drilling holes in wood, I began looking for a solution that would:
- be faster to make
- have a much higher density
After several bad ideas over the course of several months, I had an epiphany: Intersecting dadoes are perfect for keeping cylinders upright.
The idea: Find the perfect dado width. It would need to be just smaller than the shank diameter, yet large enough that the intersection of 2 dadoes would accommodate the shank. A shank can then fit in the intersection, but not the dadoes that make up that intersection.
The Benefits:
- Speed
- Density
- Organizational bliss
The Speed: Wayyyyy faster than I anticipated. In ~25 minutes, I was able to:
- Drill 63 holes for the 1/2" shank tray
- Drill 216 holes for the 1/4" shank tray
- Drill 384 holes for the 1/8" shank tray
- Change blade setups between trays
- Sand off the tearout in the grooves of each board
In this case, drill = cut a dado, and holes = intersections.
In this Instructable, I'll give you:
- All specific dimensions for making organizer trays for 1/2", 1/4", and 1/8" shank trays
- Ideas of how to achieve those dimensions using various blade setups.
Note: This is not a prototype. I do many prototypes, but the prototypes for this project were made over a year ago. What I'm showing you here is the tweaked, final project after a year of using the prototypes.
See the video!
I'm pretty stinking excited about this project. It presented a few opportunities for various fun tests. The video contains those tests as well as a walk-through of making these organizer trays.
Note: I used Baltic Birch, but recommend you just use a 2x6 to avoid the glue-up.
Step 1: Gather Parts & Tools
Parts:
- Part of a 2x6
Yeah that's all. I went fancier in the video, but a chunk of 2x4 or 2x6 is a great place to start (and end for that matter). It's the perfect thickness and you can avoid having to glue up layers.
Tools:
- Oshlun 8" Dado Stack
- Freud Thin Kerf Ultimate Plywood Blade (I love this blade, but don't use it for ripping)
- Measuring tape tape (millimeters)
- Measuring tape tape (inches)
- Magical roll of sticky sandpaper
Then of course, a table saw + crosscut sled!
--
Notice: I use affiliate links to help pay for some of the supplies used in my videos, tests, and Instructables. Your usage of them costs you nothing, and I get a small kickback on any sales, which I bigtime appreciate. I have a strong stance about how I will and won’t use affiliate links: https://www.keithstestgarage.com/affiliate-usage/
Step 2: Prepare & Cut
Here are my findings. (See picture w/ table for more details.)
Set Up Your Crosscut Sled
Measuring tape tape is extremely valuable for cuts like this. I don't care to zero the tape to the blade, but rather, just stick it on and use it as an incremental guide.
When I say "spacing" I really mean "intervals"
I realize "spacing" may refer to the distance between two dadoes. But, I'm referring to the cut increments. So, if the spacing/increment is 1", you'd make cuts at something like 2", 3", 4", 5", 6", etc. (Therefore, the distance between the dadoes will be less.)
Tray for 1/8" Shanks
- Use a standard thin kerf 3/32" saw blade. Easy, right?
- Spacing: 1/2" or 1 cm. (I did 1 cm on accident and it worked well)
- Depth of dado: 0.5"
Tray for 1/4" Shanks
- Use the same standard thin kerf 3/32" saw blade.
- Plus, make an extra cut at +1/16".
- Spacing: 1/2"
- Depth of dado: 0.6" - 0.75"
Example cut+extra sequence:
- 2"
- 2 1/16" (increment +1/16")
- 2 1/2"
- 2 9/16" (increment +1/16")
- 3"
- 3 1/16" (increment +1/16")
- 3 1/2"
- 3 9/16" (increment +1/16")
- ...
Tray for 1/2" Shanks
- Use a dado stack: both wings + one 1/8" chipper
- Spacing: 7/8" - 1"
- Depth of dado: 0.75"
TIP: Reduce the amount of tearout by using a blade with alternating bevel teeth. See picture.
It's hard to believe it, but you're almost done.
Step 3: Finishing Touches
Bust out some columns for a little tray to hold various parts that don't fit in the holes.
Clean up tearout. Old faux wood blinds and a roll of sticky sandpaper make a quick stick sander that's perfect for this.
Step 4: Organize & Enjoy
You know what to do now. Go have fun. If you make this, drop a note or post a picture!
--
Subscribe to my YouTube channel if this is your cup of tea. Or Joe, or whatever you drink that you like. Check out my website: Keith's Test Garage.
Follow me on Instagram to speculate on what that thingamajig may turn out to be.
And, then there's Twitter which I still don't know how to utilize: @KeithsTestG
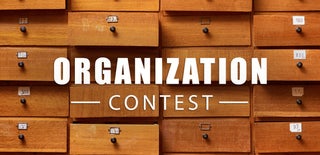
Runner Up in the
Organization Contest