Introduction: Winch Cardboard Prototype
Out of cardboard, I created a prototype for a front-mounted car winch. The idea was to test a winch that had a remote-touch interface and a front cover to protect the cabling and internals (no one wants mud or snow caked on your expensive synthetic cables). The front cover doubles as a theft deterrent as well. It's made to scale based on designs from the WARN winch company. Maybe with some luck they'll send me a real one to test with!
What you'll need:
- 4mm cardboard
- Hot glue gun & sticks
- paper towel tube (or something similar to serve as a dowel)
- Rope/string
- 1/4" Foam core (if you're making the remote control)
- Cutting tool to cut the cardboard (e.g. X-ACTO)
- In my case, I used a laser cutter: Universal Laser Systems - PLS 6.150D
- Through cuts: 75% power / 75% Speed
- Etching: 25% power / 100% speed
- Duct Tape for the panel hinges
- Velcro to make the front panel latch to the body.
Step 1: Design
Problem: Front-mounted car winches have several problems.
- Components like cables, rods/spindles, and mounting bolts are often exposed to the elements or prying eyes.
- Engaging the motor is not intuitive at times. There can be confusion with the clutch.
- A tethered or wireless control is often required, which causes another storage problem.
Solution: Design a winch that encapsulates all of the said components while providing an intuitive interface that integrates easily into a self contained platform.
Approach:
- Storyboard - a driver gets their car stuck and uses a winch to pull his or her self out of trouble. With the use of my design, the experience is fun and intuitive.
- CAD design - Draw and assemble the cardboard pieces in DSS Solidworks - based on the scale of the WRN Zeon 12-S Winch
Downloads:
Download Flat Cut File (Illustrator File)
Step 2: Cutting the Cardboard
For precise cutting, I used a laser cutter.
- The first image contains all parts for main structure.
- The second image is the cut sheet for the touch panel and spindle container (the dowel which holds the rope/cable).
- In the third image, you'll see the laser cutter
- Note: I applied etching with the laser cutter for the purpose of providing directions as well as branding (for an immersive simulation).
Step 3: Assemble Side Pockets
These pockets are where the clutch and other driven components would be contained.
The outer and inner vertical plates consist of 3 cardboard pieces each.
- Lay the parts of the larger inner panel flat.
- Using your heated adhesive merge the 3 cardboard parts together. You should have a single thick panel.
- Collect your 6 side panels and stand them upright, while nesting them in their correct areas.
- When applying your adhesive, only create your joints on the inside. It will provide a cleaner, less distracting look.
- The majority of these joints are pull-joints. Near the end of the assembly, you may need to resort to gravity joints.
- During assembly, installing a small cardboard joist to provide support may help prevent your "pyramid" from toppling over.
- You'll merge 3 cardboard pieces to create the outer "end" plate.
Step 4: Center Body Assembly
You should have your two outer pockets completed.
- Prop the pockets so that you can assemble the center body parts in their appropriate niches in the inner panels.
- Begin with the top by flipping the assembly on its head and finish with the bottom 2-piece plate
- You can install joists to assist in the assembly.
- NOTE: Do NOT glue the front panels. These need to be free to move. The top and bottom panels should be the only permanent installations with adhesive applied.
Step 5: Upper Console Assembly
- Merge your outer panels, which should consist of 3 parts each.
- The nesting steps should be on the inside of the console - that way, the surrounding panels will sit flush when compiled.
- For the clutch lever that slides back and forth, you can wrap the inner square with thin plastic (from cellophane or a shopping back. This will provide a smoother engagement.
Step 6: Console to Body Attachment
- With your upper console assembled, place it on top of your main body.
- Install push joints only on the sides and the rear. The front will be held by a friction joint.
Step 7: Assemble Multi-plate Front Cover & Install Dowel
- Nest all of your front plates onto the main body. They should be held by friction joints.
- Using duct tape, create lateral joints in-between each plate. There should be about 1.5 inches in between each plate.
- Test your cover by reinstalling the plates with friction joints and slowly "peel" your cover away. There should be definitive "de-plating" when it opens up. The plates should not detach all at once.
- Install your dowel arms. They should hang from the "ceiling" of your main body. Install your dowel by flexing the arms a bit. Install your end discs onto the dowel to prevent it from sliding out.
- NOTE: You can wrap thin plastic around the dowel's ends to provide a smoother engagement when it spins
- Wind your rope around the dowel and feed it through the rear of the winch.
- When tugging on either end, the dowel should spin freely.
- Attache your hook or carabiner to the front end of the rope.
Step 8: Touch Interface
- You may need to adjust your bed schematic for where the touch interface will nest.
- Based on the thickness of your remote, you'll need to stack mattresses to elevate your device. It should sit flush with the bed.
- Instead of using a real phone, I created a foam-core prototype with paper slides.
- The top cover should have a center plate on the bottom (inside). Merge the two with each completely centered. this will prevent the cover from sliding off. Users will have to lift or pry open the cover.
Step 9: Fin
- Time to demo!
- I printed out the front of an FJ cruiser to enhance the simulation and set it as a backdrop.
- The hook or carabiner should store itself neatly into the first floor of the upper console.
- Using the holes in the rear of the winch, you'll simulate mechanical enagagement with rods to actuate movement. The upper hole will elevate the touch interface so it can be grabbed.
- The lower hole will push the front cover open from the upper console. It should detach easily from the friction joints.
- Your user's task should be to use the winch to attach to a ring and engage the motor to retrieve the ring.
If you need additional parts or files, please DM me and I'll try to provide any assistance I can.
If you like this, please favorite or comment as I'm trying to win the Cardboard Challenge!
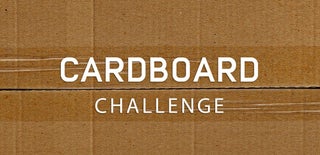
Participated in the
Cardboard Challenge