Introduction: Wood Pellet Storage Shed
My daughter and I built a Wood Pellet Storage Shed for her house. She uses her pellet stove for a large percentage of her heating requirements, her other source is an oil furnace.
She needed a covered place to store the pellets when they were delivered on pallets. I managed to get a large 8 foot by 3 foot pallet from work and that helped spark the idea for what type of shed to make.
Step 1: Supplies and Prefabrication
Supplies:
Along with the free 8 x 3 foot equipment pallet, I was lucky enough to get 18 - 12 foot by 6 inch pressured treated former deck boards when the town I live in had a give away free day, where residents could put out stuff that they wanted to get rid of, the former owner had replaced his deck boards and I got all the left over ones in good shape.
We had to buy 5 - 4 x8 sheets of chip board, 10 - 2 x4 's x 8 feet, 3.5 inch Ardox (spiral) nails, two tubes of construction adhesive, 24 Teco mending plates, 24 smaller Teco mending plates, 16 Teco rafter straps. I had some left over rolled asphalt roofing .
Prefabrication:
I prefabbed the shed at my house,
I strengthened the floor with some of the 2 x 6's around the outside of it, this also increased the floor width, this helped since the walls were going to be made out of the free 2 x 6 's without it, it would be a very narrow shed. I also covered the floor deck with some plywood that came from packing crates.
Nail holes were predrilled in the base and top plates for the walls to aid in site construction and reduce splitting of the plates.
To figure out the side profile I put one of the sheets of chip board on the ground and figured out the shape I had in mind, with that sorted out I played around with how the rafters would be laid out. That part took awhile. Once figured out the rafters were assembled with construction adhesive and the Teco plates.
The sides of the shed were cut out to suit the profile. The front header beam was made out of two 2 x 6 's nailed and glued together. The front walls were also prefabbed.
It took about 2 or 3 weeks of intermittent work to prefab the shed.
I managed to fit everything except the header beam into the back of my Ford Ranger, it took a bit of rearranging though. The beam was brought out the next day.
Step 2: Some Assembly Required
My wife and I got out to my daughters house about 10 am.
The truck was unloaded and a spot made ready for the floor of the shed. We used three 4 x 4 pallets for the base. The floor was put on these pallets and construction of the back wall was started. After the wall was finished we sheathed it with the chip board, then we stood it up and nailed it in place, construction adhesive was also used. The side walls were assembled and then put up. The front walls were then put up.
The first picture, a straight on shot makes the shed looks like it has ears.
The next day we installed the header beam, installed the rafters and put on the roof sheeting and roofing material.
My daughter bought some primer and paint and painted it over the next couple of weeks. We put some pellets in the shed so we could see how well it worked. There was also room for her winter tires.
Step 3: The Finished Shed
We installed some large cup hooks across the front so a tarp could be hung over it.
My daughter put the rest of her pellets in the shed, until she gets this winters supply delivered.
Both of us were quite pleased with how it turned out and the fact that about 50 % of the materials used were saved from going to the dump was an added bonus!
I wish I had taken more pictures during the prefab/construction, but I hope my explanation gives you an idea of what we did.
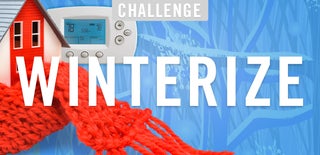
Participated in the
Winterize Challenge