Introduction: WoodWorks Fusion PC
Greetings.
So this is the Woodworks Fusion PC, a custom all-in-one computer with CyberDesk-inspired looks that was built from scratch using wood and 3D-printed parts.
The heart of this computer is an i3 4th generation desktop CPU, which is mounted on a Mini ATX motherboard with 12GB of DDR3 RAM and a GT710 GPU. Yes, the hardware is extremely outdated, but that was the whole point: to create a low-end computer with outdated components but with a better-looking chassis made of wood and 3D-printed components.
The best thing about this project is that all of the hardware can be replaced with updated versions while maintaining the same fittings. Upgrades are also possible and really simple to carry out.
Most of the body is made of plywood board, which is a strong and sturdy material that is simple to work with if you have the right tools. Using 3D-printed parts like L brackets, we can swiftly join several plywood pieces together to create a cuboid body that can hold everything and will be structurally sound.
An old LCD screen that was taken from an obsolete LCD monitor is also a part of this system.
This was made by Samsung and is a 4:3 monitor, which was very common in the early days of LDC Screen.
After disassembling the monitor, the LCD panel was exposed. It was protected by a metal housing that also had an SMPS and an LCD driver on the back of the display panel.
Older LCD monitors from 2012 and earlier often featured metal casings for several reasons, but as technology has advanced, manufacturers have explored other materials like plastic composites and thin bezels to achieve a more modern and lightweight design while still maintaining the necessary protection and functionality. Newer monitors may use a combination of materials to achieve these goals.
The whole project was first modeled in Fusion360 and then 3D-printed using a regular Ender 3. This Instructables is about the whole built process of this project, so let's get started with the built.
Supplies
- 3D-printed parts listed
- Wooden Plywood Panel, 18mm thick
- Wood M3 Screws
- Normal M2 Screws
- Varnish
- Computer Motherboard with working CPU and RAM
- HDD
- ATX Power Supply
- LCD Monitor
- GT710
- Patience
Step 1: PC Hardware Overview
As previously mentioned, a Mini ATX motherboard, an ancient GT710 graphics card, and an i3 4th generation processor are used in this setup.
Although the hardware's specs are below average, they are adequate for general use, such as web browsing and streaming videos or movies.
A Deepcool 550 Watt ATX Power Supply is being used as the power source in this case; it is brand new, and it is being used because this PC will soon receive a new motherboard and CPU, making it the ideal power source for the next generation of CPU and motherboard.
Here, a standard 2.5-inch HDD and a tiny 1.8-inch HDD are both being used as hard disk drives.
Step 2: Display
For this project, I'm reusing an OLD LDC Monitor from 2012. This was made by Samsung and is a 4:3 monitor, which was very common in the early days of LDC Screen. Now that we use wider screens, the shift to wider monitors has been driven by changes in content consumption, the need for increased productivity, advancements in technology, and user preferences.
Wider monitors offer a more versatile and immersive experience for various applications, from multimedia consumption to professional work and gaming.
After disassembling the monitor, the LCD panel was exposed. It was protected by a metal housing that also had an SMPS and an LCD driver on the back of the display panel.
Step 3: 3D Design: Fusion360
The design process for this project began with the thought, "What if we could make an all-in-one PC that is made in a 70/30 ratio of wood and 3D printed parts?"
Specifically, a design that will employ wood in a way that prevents the PC from being entirely made of wood panels Instead, it will use two full-size panels, and the remaining portion of the body will combine wood and a 3D-printed component.
Modeling all the hardware, which includes the motherboard with a graphics card and fan attached, the display, the ATX power supply, and both HDDs, is necessary before we begin the building process.
In order to create precise designs that will be simple to work around, it is recommended to start by modeling all of the physical components.
Here's a tip: for most new-gen hardware like the ATX motherboard or power supply, cad models can be found easily on sites like GrabCad or Thingiverse, sometimes on the websites of sellers or manufacturers, so check out the cad models on the internet before starting to model them from scratch.
The display served as the centerpiece of the entire design. To arrange the wooden panels in the design, we set up the display in the middle and sketched a rectangle around it.
Four display mounts keep the display in place.
Because we didn't want to use too much wood in this design, only the left and base sides will be constructed using two 60-mm-wide rectangles of wood. One full-size rectangular hardwood board will be used to construct the right side and top side.
The space between the wooden boards will be filled with 3D-printed components.
Making a wooden frame is the first step, after which we place all the hardware. The motherboard is first positioned so that the IO will face between the two wooden boards on the right side. Here, the exposed space between two wooden boards will be covered with a 3D-printed mesh, and the top side will also have a piece that looks similar.
The wooden panel on the left side is where the power supply is installed. On the left wooden panel, we cut a rectangular opening for the power supply fan. Later, a fan grill was constructed to cover this slot.
We created two separate holders that will install the power supply to the interior of the left wooden board in order to keep it in place. This holder will also keep a 1.8-inch HDD in position.
The 2.5-inch HDD was installed underneath the power supply, and for the HDD holder, we recycled the sheet metal support from the previous PC case.
Additionally, we added two handles to the top side of the computer, which will be useful when we need to raise or carry the computer.
Two coverings make up the top side of the 3D pieces. The fan and small speaker are housed under one cover.
Although the second cover is now vacant, it will eventually be outfitted with an RGB lighting system that will be managed by three potentiometers. This PC will receive it in the future, after its PCB is ready.
We design L brackets that connect two parts together using four M3 wood screws in order to assemble all of the wooden panels.
The model's back cover is made from clear acrylic.
Attachments
Step 4: Wood Panels Dimensions
The most crucial component of this project is wood; 18mm thick PLYWOOD board is used, and we simply need four different-sized sections to carry out the design.
We begin with a base wood panel that is 18mm thick and measures 250 mm in length by 364 mm in width.
Following are the left side beams, which are two long plywood cutouts, each measuring 60 mm by 355 mm.
The 3D-printed item has a slot cut out in one of the left side beams, which we can easily mark and remove with a saw.
The next component is the right side board, which measures 355 mm x 250 mm. A slot measuring 135 mm x 124 mm was built for the ATX power supply fan grill in this area.
Finally, two more beams with similar dimensions of 328 mm x 60 mm each are needed for the upper side.
Step 5: Wood Work
The woodworking procedure was really straightforward and simple to follow.
- We used measurements derived from the cad drawing and mechanical saws to cut all of the hardwood boards.
- The surface of all the wooden parts is then smoothed out using sandpaper.
- Next, we varnish each wooden board with wood varnish, giving it at least two coats.
By creating a transparent protective layer that guards the wood from moisture, stains, and damage and prolonging its lifespan, varnish applied to wood improves its durability and look.
As an optional step, wood stain can be used to change the color of the wood before varnishing.
The procedure of assembling the hardwood panels can begin once the varnish coat is entirely dry, which will take around two days.
Step 6: 3D Printed Parts
Let's have a look at all the 3D-printed parts we will be using in this built.
- L Bracket with four Holes- Total of four of them are required, and they will be printed using wood PLA with 25% infill.
- L Bracket with two Holes- Two of these are required, and the print settings will be the same for each bracket.
- L Bracket Long Version- This will be used to hold the display in place, and we need two of them with the same print settings and 25% infill.
- Motherboard Frame- You need to print one frame with 25% infill.
- Motherboard Frame Bracket 01- You need to print one of these parts.
- Motherboard Frame Bracket 02- You need to print one of these parts.
- ATX Power supply holder— You need to print two of these.
- HDD Cover— You need to print one.
- ATX Power Supply Grill- You need to print one.
- Motherboard Mesh 01- You need to print one, but at a slower speed as this design consists of many criss-cross patterns.
- Motherboard Mesh 02- You need to print one with same settings as motherboard mesh 01.
- Top Cover 01- You need to print one of these.
- Top Cover 02- You need to print one of these.
- Handle 01- You need to print two.
- Handle 02- You need to print two.
- Nameplate- need to print one.
To match the accent of the wood PC, it is vital to print pieces like the motherboard mesh and top cover in yellow or orange. All other interior components, such as brackets, can be printed in any color.
Attachments
ATX Power Supply Grill.stl
ATX Power supply holder.stl
handle holder01.stl
handle holder02.stl
handle holder03.stl
handle holder04.stl
HDD Cover.stl
L Bracket Long Version.stl
L Bracket with four Holes.stl
L Bracket with two Holes.stl
Motherboard Frame Bracket 01.stl
Motherboard Frame Bracket 02.stl
Motherboard Frame.stl
Motherboard Mesh 01.stl
Motherboard Mesh 02.stl
Nametag.stl
Top Cover 01.stl
Top Cover 02.stl
Step 7: L Bracket Joint Part
Three different types of 3D-printed L brackets are used to hold the wooden frame in place: the four-hole bracket, which is used to group two pieces of plywood together and is used at the back side in all four corners; the two-hole bracket, which is used at the front top side at both edges to hold the screen and group plywood boards together; and the two-hole bracket, which is also used at the bottom area of the top side to hold the display in place.
Because PLA is notorious for not being a structurally sound material, we use 25% infill in each bracket to give the parts structural strength and allow the brackets to hold plywood pieces together without breaking.
Metal brackets may also be used in this project, but since it was designed from scratch, it makes more sense to 3D print every bracket instead. An CNC mill could be used to mill the brackets from aluminum, but it would be for an upgrade in the future.
In total, 8 brackets are required to hold all of the wood parts together to form the chassis.
Step 8: Motherboard Holder Assembly
The motherboard frame, two different-sized L brackets, and three 3D-printed parts make up the motherboard holder assembly part that we are now preparing.
- Using two M2 screws, we first attach the Big L bracket to the motherboard frame.
- The smaller L bracket is then added in its place using one M2 screw.
- After assembling the frame, we can now attach an ATX motherboard to the 3D-printed frame and tighten four M2 screws to hold it in place.
Now that the motherboard frame assembly is robust, it will be vertically placed during the next assembly phase.
Step 9: Side Panel Assembly (Motherboard Mesh Side)
We start the assembly process by first preparing the side panel (the motherboard mesh side), which is a combination of two 3D-printed grills secured between two pieces of plywood, each 355mm x 60mm.
First, we gather all the components and place them in the right order.
Next, we mark the screw holes from the inside of the grill onto the wooden board and use four M2 screws for each side of the mesh. We add screws to both sides of the mesh, which will connect the mesh with the left and right plywood boards.
The end result of this process is a single-sided panel with dimensions of 250mm x 355mm x 18mm.
Step 10: Base Panel With Side Panel Assembly
The next step in the assembly process is to connect the side board with the base board using L brackets.
- We start by temporarily aligning the side mesh board tangentially with the base board and placing both the four-hole L bracket and the long L bracket at the corners of both boards.
- Next, we mark the holes for bracket fitment and then use a total of eight wood screws (four for each bracket) to secure both boards together.
- The side panel and base are now connected together using the 3D-printed L brackets.
Step 11: Complete Frame Assembly
As we did earlier with the motherboard mesh panel, we now use two L brackets to connect the ATX supply side panel to the base assembly.
The steps are the same: we align the plywood board tangentially with the base board first, use two L brackets, place them in the proper sequence, mark the holes, and add wood screws to secure everything together.
Then, using L brackets and wood screws, we join the two 328mm x 60mm plywood boards to the top side of the side panels.
This process will result in a sturdy hardwood chassis that is held together by L brackets that were 3D printed.
Step 12: Adding Motherboard to Wooden Frame
Next, we add the motherboard frame assembly in its position, and we make sure to align the motherboard's IO ports with the IO cutouts given on the 3D printed mesh on the side panel.
After aligning the motherboard, we mark the holes for mounting the frame assembly with the base board and use five wood screws to permanently mount the motherboard in its place.
Step 13: Display Assembly
We made a small design modification for the display assembly. Originally, an acrylic sheet was being used at the front to hold the display in place, but since we were unable to find the proper acrylic sheet for this project, we were forced to utilize an alternate approach. This method entails making four screen holders that we will screw onto the frame to hold the display in place.
We use white PLA and a 0.3mm nozzle to print all four screen holders at a layer height of 0.2mm.
- The first step in screen assembly is to install the screen in its proper position from the front. The screen will be secured in place by the lower and upper L brackets.
- After that, we affix screen holders to each corner of the screen and use a CD marker to indicate the location of the hole.
- Then, we drill designated holes into all of the screen holder components using a drill machine and a 2mm bit.
- After drilling mounting holes, we use M2 screws to firmly fasten the screen holder. Three screws were used for the top left and top right screen holders, and two screws for the bottom left and right.
The screen is now secured in position, and a screen holder and L brackets will prevent it from toppling over from the front.
Step 14: Handle Assembly 01
The handle assembly consists of two 210mm-long aluminum channels and four 3D-printed handle holders.
Fusion360 was used to model this aluminum channel, which was taken out of the frame of an old solar panel.
The channel's profile was used to construct the holder. Because this is a L channel, we had to design two sets of holders; they will be straight on one side and mirrored on the other.
Therefore, we exported all four handle holders and printed them using PLA at a 25% infill to increase the part's robustness.
The handle assembly is finished by adding a set of handle holders to each side of the aluminium channel.
Step 15: Handle Assembly 02
Following the fitting of the display, we begin the handle assembly, which is similar.
- We first position the two handles in their positions, align them, and mark the holes where they need to attach with the CD marker.
- After that, we drill out marking holes for the handle using a drill machine and a 2mm bit.
- For each handle, we mount it with two M3 wood screws.
Step 16: Name Plate
The 355mm x 250mm wood panels will then receive a nameplate.
- To do this, we first place the nameplate just above the panel's ATX Grill Slot and use a CD marker to mark the holes.
- Next, we drill holes in the designated locations using a 2mm bit, and then we fasten the nameplate in place with four M2 screws.
Step 17: ATX SUPPLY FAN GRILL
After adding the nameplate, we add the ATX Grill to the 355mm x 255mm side panel.
- Using a CD Marker, we placed the grill in its proper location and mark the holes on the grill. We then mark the holes and make holes in the designated spots using a drill machine and a 2mm drill bit.
- Four M2 screws are then used to securely fix the grill in place.
Step 18: 2.5 HDD Assembly
We now add HDD inside the PC Case.
- We are using a 2.5 HDD Metal Mount that we removed from an old PC Case to mount the HDD in its place. We slide the HDD into this Metal Mount and secure it with two M2 Bolts.
- The HDD is then inserted into the PC Case between two L brackets on the side that is opposite the motherboard, on the right.
- We mark the locations of the mounting holes for the HDD on the wooden case with a CD marker, and then we drill the holes in the base panel using a 2mm drill bit.
- The HDD is then permanently fixed in place using two M2 screws.
Step 19: 1.8 HDD Assembly With ATX Supply Holder
We design an ATX supply holder that consists of two holders joined together, accommodates a 1.8 HDD in the center, and has an H-shaped portion that connects the two ATX holders together and also acts as a cover for the HDD mount. This holder is used to mount the ATX supply inside the wooden case.
Using two M2 screws, we first attach the H-shaped HDD cover to one ATX supply holder, then attach the other ATX supply holder using two additional M2 screws.
These two ATX supply holders have 1.8-inch HDDs mounted to them, and we can now use this component in the ATX supply assembly process.
Step 20: ATX Supply Assembly
The ATX Supply is mounted in its place by using wood screws to fasten the ATX Supply assembly portion to the inside wall of the wooden panel by utilizing the ATX Supply holder assembly to hold the ATX Supply in the huge slot on the 355mm x 250mm board.
Step 21: Wiring
In order to connect a motherboard to an ATX power supply, as well as other devices like a hard drive and a power switch, we simply need to follow the guidelines listed below.
- First up is the main ATX Power connector, which consists of a 20-pin connector that attaches to a 20-pin connector of a similar size, which is located near RAM DIMMs.
- The P4 connector, often known as the four-pin CPU connector, is added to the motherboard next. It is a power supply connector primarily used to feed the processor with an extra stable 12V.
- After connecting the 20-pin ATX connector and the 4-pin Power connector, a SATA cable with port 0 and a 1.8-inch HDD that contains Windows are connected. A second SATA cable with port 1 and a 2.5 HDD are attached.
- Last but not least, we attach a push button to the F Panel connector, also known as the front panel connector, which is located on ATX motherboards. Since the F Panel connector is typically labelled, we can use the label diagram to connect the push button's two terminals to the F Panel connector's Power SW 1 and 2 ports.
If we want to use a second fan or case fan, there is a four-pin PWM fan header on the CPU that may be used to power the additional fan. Some ATX motherboards can support up to four fans.
View this helpful article for a detailed analysis of the PC power supply.
https://www.informit.com/articles/article.aspx?p=31105&seqNum=4
Step 22: Result
This project's result is a PC made entirely out of scrap using out-of-date components, a DIY wooden chassis, and 3D-printed parts.
This computer is lacking a few parts that will be added to it later on, including the top cover 01 and top cover 02; one part is for the fan grill mount, and the other is for an RGB light that can be controlled using three pots that are provided on the top side of the computer.
The 2.5 HDD is being used as a storage drive, and the 1.8 HDD is currently running Windows 11.
Regarding the old hardware, this PC appears to run more than OK, and the side mesh looks amazing.
Step 23: Running Games
We tested the hardware by playing games like Halo 1 and Minecraft, both of which run really smoothly. We got over 240 frames per second in MineCraft, which is amazing, and Halo 1 was running incredibly smoothly at 60 frames per second on high settings.
Overall, this configuration is capable of operating anything that falls under the category of basic computing, such as running CAD software, editing software, or even a selection of games.
Step 24: PC As Media Center
One of the best uses for this computer is as a media center. We loaded a few One Piece episodes onto it, and it was really entertaining to watch because the wooden panels on the computer matched the classic aesthetics of the One Piece anime. This system is capable of running YouTube and playing movies.
Step 25: Latteintosh PC and Woodworks Fusion PC
A comparable concept that used just 3D-printed parts was the Latteintosh PC Project, which we developed previously. The Latte Panda 3 Delta, an SBC with an Intel Celeron processor, served as the computer's hardware.
Learn more about LATTEintosh PC from here:
https://www.instructables.com/LATTEintosh-DIY-Mini-PC/
Comparing the Latteintosh and the Woodworks Fusion PC side by side, it is easy to see the size differences between these two computers.
Latte Panda includes features like an integrated BT and WIFI chip, PD port, and even an audio AMP, despite the fact that the motherboard we are using is quite ancient and just has a VGA port as a display out, highlighting how outdated this PC hardware is. The I3 Desktop CPU and a dedicated GPU nevertheless allow PC to operate far more effectively and efficiently than Latte Panda in terms of both hardware and computing power.
Additionally, due to the different screen sizes, the Woodwork PC is ideally suited for content consumption or even light gaming.
Step 26: Improvements and V2
Let's look at a few of the features and add-ons we still need to improve or add to this PC in order to turn it into a real monster.
#1 Add an SSD inside the HDD as a boot drive. Because the SSD will enhance the data transfer rate and affect the system's overall speed, we can significantly speed up this PC by making this upgrade.
#2 Audio Amplifier and onboard Speaker: The Woodwork PC is currently a silent PC, which means it lacks a speaker and is unable to produce any sound. Since most motherboards have speaker ports, we can connect any small speaker to them and use them as sound sources, but the disadvantage of doing so is that the sound quality is poor. To remedy this, we can create a loud speaker using an audio amplifier like the PAM8403 connected to a few powerful speakers and add it to the PC body to make it a fun and enjoyable system.
#3 TOP COVER Both parts: We still have to finish the TOP COVER component, which includes a DC fan whose speed will be controlled depending on the temperature of the CPU heatsink. For TOP Cover 1, we will use an MCU with a temperature sensor, and for TOP Cover 2, we will print an RGB Box-like device with three potentiometers and an RGB LED board that will be controlled by an MCU board. This PC's aesthetics will be improved by adding RGB.
#4 The front side needs an aesthetic makeover. There is a vacant space just below the screen where we may possibly add items like tiny screens that show the CPU temperature or other random information like photos or time.
#5 Hardware Upgrade: Upgrading the hardware, such as replacing the motherboard with a new one and switching the i3 4th generation processor for a newer one, can significantly increase the power of this PC. The best aspect of this upgrade is that no modification is required to the 3D parts or the wooden chassis.
#6 WIFI and BT PCIE Card: Since this system doesn't come with an M2 Key Slot or an integrated WIFI or Bluetooth chip, we can add a PCIE WIFI and Bluetooth module to the motherboard to turn this PC completely wireless.
These were just a handful of the present requirements that will be added in version 2 of this project.
This project is currently functioning, and I'm happy with the final result.
Thanks for getting this far; all the project-related materials are included. Please let me know in the comments if you need any further help or information.
Check out the video for detailed build instructions.
Thank you, and I'll see you soon with part 2 of this project.
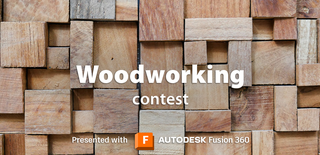
Participated in the
Woodworking Contest