Introduction: Wooden Log Cake and Cheese Platter
This is my first Instructable and I hope you enjoy it.
My daughter is getting married in October, and her mother is baking the cake. Her wedding theme is rustic, and knowing I love wood working, she asked me if I could make her the stand for the wedding cake. I wanted to make it simple using a slice of a tree log, but could not find a tree stump that was around 38cm in diameter.
I had to think out of the box, so decided to make the stand using smaller logs. I have a lot of our local Sekele wood logs that we use for braai-ing, wood fires etc, so I found some different sized logs and got busy.
Step 1: Tools Required
For this project, you will need the following tools and supplies;
Tools;
1. Band saw, or hand saw if you want some exercise
2. Hand held belt sander with 80 grit and 150 grit belts
3. Hand held orbital sander with 180, 220 and 400 grit paper
4. Hand held electric jigsaw
5. Hand held Fretsaw
6. Various clamps
Supplies;
1. Odd sized wood logs (I used logs between 3cm and 9cm)
2. 1 x 12cm length of 25mm dowel. (For the small legs you will be adding.You can use an old broom handle if you like
3. 1 x 38cm square x 14mm MDF board or some plywood would do.
4. A few small screws to hold in the legs you will be attaching.
5. Waterproof wood glue. I used Alcolin.
6. Varnish
7. Plastercine, or modelling clay
8. 2 part clear epoxy resin.
Step 2: Making the Round Board
1. It goes without saying, that you are going to be using electric tools
and mixing epoxy resin, so please take all safety precautions necessary. Wear your dust mask and mix and use the epoxy resin in a well ventilated room.
2. I started out drawing a 38cm circle on the MDF board and cutting it out using my electric hand jigsaw.
3. Sand both sides of the cut board smooth.
Step 3: Lets Get Started
1. On your bandsaw, cut the 25mm dowel into 4 equal length pieces. I cut mine to 35mm length. These are for the short legs that just lift the platter off the table slightly.
2. Measure the placement of these dowels equally around the edge of your circular board and then glue and screw them down. If I ever make another one of these boards, I will go with 3 legs, as 4 legs make it hard to get level on different surfaces.
Step 4: Cutting Your Logs Into Slices
Now comes the fun part, slicing the logs. I decided to go with about 1cm thick slices of my logs.
1. Adjust the fence of your bandsaw to 1cm, and start slicing. Be extra careful while slicing as the logs are not even, and it took a bit of arm wrestling to keep the log on an even keel. It is not that critical that the slices are totally flat, as you can always get them level in the finishing stage. Depending what size your logs are, you will need a lot of different diameter slices of logs. I just sliced a whole bunch of different sizes so that I could mix and match as I went.
Step 5: Laying Out Your Slices
Once I had a fair amount of different sized slices, I could start laying down the top of my platter. (You can always slice more at a later time to get some to fit)
1. Start laying your slices onto the board. Take a bit of time to alternate the sizes and try get them to fit as close together as possible. Once you are happy with the puzzle, you can start gluing them to the board.
2. When you have finished the gluing, place some heavy weight on top, and leave your board to dry completely.
Step 6: Adding the Rustic Look
1.The next step was to cut between the outer log slices to make the platter look more rustic. I used my fret saw for this purpose. This step is not necessary, you can just leave the edge round if you prefer, but I did it anyway and I think it looks good.
Step 7: Sanding
1. It was now time to get sanding. Using my belt sander with 80 grit belt, I proceeded to sand the entire top until I was satisfied that it was level.
2. I changed the belt to 150 grit and gave it a further sand.
3. I now swapped to my orbital sander with180 grit paper, then 220 and finally 400 grit. It is important to get the finish as smooth as possible as the resin will show up every imperfection there is.
Step 8: Sealing Your Stand
1. If you have ever used self-levelling resin filler, you will know that it is very important to seal your project well before pouring your resin. Air bubbles can play havoc with your finish.
2. Using varnish, I painted the complete stand, making sure that you try and get into every nook and cranny, as you will be amazed as to where the bubbles come from.
3. Once I had finished painting the varnish, I left it to dry overnight.
Step 9: Blocking Off the Leak Holes
1. The theory behind using the self-levelling epoxy resin, is that you pour enough resin over your project to allow it to run over the sides. Please read the instructions on the label of the resin you are using, as certain resins allow you to pour deep amounts onto your project. Most that I have used suggest doing the pour in thinner stages.
2. As I needed to fill in the gaps between the log slices before the resin flowed over the sides, it was necessary for me to plug up any holes and gaps between the edge logs before my first pour.
3. I used Plastercine for this operation. You could use modelling clay as well, but it needs to be something soft that you can remove later without the resin sticking to it. Make sure you push the clay well into all the gaps. (I took a lot of trouble in pushing the plastercine into the gaps, but still had quite a lot of leaks)
Step 10: The Resin Pour
1. Find a place in your workshop that is away from dust and somewhere where your project will not be disturbed.
2. Place some waste paper under your work, as at the final pour, you are going to let the epoxy overflow from the top of your platter and drip down the edge, which will drop down onto your work place.
3. Set up your platter on a level work place, and using a spirit level, ensuring that the top is perfectly level, as when you pour the epoxy, it is self leveling. Follow your brand of epoxies mixing instructions precisely as if you do not mix it correctly, it will not set. Please ensure that you have good ventilation while doing this, as the fumes are toxic. It is also prudent to wear a dust mask and gloves.
4. Once the epoxy is mixed, start pouring it onto your platter, making sure it fills every nook and cranny of the wood slices. I did my pour in 3 stages. The first pour was to fill in the gaps and to come up to the tops of the wood slices. Please try and pour slowly and as close to your project as possible. This is to try and minimize the bubbles that will occur. Bubbles will spoil your finish.
Step 11: Controlling the Bubbles
1. Once I had got the first pour done, I used a butane gas burner to eradicate the bubbles. Ensure that you do not overheat your surface, as it can catch alight and burn. Slowly move the flame over any bubbles you see, and be amazed at how they disappear. I placed a board over the stand to keep dust from settling onto the resin. It is worth coming back every 10 to 15 minutes to re-heat the surface as more bubbles will appear. If you do not have a butane torch, you can just blow warm air from your mouth and this will work. You can also use a tooth pick to pop the bubbles.
2. The board over the stand is to stop any dust settling onto the epoxy while it dried, as this dust will spoil your finish.
3. Let the epoxy set and dry completely. I left mine for 24 hours.
4. The next day, I got ready to do the next, and hopefully last resin pour. I found that even with so much care in eradicating the bubbles the day before, there were still some that I had missed.
5. You can drill into these hardened bubbles, using a small drill bit and clean out the drilled hole, which will fill on the next pour.
6. Now mix up the next batch of epoxy, and pour over your platter. You will need to coax the epoxy to flow down the edge of your platter. Cover once again and let it set completely.
Step 12: Cleaning Up the Residue
1. The next day, I could work on the stand.
2. After removing all the plastercine from between the logs, I used a steel burr fitted to my Dremel tool and cleaned up all the left over plastercine and well as any high spots on the edge of the logs.
3. There were some high spots on the surface as well, and using 1,000 grit wet paper, I sanded down the complete surface.
4. Making sure I dried off the entire work piece, I mixed a final batch of resin and poured it over the complete stand.
Following the earlier procedure of getting rid of any bubbles, I left it under cover for 24 hours to set.
Step 13: Finising Touches
1. Once the stand had set over night, I painted on a few coats of Varnish on the underside of my stand. This will make it more durable.
2. Once the varnish had dried, I then cut up some small discs of "stick-on" felt I had from a previous project and placed them on the bottom of the legs to protect any surface that the stand would be on.
3. All that was left to do now, was to sit back and admire my handy work, and of course get the wife's approval.
Step 14: The Finish
1. I do hope some of you try your hand at this, as I found it very rewarding and the finish you get from the epoxy resin pour is outstanding.
I do hope you enjoyed my first ever Instructable and that my instructions were clear enough.
If you did enjoy, please give me your vote.
Cheers
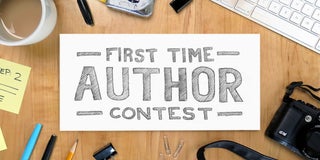
Runner Up in the
First Time Author Contest