Introduction: Wooden Table Saw
I have been working on building up my new workshop since I moved to my house last year.
The space is small but I still want to do all the projects I've been planning while waiting. One of the key tools in my dream tool room is a table saw, however, I found 2 problems with what was available on the market:
- Standard table saws are HUGE, my shop is only 2.7m (9ft) wide and 4.2m (14ft) long, this rules out full-size saws
- Contractor saws are really small, the tables are microscopic and from some of my reading, they are quite underpowered.
Then my dad offered me an old Makita circular saw, I had no need for it as I own 2 other saws but this one was still functioning but had gotten a little much for my dad who had moved to a modern, lighter and safer tool.
I used the saw once and it scared me a little too much to want to use it in hand again, it's 2000W with no soft start, it weighs about 5kg (11lb) and when it starts it wants to twist from your hand whilst dimming the lights...
It was then that I decided that its future was to be the heart of my table saw.
NOTICE/DISCLAIMER: this instructable is INCREDIBLY dangerous, there are high-speed spinning blades, mounting equipment in ways it wasn't designed for and 220V mains electricity (please check your local electrical codes and only undertake electrical work if you are competent to do so).
Step 1: You Will Need:
The following is a list of materials I used, your list may differ as I spent exactly E0 on this project. Everything I had was a scrap, from a parts bin in my workshop or donated (all by my dad).
The saw I used was a Makita 5009B, the one I have is over 35 years old so it the really heavy version with no soft start, this model is still available today but with many improved features.
Timber wise, I used a half sheet of 18mm softwood ply left over from a previous build and some scraps of 12mm ply.
I had some lengths of extruded aluminium channel, this stuff is used for mounting road signs and I had some from a previous life in the industry, your local road sign manufacturer will normally sell this quite cheaply along with the compatible T-bolts. There was also some 25mm aluminium extrusion donated.
I had an e-stop button pulled from some machine I decommissioned and a 4000W speed controller I had hoped to use on something several years back. (if I recall I got it on AliExpress and paid about E3 for it)
Assorted nuts, bolts and screws
Tools used:
Cordless drill
Impact driver
Circular saw (yes the one that I integrated)
Clamp-on saw guide
Countersink drillbits
Forstner Bits
Oscillating multi-tool
Mitre saw
Measuring tools
Pocket hole jig
Trim router & bits
Step 2: Stripping the Saw
My first task was to strip the saw, there were a couple of components in my way.
The rotating guard was not needed for the table saw and reduced the max depth of cut, this had to go. Also, there was a separator plate behind the blade, I'm not sure what this is called but I'm sure someone could answer that. This would prevent the saw from making a plunge cut so I removed that.
As I said this saw is over 35 years old and as I stripped it, I removed a lot of compacted sawdust, some of which may have been older than me!
With the guards removed and the saw put back together, I turned my attention to the shoe, this has a piece of 6mm MDF bonded to it, this again would reduce my max depth of cut by 6mm so it had to go. Removing this took a long time and some of the adhesive was still liquid in the groves (I asked about this and my dad told me he had fitted it in the late '80s after dinging the front edge of the shoe, last image) this means that this glue has been sealed in and remained wet for 30+ years.
The dent in the shoe was not a concern as I would not be using it to run the saw to a surface so I cleaned it up and moved on.
Step 3: Mounting the Saw
Using the saw and a clamp on guide, I split a half sheet of 18mm ply to a 600x1200mm 1/4 board.
I spend a lot of time and was very careful to find and mark the position of the saw for the blade to be in the centre of the board and for the blade to be aligned perpendicular to the long edge of the sheet.
When all was marked, I drilled some small pilot holed through the shoe and all the way through the ply. I then removed the saw and flipped the sheet. Using a 12mm flat bit, I drilled 6mm into the surface using the pilot hole as a guide for the counter-bore.
I used 6mm roofing bolts to secure the saw to the board, the heads of the bolts sit in the bottom of the counter-bore and do not interfere with the workpiece being cut.
When the saw was mounted, I released the locking clamp and slowly completed a plunge cut until the saw was bottomed out.
Step 4: Base
The saw was now a viable tool but not very practical.
Using the remaining 18mm ply I made a box base.
I don't have space for a floor standing tool so I wanted to make the base similar to the size of a contractor saw.
the base box was cut to 600x550mm and is 350mm tall to allow the saw to fully withdraw through the table for blade changes. I also made the back side short to allow access to set the height of the blade and to allow access for blade changes.
Using the clamp on saw guide, I cut the pieces for the base. This was when the saw was most dangerous. You can see in the first image that the board is supported on my foldout bench and one of the drawers in my tool chest (this was not clever!)
When the boards were cut, I drilled pocket holes to mount them together and all around the top to mount the saw and tabletop.
I could use a little help here as I continually get tear out on the edges of the pocket holes despite the jig and bit being new (it's a Wolfcraft jig).
Step 5: Tracks and Guides
I have an intention to make a crosscut sledge at some point for this saw so I wanted to add the groove for it now.
Using the clamp on guide and a square ended bit in the router, I cut a 6mm deep 25mm wide channel in the table top. I cut this on the left of the blade due to my left-handedness and the orientation I am most likely to run material in my shop.
I also drilled out the roadsign channel on the drill and mounted it on the underside of the table, this was the reason for the box underneath not being square, leaving space for this to be mounted.
Step 6: Control (Electrics)
Up to this point, I was controlling the saw by using a cable tie around the trigger and then switching the saw from the socket. I removed the trigger and bypassed it (don't do this if you want to be able to remove your saw to use it outside of this setup).
I cut the power lead and routed it through and e-stop and a speed controller, the idea is that the e-stop adds the safety that you can kill the power to the saw with a tap from any part of your body and the speed controller allows me to simulate a soft start by ramping in the speed. The speed controller was mounted inside an old project box which happened to have a hole right where it was needed for the speed knob.
Step 7: Rip Fence
I needed a rip fence to get me going.
For this I again used the clamp on guide, using some scraps of 12mm ply, I cut:
2 qty 600x80mm
2 qty 600x25mm
I made a "C" section with 1 of the 80mm boards and the 2 25mm boards. I then inserted a section of the aluminium extrusion. This stuff if poker straight and due to it's section profile, it's very difficult to bend. The box was then closed using the other 80mm board. All of the screws were countersunk to prevent them from catching on the workpiece.
Using the ruler, I confirmed that the fence was flat and straight.
I then bolted and oversized block into the channel using the correct T-bolts. I offered up the fence and set up everything for square before fixing. It did require a little packing before its final fix, this only required a small strip of sandpaper under one edge.
using the ruler I checked how parallel the fence was to the track I cut for the sled. As you can see in the images the measurements from the front and back of the saw match.
The block on the end was then trimmed to size and shape using an oscillating multi-tool, this gave a flush cut on all sides.
Step 8: Final Thoughts
The saw works really well, there are, however, some ideas were I to do it again.
The surface of the ply is fine for the table top, but even after only a few weeks, I can see some rub marks appearing. To remedy this I will finish the top in something like diamond coat to try and harden the surface.
The support block holding the fence to the track is a little light and can deform if you lean too hard against it, this would cause you to lose dimension on a cut so I'm going to beef that up.
You can see in the image that I made a push stick, I didn't take any pictures of this but buy one or make one, better risk it than your fingers, also it helps to hold down the timber and prevent kickback from the blade, see this video if you don't know what kickback is.
I need to make knobs for the nuts on the fence, at the moment I use a 13mm ratchet spanned to open and close them but I will soon become impatient with that.
I need to work out a method of raising and lowering the blade with a wheel or handle and not the depth setter on the saw, this is agricultural and no good for accurate positioning if I wanted to cut dados or rabbits.
If you have any suggestions for me or can direct me to resources for making improvements I would really appreciate it.
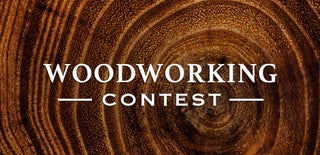
Participated in the
Woodworking Contest