Introduction: 3D Pentominoes Wood Block Puzzle
Have you ever played with pentominoes? What about a 3D Pentominoes Puzzle? You are missing out if you haven't! Young or old, there are plenty of challenges to puzzle over with these 12 simple pieces. Each pentomino is a unique shape, made up of 5 connected squares. You are welcome to spend all day looking up the background, mathematics, and other magical properties of pentominoes (Pentominoes on wikipedia), OR you can keep reading to see how to make your own set and the many challenges and solutions there are!
(If you already have a pentominoes set and want to view the many different challenges and solutions, skip down to the last step!)
I was introduced to a simple plastic 2D pentominoes set while on vacation with lots of extended family, and remember everyone trying their hand at just getting the pieces back in the box. It was challenging and so fun! Everyone wanted a turn! I just had to make one. So, I found a basic explanation and plan to get me started here. Then I went at it, delving into other tips and tricks of woodworking along the way. This turned out to be a major upgrade from the regular flat sets as these pieces are made out of cubes instead of squares! And for the puzzle enthusiast, like me, this opened up an entire new world of very challenging 3D possibilities. I decided to write this Instructable since when I was making this I couldn’t find a simple, thorough explanation of how to go about making these! Hope you enjoy!
For those with a 3D printer, here is the link to a Tinkercad project for the Basic Pentominoes. Each pentomino is 1 inch cubed, so to get the right sizing, I understand you would scale between 60-70%. You still may have to arrange the individual pieces to fit your printer bed, or let your slicer software auto-arrange for you.
Step 1: Understanding the Construction Method
The basic method for constructing this project from wood is to cut rectangular pieces of various sizes and glue them together to form each of the 12 pentominoes. Explaining how each of the pieces is cut, rotated, and combined at first seemed like a daunting task. However, Tinkercad (a simple online 3D modeling tool) came to the rescue! This is my first time using the program, but I was able to quickly model the pieces, the configurations, and the cuts and rotations to show how they are each formed and go together. Also, at the end of the instructable I used Tinkercad to show all the possible challenges and many of the solutions (Even 3D solutions!).
In the pictures you will see how each of the 12 pieces is made up of multiple rectangles, 1 - 5 units long. Since I was making mine out of wood, I tried to keep the grain and color of each piece as consistent as possible, so I've included the diagram of how I cut the pieces from the same wood stock and rotated them to form each pentomino. This will make more sense in the next steps.
If I owned a 3D printer I could have just printed my Tinkercad model and been done! However, since I was creating a wood set I needed the tools, materials and a plan to make it happen. First, I laid out one of the many 6x10 solutions to the puzzle and decided which type of wood I would use for each piece. Let's get started!
Tools
- Miter saw
- Table saw
- Planer or Router
- Clamps
- Wood glue
- Sandpaper
- Tack cloth
- Clear wood finish
Step 2: Getting Into the Woods
Being a novice woodworker, I love how this project turned out with the different colors and grain patterns!!! I chose 6 different kinds of hardwood boards for the puzzle pieces, so each pentominoes set could have 2 pieces in each color. Most local hardware stores carry multiple types of hardwood boards sold by the linear foot, so just pick the ones you want. Looking back I may have tried some different hardwood dealers or a Rockler store so there would be even more variety. The extra expense wouldn't have been too much since it is not a lot of wood.
Note: Each of these boards will seem much duller in color and luster at the store and during the creation process! The real pop comes from the clear wood gloss finish. You can see the difference in the picture of the 12 sets above where only the one had been sprayed with the finish, making the colors just pop!
Here are the types of boards I used:
- Walnut (dark color)
- Cherry (red color)
- Hickory (white color)
- Poplar (yellow color)
- Oak (light brown color)
- Knotty Alder (brown color)
Puzzle Pieces:
To make the pieces, you need 1 x 2 hardwood boards (Actual 0.75 in by 1.5 in). These will be cut in half at the beginning of the project, so you could use 1 x 1 boards if you can find them. One puzzle only needs 2 feet of 1 x 2 board for the 12 pieces. Since I got carried away making 12 of these sets as Christmas presents for family, I used a total of 24 feet of 1 x 2 boards (6 types of wood each 1 x 2 x 4 feet).
Note: If making only 1 set with 6 different colors you may have to buy extra wood since you'd need just 4 inches of 1 x 2 in each color.
Puzzle Box:
It is easier to make the pieces first and then size the box to fit the pieces. For the sides of the box I used one of the cheaper hardwoods above (Knotty Alder) and needed a little over 1 foot for the four sides (1 x 2 x 14 in). Again, the 1 x 2 will be cut in half (I actually cut even thinner), giving 28 total inches since the sides are about 8 in by 5 in totaling 26 inches of board. The back of the box uses 1/4 inch MDF panel.
Step 3: Starting With a Prototype
When I started this project, I first built a prototype. I would highly recommend taking a scrap piece of 1 x 2 (about 2 feet) and trying the methods suggested start to finish. The hardest part of building this puzzle is that the dimensions of the pieces need to be consistent, so it is best to make any mistakes in practice first. I won't explain how to build the prototype as I followed the same methods with the finished product and it would be repetitive. Instead I'll give a few major lessons learned from the prototype, then explain the details in the next steps.
- All the boards will need to be planed to the thickness of the thinnest piece. Once you've cut the 1 x 2 boards in half, if one has a thin side, that will have to be the size you plane each square down to for consistency.
- When cutting the blocks with a miter saw, you need to develop a good method for holding the pieces (especially when cutting the single unit cubes) or it will kick out and could get damaged. I used a scrap piece of wood about 8 inches with a straight notch cut out of one end to hold the blocks during each cut.
- Using the miter saw it is best to use a sharp blade and cut slowly through the block to prevent splitting on the back of the piece. I also suggest replacing the miter slot with 1/4 inch MDF to prevent tear-out on the bottom of the pieces (explained later).
- The "U" piece is the only piece with a slot where other pieces will be inserted, and so the 2 side sections will need to be slightly shorter to allow for other pieces to fit. (This will be explained in more detail later)
- Planning each piece separately and which cuts (how many units) you need to make it, will prevent cutting single units and then realizing you actually need only 2 unit and 3 unit sizes for that piece.
- When cutting the pieces, the best way to preserve the grain and the color is to cut each block needed from the same board one right after another so you get the most similar color and grain. If you are doing multiple sets and cut all the single units of a piece one right after another, then all the multiple unit sizes for the piece, it will lead to greater variations in the wood and make the blocks harder to match up since they are from different locations on the original board.
- Using tape helps keep the pieces oriented correctly and together until they are glued. (More on this in the next steps)
- I used a router on the edges/sides of the pieces (as seen in my prototype), and it was a flop! It was harder to build the 3D puzzles and didn't look or turn out like I hoped. Scratch that!
Step 4: Preparing the Wood Strips
First step in preparing the wood is to split the 1 x 2 's in half. I ran each board through a table saw to split them down the length. This should give you approximately 3/4 in by 3/4 in square lengths of wood.
Next, all the pieces of wood should be planed to the same thickness so they are perfectly square. For this, you need to determine the thickness of your thinnest piece and plane the rest to that size or smaller. I went with a thickness of about 11/16 inches (or 0.6875 inches) which was slightly thinner than my smallest board width. This thickness will determine the overall size of the puzzle - at 11/16 in the overall box is about 8 x 5 inches. I thought that was a perfect size, but you could go a little smaller or bigger if desired.
Not owning a planer myself, I used my mounted router with a 1/2 in straight flute bit, a tightly clamped board as a fence, and shaved 2 sides of each board to make each board square to the same thickness. I set the fence a distance of 0.68 inches away from the edge of the bit (the width of my smallest board) and did not move the fence the whole time. The router is shaving off the side of the board opposite the fence. To do this right I used a featherboard to hold the board tight against the fence. If there was only a small amount to take off on that board’s width I would have the bit fully extended, but when a more significant amount needed removing I started with the bit only part way out and made multiple passes extending the bit further up each time. This way I wasn’t taking off too much at one time, making it easier on my router. Once I shaved each side I ran it through again to make sure it was as clean as possible.
Step 5: Creating the Spacer Blocks
At this point it is best to run an extra scrap length of board through the table saw and planer or router to get it to the same thickness as the other boards, so you can cut it up to use as spacers. I cut 5 pieces of this scrap board each about 4 inches to start.
To setup the saw, put the 5 spacers (my scrap was not square so I marked the side with the correct width) side by side up to the left side of the miter saw blade. Carefully clamp a 1 x 2 board to the rail on the left side of the 5 pieces, making it 5 units away from the blade. This will be your stop block and should not be moved for the duration of the project.
Next, to cut the length of each spacer, put a single width spacer up against the board and cut one of the spacers to a 4 unit length, labeling it. Then, put two width spacers up against the stop block and cut another spacer to a 3 unit length. Do the same to make a 2 unit length. You don't really need the 1 unit length since the width of any of the spacers is 1 unit. Now with the spacers in hand, you will be able to use them in the same method to cut the right lengths of rectangles to create each pentomino shape.
Note: Replacing the miter saw slot with a smaller 1/4 inch MDF board will reduce the possibility of tear-out from the back of the pieces when cutting them. Here is a link to an instructable showing how to switch it out - Miter Saw Zero Clearance Insert
Step 6: Cutting the Pieces
For each of the 12 pentominoes, you follow the same method as cutting the spacers to cut the right lengths of 1, 2, 3, 4, or 5 units for each of the pieces. As you cut each piece, simply put the right size spacer up against the stop block, place your board snug against the spacer, then clamp the board in place on the right side of the miter saw (you may add another spacer on top of the board on the right side as shown to make it easier to clamp). For the long straight pentomino, no spacer is used, simply cut to 5 units length. I advise starting with the simplest pentominoes made up of only 2 pieces, then working to the harder ones.
Note: Again, it is important to hold the piece being cut (especially the smaller pieces) with a scrap piece of wood otherwise it can move around or kick out, damaging it.
For example, for the plus (or X) piece, put the 4 spacer on the stop block and cut a single unit cube. Set this off to side not disturbing the position from which it was cut. Next, put a single width spacer on the stop block and cut the 3 unit length piece. Place this together with the other piece in the same orientation it was in on the original board. Repeat again cutting a single unit cube and set next to the others. This will help to best matching the grain and color of the pieces when assembling because you simply rotate the pieces to form the pentomino as shown. Use masking tape to keep the pieces together in the original grain directions and positions until they can be assembled.
Note: If any of the pieces need to be trimmed slightly smaller (such as the "U" pentomino), rather than moving the stop block you can add business cards or cardstock between the stop block and spacer piece as shown to shorten it. Again, this is necessary for the "U" pentomino otherwise the gap will be too small to insert other pieces!
Step 7: Putting the Pieces Together
Once your pieces are cut, rotate them into place, lining up grains as best as possible. Here you use your spacers to make sure each piece is in the exact right position in relation to the other before gluing. Dry fitting these is very important! Apply wood glue using cardstock or a business card, spreading a small layer evenly on the surface of the smaller piece. Put it in position against the other piece (using spacers), hold for a few seconds, then carefully clamp with a spring clamp.
Note: A little glue goes a long way! Adding too much glue so it comes out the sides is not what you want and makes the cuts more noticeable! Even a small amount of glue when dried will make it so they cannot be pried apart.
Note: It is best to clamp just 2 pieces together at a time even if the pentomino is made up of more than two pieces. Let the first 2 pieces dry for a few minutes, then clamp the 3rd piece on. (Being careful to remember how the 3rd piece is oriented in relation to the first two is tricky, but you can use a small piece of tape to mark this.)
Note: The 8 brand new spring clamps I bought for this project left some sort of oily residue on some of my prototype pieces that soaked in and wouldn't sand off! So, I used cardstock (you can see green cardstock in the picture with the clamps to prevent this).
Step 8: Building the Puzzle Box
After assembling your puzzle, measure the outside rectangle of your pieces. Add 1/8 inch to the length and width. This will be the measurements of the inside of the puzzle box. Miter 4 boards to the right lengths of these inner dimensions, then glue together. I used multiple rubber-bands tied together and stretched around the frame to hold it in place. Next, measure the bottom dimensions of the frame and use 1/4 inch MDF as the bottom. If desired, use a 1/4 inch router on the back inside edges of the frame first to inset the MDF board.
Step 9: Finishing the Job
Use a 1 x 2 block of wood wrapped with sandpaper to smooth down the pieces once the glue is dried. Sanding takes a long time and is probably the most time consuming part of the project! For each pentomino there are a minimum of 6 faces and somewhere between 8 and 20 edges to gently sand smooth. Sand them with 220 in rougher areas as needed, then polish with 400 extra fine. Since I use a clear wood finish spray, the smoothness of the sanding is what you will feel when finished.
After sanding use tack cloth to wipe clean, then lay the pieces out on dropcloth, spraying coats of finish on each side, allowing drying time between as directed. Multiple lighter coats may be required to get the beautiful look you want and bring out the colors of the wood.
Step 10: Completed Project!
All finished! Whew, 12 sets for Christmas, check! All of the family members love these and no pieces have broken in the last 2 years.
Warning: The video runs through all of the challenges and solutions you can build with this pentominoes set, so if you have a photographic memory don't watch unless you want to see the solutions!
Step 11: 2D and 3D Challenges and Solutions
I've included 3 sets of challenges I drew up in Tinkercad, as well as the solutions to almost all of the challenges. Good luck! I've solved all of these on my own the past 2 years, but still have half of the 3D ones to figure out.
Warning: Don't view the additional images unless you want to see the solutions!
For more 3D solutions, here are a few links to my Tinkercad projects where you can dissect the completed 3D Solutions and build them yourself!
https://www.tinkercad.com/things/cqcue4pT74a - Solved 3D 3x4x5
https://www.tinkercad.com/things/kIu5mpeSRSQ - Solved 3D 3x10x2
https://www.tinkercad.com/things/7AN7kv94PKy - Solved 3D 5x6x2
https://www.tinkercad.com/things/3Jtln2qwTub - Solved 3D Letter L
https://www.tinkercad.com/things/1PF5lbWrc9s - Solved 3D Corner Staircase
https://www.tinkercad.com/things/5kdmvG6MXHL - Solved 3D Utah shape
https://www.tinkercad.com/things/0f0MnU0HsMi - Solved 3D Staircase
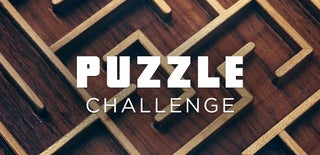
Second Prize in the
Puzzle Challenge