Introduction: 3D Printing Papercraft Darth Vader Helmet
3D printing big objects can be time consuming and waste a lot of plastic on supports and infill, especially if the print fails. So in this instructable I'll be showing you how to make big objects fast and using small amount of plastic by making wearable Darth Vader Helmet. To do this you have to unfold 3D mesh into 2D shapes and then print them on 3D printer so you still end up with plastic model.
Step 1: Choose Object to Make
It's best to search online for models that already have been unfolded and tested by other people in paper, just search for .pdo files, pepakura files or just papercraft. I'll be using Darth Vader helmet from this link: http://www.tamasoft.co.jp/pepakura-en/gallery/gall... .
You can open .pdo files with pepakura designer.
Step 2: Prepare File for Printing
Now you need to take 2D shapes and extrude them so you can print them on 3D printer. In this example I'll be using photoshop because it has 3D mode where you can extrude file and export it in .stl format. If you're using .pdo file you'll need to export it in pdf or vector format, or you could just use pdf or pictures. After importing file in photoshop, select shapes, go to 3D tab and choose New Extrusion from Current Selection. Then right-click on model and seth extrusion depth to 0.02 cm. In this part you can add custom details and extrude them bit further (you'll need to keep in mind size of your nozzle if you're adding high details). When you're done extruding right-click on layer with 3d model and choose Export 3D layer, for file format choose STL and save it.
Step 3: Print the Pieces
Now you can import STL file in your slicer. In slicer set layer height half as file hight, in this case 0.1 mm, so printer prints part in two layers. You can change this to your liking. Make sure the scale of all pieces are right.
When that's done you can print all the pieces. I printed in ABS plastic with heatbed heated to 110°C.
Step 4: Connect All the Pieces
When all pieces are done printing you can bend and connect them. Pepakura is useful in this situation for more complicated parts because you can check which parts connects to another and where. For gluing the parts together I used acetone with a bit of dissolved ABS plastic so parts quickly welded together and I was able to work faster.
Step 5: Finishing Model
If you have some holes or rough spots you can fix them with wood filler just like normal prints, and sand it down. At this point you can print little details, for example little mouthpiece and small caps on Darth Vader. To finish it I just painted the helmet with black color and little detail caps with silver.
Step 6: End
Like I already mentioned, this method is great for saving some plastic and time. Also it's great if you need light and thin models that you wouldn't be able to normaly print on 3D printer. The helmet that I printed used only 62.77 g of plastic so the cost of the print is about $1,5 and it took 7 hours to print all parts. There are many great low poly models on the internet that look awesome and are perfect for this technique.
This method is also a big upgrade to normal papercraft because all parts don't have to be cut out of paper, just print them and put them together, and end piece is much stronger and sturdy than paper so you don't have to finish the models with fiberglass or something like that.
I hope you liked my idea and would love if you leave a comment of what you think.
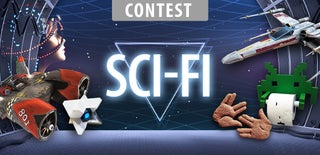
Participated in the
Sci-Fi Contest 2016
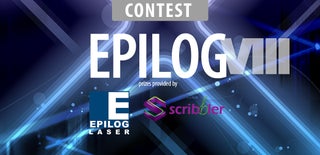
Participated in the
Epilog Contest 8
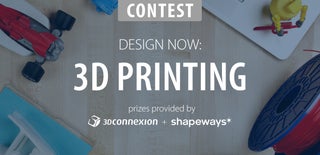
Participated in the
Design Now: 3D Design Contest 2016