Introduction: 5 Ways to Remove a Stripped Screw
We've all been there; clumsily fumbling with a screwdriver trying to remove a screw only to notice that it's been stripped, either by your hands in haste or left behind by a previously frustrated repairer. I guess the screw is there for good, right? Nope!
Removing a stripped screw takes a little ingenuity, but is fairly straightforward. We'll look at a 5 surefire methods to remove a stripped screw, starting from least destructive and moving through to more destructive methods. The method you chose will depend on your circumstances and how important it is to remove that stubborn stripped screw.
We're not going to let that screw ruin your day. Screw you!
Step 1: Rubber Band
Sometimes all that's needed to get a stubborn screw out is a little extra grip. The rubbery surface of an elastic band can help keep the screwdriver end in the stripped screw head and prevent cam out.
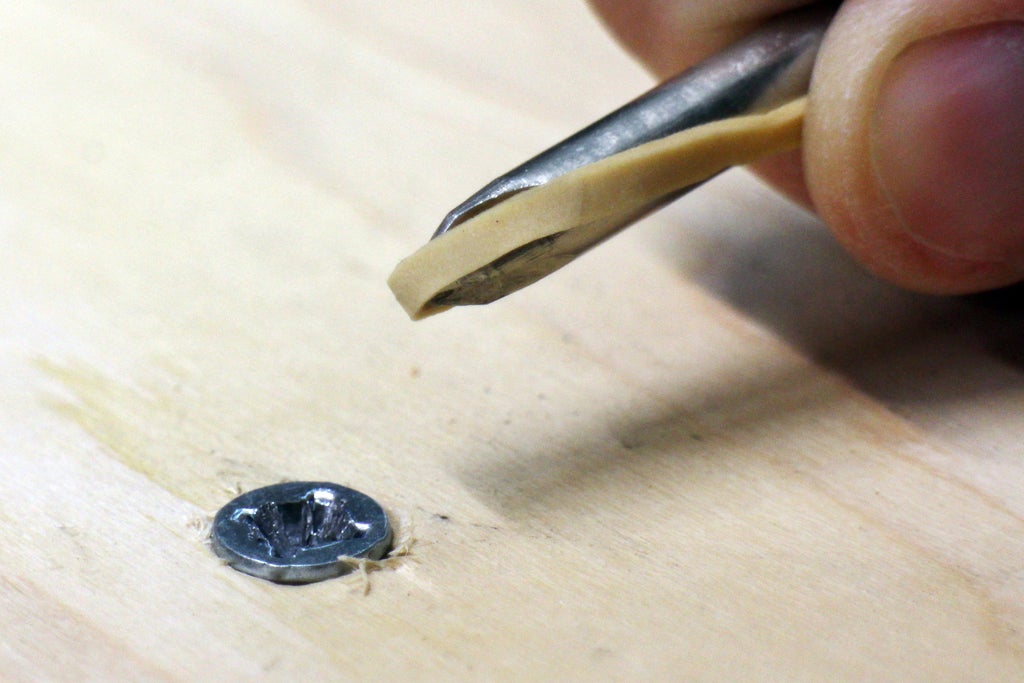
Any rubber band will work, but wide bands work best as they provide the most contact area between the screw head and the driver bit.
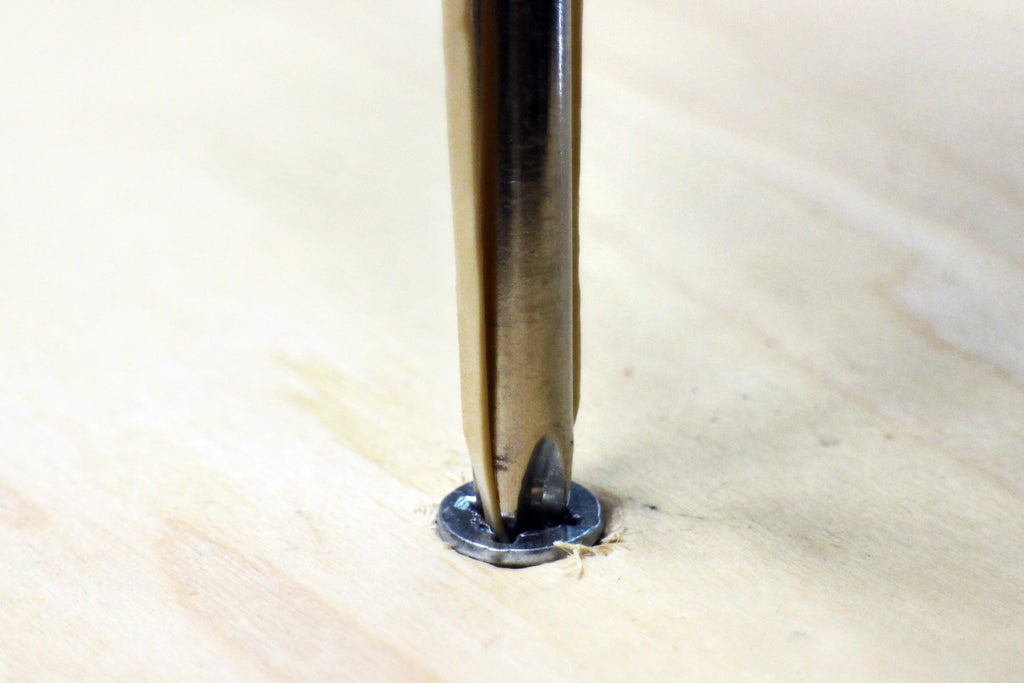
Place the elastic band over the driver bit and pull tight enough that there's no slack, then gently insert the driver bit into the stripped screw head and turn the screw loose.
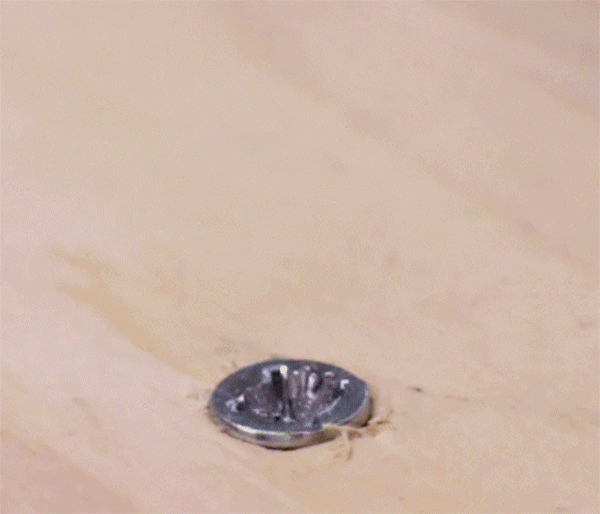
If the screw isn't totally stripped the rubber band will help fill in the areas where the screw has been stripped and provide friction where it's needed, allowing the screw to be removed.
Step 2: Grab With Drill
If the screw is not completely sunk into your material there's a good chance you can grab it with an electric drill and easily back it out.
Open the chuck of the drill and place over the head of the screw, then hand tighten to secure the jaws of the chuck over the screw. Set the drill to reverse and gently back the screw out of the material.
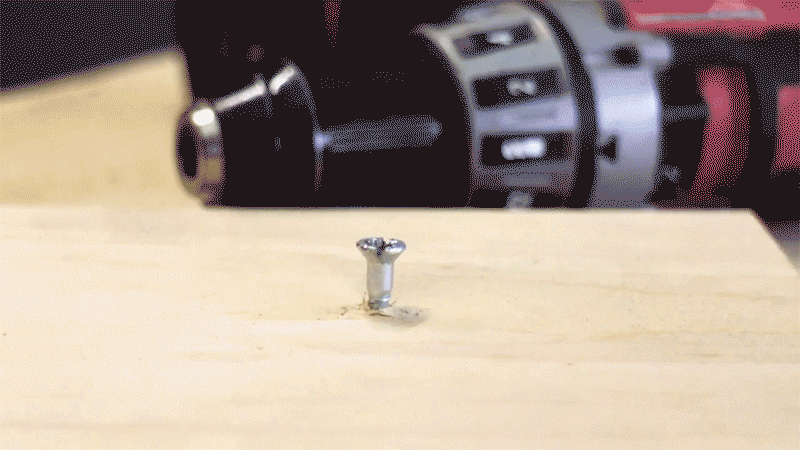
This works on just about any type of threaded screw or bolt stuck provided there is a portion of the head the chuck can grab onto.
Step 3: Screw Extractor
If there is a particularly stubborn screw that just won't come out then it's time to get a little destructive.
Screw extractors are a good choice as they are counter-threaded to how screws are threaded - screws have a right-hand twist and screw extractors have a left-hand twist.
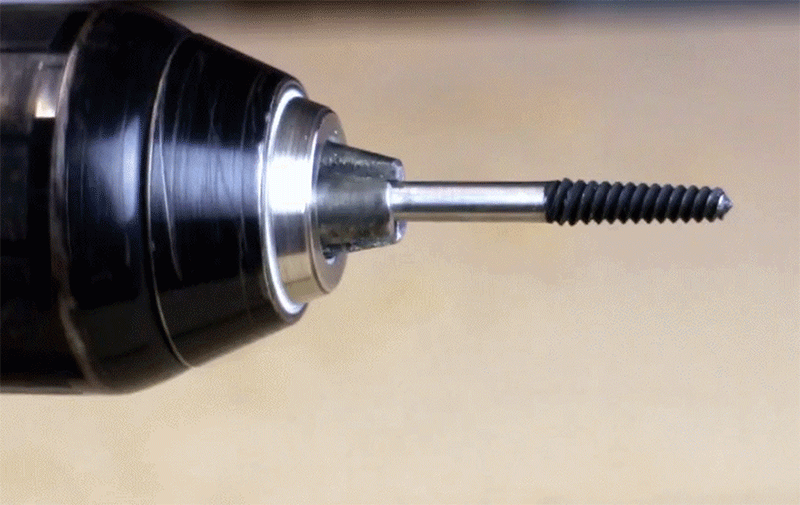
Screw extractors come in a few different sizes, and you'll need to select the right size to fit into the screw head of your stripped screw. Load the extractor into the check of your drill and tighten the chuck to hold the extractor securely.

Set the drill into reverse. Since the extractor is reverse-threaded this means that with the drill in reverse the extractor bit will drill into the stripped screw and bite into the screw head, continue drilling in reverse and the extractor will start turning the screw in reverse and back it out of the material.
Step 4: Cut a Notch
Slightly more destructive than a screw extractor is to cut a notch into the stripped screw head with a rotary tool. Depending on how deep the screw is in the material the notch cut might damage the surrounding surface.
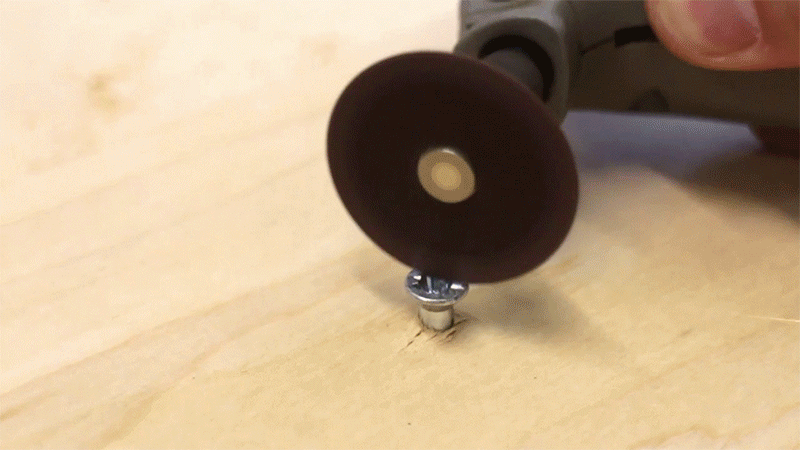
Using a rotary tool with a cutting wheel cut a single slot into the head of the stripped screw. This will make a channel for a flathead screwdriver to seat and allow you to back the screw out.
Step 5: Wood Plug Cutter
If the stripped screw is really deep inside your material and no other options seem to work then it's time to get really destructive. Wood plug cutters can be used to remove material from around the deep set screw and allow you access to an otherwise unreachable screw.
![]() | ![]() |
Place the plug cutter in an electric drill and position above the screw. Engage the plug cutter with the wood and remove material from above and around the stripped screw until the plug cutter has reached the screw head depth.
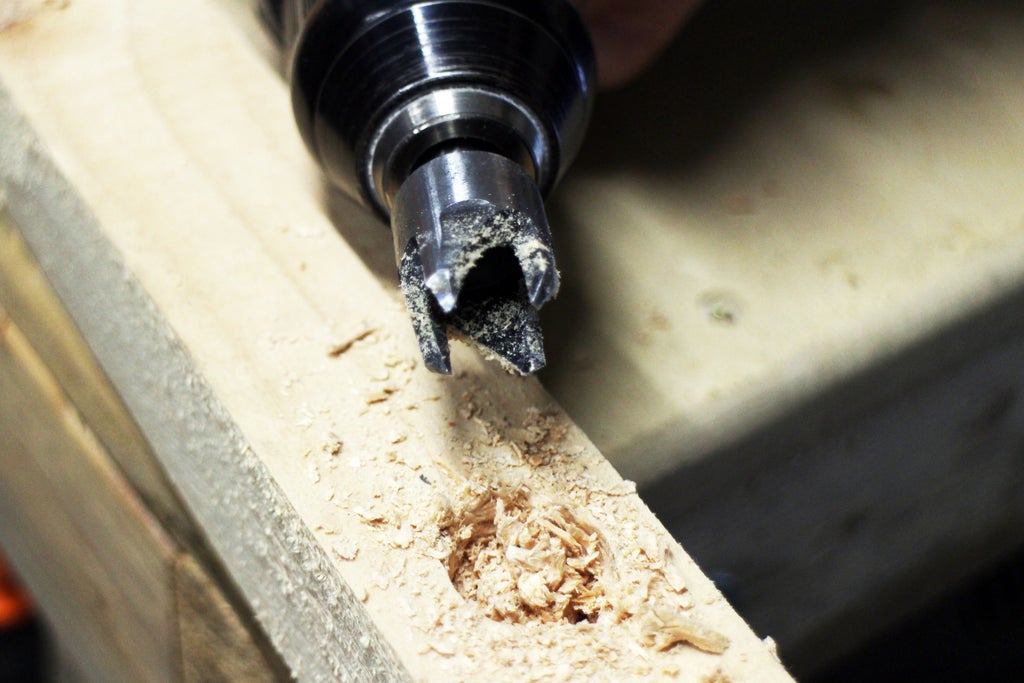
Remove the plug cutter and any debris it created and see if you can get access to the screw head for removal.

Step 6: Leave It?
Can you live with just leaving it? Sometimes screws are just too buried or difficult to get, and not worth the hassle.
Though not ideal, there may be no other way to deal with a stripped screw and you might be able to work around it. If you're resigned to leaving the screw in situ then maybe you could try and hide the screw with a patch of similar wood.
Step 7: Share Your Tips!
Necessity is the mother of invention, and I'm sure there are plenty more clever ways to remove a screw that people have come up with. Why not share your unique way to remove a screw in the comments below?
Happy making :)