Introduction: Advanced Useless Machine
Hi everyone today I'd like to present my unusual useless machine. I hope everyone heard about useless machine, but I built advanced version with seven toggle switches.
The idea of doing this box came up the husband of my cousin. As approached their wedding, I decided to do this them as a gift.
Elements I used:
- Microcontroller Atmega8
- capacitors (electrolytic and ceramic)
- resistors to reset pin
- quartz 16MHz
- connectors
- many wires
- DC motor driver L298
- 7 toggle switches
- limit switch
- power connector
- two wires supply switch
- power supply - I have witch four wires - GND, "-", 5V/2A, 12V/2A
- two servos - I dismantled from old toy
- stepper motor
- from old printer
- rail on which the carriage moves - also from old printer
- arm - I made of the nail
- boards, screws, hinges, timbers - everything needed to build the box
Step 1: Box Construction
Build my box started by gathering all the items I needed. It included elements from old printer, motors, servos, etc. Many items I took from recycling. At first I had to found old printers. I asked my friends and they gave me three printers. outside stepper motor and rail I dismantled capacitors and many wires. Testing my elements lasted a very long time. I wrote testing programs for servos, stepper motor, switches. When I was sure that all working I started to build wooden box. Everything else I bought at a DIY store.
For this I used:
- Planed board(?) with dimensions 2000mm x 80mm x 15mm (78" x 3.14" x 0.5")
- Planed board(?) with dimensions 2000mm x 120mm x 15mm (78" x 4.7" x 0.5")
- Timbers with dimensions 2000mm x 30mm x 15mm (78" x 1.2" x 0.5")
Also I needed two hinges and many screws Torx T25.
My rail is 400mm(15.7") long so size of my box is:
- Width 430mm (17")
- Height 120mm (4.7")
- Length 160mm (6.3")
Before installing all the elements in box I had to adapt the stepper motor to the transtainer. Originally there was DC motor with perforated tape and encoder. Unfortunately I had problems reading value of the encoder, so I exchanged DC motor on stepper motor from another printer.
The next step was the location in the box all the elements. At the beginning Of the two wooden beams I have placed transtainer.
I screwed on the sides another two timbers and to one fitted a servo, which open the flap, while the second contactor. Then I drilled holes for switches. Construction of the box was finished.
Step 2: Electronics
From the power supply 12V I connected by the L298 driver to stepper motor. At first I wanted to use L293 driver but it too much warming because my stepper motor receiver 2A.
5V I used to supply logic part and servos. I started tests on a breadboard. When everything worked I moved everything on the prototype board.
Program on Atmega I wrote in Arduino IDE. At the begin I wanted to do it in C in Eclipse, but I didn't have experience. (program code) In a large summary, box starts its operation in position "0", while holding the contactor. when is more switches on , flap does not close. If it turn of all the switches flap closes and a few empty loops scanning, arm returns to position "0".
Step 3: Program
Program on Atmega I wrote in Arduino IDE. At the begin I wanted to do it in C in Eclipse, but I didn't have
experience.
Program code is not so complicated. If you know a little bit C language or Arduino IDE you can understand everything.
In a large summary, box starts its operation in position "0", while holding the contactor. when is more switches on , flap does not close. If it turn of all the switches flap closes and a few empty loops scanning, arm returns to position "0".
Step 4: Conclusion
I built this useless machine for almost 3 months. Sometimes I had a big problems, which took me many days to solve, but I'm so proud of my box. It got me so much pleasure and knowledge during building it.
I know that article is not so long but I'm from Poland and I'm not writing in my language. If you have some questions, please ask me in the comments section, I will try to answer :)
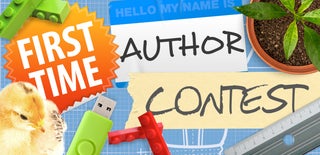
Participated in the
First Time Author Contest
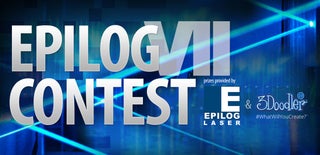
Participated in the
Epilog Contest VII