Introduction: Adventure Bag!
Do you have an adventurous spirit? Do you long for the great outdoors? Do you want to look stylish while traveling? Do you have a spare $1,600? If you answered YES! to all of those questions then can I borrow $1,600?
This 'ible is all about showing that you can make a practical, stylish, durable and AFFORDABLE leather adventure/travel bag with very few specialty tools and very little experience. If you can use a knife, a needle and thread, and a ruler with any level of proficiency then you can make this bag or something similar or something better!
Step 1: The Goal
My wife and I have been establishing a 10 year plan of trips and vacations that our family will be taking to parts of the world that we'd like our kids to see before they become broke young adults and we become broken old people. One of my pet peeves about travel is that I like to be prepared for everything yet I don't like to carry more than one bag. I usually settle for the traveler's standard backpack. They're simple, affordable, and are allowed on pretty much any plane. Unfortunately they look like crap most times. I need a bag that is going to be durable (ten year plan), simple (like me), and allowed on pretty much any plane. I was cruising Pintrest and came across a bag from a leather shop called quite creatively, The Leather Shop, which caught my eye. It was just the right combination of rugged, old-timey, and stylish. I decided to recreate this bag as closely as I could with my level of skill. It also needed to meet the most stringent of airline carry-on bag size requirements. The bag could not exceed 22" x 14" x 9" (56 x 36 x 23 cm).
Step 2: The Cost
The bag that I wanted to copy costs $1,600! (*note: I cannot afford that). At first I was outraged by that price. But then I did the math...That's pretty darn reasonable considering material cost, labor and overhead. They're stuff looks really well made and i'm not going to start pooping on what a craftsman's time is worth. This is an art that i'm still just beginning and I have to respect the skill that they are factoring into their prices.
But down to counting the beans of this project: $300 - $400 and 40+ hours of your life.
I will be using about $200 worth of leather. Another $100'ish of tools, and $100ish of accessories and materials.
If you are starting from scratch, i'll be honest, this is an ambitious project to start with. There will be mistakes in leather work, and they are costly if you make a bad cut.
I'll go over some of the specialty tools used but most of them could be substituted or made do without.
Step 3: The Inspiration
An image of the bag I wanted to copy is pretty much all I had to go off of at first. I googled a bit and found an "unboxing" video of it on youtube. Side note: Am I the only one who finds the whole Unboxing video genre ridiculous? I acknowledge that I'm a bit of a curmudgeon but watching a video of someone unwrap an item just seems like a waste of time. But seeing as I did just that to get some more information on this bag, i'll let it slide. The professional version has a lot going for it that my version will not. Like the original mine will be a single large pocket with small external molded pockets. It will also be convertible from a handbag, shoulder bag, and backpack. Unlike the original, mine will not be quite as embellished with as many fancy shiny buckles.
Step 4: The Leather
I get most of my leather from Tandy. There are many places online you can order it from, which I do occasionally, but mostly I like to look it over to look for blemishes before I purchase it. If you are going to be making a fair amount of leather projects I would recommend becoming a discount member of whichever retailer you are going to be buying from. The discounts aren't that spectacular but you will get notifications of sales that help a great deal. Just before Christmas they had a really good sale on craftsman oak veg tanned sides for about 60% off so I asked my wife for two of those as my gift. Its not grade-A stuff but its not bargain basement either.
Most of the bag will be made of 9 - 10 oz leather which is fairly thick...about the thickness of a good sturdy belt. A few of the straps will be lighter 6 - 7 oz.
Step 5: The Beginning
Unfortunately I am not very big on putting pen to paper when it comes to planning my builds. I often have to start from scratch or try to reverse engineer things I've already made if I want to duplicate it. I don't have a pattern, or template that I can give you to recreate this exact bag but it is a really simple construction. The main body of the bag is one large single piece that makes up the front, back, top and bottom. Did you ever have to make a cube out of construction paper when you were in elementary school where it was just one piece that got folded? It was probably divided into six squares in a T-shape when it was flat. This is essentially the same thing but the sides are separate pieces. The only extra material for the main piece was the overlap of the lid and the front. So this first piece is 13" (front) + 8" (bottom) + 13" (back) + 8" (top) + 3" (lid overlap) + 2" (front overlap) + 3/4" (bend allowances). Because the leather is so thick it requires some allowance for where you bend it. I gave it about 3/16" for each bend. The final dimension of this piece is 47 3/4" x 18".
The sides of the bag are 9 1/2" x 15 3/4". There is a 2" overlap on top and 3/4" overlaps on the bottom and sides for stitching.
All of the cutting is being done with a razor blade. You could purchase specialty knives for this but i find that a box of 100 blades for a couple bucks works just fine. After a bunch of cuts I just toss it in the recycling bin and grab another.
For the corners there are specialized punch sets for getting perfect smooth round corners but they are pretty expensive so I haven't ever purchased a set. Instead I use whatever I have available that makes a radius that i like. In this case I used these little plastic cups.
Life Hack: Whenever you go to a fast food place that has these little plastic cups (these are courtesy of Wendys) take as many as you can without feeling guilty. I usually grab about 20 every time i'm there. They make really good mixing cups for small amounts of craft paint. I give them to my daughter all the time when she's feeling artsy.
Step 6: The Pockets
The side pockets on the inspiration bag are small rounded wetformed pockets. I wanted to recreate this aspect but I wanted slightly larger pockets with more of a blocky look. Wet forming deep square-ish corners can be tricky because there is going to be more bunching in the edge of your corner. To help with this I created a jig out of 3/4" pine. There is a square "buck" that the leather will go over and take the shape of and a ring around that which will hold the leather to the shape as it dries. I cut a piece of the thinner leather to bout 4" larger than the buck on the sides and bottom then soaked it for 10 minutes or so in room temperature water. After it soaked I layed it over the buck and stapled the top in place. I slowly worked the leather down the sides and corner until it started taking the general shape. Next I stapled the excess leather down on the base piece of wood and worked at it some more. Once the shape was pretty close to what I needed I screwed the ring down to the base. I realize this all sounds like jibberish as I'm writing it so I encourage you to go watch some videos for a better explanation.
There are other ways of making folded pockets that are just as good, but this is the aesthetic that I wanted.
Step 7: Prepunching
I am not good with a stitching awl and I don't have a fancy leather sewing machine. For this reason I pre-punch all of my stitching holes. This is accomplished with a set of punches. This is one specialty tool that is really helpful. They are not that expensive. The perimeter of the bag is all going to be double stitched for added strength. I used a stylus to scribe a line at 3/16" and 11/16" on the side flaps and the perimeter of the largest piece. The trick to pre-punching the holes is making sure they line up when the pieces are assembled. The punch sets are all uniform in their spacing so what you need to do is pick a point along your scribe line that is common to both pieces. For instance i started at the top front of the bag and punched the first hole 1/4" from the edge of the leather. When I started punching the side piece that was being stitched to it I started at 1/4" from the same corresponding edge. As I said, the punch spacing is uniform, so if you use the 4-hole punch and then place the first prong in the last hole of your previous punch they will always have the same spacing.
Another pre-punched hole is for the decorative rivets.
Step 8: D-Rings
The D-ring attachments on the side took some trial and error and I screwed up several pieces of leather. The final product still wasn't quite what I wanted but I got tire of messing up so I went with it. The object was to have the D-ring sit flush with the surrounding leather and be kind of inset surrounded by a thicker leather. After I created the ring holder I pre-punched the holes for stitching. Because this is a more intricate shape after I was done pre-punching the ring holder i placed it on the side piece where it would eventually be stitched and nailed it down to a piece of wood using some brad nails. This held the top piece in place allowing me to punch through it to the bottom piece to ensure all of the holes matched up.
A quick tip at this point is to label the back sides of all of your pieces so that they match up at assembly time. The left and right sides of the bag are going to be identical but tiny variations in the hole spacing could be irritating during assembly if you accidentally used the left side ring holder on the right side of the bag. A small pencil mark on the back of the leather is all you need (left/right, 1, 2, 3, a, b, c...etc).
Step 9: Pocket Prep
The side pockets are made up of three pieces; the molded pocket, top flap, and decorative thumb flappy thing. Just like the D-ring I pre-punched the pocket edges. After the pockets were pre-punched I nailed them in place on the sides and then punched through them on the sides. The molded pocket and the thumb flappy thing also got holes punched for a button rivet later.
Step 10: Folds
This leather is pretty thick so it can be difficult to fold it in an exact spot like a thin sheet of paper. To assist in the folding I scored the back side of the leather. These lines are kind of like relief cuts in wood that is getting bent. I folded the bag up and made some temporary stitches to test fit the overlaps. The test fit was also to help motivate me. I can get a little impatient sometimes and seeing some kind of finished product at this point allows me to keep moving forward better.
Step 11: Straps and Accessories
The shoulder/neck strap is pretty intricate because of the multipurpose aspect of it. There are three main parts made up of several pieces of leather each. The strap is "hinged" in the middle to allow it to convert from shoulder strap to backpack strap. The straps pictured are all cut with a razor and pre-punched.
Step 12: Dyeing
Once all of the pieces are cut out and punched I started the dyeing process. I wanted something that would POP but I also wanted something..."organic" if that makes sense. I tried a couple variations on my computer to see what I liked, and finally settled on a nice forest green. The main body of the bag would be Forest Green with some Bison Brown straps and pockets. I use the Eco-Flo brand of dye. Fun Fact: Your skin is also highly dye-able.
Here are some good dyeing tips:
- Wear gloves
- Clean your leather before dyeing. There are product available for this or you can make your own. Cleaning the leather will remove any oils from manufacturing or from your own hands that could inhibit the dye from setting in. It may not be visible before you apply the dye but once you do it becomes really apparent where the leather wasn't clean and now it won't accept the dye evenly. I did not follow this rule which made a good portion of my dye just sit on top of the leather rather soak in.
- Wear gloves
Step 13: Buffing and Edging
Buffing the leather allows you to remove the excess dye before finishing. This can take some effort on larger pieces. I used the super classy technique of an old sock on my hand. Is anyone out there old enough to remember playing the Nintendo Track and Field game on the Power Pad? Remember how you felt like a genius when you figured out that you didn't have to run on it like an idiot and could just put a sock on your hand and rub it over the power pad to make your character run faster? Yeah this method feels alot like doing that...but for hours.
For the straps I cut up an old pair of jeans and laid them over my knee. I just pulled the strap over is from side to side.
Burnishing is a method of finishing the edges of the leather to give them a smoother look as well as helping make them more resistant to moisture. To do this you can use a liquid called Gum Tragacanth and a burnishing tool. You simple brush the liquid on the edges and them run them over the burnishing tool. There is a hand held burnishing tool that is just as good but requires a lot more elbow grease. The burnishing tool in the picture is one that can be inserted into any rotary tool or drill press. This makes it a great deal faster. I only ended up burnishing a few of the straps before i decided it really wasn't the look I was going for...and i'm impatient.
Step 14: Protecting
After everything is dyed and buffed you can choose to add a protective top coat. This protects the leather from moisture and can also add a gloss shine. If you cleaned the leather before dyeing and did a good job buffing the excess then this step should be pretty simple. You can apply the protective coat using sheep' wool, or in my case, another sock. If you didn't do a good job cleaning the leather and the dye didn't soak in very well then a good amount of the dye will come off on the sock when you start applying the top coat. Since i used so much dye it didn't really affect the color. I am going to start trying to apply the top coat protector with an air brush from now on, which I'm told is the better way to do it.
Step 15: Stitching and Mistakes
Once everything is dyed I start stitching it all together. There is soooo much stitching. I started with the simple stuff like attaching the side pockets and the d-ring holders, then the straps. I like to use a saddle stitch with two needles because it makes a good strong seam. Generally all of the pre-punched holes lined up nicely. The top handle strap is just a thicker piece of leather folded over. This took a little more effort to keep the thin strap folded over as I stitched but some small binder clips helped. Once i got the straps on I did another test assembly and found that the handle was actually much too long. This meant cutting the stitching of the entire handle where it was attached to the bag and cutting off a couple inches, then re-sewing it all back together.Handle
Step 16: More Stitching...so So Much Stitching
Stitching the edges of the main part of the bag took several days in small 1 to 2 hour sessions. These edges have a double row of stitching for added strength which equated to a little over 24 ft of hand stitched seam for this part. My fingers were pretty numb after this.
Step 17: Accessories
I wanted to add a little embellishment to the bag with some pieces that are called footman's loops, or coachman's loops. They're flat eyelets that you can pass straps through. They are nice looking but also serve to hold the handle straps flatter to the front of the bag. There was another last minute addition to the bag of bundle straps to hold the handle together and to hold it down to the top of the bag.
Step 18: Shoulder Straps
The shoulder straps are three separate pieces intended to make a "hinge" of sorts in the middle so that it could be converted from a shoulder bag to a backpack. I padded it all with foam rubber and then covered that with sheepskin. The sheepskin cover isn't perfect but it'll hold up.
Step 19: Adventure!
I'm really happy with the way it turned out. I'm exited to see how it ages with each trip we take. All the nicks and scratches it'll get will only add to the character of the bag.
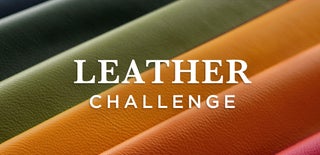
Grand Prize in the
Leather Challenge