Introduction: Armchair 400 by Aalto?
A perfect replica of the icon chair by Aalto: Armchair 400. But is it perfect?
Look closely because actually this is a scale model of about 20cm x 13cm x 16cm. To teach myself to deal with new materials and processes I made this scale model of the chair. In the next steps I will take you through my process.
Step 1: Research Dimensions
The first step is to figure out the different dimensions the chair will have. I found pictures of the original chair online and the rough dimension. Going from there I drew the front and side face of the chair and proportionally rescaled all the dimensions I would need. This way I had all the rough dimensions of everything and drawings of the views I can use during the process.
(Note all dimensions are in mm)
Step 2: Reserach Techniques
The chair exists of two main pieces, the seating and legs.
My first idea to manufacture the legs was bending plywood to the shape I need. But because of the small scale of the legs the bends it needs to make are so sharp the plywood would crack under the tension (even it you make it wet and steam it). So I had to figure out an other way to manufacturing it. After watching a lot of YouTube videos I decided to laminate wood veneer to shape the legs.
YT video: Bent plywood in 7 easy steps.
YT video: Pre Bending Parts for Easy Laminating
For the seating I was thinking about shaping Seat Foam to make it a real replica. After testing the seat foam I noticed it would be very difficult to make the exact shape I wanted and still look good after I put covered it with leather (YT video: Cutting Seat Foam). Instead of using foam I decided to use a piece of wood that I would shape to desire to make sure the chair is structural sound and the foam wouldn't mess with the leather seating.
Step 3: Legs Veneer Cut
Lets begin with the legs.
What you will need:
- MDF (for the mold)
- Maple veneer
- Cutting tools
- glue clamps
- Plastic foil
- Wood glue
- Band saw
Find some veneer (Maple is the best to bend) at a local wood shop. Make sure you have a large piece to get enough layers out of it. We will make a mold of about 8cm width to fit the two legs in one go. So I cut straps out of the veneer of 8cm width. Because I want a thickness of 2.5cm I need 14 layers of veneer. Make sure you check your veneer thickness and adjust.
Step 4: Legs the Mold
I glued a couple of scrap pieces of MDF together to get a thickness of about 8mm. I glued the drawing from before to cut out the inner mold for the leg with a band saw. In the middle of this mold I drilled a big hole where the head of the clamps will be. Using the other pieces I created negative molds to clamp on the outside of the veneer. To prevent the veneer sticking to the mold I place baking paper on the mold and plastic foil on the outside pieces.
Step 5: Legs Glue Up
I tried different techniques to bend and glue up the legs. By trial and error I found out that going slow in the glue up is key. During my test runs I tried to glue al the layers at once which failed over and over again.
So finally I took another approach. Every day I would glue up a small piece of the legs (one corner or side every day) with only half the amount of layers. Using a paint brush I applied glue in between the layers for the section I wanted to glue that day and clamped everything together when done. I did this over and over again till done.
I did the same for the other half of the layers on top of the existing layers . After 12 days of gluing and drying the glue up was complete and ready to process.
After drying I got the veneer of the mold but I notice it is a bid bend. Luckily the 8cm width is more than enough to get two 2,5cm out of it eventho it is a bit bend.
NOTE: It would have been ideal if the direction of the veneer grain would turn 90° with every layer. But the veneer I got in the beginning wat not wide enough to cover the whole stretch. To not mess us by gluing different straps next to each other to cover the whole distance I decided not to do it.
NOTE 2: Why my first tests were a disaster? In test one I pre-bended the veneer by making it wet in hot water, clamping it on the mold and letting it dry. Next I glued al 14 layers at once and clamped them. As a result it took to long to glue everything and half the glue did not take well. At this point I did not have the negative molds on the outside yet so all the corners had gaps in it. I used the negative molds on the second test. I glued up 5 layers now which was better to apply the glue and the gaps were gone but after it dried out the whole leg was totally bend and unusable.
Step 6: Legs Cut and Sand
After drying out I detached the veneer from the mold and applied blue painters tape to minimize blowout while using the band saw. I use the inner mold to stabilize the veneer while sawing. This way the veneer wouldn't wobble up and down while using the band saw. I cut out two legs a bit wider than the width I need. Using a belt sander I bring them down to the size I want and finish the edges.
Step 7: Seating Shape
I had some beech blocks laying around which I used to shape the seating. I divided the seating in two, the vertical back block and the horizontal block. This makes it easy to shape everything as I want.
First I use the drawing from the beginning to mark the seating shape and use a band saw to cut it out. Then I use a belt sander to shape the edges and curves. When done both pieces together make a perfect chair.
NOTE: This shape will define the chair part. Make sure you sand it how you want because the leather wont mask big mistakes.
Step 8: Seating Leather Cover
Next up is covering the seat with leather. Use a piece of,paper to get the dimensions right. Cut the leather and sew together (to be honest I had a lot of help with this so I am not the person to give you solid advice about sewing, if you're not comfortable with it find someone who can help you). I nailed and glued (superglue) the ends of the leather on the wood where the horizontal and vertical block come together. The vertical block has a big flap which will cover the full underneath of the chair. This makes it possible to secure the leather to the horizontal block with nails and glue at the underside. Don't glue the flap yet.
The holes and dowels are explained in the next step.
Step 9: Assemble
First I assemble the chair. I drill holes in the vertical and horizontal chair blocks to fit dowels. Glue in the dowels and press the two pieces together and let dry. Next you can glue the big flap to the underneath of the seating and finish it.
Next up I bring together the legs and seating. Because there will be no heavy load on the chair I use metal pins. I chose not to glue them in to not mess up the leather. I drill holes in the seating through the leather and into the legs. Place the pins and assemble the legs.
And we are done!
Step 10: Armchair 400
The result! A miniature replica of the icon chair!
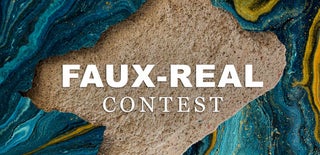
Participated in the
Faux-Real Contest