Introduction: Big LOVE Sign Marquee Letters
This project was quite a challenge. The sign was to be 1.5 m high, and at the same time be quite light and resistant to impact.
I received the order for letters from the wedding photographer, the product was to be useful in the outdoors for photo sessions as well as in the room during the wedding.
If you want to see how I dealt with it I invite you to look through the instructions and watch the two-part video presenting the process of formation of this giant sign!
Consider subscriptions of my YT channel!
Supplies
The links are affiliate, so by buying through the links you can support me a little, I tested each of these stuff and I can recommend.
Materials:
- 1 sheet of plywood 1.5 x 3m (~ 5 x 10ft) 10mm thick (~ 3/8 in)
- 2 sheet of plywood 1.5 x 3m (~ 5 x 10ft) 5mm thick (~ 3/16 in)
15x15mm (19/32 in) steel tube
20mm (3/4 in) flat bar
WS2811 RGB LED 30mm milky module: http://ali.pub/3fn7ln
Contoller K-1000C: http://ali.pub/3fna0r
DC-DC converter SD-100A-12: http://ali.pub/3fncto
Screws for wood
M6 thumb screws
Small hinges and a lock
Paint, varnish
Wood glue
Tools:
- Circular saw
- Jigsaw
- Drill, driver
- Nail gun
- Orbital sander
- Chop saw or table saw with cross cut sled
- Angle grinder
Soldering iron Bakon 950D (in the project I use a different one but this one I have now and it is awesome): http://ali.pub/3fnc74
Wire stripper: http://ali.pub/3fndpy
Side cutters: http://ali.pub/3fndpy
- Drill bits
Brush and paint roller
Step 1:
Step 2: Layout
The design of these letters was proposed by my client, the project came out simple enough that basic woodworking machines will successfully work for us.
At the beginning, I placed the letters so that they fit on a sheet of plywood and I printed layout a 1:10 scale.
I have transferred the pattern in full dimension to a 10mm plywood sheet.
Attachments
Step 3: Cut, Cut, Cut...
I put together a sheet of 5 mm and 10 mm plywood (with a drawn layout) and squeezed with the clamps. With the help of the aluminum bar as an guide rail, I cut the letters with a circular saw. All corners to which the circular saw did not reach was cut by a jigsaw. In this way, I also cut the front and back of the letters.
Then I cut about 100 square pieces of plywood 10 mm with sides equal to 35 x 35 mm (~3/8 in) and sanded them. These will be internal letter brackets.
I cut the second sheet of 5 mm plywood into 15 cm wide strips (~ 6 in), they will be the sides of the letters. If you want to have deeper letters, the strips must be wider and maybe of thicker material.
Step 4: Drilling Holes for Lighting
On the front I drew lines about 65 mm from the edge, then divided them into lengths from 10 to 15 cm. At the points of division and on the corners I drilled holes with a diameter of 30 mm.
Then I sanded everything, getting rid of the jagged edges of the holes. And then I shrank and turned into a little girl...
Step 5: Assembly Main Structure of the Letters
It's time to put something together. On the fronts, marked places where there will be internal supports that I have tucked under the bottom. After making sure that everything is flat, I individually glue each support and nailed down.
Then I put the back of the letter underneath and started to measure and cut the sides. When I had everything cut, I drew lines on the sides, marking the center of the front sheet. I applied glue to one side of the front and the sides of the supports. After that I put a piece on the back sheet and nailed the side strips.
After the adhesive dried, I patched all nail holes and sanded flat.
Step 6: Rear Supports
If the sides of the letters made wider than I did, it may turn out that the back supports will be unnecessary and the letters will be stable without them. I made letters quite shallow, because the client wanted their mobility.
I cut four pieces of 15 x 15 mm tube with a length of 100 cm (~ 40 in). By setting one of the letters on the table I determined more or less the position of the support and its angle. Holding the tube at the edge of the table and letters I traced the cut lines on the tube from their surface. After cutting the first tube at the right angles, I traced the cutting lines on the next three. I also cut the flat bar pieces to the feet of the supports and their mounting sockets.
I set the support on the footer at a proper angle, leaning against the mounting element attached to the work table. After welding everything together, I've grinded the welds and I drilled 6 mm holes in the mounting elements.
Step 7: Back Covers - Pre-drilling and Controller Door
In the lower part of the rear I drilled two 30 mm holes in each letter and one in the letter "E". These are holes for power sockets and for data transmission (more on this later).
I put together the main structure of letters and their backs, pre-drilled them and screwed them. Pleacing the support on the back of the letters, I traced their mounting parts on the back sheet. Then I drilled and cut out the sockets holes with the jigsaw.
In the back sheet of the letter "L", I also cut a larger opening for the door to access the controller mounted inside that letter. I placed and screwed the hinges to the door and mounted the lock.
Step 8: Back Covers - Mounting Points for the Rear Supports
From the inside, I glued pieces of plywood covering the hole to the support, then reinforced the connection with screws. After inserting the supports into the sockets, I drilled the mounting holes in the sockets.
Smaller, square pieces of plywood I drilled in the middle with a 6 mm drill, then with a 10 mm drill I widened these holes halfway down the plywood. In enlarged holes, I hammered the M6 nuts and reinforced them with CA glue. I glued these pieces to the back of the mounting sockets and screwed them (while the glue was drying) with M6 screws with a knob that would later serve to screw the supports.
Step 9: Painting
I dismantled the letters and started painting them. First I painted with a brush but it took a long time. It turned out that the paint roller is a much faster solution and makes it easy to paint the interior of the holes for the LED modules. I applied three layers of white paint (two on the backs) to the full coverage and one layer of matt clear varnish. After drying each layer, I sanded everything with sandpaper.
And I had an unexpected guest in the workshop.
Step 10: Mounting LED Modules
LED modules have been pressed in from the back starting and ending at the bottom of the letters. Each module has been additionally screwed on with two small screws.
Unfortunately, I was not ordering distant wires and I had extra work to extend them...
Step 11: Power and Data Sockets
Through the holes in the back I have traced the places where the power and data transfer sockets are to be located. The sockets had to be a little higher, so I attached pieces of plywood to which they will be screwed. I connected everything with wires according to the attached diagram.
Attachments
Step 12: Inverter and Controller
According to the diagram in the letter "L" there is an DC-DC converter SD-100A-12 to which the power from the first socket is connected. The converter allows to power the sign from any 9 to 18 volt power supply, from an automotive installation or a 12 volt battery. The converter provides power for LED modules and K-1000C controllers which need a stable voltage of 12 V.
After connecting everything all loosely hanging wires are fastened with nylon straps.
Attachments
Step 13: Assembling and Connecting Letters
It's time to assemble the letters! After screwing on the backs and door for the controller I attached PVC pads with double-sided tape to the bottoms of each letter. Pads were also placed under the feet of supports and I attached the supports to the letters.
Now there are only set the letters on the floor, connect the cables and connect them to the power supply!
Step 14: Programming and Running
Nope... first I have to program the controller K-1000C. The programs for this controller are created on the computer using the free LedEdit-K software and transferred to the memory card. The software allows you to arrange the order of each LED module WS2811 and arrange them in space, so you can display animations as on a digital display.
The software itself and the instructions for its use can be found on the Internet. Unfortunately, I do not feel at home with my poor English to describe the whole procedure, forgive me. This is the topic for a whole separate article.
Step 15: Glamour Shots!
Where you can find me:
YouTube: https://www.youtube.com/catlighting
Instagram: https://www.instagram.com/catlighting
Facebook: https://www.facebook.com/catlighting
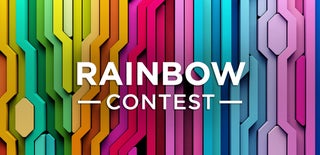
Runner Up in the
Colors of the Rainbow Contest