Introduction: CNC Guitar Using Fusion 360 and a Shapeoko XL
Hey makers, today I want to share with you my process for designing and making a guitar using Fusion 360 and my Shapeoko 3 XL. We're going to walk through the process of designing the guitar to ensure that all of the pickups, volume cavity and neck pocket will work with your electronics. I'm going to spend the most time on using Fusion 360 and how to design the guitar and tool paths to cut out the guitar on your CNC machine. For those of you who aren't familiar with Fusion 360, it's a great tool for hobbyists (and Free). You can use it for the designing and CAM process. I've found that it works great with the Shapeoko 3.
I've also attached my Fusion360 file so you can follow along as I walk through the design and CAM process.
Attachments
Supplies
Body:
Maple wood (2 pieces glued up to make a stock piece measuring 20" x 15" x 1.625")
Electronics & Hardware:
1/4" Oval Guitar Input Jack Output Plate - Amazon
Electric Guitar Neck Plate - Amazon
Copper Foil Tape - Amazon
2x Humbucker Pickups - Ebay
TELE Wiring Harness,Black Plate, Knobs,Switch For Fender - Ebay
Humbucker Guitar Bridge Roller Saddle - Ebay
6 Right Guitar String Tuning Pegs - Ebay
Neck:
22 Fret Maple Wood Fretboard - 25.5 Inch Scale Length - Amazon
Step 1: Designing the Guitar in Fusion 360
If this is your first time designing a guitar body, I'd grab some guitar blueprints online first and use those as a baseline. I grabbed a Telecaster and a double cutaway Les Paul to use as examples. A great feature in Fusion 360 is the capability to calibrate a canvas to make it to scale. Once I imported a canvas (Insert -> Canvas), you can right click on the Canvas on the left side of the screen and select Calibrate. This will allow you to calibrate any of the measurements in the blueprint to be scaled to actual size in Fusion.
Before doing anything else, draw a construction center line down the guitar. This will help especially if you design the neck in the future. After overlaying both designs, I started with the general shape of the guitar. I wanted to do a mix between a Les Paul and a Gibson SG. I decided to go with the classic Tele style top and a volume control cavity to style, but I wanted to use humbucker pickups and add some SG style lines. Once happy with the body shape, I added the volume cavity, both pickups as well as the neck cutaway. Once I knew where all of my hardware was going to be placed, I gave it a few more lines where I wanted to trace the cutaways in the body.
Now from the sketching, we're moving into the actual 3d aspect. I knew that my maple glue up was roughly 1.65 inches, so I needed a body that was going to be thinner than that, allowing me to do a facing operation with the CNC machine to make sure it was clean and level. I ended up making the body 1.55 inches thick, which also helped make the guitar more manageable since maple is a pretty heavy wood. So you'll want to extrude the body to your total depth desired at this point. I then extruded out the pickups, volume and neck cavities.
The question I get asked the most is how I did the cutaways. The way I find to be the easiest is to draw a triangle and then use the Sweep function to cut away the body you want removed.
Step 1: Create a new plane for which you can draw a triangle on which is at the end of one of your cutaway lines.
Step 2: Draw the triangle with the point starting at the line edge you want cut away. The larger the angle at the edge you're cutting, the bigger the cutaway will be. In the top cutaway of the body, I used a triangle with a 15.9 degree angle that was just over 3.6 inches long.
Step 3: Use the Sweep command. Select your triangle as the profile, the line you want cut as the path and make sure the operation is set to Cut.
Finally, when you are done with your cutouts, we get to move on to the toolpaths.
Step 2: Setting Up Your Toolpaths
The first step here is to make sure that you have the correct Setup for whatever you are machining. For this build, it was my first time machining a guitar body, so I wanted to go with some cheaper wood in case I ran into any issues. I used 2 pieces of maple which I glued together and tried to bookmatch it as best I could. I came up with a stock piece measuring 20 x 15 x 1.625 inches. I also made sure to set the orientation (origin) of my tool to be in the center of my stock, so I could line it up with the glue line of my body. To simplify my machining, I used the same tool for every cut. For those of you using the Shapeoko, it is the #201 1/4" Cutting Diameter: .250", Cutting Length: .75", Shank Diameter: .250".
https://shop.carbide3d.com/collections/frontpage/p...
From here I created 6 cutting operations for the guitar body which I will describe in detail below:
Operation 1 - 2D Face : This operation cleans off the top layer of the wood and makes sure it is clean across the top of the guitar. I also added a bit of a stock offset which allows it to cut further around the body giving it some additional clearance for the bit, specifically when it does the next Countour step.
Operation 2 - 2D Contour : This is the step that cuts around the guitar, giving it the shape and cutting around the body. For this step, there are a few ways to do it. Some people use tabs in their guitar. I chose to have it leave .25 inches at the bottom. When the full cutting operation was done, I planned to take it to the bandsaw to remove the excess and then hit it with a flush cut router bit to clean up any edges. This is a point of preference really. If you don't have a bandsaw and router, I would opt for doing tabs and cutting them with a handsaw after.
Operation 3 - 2D Pocket : This operation was used to cut out all of the holes for the volume control, pickups and neck hole. Make sure that you set your operation to multiple depths for any deep hole so you're not trying to remove more material per pass than your CNC can handle.
Operation 4 - Drill : This operation cut the 4 holes for the neck screws. This can easily be done with a drill and doesn't necessarily need to be done on the CNC. Make sure the hole spacing is correct for whatever back plate cover you have.
Operation 5 - 2D Procket : This was used to remove the cutaways at the top and the bottom. Make sure to leave a little stock at the bottom so you can have a clean finish with our final toolpath.
Operation 6 - 3D Parallel : This operation is used to finish the guitar top. Since I used a single flat bit, my edges aren't going to be the best and will still need to be sanded down after. I set the stepover so that I would have a ton of passes, which made this machining time quite long, but it did give me a relatively smooth finish on the angles even though I used a flat bit.
Finally, once you are happy with your tool paths, it's best to run a simulation in Fusion 360 before post processing. Fusion does a great job showing you the tool path and walking you through each cut by color coordinating them in the simulation.
At this point, you are ready for post processing and generating your code for the CNC machine.
Step 3: Cutting the Body
So now the fun part, actually cutting out the guitar. My method for securing wood onto my CNC when it's this thick is blue painters tape and super glue. I put blue painters tape on the spoil board, and some on the back of the piece I am machining, then I glue them together. It provides a really strong hold and there is no hardware to get in the way. It's especially useful when I am cutting thicker pieces of wood, where the clamps could easily get in the way of the router bit.
Once the body is secure, I centered my tool on the middle of my stock and hit go in Carbide Motion. Carbide Motion is the program which tells the Shapeoko what to do. To give you and idea of how long it took, here is the machine time on each operation:
Operation 1 - 2D Face : 21 minutes
Operation 2 - 2D Contour : 38 minutes
Operation 3 - 2D Pocket : 29 minutes
Operation 4 - Drill : 1 minute
Operation 5 - 2D Procket : 45 minutes
Operation 6 - 3D Parallel : 1 hour 22 min
Observations: Overall, I was pretty happy with my first try on this. I would definitely change the design a bit as well as adjust the toolpaths. I didn't need to have such a fine stepover with the parallel pass which would decrease my cut time significantly. Also, my parallel oolpath depth went over my edges and created small grooves which needed to be sanded down. You can see it in the pics attached. It was fine after sanding, but creating additional finishing work.
I also made sure to do a quick dry fit of all of the parts and they fit like a glove. Now to the sanding, staining and finishing.
Step 4: Sanding, Staining & Finishing
Some people might think that a CNC machine is cheating, or that it's going to spit out a finished guitar, but there is still quite a lot of work to do after you get the guitar off the Shapeoko. For the sanding, I used an orbital sander and started with 100 grit just to clean up the burs from the flat bit as well as those grooves from the parallel pass. Next I took 220 to it to get it nice and smooth. Finally I took a pass at 320 to get it ready for stain.
I went with TransFast Burnt Sienna dye. It's a water based dye and comes in a concentrate form. To get them ready for this type of dye, you want to raise the grain first by applying some water, and then sanding it down again using the 320 grit sandpaper.
https://www.rockler.com/homestead-dry-dyes
I cut a piece of scrap wood to fit in the neck pocket and used it as a handle so I could clamp it to my workbench and apply the stain. After the stain was applied and I was happy with the color, I used Behlen Spray Instrument Lacquer. I applied about 10 coats of lacquer over 2 days, but when it was done, it felt great. I gave it a final dusting with some steel wool, and it was ready for assembly.
https://www.rockler.com/behlen-vinyl-sealer-for-st...
I am not going to go much into the assembly in this instructable. I still had to drill a hole in the body for the 1/4 inch jack. I also needed to use a bit to drill wire holes between the pickups and volume cavity. Finally, I used some copper tape on the insides of the pickup and volume cavities before installing the hardware to reduce interference.
Overall, the guitar was quite inexpensive as many of the parts were from Ebay / Amazon, but overall it came out really well. I will call out a few things if you are building your first instrument and lessons learned.
1. Where you mount your bridge is very important. Depending on the neck you put on your guitar, you're going to want to measure the distance between the 12th fret and the nut at the top of the guitar. The 12th fret is the halfway point from where you mount the bridge. From there, you'll want to adjust the bridge after it's installed. You can find lots of information on this online.
2. Pre-drill all of your holes and don't buy cheap hardware. I bought a bunch of cheap hardware and parts on Ebay which is just sitting in my shop now. On this guitar, I broke the head off 3 screws when trying to install different parts. Spend the money and buy good parts. It might look pretty, but the quality will probably be terrible.
3. If you're using a CNC, be careful when cutting some of the really thin pieces and use proper bits. I had some tearaway near the neck joint because of how thin the connection was on the bottom of the body where the neck connects.
4. Join a forum or community if you're really serious. There is a Fusion 360 Luthiers group on Facebook which is awesome and you can find tons of useful guitar building information on YouTube (check out Crimson Guitars).
Thanks everyone and happy making.
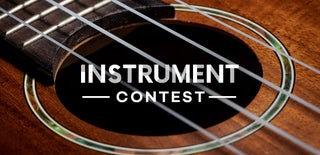
Judges Prize in the
Instrument Contest