Introduction: CNC a Small Footstool
Want to build a kit foot stool in a few hours? This Instructable takes you along the path of using Fusion 360 to design and write a toolpath program for cutout by a CNC machine. You could easily do it using a jigsaw and drill if you wish?
Supplies
600 x 600 x 16 mm mdf or ply
Paint
Good quality cross linked glue
Step 1: Start With a Sketch
There is an image attached that you can import as a Canvas and trace a new Sketch. Simply save the image to your computer. Open Fusion 360, In DESIGN - CREATE - Create Sketch on any plane. Then click INSERT - Canvas. Select the face of a plane you are going to sketch on, then select your image file - OK.
A new item called Canvases will appear in the tree to the left. Open that up and you'll see your canvas named. Right click and select Calibrate. With your mouse pointer select both ends of a dimension shown on the Canvas and enter that dimension. Your image will now expand to match that scale.
Now use the drawing tools to trace the Canvas, then Finish Sketch. I've included a close up of the pockets above. The only problem with a CNC versus a jigsaw is, the CNC can't cutout square internal corners. You're restricted to the radius of your smallest endmill. In my case 5.6mm dia, but adjust the sketch to suit your tooling?
Once the sketching is done use your mouse pointer to select each part to be cutout holding down the Shift key. Then right click Extrude - 16mm - OK. That creates 5 new Bodies. Rename them if you wish?
Step 2: Manufacture
Now select MANUFACTURE from the DESIGN dropdown. Fusion surrounds your stool parts with an imaginary rectangle. We'll assume that you have a piece of 600mm square x 16mm material?
Select SETUP - New Setup A new pop up box appears! An XYZ triad of arrows will appear centred on that rectangle. The red X axis arrow should be pointing East and the blue Z axis arrow pointing right at you? In the Model space click the pointer and then click on your Bodies whilst holding down the Shift key.
Now select the Stock tab from the popup. In Mode select Fixed size box and change the dimensions to whatever size material your using (provided it fits onto your CNC table?). In my case 600 x 600 x 16 mm. OK
Now select 2D from the top bar. 2D - 2DContour. A new popup will appear titled 2D CONTOUR : 2D CONTOUR1
Select a tool from the tools that you've pre-installed in the Tool Library. Not sure how to do that? Then watch this youtube by Winston Moy
I select a 5.6mm dia flat end mill. Disable Coolant. Select Geometry tab. In Contour selection use your mouse pointer to select the bottom edges of all the Bodies. The red arrows adjacent to the blue contours should always be on the waste side of the line. If not just click them and they will jump across the blue line.
While still on the Geometry tab, tick Tabs Change the Tab Shape, Tab Width, Tab Height and Tab Positioning to as shown in the picture. I nominated Tab Positioning as At points? This is where you will nominate the position of the tabs. You don't have to do this. You can simply select By distance in the dropdown and Tab Positions turns to Tab Distance. You nominate a spacing say 100mm for example and Fusion will insert them for you. To nominate tab positions return to your original Sketch right click Edit and insert Points at will. Once complete Finish Sketch and whilst in this MANUFACTURE work space and with the 2D Contour popup selected, use your mouse pointer to click on those points.
Now select the Heights tab. You want to cleanly cut these parts out so a little over cutting will ensure crisp edges. Change Bottom Height to From - Stock top and Offset minus 16.2mm. That's a 0.2mm overcut and best that you sit your sheet of 16mm material on a 3mm waste board atop your CNC bed.
Lastly select the Passes tab. Tick Multiple Depths and I'll change the Maximum Roughing Stepdown to 3mm. This is dependent on the size, type of mill and material you're using? There's a Science just on the subject of feeds and speeds for you to google and arm yourself with the knowledge. Finally click OK and Fusion will generate a toolpath.
To watch Fusion simulate the operation of cutting out your bodies, select ACTIONS - Simulate. If it all looks OK then select ACTION - Post Process and save the Contour toolpath to a file.
Step 3: In the Workshop
I can only assume that you are familiar with your CNC machine and it's Control software. There are so many variations that I can't possibly try to cover all these in this Instructable. Suffice to say that you securely clamp your 16mm material with a sandwich of 3mm waste material to your CNC table. I assume you know how to zero your XYZ axis and load the Contour file? There are many cross checks that you should carry out for both a safety and a production point of view. CNC machines are weapons and can cause you an injury as well as destroy your work piece if not careful. In my series of Instructables, "Let's Build Cubism Gal" Parts 1 to 5, I make detailed mention of these checklists and indeed for me, it ended badly for my model? Things can and will happen that you would least suspect, so take your time.
Once you've cutout your bodies, you need to cut through those tabs with a jigsaw. Now sand the edges and pre-assemble your stool to check that everything goes together OK? Now for some paint and once dry re-assemble the stool. Bear in mind that glue doesn't stick to paint as well as to raw timber! Use masking tape prior to painting to mask the inside of the pockets and male protrusions where they meet face to face to ensure the best adhesion.
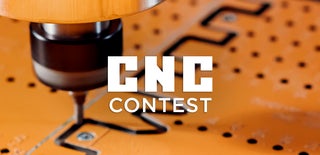
Runner Up in the
CNC Contest