Introduction: Custom Rod Building: Multiple Rod Dryer
Hello Instructables,
Wow it has been a long time since I posted a project. A lot has changed since my last project. I have 2 handsome little boys, I started and currently running a small business in custom fishing rods and repair, I even have gotten sponsored for my rod building craft. It has been amazing. But you know the whole time I have been doing this, I have been thinking about you, instructables.com and the people that are on here. The community here is so special and so I want to get back to sharing my projects. So he we go...
Sorry, the first one back is for those, DIY fisherman, but if you do lure crafting and/or jewelry making, or anything that requires something to be turned while it sets or hardens, then this is for you too. I needed a multiple rod dryer for my fishing rod business, more specific, a 4 rod dryer. It has been a thought for some time now so I decided to build it. Yes, I could of bought it, but I really wanted to try my hand at some easy woodworking and some easy electrical setups. The goal of this build was to successfully build a dryer that would hold 4 rods, have a main on/off switch, along with each rod having their own on/off switch. And yes it was a success.
Step 1: Videos for Those Video Learners
OK, so I thought to myself I need to make a video and a document on this project. So I made 2 lengthy videos explaining the in's and out's to this build. Come along as I show you how I come up with almost everything on how to build this dryer. I wanted you (viewers) to feel like you were there with me brainstorming, how it was going to work. AND you really were right there with me. I had an idea and I really didn't know how exactly it was going to turn out so I took a shot and here it is.
Why are they so long...
I felt, in order to express my passion and communicate the proper steps, I had to make it more hands on then entertaining; therefore longer.
Why is this Instructables so short...
Well because of the videos being so long. This is for those wanting to try a build like this, to be able to come and get the schematics of the supports, bases, electrical, when ever they feel like it.
Follow, Subscribe, and leave some LOVE!
If you are this far go ahead and leave me a follow, subscribe to my YouTube channel, and leave a like and/or comment. I will always get back to you.
Step 2: Components, Cost, Clickable Links
Picture shows what I used and how much, how many, and where I got them from.
Components:
I used 4 synchronous motors (4 microwave turn-table motors) of 15-18 rpms. Yes, you can safely and responsibly remove and reuse motors from a microwave(s). My opinion, my preference for what rpms to use, I like the rpm of my dryers to turn at most 15-18 rpms and at least 6 rpms. I have heard of other builders using around 2 rpms, but for me, that's way too slow. Then on the other side... I have heard builders using 36 rpms, again for me, way too fast. Having too slow or too fast does effect how epoxy/finish will set. Be cautious and test your rpms to make sure they are of your preferred speed at which you want the epoxy to be applied and set.
I used 5 two pong rocker switches. one for the main on/off switch and the rest for turn on/off individual rods. Reason...I do work on multiple rods at one time, but I might have them done at different stages so I wanted the option to be able to turn on/off rods when they are not in use.
When buy or making shaft couples, make sure they will fit the shaft of your motors.
Base material and Caps for Chucks. I went to my big box stores to find these materials. I had a beautiful piece of leftover oak plywood I used for mine. PVC caps were just too expensive over Amazon or anywhere else, but my local big box had a good price.
The hardest part of the components to this build was...figuring out how to get the rods to be self-centered, but rigid enough to hold large diameter blanks. I brainstormed fitness bands, bicycle tubes, rubber-band/bolt method... Then I found it. I found 2 products on Amazon. The first one was these little kids' universal silicone cup caps that are used to stretch over your typical cup, that helps them from spilling and they have a straw hole that was already in the center for easy marking. They are the thicker ones' of the two. The second one are these universal silicone cup caps used for putting a lid on basically any container of around that size. The are clear and very thin compared to the other ones, but I am currently using both of them. To put the center hole in the silicon material on either one, I used a sharpened pipe to cut or punch a hole in the center.
What ever product you decide use, make sure you measure your chuck and get the proper size to them...snuggly.
Cost:
The cost of everything was around $60.00 USD. Obviously, if you had to go out to buy the wood, your cost will be increased. It would probably take about 3-4 hours to make.
Links:
All links are under my video's description. *No I do not have an affiliate account with these companies, so I do not make any profit from you clicking or buying from these links. They are there for you.
Step 3: Supports and Bases
Picturesare of the measurements/cuts of how I came up with the supports.
The stock I used to cut the supports were made from a 10 1/2"x 17" piece of plywood, I cut on the table saw. To cut the curves of the two supports, I used two ways on the video. The first part was cut with a Jigsaw, and the second was cut using a hole saw bit in a drill press. If I could do it over again, I would use the hole saw method.
For reference, I drew a 20" diagonal line from corner to corner at an angle of 58 degrees. If you know the equation for rise and run. 10 1/2" Run and 17" rise comes out to diagonal of 20" at a angle of 58 degrees. From there, I marked the center of each chuck (pvc cap) on that line. See picture for placement. I also made sure I had a 1" cushion on the bottom of the support to make sure the motor would not touch the base. If you use a different size chuck other than 2", then your measurements will be different. Use a compass, to set the diameter of your chucks to mark the board. I set mine at 1 5/16". I would use this to set up my curved rests for the motor stand and support stand.
Bases were cut from the same material. I made sure they were the same width. Now, because I am going to have 4 motors set up on one side of this thing. I made sure put the support board off center to the base with the wider side having the motors. I cut a dado that was the same width of the board used (1/2") for the supports. I cut the dado on the table not using a dado blade, but my regular blade using a Kerf maker.
I pre-drilled all my holes and countersink all my screws. No glue was harmed in this build. Because I used no glue, it gave me the option to break down, or fix any mistakes without redoing the whole build.
Step 4: Electrical Schematics/ Finishing Touches
Picture is the schematics of how I set up and connected all the electronics.
How I set up the wires was pretty simple. I set the motors in parallel so that all motors would get the full 120 volts (US) no matter if one was switched off. If you set them up in series (which you can do) don't bother putting switches on because if the first one is off, they all will be off. Its like those old school X-mas lights. I could of soldered everything, but I want to make it as easy as it can possibly be, to all average Joe's. In my opinion, I think it would of been easier to solder all the connections, but I'll save that for my second one when ever I build it. To conceal all of the connections I made a little junction box with a switch panel on it. To make the wires neat and orderly instead of the hot mess like when I put it together (see video), I used coagulated electrical wire covers. No you don't need them, but I think they make it look a little nicer.
Coat the wood with some kind of sealer and then you'll be done.
Thank you so much for visiting my Instructables and if you like this project. Please vote for it, favorite it, and follow for more projects to come. If you have any questions, please leave me a comment and I will be sure to get back to you.
Follow me on my other platforms:
YouTube: CASST'ONE
Instagram: casst_one
Twitter: @casst_one
Facebook: @Casst1customs
Step 5:
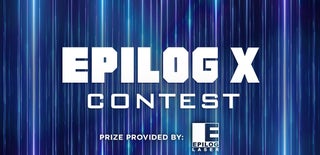
Participated in the
Epilog X Contest