Introduction: Doughnut Safe
Step 1: Getting Started
I thought about this project for a couple weeks. Normally I have an idea about what I'm going to do before I do it. This time I wasn't getting anywhere with my thoughts. So I decided I would just have to start building it. Whatever the design I knew it had to have a lid. I started with that.
To get a solid measurement I placed paper over the rim and traced it with a crayon. You can find big rolls of this paper in the painting section of home improvement stores. Next I cut it out with scissors. Now I had the right size but I still needed a measurement for material thickness. For that I laid a piece of flat bar across the rim and measured the gap with calipers. ¼”.
Legal Note: There are jurisdictions which have hidden compartment laws. More or less they read like California's statute below. The major factor here is your intent with this compartment. All law enforcement officers are trained in vehicle searches. Locating this would be routine for them. If you use this or any compartment to conceal a controlled substance (even empty a K-9 will alert on it) you may be the winner of an extra felony charge.
California Health and Safety Code Section 11366.8
11366.8. (a) Every person who possesses, uses, or controls a false compartment with the intent to store, conceal, smuggle, or transport a controlled substance within the false compartment shall be punished by imprisonment in a county jail for a term of imprisonment not to exceed one year or pursuant to subdivision (h) of Section 1170 of the
Penal Code.
(b) Every person who designs, constructs, builds, alters, or fabricates a false compartment for, or installs or attaches a false compartment to, a vehicle with the intent to store, conceal, smuggle,
or transport a controlled substance shall be punished by imprisonment pursuant to subdivision (h) of Section 1170 of the Penal Code for 16 months or two or three years.
(c) The term "vehicle" means any of the following vehicles without regard to whether the vehicles are private or commercial, including, but not limited to, cars, trucks, buses, aircraft, boats, ships, yachts, and vessels.
(d) The term "false compartment" means any box, container, space, or enclosure that is intended for use or designed for use to conceal, hide, or otherwise prevent discovery of any controlled substance within or attached to a vehicle, including, but not limited to, any of the following:
(1) False, altered, or modified fuel tanks.
(2) Original factory equipment of a vehicle that is modified, altered, or changed.
(3) Compartment, space, or box that is added to, or fabricated, made, or created from, existing compartments, spaces, or boxes within a vehicle.
Step 2: Cutting Circles
Since the design was up in the air I made sure to use MDF for the prototype. It is much easier to work with than steel.
I knew there was two ways to cut this circle out. One, I could do it freehand and hope it looked clean. Or two, I could use a simple woodworkers trick. I chose two. I screwed a plank of wood to my scroll saw table and used a nail as a center point. I stuck that nail through the center of the circle and into the plank. Once everything was in the right position I rotated the material until it cut out the circle. Because of the flex of the scroll saw blade, I had to do a second run to trim it to the proper size. You can see what I’m talking about in the first picture.
Now I had a lid for the tire but I still needed a way to keep it locked down. This was the tricky part. Of course an easy solution would be to just have a pin come up from the center of the tire and through the plate but that would obstruct the storage area. I knew the locking action had to happen around the circumference. So, moving forward without a clue, I cut another circle for the bottom plate.
Step 3: Laying Out Holes
I was still stuck on how to lock this plate down but I knew there were two features that were going to be included regardless. The first being I needed holes in the bottom plate to mount it. The second was the lock and key would be centered on the top plate. With that in mind I moved on hoping to connect the dots along the way.
I drilled holes in the bottom plate to match up with the lug holes on the rim. These were 100mm apart. I drilled a single hole, centered on the top lid, for the lock and key.
While the holes looked nice they still didn't do much. So back to figuring out how to get this locked.
Step 4: Fitting the Side Supports
I had to balance this part between the tools I have available, and the materials I had on hand. At first I thought I would take a wide band of material and line the inner circumference of the rim. I would then attach that to the bottom plate. The problem with that is it takes up space around the entire perimeter the storage area. Space which is already at a premium. Also, how on earth would I shape that width of material myself? At a minimum I would need two points to lock the top plate down. Though, with only two points it makes it that much easier to pry the plate off. I settled on four points.
For each point I used aluminum flat bar and bent it at 90°. I left a couple inches on one side for rivets. I cut out notches around the circle so the flat bar sat flush in the circumference.
Step 5: Peening Rivets
If you ask me there's something therapeutic about setting rivets. Especially when doing it by hand.
Before setting them I had to drill holes. It's not necessary to lay out every hole precisely. As long as you keep each support in the same spot you drilled it, it will line up just fine. Normally I would use a rivet gun but mine is broken at the moment so I used ball punches. A smaller gauge started the flare and a larger one expanded it flat. To finish it off I hammered it with a ball peen hammer.
Step 6: Cutting the Center Disc
By this point my thinker's block had cleared and I got the idea to use four retractable pins for the lid.
I knew the amount of travel in the pins was related to their distance from the center of the rotation point. I figured a little more than an inch would be plenty of travel. Luckily I had a container in my garage that was the perfect size (PVC pipe glue). I traced that shape on 22 gauge sheet-metal and cut it out with shears. I placed the disc in my drill press and used sandpaper to clean up the edges. Hobby files nicely cut the square hole needed to fit onto the locking mechanism. Measurements for this disc can be found in step 13.
Step 7: Fabricating the Locking Pins
Now I'm ready to make the locking pins but I don’t have materials. At this time of night no stores are open to buy any. I used what I had and sacrificed aluminum tent pegs.
I cut off the hooks with my scroll saw to start. Next I heated the ends with a torch. This made it easier to hammer the ends flat. These flat surfaces created a place to drill holes. Once I trimmed them down to size I rounded each over so they would fall into position easier.
Step 8: Putting the Mechanism Together
I wasn't exactly sure about the positioning of the pin guides but I knew I had to have them an equal distance apart. So, I cut more aluminum flat bar, and bent each part at 90°. I riveted them into place by hand. Now, I did think far enough ahead to know the position of the guides had to correspond with the 90° range of motion for the locking mechanism. It was also important to place the guides as close to the edge without the the pins falling out when retracted.
Figuring out how to attach the pins to the center disk wasn't too bad. At first I placed screws through each pin and attached them to the disc with a single nut. That setup allowed too much play, leaving them wobbly. To fix it I mounted the screws with one nut and then mounted the pins separately with another.
I cut the screws with wire cutters and filed them flat. To keep them from loosening I used an automatic center punch to lock the threads. See the last two pictures.
Step 9: Trunk Mount
This was the easiest part of the whole build. But I do have to give credit to necessity. When I was thinking about what method to use to mount the tire I stumbled across a stainless steel rod I had in one of my drawers. This was really the only thing I had at the moment so I figured out how to use it.
I drilled a hole through two bolts and slid the rod through. It worked great. To clean up the part I machined the ends round on my lathe.
Step 10: Locking Ring
My original thought was when you turn the key the pins would throw out and go into holes drilled into the side supports. It turned out to be especially difficult to get each pin to line up with its corresponding hole. What a bummer to turn the key and it only turn half way. I also thought if I cut slots in the lid the supports would line up and so would the pins. That didn't work but it did give the idea to include slots in the final design.
I needed to figure out a better way. A way for the pins to catch every time you turn the key. I turned back to the same shape I was working with for the solution. The circle.
I thought if there were a ring connecting each support it wouldn't matter where the pins fell. So, I took three strands of wire and twisted them together. I then formed a circle and soldered it closed. I attached the ring to each support by crimping it in place with a wire.
It worked! Finally the excitement of a proved concept. The lid locks and the base mounts in the trunk. The only problem is you could probably pry this apart with a popsicle stick.
Time to call for reinforcements. AutoCAD.
Step 11: Drawing It Up in Autocad
Laying out these locking plates is a pretty simple task on AutoCAD. If you're not familiar with how AutoCAD works you can click on the circle button, type in a diameter, and press enter. Easy as that it draws right up. The rest of the layout is a matter of making the corresponding shapes and putting them in place. Afterwards, I used the trim tool to remove sections of shapes like I did on the edges of the locking plate. The offset rectangles in the larger plate help the welding process in step 18. I included the files in DWG and DXF to make it easier for anyone wanting to use them.
I sent this file to a local laser cutter and after about a week and a half I finally got a call to pick them up. Getting them was exciting and nerve-racking. What if it didn't work? I didn't want to have to wait another week and a half to get a second set of plates and I had my fingers crossed all my measurements translated correctly to real life.
The top plate fit perfectly. The bottom plate stopped once it came in contact with the curve of the rim. I did make a good effort to get a proper measurement though so I knew if I removed the corner around the circumference of the bottom plate it should fit right in place.
Step 12: Removing the Edge
Even though I had a nice big file, rounding over the edge would have taken a lot of time. I wouldn't recommend this but this method actually worked pretty well for me. First off, flying metal pieces are no joke. If you get one in your eye you can suffer permanent vision damage.
As a precaution I used two layers of protection. A pair of swimming goggles under ANSI approved safety glasses. After cutting the chamfer I rounded over the edge with a file and smoothed it out with sandpaper. The fit was close but it wasn't bottoming out just yet. I used a feeler gauge to go around the edge of the plate and marked every high spot. I went back over those spots with a file.
If you look at the last picture you can see the curve that prevented the plate from falling into place.
Step 13: Fitting the Side Supports Take 2
For the second time around I used steel flat bar instead of aluminum. Now if the supports went straight up we would lose the space that flares out at the top of the rim. To better match that shape, I stuck the flat bar in each recess and bent it out towards the edge. To mark the cutting point of each support I laid a piece of flat bar across the opening and used a sharpie. With a hammer and chisel I scored a deep line and separated each piece by bending it back and forth a couple times.
I prepped for welding by cleaning up the edges with a flap wheel.
Step 14: Learning to Safely Weld
I needed to tack weld the side supports into place. The best way to do that was with the setup inside the rim. The problem is in welding near compressed air. There is a chance the air will expand enough to explode the tire. I knew the risk was probably pretty low with tack welding but I didn't want to take any chances.
I removed the valve stem from the rim allow for any air expansion. The last thing I wanted was an exploding tire. Once the tack welds were in place I removed the plate out of the rim and did a solid bead on every support. Next I welded the underside and filed each bead flush.
Step 15: Rolling a Ring Without a Ring Roller
This part was a challenge. I didn't have a ring roller but I wanted a ring as close as possible to a perfect circle. For my first try I wrapped 1/4" metal dowel around the outer edge a brake rotor. That circle was too big. On my second try I welded the rod to the inner hub of the rotor and wrapped it around again. This time diameter was too small but I could handle that.
To expand the circle I placed the ring in my vice. I closed the jaws until it started to expand the ring. I moved the ring through the vice, opening up the curve enough so it would slide through the jaws. I did this until the entire ring was the shape I needed.
Now I don't have many specialized tools but the one you see in the 7th picture is one of them. It worked out great in holding the ring closed while I welded it together. Once I had the ring formed I flipped the basket over and welded it on.
Step 16: Center Disc Take 2
On the first disc, after I used files to cut a square in the center, I drilled the holes 90° apart. The problem was the holes were drilled off the corners of the square. This was fine when I could put the pin guides wherever but when they are cut inline with the key hole they have to be cut along the edges of the square.
I had to make a new one. This time paying better attention. I used the same container for the circle and refined the shape on my lathe. I use a center punch to mark the holes and drilled them out with a 3/16" inch bit.
Step 17: Cutting the Pins
The prototype used 20 pieces total for the center disc and locking pins. That included the nuts and bolts to attach them. To reduce the amount of hardware to 8 pieces, I decided to tap threads into each pin.
This is the point I decided I needed the pins to be thicker. It was necessary to make it more difficult to pry open the safe. I increased the pin diameter from 1/4" to 3/8”.
I used the same chisel and hammer method for cutting. I cleaned up all the edges on my lathe.
Threading everything was simply a matter of drilling holes and running a tap through them. Don’t forget to use oil to help the tapping process.
Step 18: Fitting the Pin Guides
On the prototype I used 3/8" holes in ¾” flat bar with a ¼” pin. When I increased the thickness of the pin I had to increase the hole to ½”. If I didn't, there wouldn't be enough play to allow the pin to move back-and-forth. The problem is the ¾” inch flat bar would only have an eighth inch of material on each side after drilling the ½” hole. I don't know the exact tensile strength for steel this thin but I wanted it to be stronger. My solution was to double up the flat bar by folding it in half. I did that with my vise and a hammer.
To properly position the height of the guides I rested the pins on the locking ring and tack welded each tab in place. Their position on the plate was easy to locate because a slot was already laser cut for them. After tack welding, I welded each guide from the top of the plate.
I could have grounded the welds flush but I like the look of it all. It kind of reminds me of a manhole cover.
Step 19: Final Touches
There's a lot of little touches that tie this all together. One of the things I did add a small bevel to the end of each pin so it would slide under the locking ring easier.
I also added Loctite to all the bolts that attach the pins to the center disc.
I ruffed up the plates with a sander so the coatings would stick better. The top of the upper plate was sprayed with rubberized undercoating. Everything else was spray-painted black.
The last thing I did was drill a couple holes for a paracord handle. I went back-and-forth on whether I should make a metal handle. I decided on parcord because it's strong but not so strong it could be used as a prying point.
Step 20: Installation
To get a good idea on the installation click on the video in the intro.
When I measured the side supports I did it so the locking ring would sit at the very lip of the rim. However, when I dropped it in the rim, the ring sat lower than the lip. This kept the pins from locking out. The only thing I can figure is when I welded the side supports on, the plate contracted from all the heat allowing it to sit further in the rim. In either case, I had to raise the basket so it would lock properly. That’s why in the video you see me place a spacer between the rim and bottom plate.
Thanks for reading.
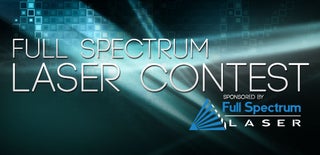
Third Prize in the
Full Spectrum Laser Contest