Introduction: Ford Mini Glovebox Guitar/ukulele
Stuck in traffic?
Bored with nowhere to go?
Nothing on the radio?
Passengers complain you smack them in the face with the head stock when you play a full sized guitar in the car?
Not enough room in the car for a grand piano?
Reach over and grab your Ford half size guitar/sopranino ukulele and play.
The rough idea is you take a box add a stick, and some strings and it makes noise. The rest of the details are a bridge in the right spot to make it sound louder, a fingerboard (aka fretboard) and frets and a nut (really the zero fret) to allow you to play extra notes more accurately, tuning pegs to allow you to tune it and the rest is finery of the sort to make things work better.
I have refined my method a bit since writing this instructable so I have added a few edits;)
Step 1: First Find a Suitable Tin
First find a suitable tin or box then decide of what scale length you think you can get out of a tin or box that size.
To do this you take a length of suitable wood for your neck. I tend to allow about 60 or 65 mm from the base and then double the remainder of the length of the tin plus an allowance for the bend out of the lip of the top will give me the minimum scale length, unless I decide I can make do with only 10 frets that is. Going larger of course just adds length to the neck and frets that you can show off on.
This one is getting a 272mm notional scale length which becomes about a 275mm real scale length once the compensation for bending the strings as you push them down into the frets is taken into consideration. This will give me roughly 12 frets to the body, which is a full octave.
After that I add about 120mm for the head stock and cut it off.
Step 2: Remove Some of the Neck Stick to Give the Top Some Room to Vibrate
Now we remove some of the top of the neck stick from the bit that is going to be inside the box so that the box has room to vibrate. Only the middle section of the top needs to vibrate so I tend to leave a little at either end where the neck joins the box intact. On larger boxes I might leave a small central section as well to help prevent the top from sagging in. Where the lid is particularly floppy I have had to go back and glue an extra support in.
The placing of the extra support should be 30mm (an inch) or so up from the location of the bridge.
I cut a few slots with my trusty Irwin Japanese style saw and removed the waste with my chisel. It doesn't have to be much, 5mm or so is fine.
Step 3: Make a Head Angle
Just before I started doing the head angle I cut my side cheeks, from the same material as the neck. Didn't need to do it right now but it had to be done some time.
Conventional wisdom states that the head angle on a guitar or ukulele should be around 15 degrees for a peg through design and about half that for a slotted classical guitar style head. This is a peg through design so we get a 15 degree angle.
To ensure I get an accurate cut I use the set square as a saw guide, holding the square at the correct angle, along my pencil line and run the saw along the side to get an accurate start.
Because this join is at an angle if we just glued and clamped together the ramp would slide apart. To stop this happening I glued them together and while the glue was still wet I clamped the two pieces to a melamine coated shelving off cut but if you don't have one of these you can use plastic or baking paper on a regular board. Now the two pieces were prevented from sliding apart I added the clamps to hold the two pieces firmly together. In the past I have just used a temporary small nail or drilled holes and added toothpicks which I left in to prevent the sliding.
In the last two photos I show how I tend to do it now. I held the pieces temporarily in place sideways using a spring clamp then add two staples and clamp firmly. The staples come out later. The staples can be hard to get out from some hardwood and I don't want them in there permanently (they damage my tools) so I use the side clamp method when using hardwood necks.
Step 4: Add Reinforcing Blocks to the Tin
While waiting for the headstock glue to set I decided to be productive and add the reinforcing blocks to the tin. Use the cheek blocks to hold a small wood off-cut at the right height. mark with a pencil and cut it off. Place the resulting block in the tin and bend it with your fingers neatly over the block. This tin has a rounded edge on it so I used my pliers to flatten that. A short process of pushing the recessed bit of tin down to the reinforcing blocks so the the top of the tin is level when a straight edge is held across the top. The reinforcing block you just cut now may have to be trimmed by a mm or two to fit snugly under the bent down tin lip. Double check everything.
This process creates an air gap either side of the neck which serves as a sound hole. If you want to make a sound hole in the face of your instrument you have to take into consideration covering the sharp edges it will leave. I have used brass tarpaulin grommets to do this and I have seen others use cupboard vents and larger grommets used for curtains. I have seen pictures of one bloke who spent ages firstly putting in a reinforcing plate and then bending back the edges over the reinforcing plate to remove as many sharp edges as possible.
The rear block is made in a similar manner but to create a slight neck angle the block is made slightly large so that the base of the neck would sit marginally higher (4 or 5 mm or around 3/16 inch) than the top of the tin. This is trimmed off later. This neck angle increases the height the bridge needs to be and hence the angle at which the strings have to bend going over it. This increases the downward force onto the box top, helping sound transfer and stopping it from wandering.
Now I glued both blocks in with epoxy though other glues such as building adhesive or polyurethane glue work as well. Basically any glue that works on metal and wood. Using another piece of off-cut I cross checked everything still lined up.
In this build the front lip of the lid was bent out to accommodate the neck. This works quite well on rectangular boxes and does not disturb the safe rounded edges.
Step 5: Improved Method and Notes for Circular Tins
For a slightly improved fitting experience and to include notes for circular tins I have added this step using a circular tin, though the relief cuts make for a more relaxed fitting experience on square and rectangular tins as well. Not having relief cuts causes the side of the tin to bow outwards as the edge is bent over the reinforcing blocks.
Similar to the earlier version I use some offcuts to make reinforcing blocks using a support inside the tin the same thickness as the neck wood. Marking the curve of the tin is relatively simple by keeping a pencil line roughly parallel to the edges supported by a finger. Cut it to length and shape it to fit the curve. Make a similar block for the rear only a few mm longer than the front block you just made to give a neck angle.
Place it inside the tin and make two relief cuts a short distance apart, no wider than the neck wood. With a decent pair of tin snips this is simply a matter of holding the reinforcing block in place with your fingers and resting the tip of the tin snips down on the block and squeezing your fingers. Cut off some of the rounded over part of the top edge of the tin so it doesn't get in the way or flatten it really well with a strong pair of pliers.
Push the loose bits of tin down over the reinforcing block and tap gently to flatten the neck cutout space without deforming the rest of the tin. Because tin has a bit of spring back in it for a really snug fit remove the block and push the cutout tabs down just a touch beyond 90 degrees so they actively pushed down on the reinforcing block slightly.
Check the neck will be level with the top when inserted using a straight edge and that the lid still goes on.
Then glue the reinforcing blocks in place. This time I used a polyurethane glue.
Step 6: Deforming a Circular Tin Lid
If using a circular tin bending the lip of the lid out without putting in relief cuts causes the lid to deform so that it becomes difficult to fit. Here I put two initial relief cuts either side of the neck making sure the lid was in the alignment I wanted to mount it in. I made another couple of relief cuts to allow me to keep the curve at the top but this was not really necessary.
Then the rolled over edge is cut off and the tabs bent in and squeezed tight. I used to add a drop or two of super glue here to minimise rattles but I don't think it is necessary. What is important is to fold the outside corners over at 45 degrees towards the inside of the tin to keep sharp edges way from inquisitive little fingers.
Step 7: Add Some Side Cheeks
Once the headstock glue has set we can undo the clamps and sand down the sides ready for the side cheeks. The two bulldog clips at the top are just to hold the pieces in alignment. and hold things together while I grab the clamps I need to clamp it together.
Step 8: The Face Plate
Now I flattened the face with my trusty sanding block.
While not 100% necessary I like to add a face plate. Getting thin wood and getting wood thin is sometimes difficult and frequently expensive so here I just took another little bit of that 2 by one dressed meranti and cut it in half down the middle with my trusty Irwin Japanese style saw, glued it to the top of the headstock and shaved it thin with my trusty planes.
Step 9: Check Everything Still Goes Together and Shape the Headstock
Now we check everything goes together and still looks like it all lines up.
This headstock shape is nice and simple so I use it a lot. For more elaborate shapes use the search engine of your choice using terms like "Headstock stencil" though if you want something fancy try "banjo headstock stencil".
The above shape is drawn with two vertical lines along the line of the neck, two points about 15mm out and 30-45mm up give you the points at the sides a line from one to the very top and to something a fingers width or so down give you this shape. I like to make the top bit slightly curved as well. I think it looks fine and is easily cut with a straight handsaw.
Step 10: Cut Your Fretboard
I have a home made fret board duplicating jig that uses a commercially cut fretboard as a pattern for me to duplicate the fret locations on a pre-cut fretboard. It is simply made by cutting a U shape made from 3 bits of wood (or 2 bits of wood and a bit of MDF in my case) at right angles and putting a bit of snap off razor knife at the bottom to lock into the frets of the existing fretboard, which ensures that the frets I then cut in the top fretboard duplicate the ones in the bottom. Many fret slotting jigs go to a deal of trouble to ensure the depth of cut is uniform and deep enough for the fret tang. I now use the startlingly simple method of stopping when I can no longer see light through the bottom of the saw teeth. The saw I use is a standard dovetail saw.
One of the magical things about fret boards is that if you start one fret down you have a fretboard that suits a guitar with a length on fret shorter. Most guitarists will be aware of the use of the Capo which is a non- permanent application of this principle. In this case I used a standard 648mm scale length 26 fret fretboard given to me by Big Stan at Bilinudgel woodworks https://www.facebook.com/BillinudgelWoodworks By starting at fret 15 I had a fretboard that was a notional 272.45mm scale length.
At the top of the fretboard I make a small recess to put the nut in. All a nut is is a zero position fret which has slots in it to hold the strings in place, but now I have lectured you about capos and how I use the regular fretboard to make my much shorter one you probably knew this already.
If you were paying attention you would have noticed that 26 minus 15 is 11 and that this leaves me a with a fretboard with one too few frets on it for a standard 12 fret ukulele fretboard. This is easily overcome by making a mark at 136.225mm using my vernier calliper and a sharp knife. Pencils are fine for most work but a knife cut using an exacto knife or scalpel or something similar gives a much finer line exactly where it should be. Using the set square as a guide for cutting is an excellent tip that keeps the cut accurate and square at the same time.
Ways to mark out fret spacing for any length of fretboard is to use the fret calculator at
http://www.stewmac.com/FretCalculator
or print out a template from
http://www.ekips.org/tools/guitar/fretfind2d/
If you are going to use the fretfind2d page you have to make sure you print your PDF at actual scale because Adobe reader defaults to shrink oversize pages which gives you an accurate scale, just a little shorter than the one you thought you were printing.
Most of these tips I got from the cigar box nation site
http://www.cigarboxnation.com/
Step 11: Cross Check Every Thing Aligns and Attach Fretboard
Cross check everything fits together still and that the neck angle is sufficient to ensure that there is a nice space (5-10 mm) for where the bridge is supposed to go. The end of that part of the neck should be trimmed level with the box and the middle of the neck in box section needs to be a few mm lower than that to give the top room to move. The neck at the entry to the box should finish level.
I was able to trim just a smidgeon off the end of the neck where it was to join at the bottom of the box- about 6mm (1/4 inch).
Now cut the fretboard to length. I like to have a bit of fretboard overhang to hold the top of the tin down, but this is not 100% necessary.
When gluing the fretboard to the neck I like to put in a couple of nails to stop it sliding around these go in through the fret slots so that the holes will be covered by the frets.
To clamp the fretboard securely I like to use a strip of bicycle tube as an elastic, others use surgical tubing elastic or just use lots of regular clamps.
Step 12: Put in the Holes for the Tuning Pegs, Thickness the Headstock and Shape the Neck.
Before you make your holes for your tuners and thickness the headstock you need to know which tuners you are using and how much space they need (on the back as well as the front). Here are 4 examples
Top left needs a headstock about 16mm thick, an 8mm hole all the way through and an 10mm hole at the underside about 10mm long (it is really a guitar tuner but they are cheap and really really good.)
The bottom left needs a headstock about 15mm thick and a 6mm hole with an 8mm hole for the ferule at the top. Both left hand tuning pegs need to be about 12mm from the edge of the headstock.
The two on the right need a headstock about 10 - 12 mm thick and a 5mm hole with an 8mm hole for the ferule on the top one and a 7mm hole for the ferule on the bottom one. I am using the tuning peg on the top right.
I use a cordless drill to make the small hole first and then run my drill in reverse to wear down the hole for the ferule (or base in the case of the tuning peg on the top left). This minimises tear out and keeps things relatively centred. I admit that sometimes I need to adjust my holes with a small needle file to centre them sometimes. Some people like to drill the hole for the ferule first and then drill the rest of the way with a smaller drill for the shaft. I have also seen people drill the same size as the ferule the whole way through, which works for some tuning pegs but not others.
To minimise "grinding" I first cut the headstock with my trusty Japanese style pull saw till it was within a couple of mm of the final 12mm I was looking for. Then I just ground this down with some rasps and sandpaper. I have also used chisels to do this sort of thing and am beginning to think the chisel method is better.
Now I trimmed my fretboard even with the sides of the neck using mainly my small plane but also the ultra sharp Kiwi brand "seeding knife". All the Asian grocers round where I live carry kiwi brand knives, which are the sharpest knives I have ever purchased, but I have only seen these seeding knives at one of them - they cost me $1.85 each and they are ideal for whittling because they are hollow ground on one side and flat on the other, giving a perfect curl on fine shaving.
The next implement of destruction I am recommending is the pink handled kiwi brand vegetable peeler. They are a little more expensive at $4.95. It works as good as any spokeshave, if not better. Together with the seeding knife I shaped the neck roughly within a few minutes.
Step 13: Make Fret Marker Dots and Add Them and Smooth That Fretboard
The fret marker dots are traditionally made from mother of pearl, which is oyster shell and I like to eat oysters. A set of diamond core bits set me back ten bucks on ebay. This gives me roughly an infinite number of free fret dots from leftovers when mother of pearl dots from a luthier supply company are not.
Using a brad point bit drill holes in scrap and check your dots fit then drill appropriate holes in the traditional third, fifth seventh and twelfth fret positions.
I glued mine in with superglue.
Now use some fine sandpaper glued to a dead flat board to flatten and smooth that fretboard because once the frets go on the flattening game is over.
Step 14: Add the Frets and Make Them Smooth
Now we go over all our fret slots with the saw to clean them out and double check the depth. Remember that no light showing under the teeth trick.
Fret wire is hammered in with the soft face mallet and cut flush with the pincers. Then the ends are filed flat against the fretboard and then they are filed at an angle. A bit of fine sandpaper held in the fingers will take the sharp edges off.
A quick check and tap flat of any high frets followed by a long sandpaper covered board really does make them a uniform height.
Step 15: Decorate Your Headstock and Add a Nut
Decorate your headstock and add a nut.
I drew on my design in pencil on masking tape and burned through using my soldering/wood burning iron. This gives me the added task of removing melted glue on the face of the headstock from the masking tape using a pencil eraser.
A drop of superglue and a short bit of melamine chopstick makes the nut.
Step 16: Varnish, Dry Fit, Last Minute Trim Glue and Screw
Do a dry fit and any last minute trimming
Measure and pencil marks to center everything - measuring while gluing is slippery and messy and no fun
A bit of epoxy and some screws to hold it all together I glue and clamp then add screws - epoxy to tin is not very reliable.
Step 17: Sand a Nice Shape to the Nut and Cut String Slots in It
Sand a nice shape to the nut the height does not need to be too much higher than the frets (a mm or so).
Mark out your nut and cut string slots in it I use a handy junior hacksaw and then shape the slots some more with the edge of a half round needle file.
See my instructable Poor man's nut and bridge string spacing guide.
https://www.instructables.com/id/Poor-manhttpwwwin...
Or use a ruler.
Step 18: Align and Add Your Tail Piece
Lay down some masking tape and use a straight edge to make some alignment marks for the tail piece.
This tail piece is made from a picture rail hook. On other ukes I have used decorative hinges as well.
As you can see from the photos 2mm holes are drilled and tidied up/ deburred with a larger drill bit. A small file is used to take off any remaining sharp edges.
Step 19: Measure How Big It Needs to Be Then Make a Bridge.
Using a straight edge and a judiciously marked wedge and add in 6 mm I made a 14 mm high 4 or 5 mm thick, bit wider than the fretboard piece of wood.
40 grit sandpaper does the rough shaping and the rest is tidying up. 4 evenly spaced slots and using a hole in the workbench and a half round file puts a nice bridge shape into it. A coat of shellac finishes the job.
Step 20: Add the Tuning Pegs and Strings
Now we add the tuning pegs and some strings
As you can see there are a few components to this tuning peg that put it a level above the ultra cheapest but it is still a friction tuning peg and they do take a little time to bed in, on top of the time the strings need to bed in. The strings are tied on with basic fishing knots, the one I used was the Pitzen knot http://www.netknots.com/fishing_knots/pitzen-knot but feel free to try your own.
Because I have a 275mm (approx) line length and am tuning all the way up to octave over guitar I have used 40, 60 , 50 and 30 lb breaking strain line for the D5 G4 B4 E5 strings respectively. That is 2 octaves above a standard D string on a guitar and one octave above the G B and high E strings respectively.
Because these floating bridges are known to get bumped about a bit it pays to put a mark where it should go.
Step 21: Fine Tune the Action and Play It
Fine tune the action by measuring how high the strings are from the first fret and the last fret
The before measurements show just over 1 mm at the first and nearly 4 mm at the 12th fret.
Deepening the string slots on the nut and sanding a little off the bottom of the bridge reduce that to just under 1 mm and around 2.5mm at the 12th fret. The difference is called the relief because the strings vibrate more in the middle than at the ends. This makes it play much nicer, though to tell the truth I was not that unhappy with the before numbers either.
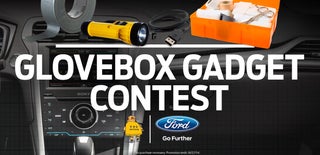
Participated in the
Glovebox Gadget Challenge