Introduction: 999. Fine Silver Heart Pendant From Clay!!!
Aloha fellow creators,
Wouldn't you love to start making amazing silver jewelry but ya ain't got time to learn. Wanna forge sophisticatedly designed silver rings but ain't got the money to pay for the schooling? Well I'm about to show you how to create this breath taking .999 silver pendant with a few easy steps. "How easy?" you ask? Lets just say after a week of research I was able to create a similar pendant without instructions or experience. Now the price point for the silver might be a bit steep for beginners, but I'm sure once your finished you'll be happy you invested. So I get it, now a days your dollar doesn't stretch as far as grand papi's did. But trust me, after a few projects you might even be able to make a good business off these bad boys.
Step 1: Know Your Sh!*
So research has always been a good friend of mine. We go way back to grade school days. So make good friends with her cause every bit counts. Watch a few youtube clips and read a ton of online articles. Maybe I even dabbled in some light book reading. All in all this instructables is designed to help you skip past that. But if wanna take this a few steps further than I suggest you know your sh!*.
Some light info on the Silver you'll be using for the project...this stuff starts off as clay yo!!! Hence the Silver Alchemy title. Yup, well sometime in the 90s some Japanese scientist end up mixing tiny silver particles with organic plant matter/binder and a bit of h2o to create PMC!!! PMC stand for precious metal clay and after you've formed and dried it you'll need to "fire" it at a temp of at least 1200°F before it "sinters" in to .999 pure silver. Easy stuff right? Well kinda...
Very important note!!!! You will be using various tools that require basic handling skills such a knife and torches. I will assume no responsibility for injury that may occur during your project. That being said, have fun and be safe!
Step 2: Gathering the Supplies
Like any project you'll need a list of tools and supplies. First things first, order some PMC!!! For this project I used PMC3 which I bought on Amazon for $120 for 50g. It took a few days to ship to me so I had some time to gather a few more supplies listed below.
X-acto Knife
Sand paper 400 and 800 grit
olive oil
small butane torch
clear wrapping plastic/ plastic wrap will do too
Fire/kiln brick
scissors
photo paper/thick paper
playing cards
pocket mirror with textured design
steel wire brush
liver of sulfur patina gel
baking soda
renaissance wax
silver jump rings
silver box chain
airtight container for opened PMC3
paintbrush
stir stick/ chopstick
String
needle nose pliers
acrylic rolling pin
PMC3
P.s. also used some needle files and dremel bits but these are optional
Step 3: Phase 1: Shaping
After you got all your supplies organized your ready for some action. Start by taking a piece of photo/ thick paper and folding it in half. Now proceed with drawing half heart along the crease and cut it out with a pair of scissors. When you open the cut and folded piece it should resemble a heart thats around 2in diameter. This will be your template for cutting your PMC pendant so make sure its nicely cut.
Next off cover your cutting surface with some plastic wrap. I use some clear christmas wrapping plastic because its thick and reusable. simply dab some water on the cutting surface and adhere the wrapping plastic as pictured. Take some olive oil and smear a bit on the plastic wrap so that the clay doesn't stick to your cut surface. Now take 10 cards and split them in half, arranging them 5 on each side. This will gauge how thick your clay will be rolled insuring an even ratio. Make sure to leave a small space in-between for the clay to be rolled.
For this next step you'll need to be ready to work fast as the clay will begin drying quickly after being exposed to air. So oil your hands up a bit and open your bag of PMC3. Take out a small piece the size of a marble and store the remaining clay in an air tight container. Begin by kneading the clay in your hand a bit to warm it up. This will help with the pliability so that it'll roll out nicely. Take the freshly kneaded clay and slightly squish it a bit laying it in the middle of the cards. Oil your rolling pin a bit and evenly roll out the clay. Make sure the rolled out wide enough to fit your template on it. The rolling pin should never rolls off the cards as it might create and uneven surface for your pendant.
With you clay freshly rolled, proceed with laying your heart template on the clay. Slightly hold down the template with your finger and begin cutting around the edges with the X-acto knife. A steady hand sure helps in this step to ensure a nicely shaped pendant. After the clay has been cut into a heart, peel the remaining clay off and store it with rest of the PMC. At this point the heart clay might be a little rough on the surface so I tend to smooth it out again by wetting my finger and gently rubbing it on the surface. Just a little wetness goes along way so be careful.
Last part of phase 1 can be a little tricky at first but I'm sure you'll get it. There are many stamps out there that you can use on the clay but I was sh!* out of luck and didn't have any. Psych!!! I had found a pocket mirror on the rode earlier this week that had a pretty texture on top. Guess my luck turned out to be okay right? So I took the mirror and rubbed a bit of olive oil on the texture. Then I carefully pressed the texture onto the clay and rolled over it lightly with the rolling pin. This part was tricky and took a few tries to get a nice deep imprint without squishing the clay too much. If you fail then work quickly to re roll the clay and cut to shape. Took me a couple tries but with fast hands and a little caution I was able to get a good enough texture.
Step 4: Phase 2: Drying and Sanding
After your pendant has been cut and textured its time for Phase 2!!! Its time to dry your clay and there are a ton a methods for this. Well you can always just air dry it which should be for 24hrs just to be safe. Other methods include drying it in a toaster over, on a pan in a regular oven, blow drying it and I've even heard of people drying it on usb mug warmers!!! Well since I'm poor and didn't have most of these things I decided to throw it on a skillet and dry it on my electric stove top. The temp was set at medium low and sat on the stove for about 40 mins. You can check if the clay is completely dry by placing on a mirror while its still hot. After a few seconds move it an inch or so and check if there is any heat fog left behind. If your wondering what heat fog is then go into the bathroom and exhale hot breath on the mirror. Boom, Heat Fog!!! So if there is any heat fog left behind then your clay should be dried more.
Assuming your clay is now dry, its time for some sanding and refining. This is a relatively simple step if your rolled you clay nicely and made sure your surfaces were nicely smooth. This is also the best time to make any refinements to your piece before we sinter it to solid silver. So with that being said begin by lightly sanding the textureless side and some 400 grit sand paper. Check to sanded surface periodically to make sure your not sanding too much by brushing of the sanded particles with a paint brush. After that side is looking pretty even then with to the 800 grit to ensure a nice smooth surface. Don't forget to sand the sides of the piece too. Its very important to save all the shaving as it can be used later for more projects.
With your piece all sanded and smooth its time to carve a few holes in the top for some jump rings. On the flat surface a took a pencil and mark a spot on each side evenly. Then using my exacto knife began to twist the blade into the clay. Full circular motion is needed to keep an even circle going. Optionally you can use a dremel bit for this part. Since I happen to have a new set I used a needle bit to drill a couple holes by hand. But Ive done it both ways so like I said, dremel bits are optional. After both holes have been drilled nicely its time to fire this baby.
Step 5: Phase 3: Fire
If you've reached this step then your close to finishing the project. This part can get a bit tricky as well since you'll be dealing with a torch and well if you haven't used one then it can be a bit dangerous. Now if your ready for the task then get out your fire brick and place your piece texture side down on it. I happen to find a fire/kiln brick at my local jewelry supply store for $10 but I've seen them sold online for similar prices. The room should be prepped by insuring it has good air circulation and the lighting is adjustable. I just closed the door in my bathroom and fired the piece i the dark. Up to you though. anyways get out a timer and set it for ten minutes, this will be used to time how long you fire your piece for. Now would be a good time to get your torch out and with the lights out turn fire that baby up!!!
Now with the flame set on low begin torching the side of your piece. You should see a small flame appear on your piece. This is the organic binder burning away leaving the silver particles to sinter together. Keeping moving the torch across the piece until the flame disappears and the piece begins to glow hot. The PMC begins to sinter into silver at around 1300°f and needs to stay around this consistent temp for the duration of the timer. while firing the piece will turn different colors depending on the temp your firing at. You'll want to keep it at an cherry-orangish glow for the entire time. If the piece being to get a bit white the your heating it to high and it might melt. But if you let the temp drop to low it might not sinter properly and break after. I kinda rotate the flame around the piece and periodically pull the flame off to check the color. I watched a few videos on youtube to help my learn a bit about this part and was able to accomplish this on my first try. An important note to remember is the piece will shrink about 15% while firing so don't be alarmed but the size change!
After 10 minutes of constant firing the timer will be going off. At this time I turned the torch off and quickly filled the bathroom sink with water. With my bare hands I usually pick up the brick and dump the piece into the sink water. This is called quenching the piece and should prolly be done with some kind of hand protection. I didn't have any mittens at the time so...well just be careful. If the piece sintered properly you should hear a coin like sound when the piece hits the sink. After the piece hits the water it should be safe to pull it out to notice that is like a white powdered color. Take out your steel wire brush a gently brush the piece. A good technique for this part is to hold as pictured and brush in one direction, you should see some silver popping out from underneath. If so then good job, your holding you very own hand forged silver pendant.
Step 6: Phase 4: Polish and Finish
Last Phase guys, your almost finished. Your silver pendant is prolly looking a bit rough around the edges so its time to polish. Starting off with a rougher 400 grit sandpaper will save you some time sanding the back. I usually laying the sandpaper down a rub the piece side to side across to sand. After the piece is smooth across then I switch to a high grit like 800 to polish to a shine. This time I lay the piece in my palm and rub the sand paper across the surface. After a few minutes your pice will look shiny and at this point a mirror finish can be obtained by using higher grits to polish. But I don't usually go that far so up to you. Now polishing the front is tricky cause you'll be sanding off the texture if your not careful. Lightly go through sanding and polishing with various grit sandpapers and you should come out with a beautiful shiny pendant.
The next step requires you to fill a couple glasses with hot water. In one glass drop 6-8 drops of liver of sulfur, which is a patina that essentially ages the surface of metal. In the other glass drop a few spoonfuls of baking powder. This will stop the oxidation from the patina on your pendant. Now with a bit of string tie your pendant to a chopstick or something similar to hold it in the solution. Proceed with cleaning the pendant with soap and water to remove any foreign elements that might effect the patina process. Then submerge the pendant fully in the patina solution and leave it for a few minutes. Periodically check the color for the desired look. When your satisfied with the color then dip the piece in the baking powder solution to stop the oxidation. My piece looked a bit black with a pearlescent tint. Sorry about the slightly blurry pic.
Just a bit more polishing to achieve the final look. Take the high grit sand paper and polish the back to its original silver shine. Now lightly polish the textured side to remove the oxidation on the surface but keeping the oxidation in the crevices of the texture. Your piece should look something like the picture and your just a few minutes before completion. Take some renaissance wax on a polishing cloth and rub it onto the pendant. This will seal the piece and help reduce further oxidation and finger prints on the piece while adding a layer of protection from common wear and tear. Slap a couple jump rings on your pendant and string it onto your chain and your finally finished!!!!
Step 7: Shout Outs!!!
Just a big mahalo to a few people, mainly my girlfriend Nicole for always inspiring me and buying me supplies. Love you past the moon and back babe.
Also big mahalo to Danger is my middle name, for reminding me of the contest and giving me some wisdom in the past.
One more mahalo to you, my fellow creators/tinkerers for checking out my instructable. If you really like it throw me a vote!!! much appreciated yea!!! Aloha
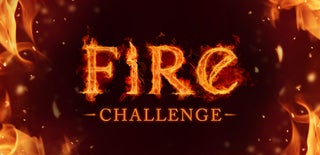
Runner Up in the
Fire Challenge 2017
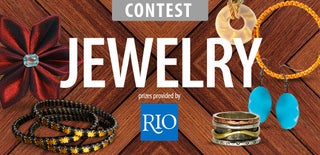
Participated in the
Jewelry Contest 2017