Introduction: How to Make Opal Cabochons
Welcome to this instructable! Here I would like to present my experiences on cutting, what is considered the queen of gems, precious opal. No other gemstone in the world is like an opal and not one opal is the same. And you can cut is yourself if you want to.
You probably already know, but opal is a glass like mineral stone like quarz that consist of hydrated silica dioxide spheres that are tightly packed and ordered in a specific way. Light is defracted by these spheres and the way they are ordered determins the play of color opal is so well known for. Every color of the rainbow can be present in opal where violet and red are the least common. This instructable only provides the information necessary for this instructable so please start reading the background information first. Also I asume that you start from a rough specimen of natural opal that you would like to turn into a cabochon shaped gemstone. Cutting opal is not difficult if you are willing to learn and understand what you are doing at a detailed level.
Supplies
Cutting opal is all about grinding, sanding and polishing. Some items you probably have lying around the house. The rest is quite specific so you need to invest some money for good results. This instructable focuses on the use of a rotary device like a Dremel. That is probably the most expensive part of the hobby to buy if you don't already own one. Any rotary tool will do as long if you can adjust the speed to some extend. Also you need:
- Waterproof sand paper in grit sizes 150,240,600,1200
-Abrassive SilicaCarbide powder in grit size 240,400,800,1200
-Polishing agent like Cerium Oxide or diamond paste (grit 10.000)
- Round wooden sticks (bamboo) and wood glue (white PVAc glue)
-Soft soap, (potassium soap, green soap)
-Various plastic containers
-Dusk mask, safety glasses
Step 1: Disclaimer
Warning! Cutting opal can be highly addictive. It can also be very frustrating and it is easy to fall in love with this gemstone. It can become a costly hobby because opal is a gamble. Don't say I did not warn you. Apart from that every opal is truly unique and it is great to collect the specimens you've cut or turn them into jewelry. So if you are ready to be amazed and like to make the journey to the world of opal please continue reading.
Step 2: Types of Opal: Welo
There are quite a lot of types of opal and only a few types of opal show the play of color. Opal that has play of color is called precious opal. Certainly most famous are the black opal fields of Lightning Ridge Australia. But to introduce you to the world of opal I will focus only on the African type, named Welo or Wollo Opal from the province of Welo in Ethiopia. This type of opal can be purchased (online) for a fraction of the price of Australian opal and is just as mesmerizing. Opal gets graded on its weight in carats (0.2 gram), color, pattern, type and rarity. Not necessarily in this order. Most of the rough stones you can purchase are not clean and are embedded in clay, sandstone or host rock. It is your job to see the potential in these lumps of rock and to me that is just part of the fun.
Step 3: Opal Characteristics. Hardness
Opal is considered a relatively soft gemstone. Shown on a scale for determing mineral hardness, Opal scores a 5,5 to a 6 where diamond scores a 10 en talc scores a 1. Because of this , opal can be cut with simple tools and or machines. It does have the label "handle with care"! Opal is sensitive to heat, pressure, vibrations, shocks, sudden temperature shifts ,contact with certain chemicals and quick dehydration. Most Ethiopian opal is stable material. Meaning that it can withstand the operations when making it to a beautiful gemstone. For jewelry, it it most advised to use it in earrings or pendants. Using them in bangles or rings has the risk of permanently damaging them.
Step 4: Opal Characteristics: Hydrophane Qualities.
Ethiopian opal is a porous stone with a certain water content. Most if not all Ethiopean opal is able to soak up some more when submerged in water. This changes the stone completely. In opal it is referred to the hydrophane qualities of the stone. In most cases the immersion of the opal in water turns the stone transparent and the stone sometimes loses its play of color too. (Or even makes it more visible) When the excess of water is evaporated naturally, the stone turns back to its original state. (Most of the times that is)The hydrophane qualities varies per stone. Some take months to soak up water and others just take seconds, also to release it. Some stones literally stick to you fingers when dry. In my experience, the hydrophane qualities don't oppose problems to cutting the opal if you know how to deal with it. Australian opal is not porous but it does have a certain water content and has most of the same characteristics described above. Except for not turning transparent in water.
Step 5: Tools of the Trade
To cut opal you dont need fancy equipment. I use a rotary multitool like a dentist drill , sandpaper in various grits sizes and abbrasive / polishing powders. Other stuff you need you probably have lying around or is easy to obtain for a small price. Don't forget safety features like a dust mask and safety glasses.
Any rotary tool like a Dremel in which you can change several shafts and rotary bits and has some control over the speed will do. It is advised to use a rotary tool that operates at slow speeds and is driven through a battery or external 12 volt power supply since cutting opal involves using water. I only use the rotary tool to clean up the rough stones, to grind the stone down to the desired shape and later to polish the stone to high gloss finish. The low speeds avoids overheating by the friction. Overheating leads to cracks in the stone.
Bits / burs / shafts
Most rotary tools come with a selection of diamond coated metal bits made for grinding or engraving. It might look fancy to have a set with more than 30 different types of burs but it makes it unclear. Here is a description of bits that you should use:
1- pointed burs. Necessary to clean up the stone and to do precision work. Sand pits may enter the stone quite deep so a small tip will help you reach these pits.
2- Straight or barrel shaped burs. 90 % of the grinding is done with this bit. The smaller tip has a better balance. The rough shape of the gemstone is determined by this bur and working accuratly with this bur takes practice and skill. I do not use it to smoothen the shape of the gemstone
3-Diamond disc. Not absolutely necessary but very handy to cut away large sections of stone. In the right hands it can also be used for shaping or flat grinding. I do consider this to be the most dangerous bit for the rotary tool. Although it is not sharp enough to cut you hand severly, the disc has the potential to shard the opal and spread silica dust at high speeds. I overcome this to only use it under water making it difficult to see what you are doing. So: safety first, use safety glasses and a dust mask.
4-Polishing discs from felt.
This consists of a mandrel in which you can tighten a felt disc by tightening a screw. I use one for every stage of polishing. 5 in total. They are cheap if you don't buy the brand. The mandrel is more expensive. When used wet, the felt discs don't wear out fast. The usually have a diameter of around 20mm.
5-6 Specialist burs. I sometimes use burs with a specific shape. The tulip shape can be used to create concave shapes to create a lense shape cabochon. The wide flat shaped bur is quite ideal to create flat surfaces for cabochons or creating doublets.
Sandpaper
I use waterproof sandpaper most of the times to smoothen out the shapes made with the rotary tool. I start with grit 150 and follow up with 240. For creating flat surfaces for the back of the cabochon I continue with 400, 800, and 1200 grit.
Abrasive powders, polishing agents.
Waterproof sand paper is covered with small particles of the substance called Silicacarbide. (SiC). Nearly as hard as a diamond but certainly not as expensive, it is the same stuff I use for polishing. I use 240, 400, 800 and 1200 grit. I mix this to a paste or slurry to use it together with the felt polishing discs. Silicacarbide is inexpensive , easy to obtain and non toxic.
1200 grit already makes a nice smooth finish but to give it the watery opal appeal you need to step it with a true polishing agent. I use Cerium oxide. Cerium oxide is expensive but you only need small amounts so it goes a long way. Alternatives are using diamond grit pastes and aluminium oxide. Later in the instructable I provide instructions on how to use it in more detail.
Step 6: What to Look for When Buying Rough Opal:
Best way to purchase opal is at a mineral fair. You can get a good deal here and you see what you buy. But let me repeat one more thing for you. Opal is a gamble. When bought blind, about 3 out 10 stones make it to be cut into a quality cabochon. Maybe one of these is likely to become a great gemstone. Opal sellers online will do everything to show you the perfect stone. I mean other than not having the right visual qualities, other factors could ruin the endresult for you. These are opal type, inclusions, cracks, treatments, fakes.
1- Know what you are buying. I focus here on Ethiopian Opal from the Welo province. Only from experience you know what you have to look for. Opal that has been formed in different layers under different circumstances have different qualities. It is good to know that besides Australia and Ethiopia, other countries such as Indonesia, Brazil, Mexico, United States and Honduras also have their own types of Opal. (Yes, even Europe has had an opal mine in Slovakia)
White opal: In my experience white Welo (picture) opal with a white to yellow crust proved to be very stable material. Usually this material is very hydrophane and is easy to cut when wet. I saw little cracks and or inclusions in this type of opal. I have seen an array of patterns from this type from pinfire to broadflash.
Shewa Chocolate opal nodules. In my experience this is a though cookie. Actually I mean that it crumbles like a chocolat chip cookie. Amazing colors predominantly green and red. Does not change colour or appearance when wet. Found in larger nodules and it is very difficult to cut without cracks. Can be polished though but not recommended to use for cabochons.
Crystal opal: Fully transparant or almost translucent clear opal. Also known as jelly opal or. Mostly covered in a dark to light grey clay like sandstone. In my experience this material is stable but more prone to chipping than white opal. Hydrophane qualities differ a lot. The color patterns in this type of opal are less pronounced than that of white opal. It moves around inside the stone like a ghost. Needs a black background to fully appreciate the color so you could glue it to a piece of black onyx to make it into a doublet.
Black opal: Recently some true black (actually slate to anthracite grey) opal appeared on the market. Only one mine I know called the Stayish mine has this material. It is quite rare and the colours are amazing. Very strong reds, blues and greens together with golden flashes. The material is not hydrophane in nature. The material I worked with was stable and did not crack over time and was relatively easy to work with. As with the Shewa Choclolat opal it is formed in nodules,but I believe the Stayish mine material is more stable. I have found that it has hidden inclusions of sand in it making it unpredictable to cut. Not your average beginners material.
Other colors: because of the hydrophane qualities of Ethiopian opal, it is easy to change the body tone completely. Except for white and transparent, the most common natural body tones are amber, honey, cappuchino,cream, coffee, yellow, grey, slate grey,anthracite,brown, brownish orange and slightly pink. Any color other than on this list is likely to be synthetic or treated, or a completely different opal (such as mexican fire opal).The hue of the stone can be completely different. Exceptions are known. For some reason I experienced that colored opal tends to be harder, less hydrophane and easier to chip.
Synthetic opal: Gilson opal, aurora opal, slocum stone, opal resin. There is a lot out there that is not the real deal. Some synthetic opals are chemically the same to real opal but are created in a lab and show beautiful but predictable patterns. If you buy rough opal watch out for fakes. A rough opal has got cracks, sand, inclusions, clay, pits holes, typical clean fractured surfaces, irregular patterns and it smells like opal (a clay like mustiness)
Treated opal: Natural opal is sometimes treated to change or enhance the colors or to improve the stability. Common treatments are dyes, smoke treatment, oils and resins. This is usually not the case with rough Welo opal. Remember the characteristics of real opal. Soaking the opal in aceton for a while dissolves dyes and oils and it will stain the resin. Buying opal shown wet or stored in water or oil is also something I do not recommend buying.
Flaws, cracks, inclusions. Remember that opal is a natural product. What you see is not always what you get. The opposite is true as well. Watch out for cracks but some are quite superficial. Use the flashlight from your smart phone to see how far they go through the stone. Also bring an eyeglass if you can. Microscopic inclusions are the main reason that stones break during cutting or polishing.
Step 7: Judging the Quality of the Stone.
When you've found a crack free natural specimen with little potch (colourless opal) and plenty of color then go ahead and buy it when the price is right. I do not give recommendations to what a good price is. Color does not always show instantly , specially on crystal opal. White opal usually shows more colour. You can buy a jewelers eyeglass with a 30x magnification relatively cheap.
Second thing I look at are the possibilities to cut a nicely shaped stone from it. Deep pits devalue the stone the most because there is no working around it. (although you can create hollow or lens shaped cabochons)
The first thing I do when I have bought stones is to put them in water. I check how quick they soak up the water and even in what way. The hydrophane qualities shows the inside of the stone and from there you can see if it is cracked or included. I then let it dry and see what it does from there. When I have my doubts about cracks in certain stones I do not hesitate to help the crack splitting the stone further. First with my fingers, and maybe later I apply pressure to it by squeezing it between two wooden boards. That sounds scary but you would not want this to happen while cutting a cabochon. I take my losses straight away.
Step 8: Cutting the Stone in 7 Steps
This instructable is written to make freeform cabochons. Don't start cutting your most promising stone just yet. Practice a lot with some colorless "potch". You might even find a hidden gem inside while grinding your way down. Practice your skills with the machine and train your eyes to look for possible shapes. I think it is just a waste to forcefully grind stones down to a cabochon when all you loose are precious carats. An oval cabochon is an aesthetically pleasing shape but also a lot harder to make with a just a dremel. I can be done succesfully with some practice.
1.Cleaning the stone.
I want to see what I can do with the stone. Submerging it a few times in water usually reveals any cracks or sand spots. If necessary I even help the crack a bit. Further cleaning the stone with a regular toothbrush and just some water.
I don't want sandpits or clay in the gem. I usually drill them out with a fine bur so I can further judge what I can do with the stone.
2. Facing the stone
Welo opal usually sparkles from all sides as opposed to Aussie opal. Do have a good look where the interesting parts are. I think it is wasteful to opt for a certain shape if this means grinding down the more interesting bits of the stone just to comply with a set shape. Jewelers quality stones are very uniform in the way they are cut and selected. Sometimes conventional is just boring and doesn't do justice to the stone.
3. Judge what shape to use.
Most gems I cut are rounded off like a cabochon. While cleaning the stone you'll develop an idea of what shape the stone could be cut into. If this is your first stone then I advise you to only round of the corners. Round shapes are less prone to chipping, have a nice look and feel and are easier to polish. There are no set rules when it comes to cutting your stone. When you want to set your stone in a bezel case it is advised to have a strong and smooth edge around your stone. Just take this in consideration: A professional cabber would grind of a lot more in order to work faster and would use professional "wheels" and templates to deliver constant results. You don't have to. Work your freeform magic on the stones.
4. Dopping the stone
Holding the stone with your vingers only leads to awkward situations of you crawling on the floor trying to find back the stone your machine flung into the room. Glue them to a stick! I keep an array of sticks varying from bamboo skewers or toothpicks to chopsticks to glue the stones to. Use PVAc glue since it softens in water. Drill holes in a block of wood to keep the stick upright while the glue dries to hold the stone. The downside of dopping stones is that you need to do it several times for one single stone to finish. So have more stones to work on or be very patient. After a while you get a nice collection of glue invested sticks that could fit similar stones for cutting. You can also dop the stone to one of your barrel shaped burs if you flatten the underside first. This way you can use the rotary tool to work as a lathe.
5. Rough cut the stone
Putting a layer of water in a round plastic bowl and using my rotary tool I rough cut all the stones I have. So, using water and having the stones being dopped to the sticks with glue poses a problem. Therefor I prefer to rough cut it all in one fast single session. This way the glue wont become too soft. Use your dusk mask and glasses!
I don't use templates, I eyeball everything. I leave the fine shaping for later. You'll see that your approach will be different if you leave it for the next day. I found out working on one stone for too long just grinds carats.
Important note: I always wet my stones for a minute or so before I dop them again. Because of the hydrophane qualites of the opal there could be some uneven distribution of water in the stone and the glue could lead to breaking the stone.
6. Fine shaping
Determin if you are happy with the shape. I like the next step to be without the rotary tool. In my opinion it works better to sand everything with waterproof sand paper. Starting with grit 150, ending with 400. For some reason I suddenly am more aware of the mistakes made in the previous step. You can easily manipulate sandpaper into several shapes. I like holding it in the palm of my hand and then circling and twisting the dopped stone to create cabochon shapes. Folding the paper into a guttershape gives nice symmetrical sides. Use plenty of water to keep the stone cool. If you work the surface too long the glue becomes weak and this will mess up your result. Do put the stone in water afterwards so that you can dop it to start shaping the other side. Any visible pits, dents, scratches can only be removed in this and in the previous step. Avoid going in straight lines for too long since this could lead to deep grooves. Wax on wax off Daniel -San! Important note: Once again, keep the stone wet in all cases. It prevents cracks and keeps dust away from your lungs.
Step 9: Polishing
You can start to pre-polish after grinding with the rotary tool and sanding with waterproof sand paper. In this instructable I focus on using SilicaCarbide (SiC) abbrasive powders which you can buy online if you search for lapidary equipment. I use a homemade version of polishing compound based on SiC.
When you decide to use SilicaCarbide (SiC) I would like two offer two methods. Dry or wet. In both cases, you use the same ingredients: vegetable oil, water, potassium soap and SiC abrasive powder . The difference is in the quantity and the way of cooling the stone. I prefer the wet method because then I do not need a face mask. Also the wet compound prevents the stone from overheating. Important note: I always put the machine at the slowest setting to avoid overheating the stone and to stop particles from flying into the atmosphere.
For the wet method I mix two heaped tablespoons op SiC with one heaped tablespoon potassium soap. I mix this this with some water and one tablespoon of vegetable oil into a yoghurt like slurry. I do this with all the different grits of SiC. The SiC particles stay suspended nicely in this sludge. I keep it in a round container with a lid. Whatever you do, keep it clean. When it gets contaminated with other grits the result might show throughout the pre polish. I prefer the wet method but you need more abrasive powder and it is harder to see what you are doing.
The dry polish compound has more oil and a fraction of the water added to the compound. It must feel like clay that you can apply with your fingers to the felt polishing disc. I keep the compounds and the polishing discs in seperate containers to avoid cross contaminating. Important note: You definitly need a face mask with this method.
I made a short video that demonstrstes some of the steps discussed in this instructable. (you need to copy the link because I can't seem to embed the video): https://youtu.be/r6douUM5peE
Step 10: Final Polish
I only use Cerium Oxide at this stage. The alternative is using diamond paste at a 10.000 grit. Cerium oxide is somewhat expensive but you only need small amounts . Diamond paste is even more expensive. Potentially you could use the cheaper aluminium oxide.
The abrasive qualities of cerium oxide are impressive. When you have finished with a 1200 grit Silica Carbide polish you'll see that the stone is smooth but not shiny. To get that watery opal finish you really should use a true polish at the end. I mix the cerium oxide with some soap and oil into a paste which I put into an empty syringe. It is then placed onto a mandrel with a felt disc. Keep this together in a zip bag to avoid cross contaminating with other abrasive powders etc.
This stage is also the scariest for me. It is when you rush into the endresult because you like what's happing but you want it to happen too soon. The stone heats up unevenly and then suddenly there is a crack. The stone needs the friction to get this ultimate shine but you really don't want to feel the heat. You could mix it with more water but then you can't see where you need to buff it up a bit more. Therefore I keep it this way. Make sure to cool the stone and to polish the stone evenly. Short burst of touching the stone to the felt disc helps. Also, keep the stone thoroughly wet.
Important tip: The felt disc on the mandrel is tightened with a tiny screw. This could make up for some ugly scratches if you are not careful. Also the drill chuck from the rotary device is something to watch out for!
And that's it! You have now turned a chunky rock into something special! I hope you enjoyed this instructable and you thought it was usefull. If so, please leave a comment.
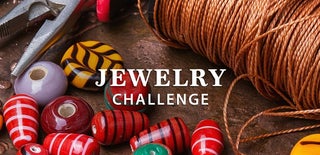
Participated in the
Jewelry Challenge