Introduction: Improved Stove Top Fan (from Junk)
Welcome Friends. In this Instructable we will be making a beautiful but functional stove top sculpture-ecofan, from junk.
The ecofan uses the heat coming from a wood burner to power a small electric motor. This blows the air being warmed by the stove around the room, helping it to warm it up quicker and save on heating fuel (a 17% saving is a figure that gets banded about by marketers of stove fans).
This one's different to the ones you may be familiar with. You know the kind, the ones that use a TEG (or peltier) to create current from a temperature difference. Although it does use a TEG, it's less, shall we say, 'disposable' than the type you can buy! It's even quite a big improvement on the DIY type that others (myself included) have made in the past. Don't know what a TEG is or what I'm talking about? Don't worry I'll explain the workings later. For now all you need to know is that we will be making a stove ecofan that, unlike any others I know of, has a way to protect itself from overheating.
Step 1: Stove Fans - the Basics
This all started a couple of years back (well more like 7 or 8), when I took apart a busted up old travel fridge. It seemed to be cooling with a small white ceramic square thing - a thermoelectric cooling (TEC) module, it turns out. "What on earth!?", thought I.
After some research, I learned that TECs receive an electric current (in this case from a 12V battery) and create a temperature difference across the unit itself. So power goes in, and through some witchcraft that you can read about later, the little unit can create a cold surface and a hot surface. As it happens TECs can be run in reverse, so you make one side of it hot and the other cold and hey presto, out comes electric energy - a small amount...
This TEC in reverse is know as a thermoelectric generator or TEG. Along with the TEG there are a few basic parts that make up the average stove fan:
- Hot side riser block;
- Cold side heat sink;
- Electric motor;
- Some mount for the motor;
- Fan blades;
- This improved version has a few more parts, but I'll get to that...
As you can see it's quite a simple system. In general the parts are arranged to make the heat difference across the TEG module as large as possible, because that increases the power output to the motor, making the fan move more air.
For a basic overview of the parts of an 'old school' design of mine, check out the first part of this video and the picture notes. It's nice to have a working knowledge of this before we move on to build the improved version.
Step 2: The Universal Ecofan Problem: TEG Failure
Nifty though they are, the thermoelectric generators (see step X for an optional geeky overview of them) have a tough job!
The trouble is that they need to be held at different temperatures at either side of the same module. This means they are expanding and contracting different amounts every time they heat up and cool down (read lots of mechanical stress). If the temperature at the TEG raises above about 150 degrees C (300F) most cheap TEGs are toast! But the surface plate of most woodstoves, when they are burning efficiently, can be much higher than this, typically about 200C (392F). I've measured a few of my friends stoves, and my own experimental one, and if let rip they have all risen to over 300C (572F). This is probably too hot a temp to run at on a regular basis - it's not healthy for a typical wood stove - but it happens from time to time.
So you see the problem? Stove too hot, TEG too weak.
The way stove fans have addressed this problem is to have a 'hot side riser block', a piece of metal that sits on the stove top, and conducts only some of the heat to the TEG. Essentially the riser block reduces the temperature the TEG sees on its hot side.
Even with this reduction the problem is that for the TEG to work well and sit in its preferred temperature range, on those rare (or not so rare) occasions when the stove really gets a fierce burn on, the temperature will still go too high! Armed with a stove thermometer, the really diligent and knowledgeable woodstove 'power-user' might avoid this overheating, but for most of us, the sheer number of factors involved (type and size of firewood, how dry it is, primary and secondary air intake adjustment, ambient temperature, the wind speed and direction causing more or less flue draw, how engrossing the conversation is, etc etc.) mean that at some points we are likely to overheat the stove fan's TEG.
I've made and repaired a lot of stove fans over the years, and that right there, on DIY and commercial stove fans alike, is the quiet but fatal Achilles heal of this whole 'eco' fan thing!
Step 3: The Overheating Fix - Overview
So you would think this would be an easy fix, all we need is a thermostatic switch of some kind to prevent overheating right?
Well, yes and no. An electric switch, the type widely available and used as overheat protection in electric motors and the like is no help. Cutting the electric circuit does nothing to protect the TEG from the damaging temperatures, instead it worsens the problem as the fan would no longer be cooling the unit. A mechanical thermostat that actually moves the TEG away from the heat source, that is simple and non-powered, seemed the best avenue of investigation...
After tinkering about for a long time with various bi-metallic strips (remember them from school science classes?) in different positions, and not getting anything working quite right, I discovered wax thermostats, of the kind used in automotive engine cooling systems.
When wax changes from a solid to a liquid (melts) it also has a relatively large increase in volume. Wax thermostats use that property, having the wax in a sealed chamber that drives a rod when the wax melts (imagine a sealed hydraulic cylinder where the fluid is increasing and decreasing in volume as temp changes).
The one I settled on using starts to open (the wax begins to melt) at 93C (200F) but is fully open about 110C (230F). This is just right for our purpose as the wax filled copper bulb is situated near the cool side of the TEG. If it is 100C (212F) there, it is likely to be approaching our t-max on the hot side of the TEG!
Step 4: Gather Your Materials
This stove fan is made from junk. Mostly...
The bulk of it is made from an aluminium hot side riser block and a cool side heat sink. If you can scavenge/upcycle these two items you will have saved approximately 90% of the embodied energy of a fan like this. The other components can be salvaged too, but not quite so easily, I will go through each in turn giving some ideas where you can get them. See the photo-diagram for an overview.
The Cold Side Heat Sink (CSHS)
An old chainsaw cylinder - if you don't tinker with chainsaws yourself, ask your friends and family. If that doesn't turn up something, make friends with more mechanics! Failing that, you can get these from garden machinery and chainsaw repair shops, usually free or at very low cost if you ask nicely (I was given a whole box full). If that doesn't work you could always try a search like this for ones on ebay. It wants to have a bore diameter of 48mm (~1.9") or more (see below). You will also need an appropriate strip of copper (best) or aluminium (ok) or brass (expensive and hard to scavenge) to bridge the gap at the bottom of the cylinder bore and transfer the heat from the TEGs. I used a scrap of copper bus bar 4mm (5/32") thick. Best aprox. size is 95mm (3.75") x 60mm (2.5") (or whatever the width of your cylinder base is). My scrap of bus bar wasn't quite as wide as I would have liked, it's what I had a bunch of though...
Alternatively, you can use an old CPU heatsink for the the 'cold side'. I have made a few in this style and while I personally think the chainsaw jugs look better, a good beefy CPU heatsink will do at least as good a job (again try a search like this on e-bay and find a used one - overclockers are changing these all the time). If you do go this route, a different method for attaching the thermostat (see step 10) will have to be worked out, as there is no longer a convenient cavity to house it.
The Hot Side Riser Block
This can be a really basic aluminium heatsink - no fancy heat pipes needed as the purpose is to reduce the temperature somewhat. This can easily be scavenged from almost any consumer electronics trash... If you score a junked 12V travel fridge, you can often bag this alu part as well as a TEC to use at the same time!
The TEG
The design here uses two thermoelectric generators (TEGs). One is ok, two is better! The best upcycled source I know for these are little travel fridges, which seem to be thrown out a LOT - being quite rubbishy made plastic items = bad scorn. Maybe there are some well made ones out there, but they don't show up in the trash so I never see them ;)
Not so good as upcycling, but you can also buy these little modules. There are cheap ones (like these), or very very cheap ones (that don't seem to last well at any temperature).
All these modules are really TECs (thermoelectric coolers), also called peltiers, which we run in reverse, rather than specialist TEG (generators). Proper TEGs are a bit more heat resistant but also a bit more expensive (see these for $10.55). If you are buying, rather than salvaging this part, in the long run I think they are probably worth the extra as they have a t-max of 250C, will last better and probably put out more current = better performance. I am currently testing some of these particular ones myself, so time will tell how they do.
The Motor
You want a small electric motor that will run at voltages from about 1.5 to 6V DC. These are easy to salvage from old CD and DVD players. If you get stuck this is the kind of thing you want. Look for ones with a nice long shaft.
Wax Thermostat
I 'discovered' these when salvaging other parts from a scrapped car engine. There is sooo many useful bits in old engines, but they take a long time and a lot of tools to dismantle, and are very dirty and oily. If you have a friendly car scrap buddy, you could ask them to look out for one for you. Probably this is a strategic part you will want to buy though.
The automotive single valve type wax thermostat I used was for a Vauxhall Astra 1.6 - ebay $7 - https://goo.gl/iPkoQi or uk £5 https://goo.gl/gLiUn4. it has an outside diameter of 48mm. Therefore if you want to house it inside the cylinder like I did, you will need one with at least that size cylinder bore - so that is likely to be a medium to large size chainsaw donor. Less than that, and I suspect it could still be made to work if you cut up the thermostat somewhat. But lets assume you get a 48mm or bigger.
Old Brass Plumbing Fitting
The brass compression elbow, was straight from my home plumbing adventures. Scavenge some or ebay it (link).
The Fan Blades
You can buy these, but they are getting hard to find, try here or here on ebay. Better, you can also fabricate your own using ~1mm (1/32") thick scrap aluminium plate if you can scavenge any. If you have to buy the plate it may be as well to buy the ready-made fan blades, although making your own is cool because you can tweak the size and shape to suit your tastes. If making your own, a brass bolt makes a good hub (see the fan blade section for more on this). You will also need an M4 (or #8) grub screw.
Bolts
4x M5 bolts - usually salvageable with the chainsaw cylinder (you can use the same ones that held it on). One M8 to M10 bolt to make the plunge pin from and a small spring to go with it.
Thermal Compound
See "Step 13: Heat Transfer 2: Thermal Grease" for more on this, but a small tube of something like this, or you could go with some copper slip if you already have a tub.
Pipe Scraps
Some scraps of pipe about 48mm OD are used to secure the thermostat in the cylinder. These can be any kind of metal.
Electrical Misc
Solder, heat shrink tubing, or insulating tape, or crimp connectors, or screw-clamp connectors.
Step 5: The Motor Mount
Lets get started by making the motor mount!
The motors that you can salvage get from cd/dvd players fit quite nicely into the compression nut of a 22mm (3/4") brass elbow. Depending on what your cylinder is like, and how long the motor shaft is, you may need to make some modifications.
For some fans I have made, a straight motor-in-brass-nut fit has worked. For others, in order for the fan blades to get clear of the cylinder, I have had to make a little extension mount between the nut and the motor. If you do need to make/ bodge together a spacer, the place to start is with little scraps of pipe. In the past I have used some standard copper plumbing pipe (the size that is designed to fit in the compression elbow) that I slit at the end and bend out, forming a kind of spring grip for the motor. That's a nice easy fix that doesn't require any special tools.
Of course if you have a little metal lathe, a custom made spacer/adaptor is a lovely little project. When I do this variant I make the adaptor tightly press fit into the brass nut and the motor a slide-fit into the adaptor. Then I tap a hole and add a little set screw to hold it the motor in place - it's a nice touch.
I'm going to resist the urge to go on about 'material based design' like I always do (see my big disc sander 'able if you want the whole rant/thesis), but really let what ever scrap bits and bobs you have and the tools available to you guide you here. Check out the picture notes for some option ideas...
Step 6: Joining the Motor Mount to the Cold Side Heat Sink
You could use all kinds of things for the cold side heat sink (CSHS), but I think a chainsaw jug is great!
Most kinds have four bolts holding them onto the crankshaft case. We can reuse those same four bolts to attach it to the hot side. Keep the gasket if you can, as it is useful in laying out where the holes should be made in the hot side riser.
We can use the spark plug recess in the cylinder to attach the 90 degree plumbing elbow (motor mount assembly) we made in the last step. The beauty of having the motor mount joining this part of the CSHS, is that the wires can be routed through the elbow and cylinder bore, keeping them nicely hidden out the way.
On most of the stove fans I have made I have been lucky and the thread of the brass elbow was just the right size to self tap into the aluminium housing. You may need to modify this somewhat, depending on your cylinder. It's hard for me to be more specific, than to say make the elbow fit in the spark plug area, because I don't know what your relative size will be like - that's just the way upcycling is some times. I'm confident you can make something fit. If you need to add packing spacers remember that really we don't want to use anything flammable like wood or plastic.
Using a bolt that fits in the actual spark plug thread can work well. On Stihl and other European saws this is almost always M14 x 1.25mm (Metric extra fine) thread. This happens to be the size of many sump plug bolts, so if like me, you keep your old sump plugs after doing an oil change, you will have one knocking about already (otherwise they are cheap on e-bay). You will need to drill a hole through the centre of the bolt for the wires to pass through. Slide on a bunch of washers on the thread of the bolt, and tighten with a locking nut. The washers need to be sized to fit into the brass compression elbow - you can tweak the size by putting the thread of the bolt into a drill chuck and spinning them against a file or angle grinder (as sparks fly, do stay safe with correct ppe). If the washers you have are too small, use a scrap of copper pipe as a shim/sleeve.
Another option that I like is to butcher up the spark plug itself, and get the elbow to fit that. You can smash the central part of a spark plug away by cracking the ceramic insulator with a hammer and drift pin (wear a face mask - again shards do go flying)! Once done you will have a hollow bolt type thing (exactly what you want). On ones I have done in the past, the outer body of the spark plug fits tightly into a 22mm copper pipe, which can be clamped onto the elbow in a standard plumbing fashion (see pic notes).
Step 7: The Hot Side Riser Block 1 - Requirements
So this can be almost any conductive non-flammable material (usually aluminium) that reduces the stove top's average burn temperature to something the TEG will handle well. For reclaimed, and cheap TEGs (TECs run backwards) this will want to be about 130C (270F). For the real TEGs (see "Step 4: Gather Your Materials" for the distinction) it can be more like 200C (400F).
Whatever you want to use as your riser block, you ideally should test to see how much heat it transfers. Though this is optional with this design as we have overheat protection anyway - it's still a good idea. Upside-down old CPU heatsinks are good, but I have also used a combination of the chainsaw piston and old heat sink with good results in the past. a section of simple box section aluminium extrusion can also work well.
Do this test by getting your stove up to good burning temperatures with the riser block candidate on the top. Leave it long enough that it reaches a stable high temperature. You will need to use a stove thermometer or something similar to do this (if you have a woodstove and you don't have one, get one - they are cheap and a very useful tool for your stove in their own right).
If you find it transmits too much heat, you can modify riser blocks by strategically removing material - think drilling big holes, hacksawing or grinding out sections.
If it isn't getting hot enough, It may not be a great candidate.
Step 8: The Hot Side Riser Block 2 - Fabrication
So after checking it out on the stove, we are going with a bog standard reclaimed CPU cooler this time. As well as having just the right amount of thermal resistance, it has a number of additional things going for it. The bottom, which will now become the top, has a nicely ground flat surface that's big enough for two 40mmx40mm TEGs, with room between them for the sliding pin. It also has enough solid material there to tap and thread holding bolts.
Lets start by centre punching and drilling an 8mm (or 5/16") hole, right in the middle of the heat sink, going all the way through. Then counterbore that with a 13mm (1/2") drill to a depth of about 20mm.
This hole will house the spring loaded sliding pin that will be depressed in overheat conditions, and lift the riser off the stove top. It's probably a good idea to fabricate the pin / scrounge about for an appropriately sized bolt so you have an idea what your aiming for, before you go ahead and drill (see the next step).
Next we want to punch, drill and tap the four clamping bolt holes. To lay these out use the cylinder gasket if you have it, otherwise careful measuring with calipers or ruler is in order. If you are re-using the cylinder bolts then the chances are you will be going metric, which means a M5 thread tap and a 4.2mm diameter drilled hole.
I use a touch of WD40 for both drilling and tapping in aluminium.
Remember to wear goggles for all the drilling, tapping, de-burring and filing - Alu is a particularly lively a material and shards tend to snap and fly off more dramatically than with steel.
Step 9: The Hot Side Riser Block 3 - the Sliding Plunge Pin
To complete the lower half, we need to make the plunge pin.
This is just a modified bolt, that will slide up and down the central hole. It is spring loaded so that it is normally not sticking out the bottom, but when the wax thermostat is engaged it is pushed through and lifts the base away from the stove.
To make it I used a regular M8 bolt and rounded off both the hex head and the thread. To do this chuck the bolt up in a drill and press it on a file or grinder (see pics). Again PPE up for this one and check your progress often by seeing how it slides in the hole you made...
The last thing to do on the riser block is clean it thoroughly, removing any trace of old thermal grease. Alcohol and a rag work well, but any solvent including soapy water would probably do if you rinse and dry so there is no residue.
Step 10: Securing the Wax Thermostat - Pipe Sandwich
So we need to keep the wax thermostat secured into the cylinder bore.
To do this we want 2 sections of scrap metal pipe of about 48mm diameter. They can be cut so that they jam the body of the thermostat in place.
Size the first pipe so that it holds the thermostat so that the copper bulb comes almost, but not quite flush with the base of the cylinder. This pipe also needs to be drilled so that we can thread the motor wires through it and into the side port of the cylinder. Make it easy on yourself and drill a nice big hole. De-burr it well, so it doesn't snag the cable insulation.
The second pipe sandwiches the stat and rests against the copper 'heat spreader' (see next step and pic notes and it should become clear).
Step 11: Making the Copper Heat Spreader
This could be copper or aluminium. Copper conducts heat slightly better, so is technically the best choice, but it depends what scraps you have... The heat spreader's job is to send the heat from the cold side of the TEGs into the cylinder. It also serves to contain the wax thermostat-pipe sandwich.
Ideally it will cover the full area of both the TEGs and the cylinder base. The observant among you will notice that my strip of copper isn't quite wide enough to contact the outer edges of the cylinder base - not ideal - but it's a copper strip that I salvaged, so I'm proud of it nonetheless...
We will need to make some holes in it for both the clamping bolts and thermostat bulb to pass through.
Carefully mark up, centre punch, and drill. If, like me you need to 'notch the edges', that can be done with a hacksaw, a file, an angle grinder, a mill, a karate chop - whatever you have to hand...
Step 12: Heat Transfer 1: Mating Surfaces and Flattening
We want to make the surfaces in contact with the TEG, especially on the cooling side, as conductive of heat as possible. To do this we want as much surface area of the TEG's cold side in contact with the heat spreader (and by proxy the whole chainsaw cylinder) as possible.
While things may appear flat to the naked eye, it isn't always so! The scrap of copper I'm using, for example, was manufactured to be used as an electrical bus bar, and while that aught to be 'flatish', it certainly isn't very flat in machinist terms. Unlike electrical contacts where highly torqued bolts mash the stuff together, we really need to rely on very well mating surfaces, rather than high pressure, to make good contact. For that reason it is worth going to a little extra effort to get the copper as flat as possible.
This can be as simple as laying a sheet of wet and dry sandpaper on a known 'flat' surface and rubbing it until the copper looks uniformly abraded. Start with a low grit (course) like 120, and work up to as fine as your patience allows, it doesn't need to be completely perfect as the thermal grease will take up some slack. Just remember that any visible scratch marks will be voids in the surface contact, and will reduce efficiency.
Tip: If you don't have a surface plate, for our purposes, a 'flat' could be a thick scrap of float glass laid on a flattish surface like a drill press table, saw bench table, or even a kitchen worktop.
Luckily the mating surface of the cylinder base and the CUP heatsink are already machined flat, so we don't need to worry about flattening those.
Note: All this is optional, but makes a more efficient finished fan. Time spent now, will be rewarded with small gains that accumulate over a long time (years of improved operation)... But, remember: better the imperfect project you finish, than the precise perfection you don't.
Step 13: Heat Transfer 2: Thermal Grease
No matter how extreme you go in the previous step, you will not achieve true flatness. Thats where thermal grease (or paste) comes in. It is usually a mix of fine metal oxide powder suspended in a silicone (or similar) base. The idea is that the metal particles fill all the voids between the surfaces, eliminating any thermally resistant air gaps.
Not all thermal grease is equal . We need something with quite high temperature resistance, and good thermal conductivity. I spent a while researching this a few years ago and bought a biggish tube of thermal compound that I use on both electronic/computer projects and stove top fans. You probably don't need that much.
With good clamping force, very flat surfaces, and a thin even layer of thermal paste, most of the comparisons I read suggested that in terms of thermal conductivity, there isn't too much difference between them... But if you want the best (and I'm going to humbly suggest you DON'T because it will be needlessly costly) then that changes all the time as new concoctions (some more toxic than others) are being produced to serve the electronics industry. Assuming you're not going to be using lots of the stuff for more things after this project, a single small syringe of something like this should do just fine.
To apply the thermal grease, put a little out with the syringe and use something clean to spread it very thinly...
In a pinch copper anti-seize grease - like you use for car brake backings - should easily be good for the high temps, and will be better than nothing.
Step 14: Soldering Up the Motor & TEGs
The circuit is super simple. The two TEGs are run in series straight to the DC motor.
I like to check everything's as it should be by using croc clips first. That way it's easy to check the motor spins the correct direction for the fan blades to be pushing air into the room. If not, simply switch the cables going to the motor around. I test it using an old upturned iron to briefly heat one side of the TEGs.
Once you have it working the way you want, you will need to rout the cables through the motor mount and brass elbow, into the cylinder bore. From here take them out the hole in the thermostat support pipe, and into the side port. A small hooking implement and/or some snipe nose pliers can help you fish the wires through.
From there you can solder them up to the two TEG wires. If you are using heat shrink tubing, remember to slide that on before soldering. If you don't have heat shrink tubing use some electrician's tape (not as neat or nice).
If you don't like soldering, this joint can also be made with crimp connectors or even a screw terminal block.
For some tutorials on soldering see https://www.instructables.com/id/Soldering/
Step 15: Clamping the Whole Thing Together
This is a bit trickier than it might first appear. In-fact Caframo (the original manufactures of these fans), claimed they couldn't sell the TEG modules so people could fix the fans themselves, for the reason that they required technical expertise to properly fit the modules. As we are both designing the way the TEGs will be 'sandwiched', as it were, and fitting it together ourselves, it pays to have a little look at this issue.
Firstly the bolt holes that clamp from the hot side to the cold side, should be positioned as close to the TEG as possible (without snagging or touching it). This helps to avoid either side bowing and crushing the edge but not making contact well with the centre of the TEG. See diagram 1. If you are using the cylinder design this is of less concern because it is super rigid and the bolt locations are all already decided. It's good to know though.
We also need to allow for heat cycling and the potential for that to exert excessive pressure on the TEG. For this reason it seems prudent to add springs to the the mounting bolts
The bolts need to be tightened bit by bit, alternating between all four, so the the clamping force is evenly applied. Remember the edge crush potential (diagram 2). If you're using four bolts, a tightening force of about 0.8 newton-meters is all that's required on each bolt. If you have a torque wrench/screw driver that sensitive then use that, if you don't, all you need to know is that it's not tight! You want just enough force to hold the thing securely together, but no more.
Step 16: The Fan Blades 1: Intro and Making the Hub
By now we should have a pretty cool looking lump of metal with a motor that spins when you put it on a hot surface. Hooray! Next we need that motor to do something useful so lets make the fan blades.
I should start by saying that on many of the ones I made in the past I have cheated a bit and used fan blades available as spares for commercial stove fans. If you wanted to go that rout, especially if you didn't have the scrap parts, that would probably be just as reasonable as buying the sheet metal to make your own.
I scored a load of 1mm (1/32 inch) thick off-cuts of copper and aluminium from a skip near the arts school (I think they use it for picture backings or something? When that happened I realised it was time to makes some blades that would be more in the upcycled spirit of this thing!
I started by making a hub from an old brass bolt, that would mount onto the 2mm (1/16inch) motor shaft. The bolt has a hex head, that will suit a 3 bladed design. I personally much prefer the look of three bladed fans, vs two bladed ones. If you rather two blades a hex shaped hub won't work so well, so choose something different.
To make the hole right in the centre of the hex head I used the lathe and three jaw chuck, which makes it easy.
If you don't have a lathe this can be done on the drill press in a procedure like the following: 1. clamp a scrap of metal or hardwood to the drill table. 2. Drill a 2 mm hole in the scrap. 3. Now take the twist drill out of the chuck and glue it cutting flutes up in the hole you just drilled. 4. Chuck up the bolt in the drill press and use the upturned drill bit to bore a nicely centred hole.
Step 17: The Fan Blades 2: Grooving the Hub
Commercial fan blades are stamped out of a single sheet of aluminium using a precise and very expensive die. They are then machine bent to form the aerofoil contours that actually push the air. We don't have any of that stuff so our way round that is to make three identical blades, and mount them in angled groves in the central hub. Our advantage is that we can make unique one-off fan blades, that will complement a steampunk-esque functional-sculpture comparatively easily.
It is really important to cut the groves in the hub all at the same angle so the finished blades look even. To this end we can make a simple jig to hold the bolt. In my case this was as simple as a scrap of wood with an angled hole drilled in it. The size of the hole is such that the brass bolt could be just about be screwed in and was tight.
From there I used the bandsaw, resting the jig against a rip fence it was possible to cut the grooves all at identical angles. A stop block was clamped to the table to ensure the depth of all the cuts was consistent.
You can see the setup in the video and pics.
Without a bandsaw a similar jig could be made to work with a mitre block and hacksaw.
Step 18: The Fan Blades 3: the Setscrew & Hub Finishing
Before we cut the thread off the bolt or fix on the blades, we want to make a set screw to fix the hub onto the motor shaft. Use a 3.3mm drill and M4 (or imperial equivalent) tap to create the thread in the hub.
Use the length of the bolt to clamp it so you can drill into any of the 3 remaining ungrooved faces of the hex. Take care that the hole you drill squarely intersects the central motor-shaft-hole. That way the grub screw will tighten onto the right place! (remember eye protection while drilling and tapping - even hand tapping).
With that done you can then go ahead and use a hacksaw to cut the thread off the bolt, creating something more recognisably a hub. Clean up the cut with a hand file, or lathe.
Step 19: The Fan Blades 4: Cutting Out & Shaping the Blades
While the copper scraps looked very cool, they were way heavier than the equivalent thickness aluminium bits, so in the interests of efficiency I opted to use the aluminium (if the copper was a bit thinner, like 0.7mm (~0.03") thick, I might have gone with that).
To make the three blades identical I stuck three scraps together with double sided tape, and then sketched out my blade design on the top one. It was shaped based off proportions I know work well on the commercial ones mixed with a hint of my own aesthetic preference, and a large does of artistic flair (read complete randomness).
Once you have draw out and are happy with your design, cut it out! Aluminium cuts quite readily, so clamping the layers in a vice and using a hand coping saw will work well. If you have one, a vertical bandsaw (wood or metal - it doesn't really matter as it's such soft thin material) with a fine-tooth pitched blade will make very short work of it.
Before pulling the three layers apart, you can smooth off the edges on a disc sander, belt grinder, or with hand files. Once done carefully prise the blades apart and gently de-burr all edges with a fine file, fine sanding block or similar. Remember that once they are apart, we don't want to change the shape of the individual blades or they will look weird.
Step 20: The Fan Blades 5: Brazing to the Hub
If you watched the video of this process you will see that I brazed the blades to the hub. Would I do it that way again? Possibly not!
Brazing is a bit like soldering but at a much higher temperature. Unlike welding neither of the base metals are melted (unless you get it wrong) as the filler rod's melting point is lower. For more brazing background check out this instructable by Steam_cannon.
Please wear safety equipment when brazing and choose your surface well. If for example, you braze the fan on concrete it can super heat moisture in the concrete which can send little bits of concrete flying at you! Use a fire brick or similar if possible.
I should preface all this with the admission that I am almost completely inexperienced at brazing. I did a test on the brass bolt off-cut and a scrap of the aluminium, and that seemed to work OK (though it wasn't super strong). I used my MAPP gas torch I use for plumbing, some HTS 2000 brazing rods (wouldn't recommend) and a little stainless wire brush.
The trouble I had was that in the process of brazing the rod tended to jostle the assembly and even though the blades were quite a tight fit in the hub, it was hard to keep them evenly placed. Also I overheated one of the aluminium blades somewhat, which deformed it a bit (luckily easily bent back - but still not ideal). I did manage the whole job without getting any of the braze into the grub screw area, which was pleasantly surprising.
In the end it worked out, but if I was doing it again I would either, create some kind of jig to hold the blades in alignment to the hub during brazing, or more likely use some kind of metalized epoxy (I'd mix my own, but similar to JB Weld). With epoxy you would have time to align everything by hand and could then leave to set. One objection to metalized epoxy would be the lower temperature resistance, but it should be good to ~ 250C (500F), and barring some disaster the fan hub area should never see anything like that!
Step 21: The Fan Blades 6: Making Blades?
Having spent a while making them, it's hard for me to evaluate the fan blades dispassionately, I like the way they look, and the shape of them. But judging by the mess of joints on the hub, my brazing needs a lot of practice/ refinement. TIG welding might be an avenue for investigation, but not having TIG access myself I haven't gone further with that. I'm sure someone with experience can chime in in the comments to say if it works with dissimilar metals like brass to aluminium. I guess the commercial ones that are push fit and mechanically crimped to a central hub get round all that.
If you wanted a two bladed version, a lot of the problems with joining could be overcome as you can have one-piece blades, drill a hole in the centre, and use a bolt and clamping nut as the hub. Assuming you had strips of sheet aluminium long enough... As I said I don't really like the look of two bladed ones though. Three and four bladed one-piecers are possible but would involve bigger scraps than I had, and would have the downside of more sheet wastage. That said, if I had scrap sheet material big enough, that's probably the rout I would go - though you do then have to worry about making accurate bends, as the blades whouldn't be angled from the hub.
I do think, if you score a bunch of off-cut material like I did, you might as well have a go at making some, even if they are somewhat less efficient, and a tad clunky. You will have turned scrap material into something you (or whoever you give the stove fan to) will cherish. Plus the pre-made blades aren't exactly cheap, or easy to get hold of (see step 4 for links).
Is it worth making if you don't already have the material and brazing kit or some other way of joining? Maybe, if you're into learning new techniques as you... I'll leave it an open question. Personally, I need to try out some more techniques before I come to any conclusions. You guys can really help here by sharing your own experiences - how did you do it? Pros and cons?
Step 22: Test, Use, Enjoy! Share.
The overheat protected stove fan is working great thus far! It is still something of a prototype, but so far all indicators are good! I'll consider this instructable something of a working document, and update it as I make more and get longer term results of how they are working. The very first bunch of fans I made six or seven years ago, for friends and family, were a little frustrating because of TEG failure, and this seems a way round that. Hooray!
The stove fans do make fantastic gifts for people with woodstoves by the way, especially at Christmas (if it's cold that time of year where you live).
There is something people really appreciate about having a bunch of unlikely stuff being re-purposed. Every piece has its own past life and alternative function, is reordered and now working away, energy free to increase the warm glow of the fire. It's just plain cool! It's a nice talking point too; 'that bit's my old chainsaw that burnt out when I..."
Well, dear reader, I hope you got something out of all that. If you have any questions please do connect, and share your experiences in the comments. I'd love to hear from you.
If you did find this interesting you may also like to encourage my efforts (and get cool vids) by subscribing to my youtube channel and sharing this with friends or family who like upcycling/ making stuff. If you feel like I put the work in here, feel free to tip me at https://www.patreon.com/floweringelbow.
Peace.
Step 23: Appendix 1: Areas for Development
Experimentation with different temperature ratings and positioning of wax thermostats.
A magnetic levitation style, set of plunge pins would be cool.
Working out the blade fabrication kinks.
Testing higher temperature TEG's.
Large ones for the mad eccentric look (small lawn mower cylinders, or 2 or more CPU coolers).
Step 24: Appendix 2: What Is This Witchcraft? How a TEG Works.
If you just care about results and are happy thinking of this as a magic white box, then you can go get on with things! If you like to look in to things, here's some info to get started with, though be warned, like most things, the more you look into it the more questions there actually are!
Thermoelectric generators (TEGs) work by having a construction of differing materials, usually P and N-type semi-conductors (overview of what these are) sandwiched between ceramic plates, with copper conductors linking them in series. This works because of something called the Seebeck effect. There's a reasonably deep rabbit hole you can go down if you want to investigate the Seebeck effect. Basically it is the observation that a temperature difference between two different conductors or semiconductors produces a voltage difference between the two substances.
The voltage induced by the Seebeck effect is typically expressed in the formulae:
V=αΔT
where: V is voltage, ΔT is the temperature difference between the hot and cold junctions, α is known as the Seebeck coefficient. α varies depending on the semi-conducting materials used to make the TEG. But as you can see the greater the heat differential between hot and cold side the higher the voltage.
In TEGs A set of thermocouples built by legs of p‐ and n‐type semiconductors, usually made from bismuth telluride (Bi2Te3) but some also have lead tellurid (PbTe), are arranged so that a small current flows with temperature difference. Good thermoelectric materials want to have a high Seebeck coefficient, low electrical resistivity, and low thermal conductivity.
On its own a single thermocouple gives a temperature-dependent voltage. This voltage is very small, and this is what is used in standard temperature sensing therocouples that you connect up to a miltimeter to give a temperature reading. Although not super accurate, these kinds of temperature sensors have the advantage that they power themselves, they don't require external power.
Our TEG modules can be thought of as lots and lots of these thermocouples wired up in series, giving us a useful voltage when the temperature difference is high enough.
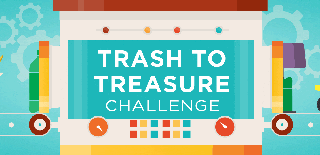
Second Prize in the
Trash to Treasure