Introduction: Improvised Folk Fiddle
use local and scrounged materials to build a fiddle.
then,
learn to play the fiddle.
I built this functional folk fiddle from free materials.
the wood was salvaged from scraps
the strings and bow "hairs" are nylon monofilament fishing line
I am spending this summer at a small farming community in northeast missouri. Almost all of the food we eat has been grown on the farm by the community. I build things in my free time.
----------------
Submitted by MITERS for the Instructables Sponsorship Program
Step 1: Proportions and Shape
I wanted my instrument to feel similar to a violin. I found dimensions for a violin online, then made a silly looking sketch of a fiddle with some useful numbers on it.
all members of the viol family (violin, viola, cello, contrabass) are built similarly and function similarly.
I started the project planning to use an olive oil tin as a soundbox. I didn't like how the tin sounded when I tapped on it, so I made a wooden box instead.
I didn't want my instrument to have as many curves as a traditional violin. I had seen pictures of teardrop shaped folk fiddles in the Foxfire books, and I read about a famous trapezoid fiddle made by Felix Savart. I decided to make my fiddle's box trapezoidal also.
Step 2: Fingerboard and Neck
a fiddle has a radiused fingerboard. It looks sort of like the letter D in cross section. This is so that each string can be bowed individually. A classical guitar has a flat fingerboard. If you tried to bow a classical guitar, you would only be able to sound the strings in the middle by bowing all of them at once.
I made my fingerboard out of black walnut. It grows so vigorously here that people use it for firewood. I started out with a blank about 10" x 1.5" x .5". I cut it on a table saw from a piece of firewood.
You can use any wood that is hard for the fingerboard.
I traced out the profile I wanted on either end and roughed it out with a drawknife. Mine was about an inch wide at the nut and 1 3/8" at the other end.
Next, I used a smoothing plane to remove high spots. I got good results by clamping the plane upside-down in a vise and running the fingerboard over it. Try not to plane your fingers while doing this.
Press a straightedge against the fingerboard in the direction that the strings will run. Hold it up to the light and make sure no light shines through to see that it's true and flat.
If your strings buzz when you put it all together, find the high spots and use a piece of broken glass or a plane blade to scrape them lower.
The neck on a violin is traditionally made of maple. I used a piece of white oak instead. You can use any stiff wood.
I salvaged this wood from some broken garden stakes, about 1 1/2" by 3/4" in cross section. I didn't have big block of wood to carve the neck from, so I joined two pieces of stake with steel pegs (nails with the heads filed off) and glue. I shaped it with a drawknife and smoothed the sharp radii with a rasp. I left one the top flat so that it could be glued to the fingerboard. At this time, I was still planning on using an olive oil tin as a soundbox, so I shaped the neck to extend through the can and poke out at the tail. I later cut this part off and shaped the remaining stub to resemble part of a dovetail joint.
Make the head big enough to hold four or more tuning pegs. Mine was the cross section of the stake, and about four inches long. I put about 3/4" between each peg. They alternate sides to nest more tightly. If there's room left on the end, carve something goofy into it. Most violins have ornamental scrolls. I made a sideways scroll with some small chisels and a coping saw. My friend who went to art school told me I should have made sketches first. I should have made sketches first.
Glue the neck to the fingerboard when you're satisfied with the fit. Real violins are sometimes held together with hide glue. Hide glue joints can be separated more easily than those made with regular old wood glue. This makes it easier to take apart for repairs or alterations. I just used regular wood glue.
You could make a fiddle with any number of strings. The Hardanger fiddle of Norway has sympathetic strings which run underneath the fingerboard.
Step 3: Pegbox and Pegs
Lots of stringed instruments use tapered pegs in tapered holes to hold their strings taut. The taper makes the peg hold well, even after lots of adjustments. Professional instrument makers use tapered reamers to make the holes and special pencil sharpeners to make the pegs.
Instead of using a reamer, I made a step approximation of a tapered hole with two similarly sized drill bits. The sizes I used were 1/4" and 9/32".
To do this, I first made a pilot hole with a tiny drill bit. Next, I drilled through the whole pegbox with the 1/4" bit. Lastly, I enlarged the hole on one side of the pegbox with the 9/32" bit.
Choose a hard, strong wood for your pegs. Real violins use ebony. I used black walnut. I ripped strips about 7/8" x 5/16" in cross section, then traced out the peg's shape. Orient the grain of the wood parallel to the axis of the peg. Cut your strips wider than mine so that you can tessellate your pegs and waste less wood.
I whittled the pegs to size with a knife. I used a drill bit gauge to approximate the taper. Test the fit in the hole. The peg will become smooth and shiny where it has been polished by the walls of the hole.
Once the peg fits at least partway through the second hole, a small hole (~3/32) can be drilled radially through the shaft of the peg to accept a string.
If you plan on making more than a few pegs, consider making Tim Anderson's peg hole reamer and peg shaver.
Step 4: Joinery
Figure out a way to solidly attach the neck to the box. Some real violins use three wooden pegs glued into holes in the neck and box. I used a tapered dovetail joint because the neck I made had a strange cross section. I chiseled out the positive on the neck, then shaped a stout piece of maple to receive the dovetail and connect to the rest of the box.
When you like the fit, glue it on. I had to add some shims to get the alignment right.
The receiving end should have thick sides to increase the contact area between it and the front, back, and sides of the box.
The section on fiddles in Foxfire 4 cites the use of a dovetail joint for this part of the fiddle. It also contains useful information on fiddle making.
Step 5: Box
In real fiddles, maple is commonly used for backs and sides and spruce is the preferred material for the top. I had a maple board, so I used that for the back and sides. I couldn't find spruce or pine, so I used some eastern red cedar, Juniperus virginiana, for the front. It's a native here in northeast missouri, and in lots of other places too.
Look for light, stiff woods. Light, because it needs to be moved easily by the vibration of the strings. Heavy or thick woods will sound quiet. Stiff, because it needs to resonate and not dissipate energy too quickly. Stiffness means a string will vibrate for a longer time unstimulated. If your friend with a violin says it's okay, go tap on their violin and listen for the hollow tonk it makes. Other wooden instruments do it too. That's the sound to go for.
The back of the box was made with two symmetrical boards, glued together to form a spine. I started with a maple board of approximate size 0.75" x 4" x 14". I ripped the maple board into two thinner boards on the table saw. The blade I was using could only make a cut about two inches deep, so I made two passes (one on either side) to cut through the four inch wide board. The kerf of the blade left me with two 4" x 14" boards of approximate thickness 0.3" I clamped the two pieces together and cut out the trapezoid shape with a hand saw. I planed the boards by hand to an approximate thickness of 3/32", mostly just aiming for somewhere between an eighth and a sixteenth of an inch.
To support the glue joint along the spine of the back, I made some ribs to go on the inside of the back of the box. The ribs were whittled from another piece of maple
I once saw a neat looking fiddle made with a wooden box that was intended to hold a wine bottle. Cigar boxes have also been used to make fiddle boxes. Liquor stores and smoke shops are good places to inquire about free wooden boxes.
I planed the sides just like I did the back. I fastened one end to the bench with a clamp and planed away from it. Sharpen your plane to reduce tearout. I used clamps to hold the sides in place while the glue set.
The face of the box was made of western red cedar. It was cut from a thicker board in the same way that the back was. The wood didn't plane well because of inconsistencies in the grain, so I used coarse sandpaper to reduce its thickness. I got it to about 3/32" in thickness.
Real fiddles have bracing to stop the soundboard from caving in under the pressure of the bridge. Under the bass side, there is the bass bar, a long beam glued to the underside of the soundboard. On the treble side, there is the soundpost. This post is wedged between the front and the back of the box, just southeast of where the bridge is.
I read about violin construction on the internet, then shaped a bass bar and soundpost out of the same piece maple that the rest of the box came from. I glued the bass bar to the back of the bass side of the the soundboard. I wedged the soundpost in to place before gluing the box shut. The section on fiddles in Foxfire 4 also has excellent pictures of the bass bar and sound post.
After all was glued and set, I went over the edges of the box with my hooked knife to smooth them.
Step 6: F-holes
Members of the viol family have funny f-shaped holes on the front of them. Part of the reason they exist is to let sound escape from the box. I don't really understand why there are only two of them, and why they are so goofily shaped, but I figure that there's been enough trial and error put into them that they're probably a good thing by now.
I took my artist friend's advice and made some sketches first. When I got something I liked, I traced it out onto the soundboard in pencil. I used a straightedge and a ruler to approximate symmetry about the center of the box.
Next, I drilled a bunch of small (~1/8") holes inside the traced profiles. I used a hand drill at high speed with a low feed rate to minimize tearout on the inside of the box. You could also do this before putting the box together, clamping a sacrificial block of wood beneath the soundboard to prevent tearout.
When the holes are drilled, carefully carve out to the edge of the traced line with a small knife. I didn't have an X-Acto or a small knife, so I used a razor blade instead. When this is done, invert and shake your nearly completed instrument to liberate the woodchips that have fallen into its box.
Step 7: Hardware and Strings
bridge
maple is traditionally used. I used maple also. orient the grain so it's in the same direction that the bow travels. I cut mine out with a coping saw, then whittled it thin. I shaped the tricky inside corners with small round and triangular files. It's best to leave the bridge tall until the strings are on, then it can be removed and trimmed down until the strings are held at a comfortable height above the fingerboard. Cut a shallow notch into the top of the bridge for each string to rest in.
tailpiece
this piece holds the strings at the tail end. It is attached to the endpin with cord. When the instrument is strung, the tailpiece floats above the soundboard. It's traditionally made from boxwood or ebony. I used black walnut. I cut out a rough shape with a coping saw and whittled it down. I drilled four 3/32" holes for the strings to pass through.
endpin
this pin is driven into the bottom of the box. It holds the tailpiece in place with cord. I used the drill bit gauge to fit it to the hole in the bottom of the box.
nut
the nut holds the strings at the right height and spacing after they leave the pegbox. Bone is a common material to make this part out of. I used a small piece of a deer's leg bone. I shaped it with a hacksaw, a coping saw and files. If you can't find a bone, or are opposed to the use of bone, use something that is also hard and easily shaped. Hard wearing woods are a good substitute.
strings
Old violins used sheep intestine. Nowadays, steel or metal wound synthetic strings are used. I used nylon fishing line and strands of bicycle brake cable. Go to your local small sports supply store and tell them that you're making a ridiculous instrument. If you bring it with you, they'll certainly give you strings for free or for cheap. I got a selection of trout line at a flea market. It's thick and works well.
You can also use steel strings. Single strands of bicycle brake cable work well for high strings.
When you're feeling good, string it up and pluck it. I ran the strings through the holes in the tailpiece, tying figure eight knots to stop them from slipping through. I spent a while plucking mine like a banjo and getting used to tuning in fifths
If you want to stop your instrument from turning grungy over time, give it a coat of varnish. Some real fiddle makers are very serious about their varnish. Old recipes for fiddle varnish call for strange things like garlic juice and volcanic ash. I used an old can of something I found in the workshop. "Rexpar Spar Varnish"
Spar varnish is extra nasty for added UV protection for spars on sailboats.
I just brushed it straight on, but you could thin whatever you use with a solvent like turpentine for a more even coat.
Step 8: Bow
Bows are traditionally made of pernambuco, an endangered Brazilian tree. Carbon fiber bows are becoming a popular alternative. I made my bow out of a piece of honey locust. You can use just about any kind of wood for this. The bow needs to be about two feet long.
Most bows for stringed instruments use horse hair. The long hairs come from the tail of the horse. It works very well. Hair has a directionality to it, like blades of grass. It's slick in one direction but grabs in the other. Bows work by repeatedly sticking and slipping while being dragged across a string. It's that stick-slip interaction that causes the string to vibrate. Here's a paper about how bows work.
My bow uses strands of thin fishing line instead of horse hair. If you use fishing line also, make sure it's thin.
I split a stick from a log of honey locust using a hatchet and a mallet. I whittled the stick until it was light and it flexed well. I cut six pieces of fishing line twice the length of the bow and doubled them over. I drilled a hole in the not-handle end and fed the loop ends of the fishing line pieces through the hole and back over the tip of the bow. Next, I whittled a peg with flat top to hold the strings above the bow. I drilled a hole in the bow at the handle end to accept the peg. The lines were drawn tightly over the peg, then the ends that remained were wrapped around the handle. I used a thin strip of bicycle inner tube to wrap around the ends and hold them to the handle. To tension the bow, I carved a sliding spacer about the same height as the peg. It is curved on one side where it touches the round bow stick. The other side is flat with raised edges like the peg. The spacer slides under the strings. The closer it gets to the attachment point at the end, the tighter the strings get. Tickle the strings so they rest next to one another rather than in a bunch.
Real bowhairs are dressed with rosin to improve their stick-slip characteristics. Rosin is dried pine sap. Gently scrape some from a local pine tree near you and rub it on your bowhairs.
Fishing line tends to work better if it is scuffed with some sandpaper.
If you don't want to bother with all of this bow business, you can also just use a rosined stick. Rub some dried pine sap on a smooth stick and use it in the place of a bow. People used to make toy fiddles entirely out of corn stalks, even the bows. I read about cornstalk fiddles in Foxfire 5.
Step 9: Learn to Play
The song I'm learning here is called Irish Washerwoman.
Next, start playing in a band. I practiced for a couple hours a week. This song is called Britches Full of Stitches. On the left is our excellent guitarist Jon, check out his page here. On the right is the world-class accordionist Darien. This is his page.
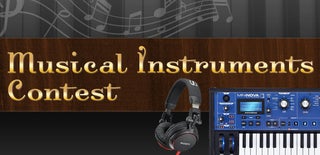
Grand Prize in the
Musical Instruments Contest