Introduction: Internet Enabled Raspberry Pi Pet Feeder
This is a dog feeder powered by a Raspberry Pi.
If you want:
- an easy way to feed your big dog
- keep track of when you feed
- control how much and how often you feed
- and optionally be able to feed remotely through email when you are not around
this is a project for you :)
If you have all the parts around, it should take a couple of weekends to get this done.
Please feel free to modify and share your mods.
Step 1: Parts Needed
- Raspberry Pi 2 Model B
- Breakout board. cobbler and cable for Raspberry Pi
- 16x2 backlit LCD
- 12V high torque DC motor
- Zevro WM100 Cereal Dispenser
- Wireless dongle for Raspberry Pi
- 1/4" D-shaft for dispenser
- 1/4" to 6mm coupler for motor
- Two pushbutton switches
- 12V power supply for DC motor
- Mini USB power supply for Raspberry Pi
- Wood for box
- Jumper cables
- Tube to make the kibbles flow to the bowl (optional)
Step 2: Breadboard Assembly: Switch Controls
The switches provide controls to operate the feeder. There are two pushbutton switches in this design.
One for controlling the feed motor. The other to reset the feed timer.
- First connect the cobbler to the Raspberry Pi using the ribbon cable. Take care to orient the red line on the cable to the corner of the Raspberry Pi
- Place the cobbler on the breadboard
- Connect one terminal of the feed motor switch to pin #6 on the cobbler. The other terminal goes to ground on the cobbler
- Connect one terminal of the reset switch to pin #13 on the cobbler. The other terminal goes to ground on the cobbler.
All the switches are done!
Step 3: Breadboard Assembly: LCD
The LCD panel is programmed to have a clock, a feed countdown timer and status messages while feeding, resetting etc.
Here are the steps to connect the LCD panel to the Raspberry Pi through the breadboard and cobbler.
- Solder header pins to the LCD panel and a small PCB to the other end of the header pins. I used an old PCB and cut it to size. This makes taking the cables out to the breadboard easier
- Place a 10K Ohm potentiometer on the breadboard
- Connect +5V and ground to the left and right legs of the potentiometer
- Connect the following pins from the LCD to the cobbler:
- Pin #1 (VSS) connects to ground (black wire)
- Pin #2 (VDD) connects to +5V (red wire)
- Pin #3 (VE) connects to the middle leg of the potentiometer
- Pin #4 (RS) connects to the cobbler #25
- Pin #5 (RW) goes to ground (black wire)
- Pin #6 (EN) connects to cobbler #24
- Skip LCD Pins #7, #8, #9 and #10
- Pin #11 (D4) connects to cobbler #23
- Pin #12 (D5) connects to cobbler #17
- Pin #13 (D6) connects to cobbler #21
- Pin #14 (D7) connects to cobbler #22
- Pin #15 (LED +) goes to +5V (red wire)
- Pin #16 (LED -) goes to ground (black wire)
There is a very nice detailed write up of the LCD wiring at modmypi.com
We will use the Adafruit library for programming the LCD (more details on that later)
Step 4: Breadboard Assembly: DC Motor
The high torque DC motor is a 12V 3.5 RPM motor with a 6mm D-shaft on it.
It is a simple transistor based circuit with the raspberry PI pin # 19 providing the control signal
Connect as shown in the diagram.
Note that the 12V power supply is a separate power supply just for the motor.
The ground for the 12V power supply and Raspberry Pi's ground will connect together.
Essentially the transistor acts as a switch control by the HIGH on the Raspberry GPIO pin to switch the motor on/off
Step 5: Programming the Raspberry Pi
Here's the basic idea of the pet feeder
- Should be able to press a button and get a measured amount of feed in the bowl
- No overfeeding. Disable the feed button for 8 hours after feeding
- Over-ride the disabled feed button with a reset button
- Accidental press of feed button, while disabled, should pop up friendly message on LCD
- Display a clock and the time left for the next feed as a countdown
- Trigger the feed through an email to a gmail account
- Trigger a query to know when the last feed and next feed can be using email to a gmail account
- Do some fun replies with Chuck Norris jokes and/or numbers trivia :)
- Make the system immune to reboots by starting the program automatically on reboot, saving state to files etc.
Attachments
Step 6: Connecting the Zevro Dispenser to the DC Motor
The Zevro is pretty cool since it takes care of dealing with large kibbles for the dog.
It comes with a mounting kit and a knob. Discard the knob and its attached plastic D-shaft.
- Use the metal 1/4" D-shaft cut to size for your motor position. It might a tiny bit loose on the Zevro side. Nothing that a cut up credit card shim can't fix :)
- Mount the motor securely (I used an L bracket)
- Connect the D-shaft from the Zevro to the motor using a 6mm to 1/4" coupler
- Mount the Zevro to one of your panels
Step 7: Optional - Dispenser Chute
Didn't want to bend down to press the button and didn't want the dog to knock off the clear plastic container with the food. But a high mounted Zevro ends up in kibbles dropping from too high and bouncing off the feeding bowl
Hence the dispenser chute
Essentially a cheap 3" drain pipe and an elbow joint.
Some duct tape to make sure kibbles are directed into the bowl.
Step 8: Box and Paint
Make a small box to put it all together and paint it
Make a hinged door to keep things serviceable, if needed
Operations Manual :)
- Just press the button to feed
- Or send an email with the subject "When" to query when the last feeding was done
- Or send an email with the subject 'Feed" to feed the dog!
Here's a video of the project in action. Enjoy!
Step 9: Adding a Camera
The pet feeder has been working pretty flawlessly for the past several months.
The one thing that is missing is positive confirmation that the dog is actually eating the food once remotely fed.
Raspberry Pi camera to the rescue!
Here's where to get the camera and installation instructions:
https://www.adafruit.com/products/1367
Once physically installed, here's a code snippet you can add to the original code to get your camera integrated into the pet feeder. This code takes a time-stamped picture and saves it to a file. You can take this file and email it if you like.
In the sendmail function in the earlier code simply substitute the "attach=None" argument with "PICFILE" and you should be able to receive the file.
Attachments
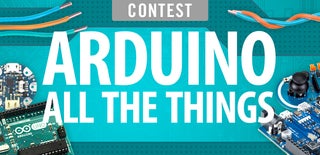
Participated in the
Arduino All The Things! Contest