Introduction: Kitchen Remodel on a Budget
My wife and I purchased our home in 2001 and we knew at some point we would remodel our small kitchen. After 18 years (and three kids) we decided it was time. In order to save money we knew we would be doing the majority of work ourselves- and we knew this was going to be a complete gut job right down to the studs.
Remodeling a kitchen can be a scary proposition- it takes a lot of time, costs a lot of money and mistakes can be very expensive. If you're on a budget like us (and who isn't!) it can be a real minefield navigating all of the design decisions and trying to figure out how to get the most bang for your buck. Based on the before and after photos I'd say we met all our goals and made every dollar count!
Be sure to click on the build photos as most of them have notes.
Here's how we did it!
Step 1: Design Considerations
Organization is the key.
Our kitchen is fairly small with a footprint of roughly 92" x 120"- about 77 sq. ft. My wife and I always have a bit of a laugh when we watch home remodeling/buying shows and you see the buyers walking into ginormous kitchens with a 30+ sq. ft. island and the first thing they say is "Well, it's a little small..."
We've never had any problem cooking for our family or even up to 20+ people in our kitchen- but with two people in there it was pretty crowded. The way the kitchen was arranged was OK in terms of total storage space but it lacked working countertop surface area, the pantry wasn't user friendly (I also constantly hit my head on the shelves), the refrigerator door couldn't open fully (which frustrated my wife to no end) and you frequently had to close one cabinet door or appliance in order to access another area. There was also a lot of dead cabinet space in the corners.
The other big issue was that the kitchen was really dark and closed in and the sight lines into the dining/living area were terrible. It was time for a new floor plan.
We decided to organize the kitchen into working areas that made sense for how we use it. Food and dry goods are at one end of the kitchen and cooking at the other with dishes and pot/pans in between. In a small kitchen just moving things around a few inches here and there and reorganizing your workflow can make a world of difference. We wanted to maximize all of our available storage space and yet at the same time increase our physical working area and make the kitchen feel larger without increasing the footprint- a tall order.
Here's what we did:
1) We relocated the refrigerator to the pantry area. This allowed us to gain additional floor space and the refrigerator door could now fully open. You can fully remove shelves and storage bins from the refrigerator!
2) We moved the pantry to the old refrigerator location and split it into upper and lower sections. We were able to retain the same pantry shelf/storage area as before but now we gained additional countertop area next to the oven (which we also moved closer to the sink by a few inches)- very handy for baking and cooking prep. We could now have both the pantry and refrigerator fully open at the same time, which is really nice when putting away groceries after shopping.
3) We relocated the dishwasher next to the sink. The old dishwasher location (at a right angle to the sink) didn't make sense- it was always awkward trying to load/unload the dishwasher because you always had to reach out over the open door.
4) The trash/recycling got moved next to the dishwasher. The trash used to be in the bottom of the old pantry area so if you were unwrapping food or scraping dishes you always had to go across the kitchen- it just didn't make sense.
5) We made the sink smaller. Yes- smaller! By installing a smaller sink cabinet and a single bowl sink we actually got more usable area both in and around the sink. A single large bowl sink fit baking sheets and cooking pans better than our old double bowl sink and we gained countertop space. The smaller cabinet allowed us to move the dishwasher next to the sink.
6) Removing the partition wall and overhead soffits and extending cabinets all the way up to the ceiling made a huge difference. Even though we removed overhead cabinets (looking out into the dining area) we gained that storage space back by extending the remaining wall cabinets up to the ceiling. We were also able to add a cabinet over the refrigerator in its new location. Removing the partition wall and soffits really opened up the kitchen- the sight lines are a night and day difference. The kitchen didn't feel cut off from the rest of the house anymore. If you are even the slightest bit unsure about removing or relocating a wall consult a structural engineer.
7) We shrunk the countertop area next to the dining room. This countertop area was 36" deep- by reducing that to 26" we were able to gain a huge increase in kitchen foot traffic area and relocating the base cabinets allowed us to move the dishwasher next to the sink. The base cabinets underneath this countertop now hold serving dishes since this is the area that faces the dining room. Because we removed the partition wall we gained back a few square inches at the edge of the countertop and pushing the countertop back gave us better access to the countertop/storage area around the sink- the net result was a lot more useable space as well as a larger entry path into the kitchen.
8) We added a lazy Susan cabinet to the corner by the stove. The old corner cabinet made it just about impossible to use the corner space for storage- it was like a black hole. Whatever went back there stayed back there. Now we keep cooking utensils, colanders and other frequently used odds and ends in the lazy Susan and it's all immediately accessible.
9) Open shelving makes the kitchen feel larger. By adding floating shelves to the corners by the sink we gained back some storage space (helping keep items off the countertops) and it kept the area around the sink feeling more open.
At the beginning of our planning stage I had a contractor friend come over and have a quick look at things to make sure I wasn't missing anything out of the ordinary- sometimes just having a second set of eyes on something like a project this big can result in coming up with a better layout or bring to light something you hadn't thought of that could turn into a much bigger problem later. I drilled small holes in the soffits and walls and used a borescope to look into the walls to make sure there weren't going to be any major electrical, plumbing or venting obstructions that would throw a wrench in our plan. We originally had thought about the possibility of stealing space from a hallway closet but a flue pipe situated in a boxed in wall section put an end to that real quick as relocating it wasn't even remotely feasible.
Now that we had a plan we had to figure out our budget...
Step 2: Budgeting -both Time and Money
Figuring out a budget for a project like this is always a bit of a double edged sword. We don't have a money tree in the backyard but we still wanted to buy good quality materials. As far as time was concerned the longer our kitchen was going to be out of commission the more expensive it would become in terms of both work hours and cost of potentially eating out (which for a family of five can get really expensive really fast.)
It's also really important to check out current building codes and file for necessary permits.
Labor plan-
I figured I could take a total of 9 days off work and not dip too far into my paid time off. Adding in my normal days off per week meant I had 12 days in row to get the majority of work done. I called in a contractor friend (he would help with demo, flooring and drywall for a reasonable fee) and we figured out a rough schedule:
2 days for demo work
2-3 days for flooring
3 days for drywall and electrical
1 day for paint
2 days for cabinets
1 day for plumbing
I would order the cabinets and once I had an arrival date we could begin construction. Once that work was done I could have the kitchen measured for countertops (approximately a 4-5 week total process) and I could work on finish/trim work, backsplash tiling and shelving on upcoming weekends. This meant I could have a working kitchen in 12 days and take my time doing finish work. Total build time start to finish was less than 8 weeks.
In order to save money on eating out we set up a small table with our toaster, coffee pot, microwave and crockpot/instapot. We also have an outdoor grill we could use for cooking. We moved our old refrigerator into our garage so we still had access to cold food. We used the sink in our laundry room for washing dishes. Not having a kitchen sink was probably the single most annoying thing about having our kitchen torn apart.
Disposal costs can also add up fast. We salvaged as much as we could of our existing kitchen and donated materials (old sink, cabinet hinges, etc.) to our local ReCycle center. Instead of a rollaway dumpster we were able to fit construction waste into a Bagster.
Materials estimates-
Cabinets- $5200
Flooring- $300
Electrical/lighting- $500
Plumbing- $150
Drywall- $350
Backsplash tile- $350
Sink- $175
Countertops $2500-3300
Appliances-
Our dishwasher, oven, faucet and sink disposal were all in good shape. We did need to purchase a new refrigerator and microwave. I did an enormous amount of research on refrigerators. When we originally began planning our kitchen we thought we might want to put in a 36" wide counter depth refrigerator as they are quickly becoming the most popular size unit. After looking at our available space it made much more sense to go with a 30" wide standard depth unit. The depth would fit fine in the pantry area and the total storage capacity would be the same. Going with a 36" wide refrigerator would have cost us about $2500 extra as not only are the refrigerators more expensive but we would have needed to bump out the wall 6" in order to make it fit and we would have had to move a return air duct in the floor -it just wasn't worth it. We specifically did not want a water/ice dispenser in the door as the vast majority of complaints centered around this feature- especially with french door refrigerators.
In the end we settled upon this really nice KitchenAid single door model.
We thought we might want to install a vent hood above our oven but then the microwave would have had to live on the countertop, which didn't make much sense. Because of this we went with a venting microwave mounted above the oven. We chose this nice slimline Whirlpool microwave and it does everything we need and because it's so slim it frees up a lot of room above the oven.
I found the best pricing I could online and my local appliance supplier was able to match it- both appliances were $2250 delivered.
At this point our total budget including helper labor was around $16-17k, which is right where we wanted to be.
Step 3: Demo Work
Once the budget is figured out and cabinets have arrived it's time for demo!
After shutting off power and water we began by rolling out thick construction paper on our floors to protect the wood. Dismantling the overhead cabinets and non structural partition wall came first. Sometimes the best way to do this is to use a sawzall to cut right through framing nails- it's both faster and safer than pounding studs with a sledgehammer. The areas above the soffits were not drywalled in (we expected this) so we had insulation falling down on us while doing this.
We were sure to be extra careful around any areas that would contain electrical wiring or plumbing!
With the partition wall/countertop out of the way we could then move the oven and refrigerator out more easily and then remove all of the existing cabinetry. The cabinets were so bad they literally fell apart in our hands. After that came any remaining drywall that would need to be replaced due to previous damage or removal because of electrical rerouting and fitting of new boxes to wall studs.
We also removed all of the old parquet flooring at this time. I had previously encountered this last bastion of 80's design when we installed wood floors in our dining area and I had my secret weapon ready. After the flooring installers tried everything under the sun to remove the incredibly stubborn glued down tiles (including a very large, very loud industrial scraping machine) I improvised a removal tool by grinding a sharp edge on a garden border spade shovel. I found I could ram/slide the sharp edge of the spade under the wood tiles and with a bit of leverage they would pop right up. This improvised tool saved several hours of work- I offered to let the floor installer keep it because he liked it so much! Luckily our subfloor was in great shape and didn't require any repair work.
With the partition wall and soffits removed we were beginning to get a glimpse of how much more open our new kitchen would be!
Step 4: Flooring
We decided early on that we wanted tile floors.
When we installed our wood floors throughout the upper floor of our house we thought we might extend them into the kitchen area. Wood floors in kitchens just look fantastic and they're nice to walk on. Unfortunately all it takes is one little unnoticed water leak to destroy them. Many of our friends have wood floors in their kitchens and every single one of them said they would never do it again. So we chose tile.
The big advantage of ceramic tile is that it's cheap and durable- with three kids, two cats and a large dog that's what made the most sense for us. The disadvantage is that it can be cold (especially if it's on ground level on a slab) and hard on your feet if you're standing in the kitchen all day. If I were a professional chef I don't think I'd want to be standing on tile all day. Another option is vinyl plank flooring- there are some varieties out there that are very resistant to water damage and it comes in a huge variety of finishes but it can be costly.
The tile we chose was the same variety as what we used in our bathrooms. At $1.19 per sq. ft. it's tough to beat for our requirements. The 12" x 24" tile size suited our space well too. I brought home a few different color examples and we went with a concrete gray color as it provided a nice transition from our wood floors while not being too dark for our small kitchen.
A moisture barrier was put down underneath a backerboard and the tile was adhered using an appropriate mortar. It's super important to try and get the floor as level as possible as this will make installing cabinets and leveling appliances much easier later on. We also brought in one of the base cabinets and positioned it where the end of the peninsula would be located in order to get an idea as to how we would transition the tile to the wood floor in that area. After the tile had properly set it was grouted in with a Pearl Gray grout (I had a fair bit of this left over from when our bathrooms were remodeled.)
Step 5: Electrical and Plumbing
On to the electrical...
Since we were relocating the refrigerator we needed to move an outlet to the new location and code also required GFCI protected tamper-resistant outlets to be located within 24" from any break in the countertop (as in a sink or oven) as well as within 24" from the end of a countertop located against a wall. We were good with already having two 20A appliance circuits and a 15A circuit for lighting. Refrigerators in residential spaces are not required to be GFCI protected.
We also needed to relocate the light switches and outlet that were situated in the now removed partition wall. When relocating items like this I always take photos of the existing wiring and label everything to avoid confusion later on. When you start remodeling you often find all sorts of "interesting/creative" wiring that needs to be corrected- usually improper grounding and lack of strain relief at the electrical boxes. When wiring new boxes I always make sure the wire is long enough to stick out 6" from the box- nothing is worse than trying to replace an outlet or switch and not having enough wire to maneuver things around. I also tend to avoid push fit backstab connections in receptacles as they have a tendency to fail- I much prefer wiring to be secured by screws.
One thing I did do was replace all of the electrical boxes anywhere that would be tiled over later. I installed adjustable depth boxes which are awesome for tile work as they allow you to easily set the box to exactly the right depth from the drywall so when you tile later on they can be perfectly flush.
For lighting we wanted something really simple so I found some really great flush mount LED lights- these lights are awesome! They are super low profile, very simple to install and they have a separate driver box that is easy to wire plus you can change the color temp of the light, which is really nice. At $30 each they are a bargain. I installed these in the existing light locations. At this time we also decided to replace the light over our dining room table (not originally in our budget!) with a light that would match the smaller pendant light we would install over the kitchen peninsula.
And plumbing...
Plumbing was pretty straightforward as we were going from a double bowl sink to a single bowl so it actually simplified things a bit. However I did manage to screw things up and measured the base cabinet dimensions incorrectly so I had to move the sink waste line over a couple inches for clearance- not a big deal. Since the new sink would be plumbed differently I had to replace everything forward of the elbow coming out of the wall. This meant installing a "T" fitting for an air vent (I like the kind that screw in place) and a new trap for the disposal outlet. The air inlet vent must be placed at least 4" above the waterline in the sink trap.
Relocating the refrigerator also required a new water line for the icemaker so that was run. It was bit time consuming but worked out just fine. The cold water line to our water heater is located in our basement downstairs underneath our kitchen so I just needed to drill a hole through the subfloor and route the copper line along the floor joists to the shutoff valve. For around $30 in materials I was good to go.
Step 6: Drywall Work
I must admit I am not a huge fan of drywall work.
I'm OK with cutting drywall and screwing it down in place but I'm not really good at finishing it. Luckily for me the guy I hired to help on this project is awesome at drywall and I learned a lot from him. Getting the drywall in place was no big deal- just screw it in and tape the seams with patching compound. I keep some of this compound around the house for quickly fixing dents and holes in walls- it's great stuff.
Once that's done the finishing begins. A smooth finish isn't hard to get- it's when you have to texture a surface to match an existing surface that can be a bit tricky. In order to do this joint compound is thinned down and sprayed through a hopper texture spray gun. Once it starts to dry a bit it can be scraped down using large steel spatulas. If done right it just skims a bit off the top and leaves a nice slightly flattened textured surface. If the joint compound hasn't dried enough it will just smear around. Once everything fully dried I used a sanding sponge to smooth over any rough surfaces.
Next I primered all of the surfaces and finish painted all areas that would not be covered by cabinets or tile. Drywall should be primered before installing backsplash tile. My favorite paint to use is Valspar Signature as it's reasonably priced and has great coverage and a nice finish. Don't believe the "paint and primer" bit though- drywall should still be primered before painting as you'll get a better finish and unfinished drywall can really soak up paint. I used eggshell on walls, semi-gloss for trim and flat for the ceiling.
Step 7: Ordering and Installing Cabinets
We were very particular about cabinets.
Cabinets represent the single largest portion of our budget and it is flat out nuts how much you can spend on them. When we first started planning our kitchen I did a ton of research and looked at everything from big home improvement store brands to RTA (ready to assemble) cabinets to even building them from scratch.
Most everything I found was either obscenely expensive or had poor to marginal case construction for what they cost. Fortunately I found an online supplier with exactly what I was looking for- Cabinets.com
I have to say I was pretty leery of ordering cabinets online but I read a lot of good reviews so I ordered a couple of sample doors (at no charge) and we thought they looked really nice. All of their cabinets feature solid plywood case construction (no particle board or MDF) and high quality soft close hinges and drawer slides. When ordering cabinets there are also a few custom options that are available, such as selecting door opening direction, glass doors and cabinet depth. All cabinets arrive fully finished with drawers and doors installed. Orders over $2500 ship free.
We wanted to use European style cabinets since they maximize the cabinet space due to the lack of face frames- we need every square inch we can get in our small kitchen. The style/color we chose is an off white called Lombard Maple Alabaster. The cabinets are built to order and the lead time is 5-8 weeks. I ordered them at the end of the year (when they ran a 20% off sale plus an additional promo code for another 5% off- and they run them frequently) as well as toe kick trim and spacer panels to fit near the dishwasher. The 3" wide spacer panels are necessary for handle clearance when opening the dishwasher and trash receptacle.
The total for our order (14 cabinets plus trim panel/spacer panels and toe kick panels) came to $5112.04
I also ordered our kitchen sink at this time. We chose a Dawn 22" single bowl undermount stainless sink. This is the largest sink I could find that still fit in 24" wide sink cabinet and the price/quality is excellent.
Time to install cabinets!
One trick I did when doing the drywall installation was to make a map of our wall stud locations by taking photos and measuring the distances between studs- it also gave me a good future reference for any electrical and plumbing lines. That way I knew exactly where to locate cabinet screws during installation.
Before installation began I made a vent cover box for the floor vent that is situated underneath our sink cabinet. The vent box is a sealed enclosure that directs air out from under the sink cabinet and exits through a grate in the toe kick. This was made from scrap lumber, covered inside with aluminum duct tape and sealed tight to the floor. I didn't know about it at the time but you can now buy ducting kits for this if you don't want to build a box.
I started with the wall cabinets as it a lot easier to install them when you don't have to reach over the base cabinets. I also removed the doors and the shelves to make them lighter and reduce the risk of damaging a door. I started in the far corner and screwed a ledger to the wall to support the wall cabinets during installation. Installing wall cabinets is definitely a two person job- my son held the cabinets (supported by the ledger) while I screwed them in place.
Rarely do houses have square/plumb walls and level floors so cabinets frequently require shimming to get the cabinet faces even. The cabinets have anchoring slats across the upper and lower back so when driving in anchoring screws be sure to have the screws go through any shims to hold them in place. Cabinets should also be screwed to each other through the cabinet side panels (make sure to use the correct length screw so it doesn't poke through!)
Base cabinet installation begins by checking the floor with a level and locating any high points- this is where you want to start, preferably in a corner. I started with the lazy Susan cabinet and worked my out from there, shimming as necessary and checking the top surface of the cabinets to make sure they were level. Holes were cut in place in the back and bottom of the sink cabinet to accommodate plumbing. This is definitely an area where you want to measure twice and cut once. Once the sink was fixed in place with silicone adhesive and the undersink plumbing was installed I installed the dishwasher and the 3" wide filler strips.
Next came the peninsula base cabinets. These were anchored to the floor using 1x2 strips and screws through the bases/toe kick area. Finally I installed the cabinet that sits above the refrigerator in the old pantry area. This was accomplished by fitting 1x4 solid wood slats as fillers and screwing the cabinet in place through the side panels. The fillers were necessary because the cabinet is the same width as the refrigerator (30" wide) and the refrigerator requires breathing room on each side.
After all the cabinets were in I reattached shelves and doors and made any necessary adjustments to the hinges to get the doors lined up properly.
If your existing cabinets are in good condition you can save a ton of money by updating them by either refinishing/painting them and/or installing new doors. If functionality is a concern take a look at Rev-A-Shelf as they make several different types of cabinet pullouts that greatly improve storage access.
Step 8: Trim and Painting
Now it was starting to look like a kitchen again!
To finish off the peninsula the side of the end cabinet was faced with 3/4" birch plywood and the 1/4" thick finish paneling was attached to the cabinet backs and side of the end cabinet over the plywood. I then fit the toe kick panels and ran baseboard trim around the peninsula back/side as well as around the refrigerator cutout.
Next I fit corner moulding to the peninsula corners as well as a trim strip along the top edge. This tied everything together really nicely and gave it a finished look.
Since the backsplash tile was going to go all the way to the ceiling we decided to install trim around the window as well in order to have a finished edge for the tile to butt up against. The window ledge was removed and replaced with a longer piece that would accommodate the width of the trim that would go around the window. For window trim we used the same profile that went around all of the doorways in our house to tie it in for a cohesive look.
The paneling on the back and side of the peninsula was already finished with the same color as our cabinet doors so all I needed to do was prime and paint the remaining wood trim and baseboards.
At this point in time our refrigerator and microwave had arrived so they were installed and I took some scrap plywood and placed it on top of the cabinets so we could begin using our kitchen again while we waited for our countertops to arrive.
Step 9: Countertops
Choosing countertops... decisions, decisions.
When shopping for countertops we again did a ton of research. It's always a tossup between usability/durability/appearance and cost. We weren't big fans of granite. Soapstone, while gorgeous, was too dark for our small space- not to mention bananas expensive. Solid surface material like LG HI-MACS (similar to Corian) looked nice and the pricing is great but the reviews were a bit mixed on it in terms of durability.
In the end it came down to two contenders- butcher block vs. Silestone Quartz.
Butcher block can be extremely durable (as in it will last forever as long as you use end grain or edge grain variety of a good quality hardwood) and it has a wonderful warmth to it. It's softer than stone or a solid surface top, which is both good and bad- it won't damage dishes as easily as stone and it's quiet when you place dishes on it BUT it also scratches easily, you can't let water pool up on it and it can look a bit beat up if not properly maintained (although some people call that character.) It requires a bit of maintenance (coating with food grade mineral oil every 6 months) but it can be easily refinished in place and doesn't require specialist installation. You can use knives on it! It's also very affordable relative to a lot of other options and provided it's in stock the lead time is zero. Most butcher block material is around 1.5" thick. If you install it yourself you can find nice material for under $20/sq. ft.
Quartz is also extremely durable and is about the lowest maintenance material out there. If you want a material that looks beautiful that you can just install and forget about it then quartz is for you. It has a wonderful high end feel to it. Standard thickness is typically 30mm. Sink cutouts are typically $300 ish and fancy edges cost extra (an eased edge is usually standard.) Quartz must be installed by a professional shop and as such prices range from around $70/sq. ft. to WHAT IN THE HE HAW ARE YOU THINKING- IS THAT QUOTE FOR REAL?!
So of course we chose Quartz. Because that's what my wife reallyreally wanted.
She wanted a bright white countertop (we chose White Zeus Extreme- where do they get these names?) to keep the kitchen light and felt that butcher block was going to be too dark in our space and the maintenance would be a bit much. As usual she was right so I went to get quotes for Quartz. The rule here is shop around, read testimonials and wait for sales (if you can.) The first quote I got from a recommended shop was an eye watering $5942 -about $156 per sq. ft. and waayyy out of our budget. While I'm sure that shop did fantastic work there was just no way we could afford that.
After shopping around and seriously thinking about butcher block again I heard our local Lowe's was having a 20% off sale on Silestone Quartz. I used a Lowe's charge to save another 5% (which we immediately paid off as soon as the bill arrived) and we got the countertops we wanted for $2594- roughly $68 sq. ft. installed including sink cutout and eased edge. Before signing on the line I found out the name of the local supplier/installer and checked out reviews on them.
When all was said and done it did take a total of about five weeks from order to install but they did a fantastic job, they look amazing and are exactly what we wanted.
I would say in situation with a slightly larger kitchen with an island I would be tempted go with a butcher block island surface and Quartz everywhere else. If you mix the two materials and they share a common edge (say if you did Quartz in a sink area and butcher block on adjacent areas) make sure to adjust the cabinet heights to accommodate the difference in material thickness.
Step 10: Tile Work
Now that countertops were in we could choose backsplash tile!
Tile is one area where you can save a lot of money as the price range could be anywhere from $4 to over $20 per sq. ft. Originally we thought we would go for traditional size subway tile and I brought home multiple samples of different colors and textures as well as glass and porcelain varieties. With white cabinets and white countertops we wanted a bit of color for the backsplash tile- something in the blue/gray area that would pull a bit of the blue tones out of the floor tile and yet not be too dark overall. The color of the countertops and grout will definitely affect the appearance of the tile.
We also looked at tile with a glazed crackle finish as it can be very subtle and beautiful but we couldn't find any in just the right shape/color combination. If you use tile with this surface finish be sure to apply a sealer to it before setting and grouting as mastic/thinset and grout can get into the tiny cracks and it will be a nightmare to remove.
In the end the tile that won was Elida Ceramica Havana Nights- a smaller mosaic subway tile that has a really nice color that isn't too gray or green with just a little bit of blue in it. The alternating pattern and smaller size made it a lot more interesting looking than the larger more plain subway tile we had seen and the size seemed to fit our kitchen space better. At less than $5 per sq. ft. (we needed about 43 sq. ft. total) it was definitely priced right too.
One thing about tile that you have to consider is how it's going to look next to trim and how it is going to fit in a corner or look if you have an exposed edge. It's important to consider the overall thickness of the tile and also allow for the thickness of the tile adhesive.
Tile Installation.
Speaking of adhesive, you basically have two choices- mastic or thinset. While I would never use mastic in a bathroom or any area that would be immersed in water it's perfectly fine for a kitchen backsplash. The advantage of mastic is that it's premixed and it's faster to use than thinset. Mastic is super tacky so it holds tile to a vertical surface really well. If we had gone with a glass tile then I would have used thinset as glass tile isn't compatible with mastic due to the transparent nature of the glass. Many tile manufacturers will recommend a particular adhesive to use.
The tile was installed over a weekend. I was lucky enough to be able to borrow a wet saw from a friend to do the majority of cutting, saving me the time and trouble of renting or purchasing a saw (and reselling it on craigslist afterward.) Small trim cuts were made using a diamond blade in an angle grinder in order to cut tile to fit around electrical boxes.
When setting tiles I start with a full height layer on the bottom row. Subway tiles in a corner are set in an alternating pattern so it looks more continuous as it wraps around the corner. Smaller mosaic tiles are typically adhered to a netting material which makes them easier to apply. You can cut through the netting with a utility knife in order to make small adjustments to tile spacing- sometimes this is necessary when working around things like electrical boxes and wood trim so you don't up with thin slivers of tile to fill in a gap. Setting tile isn't as much hard to do as it is time consuming, especially when you have to cut a lot of little trim pieces.
It's usually less expensive to go with a grout that isn't pre mixed but I was pressed for time so I went with pre mixed grout this time. The nice thing about pre mixed grout is that it's super consistent in terms of color and thickness and the type I used doesn't require any sealing afterward. Typically sanded grout is used when you have to fill larger gaps (say over 1/8") and unsanded grout is used for thin gaps.
Step 11: Shelving
The final project was to install floating shelves.
Floating shelves have a really nice open feel. For this we wanted something that was a bit more rustic and warm so we opted for using reclaimed wood that used to be flooring in an old factory. This was basically an edge grain 1.5" thick butcher block material made from various hardwoods with a nice color that complimented the Hickory floors in our house.
The material came in 12" wide sections so I first cut it down to 10" width. Each shelf was then cut to 24" length. After that it was cleaned up just a little bit with a planer and holes were drilled in to accept mounting pegs.
The pegs were screwed into studs in the walls to provide adequate support. Of course this meant I had to drill holes through the tile I just set! Drilling holes in tile can be a bit of a pain- for this job I used these Bosch tile drills and they worked really well. Just remember to go slow and frequently dip the drill bit in water so it doesn't overheat. Let the drill bit do the cutting- if you push too hard you can crack your beautiful tile you just set.
The most difficult part of this project was getting the holes for the pegs in exactly the right spot so everything lined up properly- it really helps to make a drilling jig or template. Once drilled the shelves are then pushed onto the pegs and tapped into place with a mallet. The bottom edges of the pegs have a knurled surface that provides a tight friction fit so the shelves are held onto the pegs securely. If screwed into the wall studs these are quite strong and can hold a fair bit of weight- I wouldn't set a large bag of dry cat food on them but they'll hold small dishes just fine.
Step 12: Finished!
This is by far the biggest project I've ever taken on.
It was a tremendous amount of planning and work but we are thrilled with the results and we now have the bright, open and super functional kitchen we always wanted. And we didn't go totally broke doing it! By doing a lot of the work yourself and being careful with materials selection you can save a tremendous amount of money. I'm not a contractor and this is the first kitchen I've ever remodeled. The trick is to plan ahead, try to anticipate things that could go wrong, be flexible if you have to make design changes and know your limits. There's nothing wrong with hiring help to do the parts that you are uncomfortable doing or because you need help getting it done in a reasonable amount of time.
I read an awful lot of books and guides before embarking on this project. My go to resource for all things remodeling is Fine Homebuilding. I have found it to consistently be the single best resource out there especially when I have technical questions regarding structural work, plumbing and electrical. The books they publish are all excellent guides for DIY home improvement. When remodeling a home you never know what is going to come up when you start tearing things apart and the more knowledge you have the better informed you are about making cost effective decisions, whether you are doing the work yourself or hiring someone else to do it.
The trouble with projects like this is that it can be a bit addictive- now I want to do even more home projects!
If anyone has any questions please just let me know- thanks!
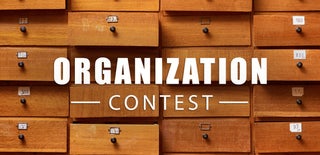
Participated in the
Organization Contest