Introduction: Lathe-Mounted Disc Sander
Sanding machines are fairly common in most woodworking shops, with models ranging from small tabletop versions to high-powered floor models. When still living at home, I used a combination belt/disc sander in my minuscule shop to shape and correct nearly every part I cut. Today, my workshop shares a garage with two cars and has the requirement to be moved every four years (I’m in the Air Force) so space is still at a premium. With that in mind, I'm always looking for dual-use equipment.
I had a small 10” disc sander from a discount manufacturer for a number of years before it fell apart and instead of getting another, I decided to attach a disc to my lathe instead… It’s a 1.5 hp motor on a level bed so all the parts are there; you just need a table. Talking speeds, most sanders run at ~1700 rpms while wood lathes usually vary from 0-3500+ so we're definitely in range. About the only thing you'll need to order is the paper and a dust collector port.
Supplies required:
2x4' sheet of plywood
3' 1x8" hardwood material
Dust collector flange
Sanding discs
Tools required:
Lathe with a faceplate
Table saw
Miter saw
Handheld router with straight bit
Drill/driver
Shoulder plane/chisels for cleanup
Step 1: The Disc
A 12” sander can cost a few hundred dollars. A 20” will set you back over a thousand. For this project, you’re only limited by the size of your lathe and the discs you can buy. Home stores carry 10-12” versions but I found a good selection of 10-20” versions on Grizzly. They’re PSA backed and used for either bench or floor sanders so they’ll work fine for this project.
For speeds: most sanders run around 1700 rpms. Wood lathes go from 0-3500 depending on your controls so we’re good to go there.
My current lathe has a 16” capacity, so I’ll be building a 15” disc for clearance. Take a 2x2’ piece of 3/4” plywood and cut two circles: the 15” one and a 6.5” one for stability (whatever you can fit from the remainder of the board.
To cut perfect circles, I drilled a 3/8” pilot hole in the center of the circle to use as a pivot. I installed a pin on my router’s fence and ran it around in a circle with a ¼” straight bit. If you don’t want to attempt this, a compass and a bandsaw will work as well. Keep your scrap on hand, we’ll use it later.
Once you have two circles, put a short 3/8” dowel through the pilot hole for alignment and glue the discs together in a stack. Let it dry overnight and mount it to the largest faceplate that will fit. Put it on the lathe and trim the edges with a scraper if needed so it runs smoothly.
Photographs:
Circles marked out on plywood
Cutting circles with pin jig on router
Glue up and faceplate mounting
Step 2: The Base
I had originally built a 12” version to fit the discs I had on hand and used a wood box for the tabletop. It wasn’t very accurate and would occasionally get pushed into the disc. So, time for a better one. This should be sufficient for a 90” surface. If you want to make one adjustable, let me know your results.
Using plywood or another strong, stable board (I had some spare maple on hand), cut a length to clear the width of the disc. Mine ended up being 17x7”. Mark the center of the board and the location of the lathe bed rails.
With a straight bit and edge guide on the router or a dado blade, mill a ¼” deep channel big enough to fit the rails. This will keep the base stable. With another piece from the same board, do the same for the bottom to make a matching mounting plate.
To attach the two plates together, cut a small notch in the side of each to accept a bar clamp. This comes down to what you have on hand. I used a large Quick-Grip clamp which required a 1/4x1.25” channel. Once assembled, it should put pressure right down the center of the board.
Next we need a way to raise the table surface to the center of the disc. With the lower plate in place, I measured up and saw I’d need about 7” of space to reach the center. Losing 1” for a plywood top, I cut two more maple blocks at 6” long and attached them to the sides in shallow rabbets.
Photographs:
Cutting dados for the bed
Notches marked to fit a bar clamp
Sides and rabbets for the top supports
Step 3: Design Changes...
Generally, you want to have a clear picture in mind of your project before you get started. Okay, maybe not generally; this is pretty critical. I was still mulling over how to stabilize the assembly after I glued up the two sides.
I decided to add a notch to each side and drop a length of 1x2.75” maple into the slot to keep everything nice and level. Problem: I now have no clearance for a router or mallet.
Instead of going another route, I marked the edges of the stopped dados and cut as much as I could with a hand saw. From there, I carefully pared away the rest with a ¾” bench chisel. Chopping through the maple at an angle wasn’t pleasant but it came out okay in the end. I dropped the brace in place and screwed it in from the outside. Everything was still square.
At this point, you'll probably need to take a few minutes and resharpen your chisel.
Photographs:
That poor chisel...
Roughed-out notch
Step 4: The Tabletop
Comparable sanders seem to use a top that’s around 17x10” so that’s what we’ll go with. I cut mine at 12x17 to have a little extra room but you won’t want to use the back to support too much weight.
To have functionality that matches a commercial version, use a router or table saw to mill a dado down the length of the table about 4” from the sanding surface. Size it to fit your favorite miter gauge that you already have on hand. I got close with the table saw and then finished off the depth with a rabbet plane.
Test-fit all the parts on the lathe and attach the top so the track is parallel to the disc surface and even with the inside edge of the supports.
At this point, all you need to do is add your sanding disc and you should have a functional sander. Depending on how you’re feeling, you could probably stop here. But…
Photographs:
Test-fitting miter gauge
Tabletop assembled and fit to lathe
Step 5: Dust Collection/Finishing Touches
A disc sander with a sub-100 grit disc can pump out a mess real quick. We should probably do something about that.
We’ll start by filling the space beneath the table. On the side closest to the disc, mill a tiny (1/4x1/4")rabbet to accept a plywood filler. Keep it shallow to avoid hitting your screws and use a chisel to clean out the corners. Cut the board to match and glue it in place.
Go back to your scrap plywood that should have an arc to match the disc. Place your new sander's base on your lathe and set the plywood along the edge of the disc with minimal clearance. Trace the edge with a pencil and cut it to fit. I left the ear on the corner even with the tabletop so I could ride over it if needed later.
Make these shrouds for the front and back. Glue and tack them in place. Add a few coats of polyurethane to seal everything up and add some wax to make the top slick.
Once everything is dry, drill or Dremel a hole in the lower rear of the 1/4" plywood and mount a shroud for your shop vac/dust collector. With the support in the way, mine was a hair too small for a 4" so I opted for a 2 1/2" model. Screw it in place and grind off any points that poke through the plywood. Upon testing I found this was enough to collect nearly all of the dust it was able to create (using a Shop-Vac with a Dust Deputy cyclone).
Last but not least, check to make sure everything is square. I checked the table front-to-back as well as the miter gauge and everything looks to be fairly straight. If you have issues, you can either add shims under the table or work the dadoes with a rabbet plane for a closer fit. Once you're satisfied, attach a disc and have at it!
Photographs:
Building the plywood filler
Cleaning the leftover plywood (Yes that's a homemade stand for a Porter Cable 121. Maybe that'll be the next 'ible).
Shrouds installed
Dust port installed
Finished!
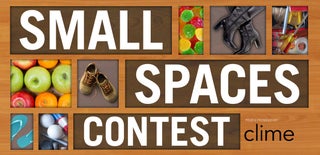
Third Prize in the
Small Spaces Contest
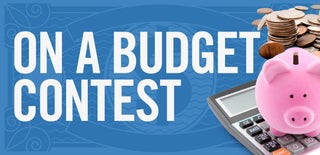
Participated in the
On a Budget Contest
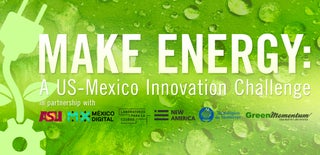
Participated in the
MAKE ENERGY: A US-Mexico Innovation Challenge