Introduction: Let's Build "Cubism Gal" Part 5
You should have a Front and Rear LH blanks, as well as a Backboard? We need to go back into Fusion 360 and write CAM procedures for the final machining. Turn on Rear 48mm blank LH and Rear LH.
Attachments
Step 1: Rear LH Setup
Rear LH is an easy piece to machine as it has a flat back,so we'll only be machining one side.
Select MANUFACTURE - SETUP - New Setup. In the popup select Stock tab. In Mode select From Solid. Use mouse pointer to select the 48mm blank. Now select Setup tab. For Model select Rear LH. For Orientation select Select Z axis/plane &...
As with all things that contain many steps you often realize later that you made an error along the way? In life you cannot undo the wrongs, but in Fusion you can? There is the history of all your steps horizontally displayed at the bottom of screen. Now way back I extruded the 8mm dia holes through Front and Rear. But these holes will be filled with dowels. We don't want to show Fusion a 3d model to machine with holes in it as it'll avoid machining those holes leaving us with dowels protruding. Sometimes that's of benefit but in the instance of machining the curved face of Rear LH we want the holes filled. You'll need to find the offending task in the history timeline, delete it and advance history marker to end again.
Similarly with Rear 48mm blank LH, we need to fill in holes. We haven't got a LH sketch, only a RH. In DESIGN, click face of body. CREATE - Create Sketch - CREATE Project - Body - OK. Select Profiles of four holes on sketch. CREATE - EXTRUDE - -48mm Operation: Join - OK. Back to MANUFACTURE. Under Rear LH click 3D - Adaptive Clearing. Use 3.15mm dia flat end mill. Click Geometry tab. Tick Rest Machining. Click Passes tab, click Stock to Leave 0.5mm. Maximum Roughing Stepdown 5mm - OK. Fusion will generate toolpaths. Now go ACTIONS - Simulate. Have Stock, Toolpath and Tool ticked. Check that it's machining what you want?
This is where it get's tricky? Remember when creating the blanks we had a centre point on the rectangle of mdf to reference? Now that's disappeared! Fortunately we will secure the 48mm blank to the 12mm Backboard LH using the dowels. Now the dowels come into play as XYZ reference. We'll use the bottom LH dowel centre as our reference. We need to create that point on the face of the 48mm blank.
Select DESIGN - CREATE - Create Sketch and select face of blank.Use mouse pointer to select perimeter of bottom LH 8mm dia hole. Select CREATE - Point and draw point in centre of that hole. Click FINISH SKETCH. Go back to MANUFACTURE.
Select MANUFACTURE - SETUP - New Setup. In the popup select Stock tab. In Mode select From Solid. Use mouse pointer to select the 48mm blank . Now select Setup tab. For Model select Rear LH. For Orientation select Select Z axis/plane &... Select Origin - Selected Point and click that sketch point you just added. Only thing now is axis arrows are wrong. Select Flip X Axis - OK.
Note you might have to switch on the last sketch you did to see that centre point, as for some reason Fusion switches off Sketches when moving from DESIGN to MANUFACTURE? You just go to the tree and open up Cubism Girl Solo (or whatever you named your file) and keep expanding the tree branches until you see Sketches. Our Setup is now complete. Rename the Setup Rear LH.
Attachments
Step 2: Rear LH Machining
Rear LH is an easy piece to machine as it has a flat back, so we'll only be machining one side.
Your backboard is clamped and Rear LH dowels glued to the backboard with washers in between. This leaves enough room to slide a hacksaw blade through later to release the body. Install your pointer in the collet and zero X & Y axis on the centre of the bottom LH dowel. Lift up Z axis, change pointer for 3.15mm flat end mill. Set touch pad under the end mill and lower the tool to touch it. Your'e set to go. tick off your checklist and hit the Start Cycle button. Once completed it will have 0.5mm cusps that can be sanded out easily. Not worth worrying about a smoothing toolpath.
Cut your Rear LH free using a hacksaw. If available use a spindle or rotary sander to tidy faces up.
Step 3: Front LH Back Machining
We now turn our attention to Front LH. You’ve got your 72mm thick blank ready? As before we need to do something with those four holes? Front LH needs to be machined on both sides. We’ll machine the backside first and then flip it, but when we flip it we need dowels protruding from the backside to glue down to the backboard to hold the piece secure whilst machining the front. At the same time we don’t want Fusion to see holes in the front or they’ll be avoided.
Turn Front 72mm blank LH on and Front LH off. Select front face CREATE - Create Sketch – CREATE – Project/Include – Project – Select Body symbol in popup – select outline of body – OK. Select 4 hole profiles, right click Extrude - Direction - Two Sides – Side 1 Distance -72mm – Side 2 – Distance -14mm - Operation – Join – OK.
Turn on Front LH, We need to turn bodies to face the backside. This is how the 72mm Front LH blank has to look sitting on the CNC table, it’ll match the drilling of 12mm Backboard LH. We need to create an XYZ reference point on the face of 72mm Front LH and the centre of the bottom LH dowel. In DESIGN select that face CREATE - Create Sketch – CREATE – Project/Include – Project – Select Body symbol in popup – select outline of body – OK. CREATE – Point and select it’s location. Finish Sketch.
Select MANUFACTURE – SETUP – New Setup. Select Stock tab of popup. Mode – From solid. Select Front 72mm blank LH. Select Setup tab For Model select Front LH and the four dowel bodies. Orientation – Select Z axis/plane – Z Axis select an edge – Flip X Axis – OK. Rename new Setup Front LH Rear face.
Select 3D – Adaptive Clearing.Tool tab = 12mm dia flat end mill (Use whatever you’ve got). Select Geometry tab. Unselect everything. Passes tab select Maximum Roughing Stepdown = 5mm.Stock to Leave = 5mm – OK . The toolpaths generated should avoid the dowels? ACTIONS – Simulate. Turn Stock on, Toolpath off. Watch and be sure it’s what is required?
Now we need to smooth this milling. Select 3D – Scallop. Change tool to 10mm Ballnose. On Geometry tick Rest Machining. On Passes tab select 1mm Stepover and Inside Out – OK. Right click Front LH Rear face in Setup. Click Simulate. If all’s good Post Process the Adaptive and Scallop.
Step 4: Front LH Front Machining
Now that the back face is done we can turn our attention to the good bit, milling Cubby’s face. At the moment her face has got 4 holes in it. We need to find where on the timeline that occurred and delete it? After doing that turn the second last sketch on where you placed a point on bottom LH dowel centre face side up, as well as Front LH and Front 72mm blank LH. Select MANUFACTURE – SETUP – New Setup. Select Stock tab of popup. Mode – From solid. Select Front 72mm blank LH. Select Setup tab. For Model select Front LH . Orientation – Select Z axis/plane – Z Axis select an edge – Flip Z axis - Flip X Axis – OK. Rename new Setup Front LH Front face.
Select 3D – Adaptive Clearing.Tool tab = 12mm dia flat end mill (Use whatever you’ve got) Select Geometry tab. Unselect everything. Passes tab select Maximum Roughing Stepdown = 5mm. Stock to Leave = 5mm – OK . The toolpaths generated should avoid the dowels? ACTIONS – Simulate. Turn Stock on, Toolpath off. Watch and be sure it’s what is required? Now we need to smooth this milling. Select 3D – Scallop. Change tool to 4mm Ballnose. On Geometry tab tick Rest Machining – Adjustment = Use as computed. On Passes tab select 1mm Stepover and Inside Out – OK. Right click Front LH Rear face in Setup. Click Simulate. If all’s good Post Process the Adaptive and Scallop.
Step 5: An Operatic Tragedy
Many a good Opera ends in tragedy and I'm sorry to say, so did "Cubism Gal" Part 5?
Once accustomed to CNC machining you soon learn that, "What could go wrong, will go wrong!". About 15 minutes out from completion using the 4mm dia ball nose, the Z axis let go and plunged into the face of the work, then proceeded on a path of destruction.
This can happen for a number of reasons and could result in an unwanted dive into the table as the software thinks its 25mm clear for example and then goes for a -5mm pass and dives 30mm into the material. The main cause is not enough torque in the z axis stepper to overcome the friction of motion. Reasons for this could be:
Dust, dirt build up on the z axis rails or ballscrews
Lack of lubrication on z axis ballscrews
Rapid travel of z axis too fast (combined with point 1 & 2)
Plunge rate too high on toolpath
Blunt bit not effectively cutting during plunge motion.
The z axis spindle alone weighs 7.5kg and its possible that when retracting from the material which is a rapid travel motion it stalled and lost position.
So there you have it, not a good ending. I was so deflated, and can't bring myself to go back and start again!
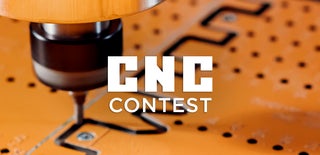
Participated in the
CNC Contest