Introduction: Make a Basic Loom With PVC Pipe
This tutorial goes over how to make a simple loom for weaving out of the affordable and easy-to-find material, PVC!
I wanted to build a loom because I had seen a lot of super cute weaving projects in home-design blogs lately and always thought 'I could make that!' - When Instructables launched the Weaving Challenge, I finally was motivated to get this Instructable up (even if I can't win :D)!
For some further context about this project, I had no previous weaving experience and learned a lot as I went. I try my best to include weaving vocabulary definitions as I go, but by all means, drop me a comment if anything needs further clarification.
Happy reading, I be-weave that you can make your own loom too!
Step 1: Tools and Materials
Here are all the tools and materials I use in this build. I like using PVC a lot because they are a little bit like giant structural Tinker Toys. A lot of this stuff I had lying around as scraps from old Instructables projects, specifically my PVC Class. If you want to get started learning tips and tricks about how to work with PVC, this FREE CLASS is full of helpful tips. :D The links below are affiliate links, all proceeds from this go straight back into tools and materials for my next Instructable - thanks for your support and understanding. Also, all of the PVC is SUPER CHEAP at your local hardware store, I definitely recommend shopping there first before ordering anything online.
Tools
- PVC cutting tool
- Center punch tool
- Drill
- Philips driver for the drill
- 2x Speed clamps
- Deadblow hammer
- Scissors for yarn and string
Consumables
- 4x 24" 3/4" schedule 40 PVC pipe
- 2x 20" 3/4" schedule 40 PVC pipe
- 2x 6" 3/4" schedule 40 PVC pipe
- 2x 3/4" 90-degree joints
- 2x 3/4" 45-degree joints
- 2x 3/4" 3-way elbow joints
- 2x 3/4" end caps
- 100x #6 self-tapping screws - not sheet metal screws, the screw heads are too large to sit next to one another :P
- String and yarn
- Cardboard scraps
Helpful but not necessary
- Notebook for doing math (I love my little Instructables pocket notebook :D)
- Bone folder (you'll see how I use this in step 10)
- Rubber feet (to stabilize the loom if it skids while you're using it)
- I don't think any of my projects are complete with blue masking tape, it really is helpful for making impermanent marks on projects :P
- Philips head screwdriver
Note
If you end up buying 3/4" PVC from your local hardware store, you'll need 2x 10' lengths, or 7x 2' lengths to complete the project.
Step 2: Marking Where the Pegs Will Go
I applied masking tape to the PVC pipe and then used measuring tape and permanent pen to mark out 1/2" distances starting and stopping 1" from each end so that the joint can still slide all the way on to the pipe later.
Drawing a straight line on a cylindrical surface is a pain, so....tape to the rescue! I've learned from previous dealings with PVC that the easiest way to make markings along the curved surface of the pipe is best with a guide adhered to the surface, versus holding a wiggly tape measure in place. :P
Step 3: Punching and Drilling in Pegs
I used a center punch tool to make little dents into the PVC along each of my 1/2" marks. If you've never used a center punch tool, you're in for a treat. It's fun, loud, and effective. You can set the plunge depth of the tool by tightening the spring on the top of the punch.
These little divots would act as indexes for the self-tapping screws to go into the soft PVC plastic. The magic in using self-tapping screws is that you don't have to pre-drill. (hands up in the air emoji here) When you're making ~100 holes, doing double the effort by pre-drilling is a drag, so this definitely reduces time.
Before I drilled into the PVC, I clamped it to my workbench with a speed clamp, I later realized it was a better idea to use two speed clamps to hold the pipe at each end.
Step 4: Level Out the Pegs
The pegs/screws were protruding from the pipe at different heights, and I wanted to make sure that none would be at risk for being pulled out nor were they so tight that they couldn't fit twine behind the head of the screw.
I got down at eye level with the pegs and made quick work of this task with a hand screwdriver, but if your arm isn't tired from holding the drill, you could use that tool too :D
Step 5: Finishing Assembly
I laid out the parts diagram in the materials step more closely, but the loom really did come together in seconds after the pegs were placed.
The elbow joints go on the bottom of the square, and the 3-way joints go on the top of the square with the peg-pieces laying laterally across the loom.
Once the square is assembled, the 6-inch piece goes in the back of the 3-way joints and connects to the 45-degree joints, remaining struts, and end caps.
Step 6: Making Adjustments
I used a dead-blow hammer to make sure the joints were REALLY secure. Along both peg rows, I went through with a hammer to level out the pegs a little bit more so the string wouldn't slip around behind them and oriented the top-row pegs pointing at the ceiling.
Step 7: Starting the Warp
I started my warp by creating a slip knot in the string and tightened it to a peg that was 12 pegs in from the edge.
I used synthetic string for my warp, which in hindsight was a mistake, I should have used some kind of natural, more forgiving fiber - cotton twine is likely ideal.
Step 8: Set the Warp
Make sure that your warp is not too tight. I learned this the hard way. The first time around, I positioned the pegs facing me and the pipe spun out of the joints as I set the warp. The second time around, I reconstructed the loom with the pegs pointing up towards the ceiling, and when I reset the warp, it seemed to be flexing less and more rigid.
I still think I probably set the warp too tight. From my understanding of weaving, the warp actually tightens slightly as you weave the weft in between the columns. Since my warp was over-tightened, my completed piece ended up buckling a little bit in the middle and being slightly trapezoidal.
Step 9: Making a Shuttle
Shuttles are the things that carry the yarn through the warp to create the weft. They are usually narrow, flat, long spools of yarn that can easily be inserted and pulled between the fibers. It is way easier to thread a flat object between the fiber than a whole spool of yarn, I made one out of cardboard in 2 seconds :P
Step 10: Start to Weave!
I'm just starting out, so I didn't try any fancy stitches or patterns, I just went back and forth between the warp slowly laying down layer after layer of weft. Getting the tension right was a bit tricky but easier once I got going.
I would intermittently use the straight edge of my bone folder to straighten the layers of weft, squishing it down with my fingers.
Step 11: Keep Going
Ok, I did NOT REALIZE that weaving is such a timely skill! Albeit it was very meditative, this part took about 4-5 dedicated evenings to complete. For (time)scale, I listened to 8 episodes of Reply All and 99% Invisible while working on this piece.
Every time I started or ended with a different yarn, I just used a single knot to adhere it to a strand of the warp.
Step 12: Taking the Piece Off the Loom
Removing the piece from the loom was super easy, all I did was twist the top PVC pipe so that the screw heads of the pegs were facing the table top and the loops slipped off the loom.
Step 13: Knotting the Edges
I know some folks like to add fringes or pom-poms to their woven pieces, but for my first try, I just went with the simplest binding method I could think of, regular knots.
I took two strands of the warp at a time and wound it around my finger to create a tight knot close to the weft.
Step 14: Gluing Down Loose String
I had a couple fly away loose ends that I wanted to hide in the piece from the tails of the weft that were left hanging off the edges. Using a yarn needle, I wove those in a couple of colums in, then glued down the tails. I used Fabri-tac because I knew it had a short open time and super quick dry time, although I think it takes 24 hours to cure completely.
Once the tails were completely dry to the touch, I snipped them close to the piece.
If you want to learn more tips and tricks for working with glue, be sure to check out my FREE Glue Class!
Step 15: Learnings
I mention this above but, I wish I had not tensioned the warp so tightly, the piece ended up bowing in the middle a bit because of the sides getting tighter as I worked my way up the loom. Another note about the warp, I used synthetic string because it's what I had, but in hindsight, I wish I would have used some heavy cotton string instead, it would have more give and maybe solved some of my wacky tension issues.
All the images of actual weaving I include in this Instructable are basically me playing around, 'sketching', and learning about the nuances of a home-made loom. I hope to post another Instructable with a finished piece and bound off edges, albeit it will likely be much narrower because, holy frijole, putting weft between a lot of warp takes a long time! Once that project is up, I'll link to it from here :D
Thanks for following along, I hope this inspires you to try making a loom and don't forget to check out the Weaving Challenge!
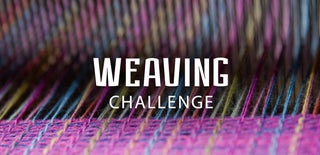
Participated in the
Weaving Challenge