Introduction: Mali Weave Atabaque
Percussion is my thing, especially Drums. I made this Atabaque, experimenting with a few different methods in its construction, and it turns out to be the stand out, with the best sound and volume, ease of tuning and even a shorter creation time with no complications. The extra rope from the tightening process (diamond pulling) can even be chained crochet style to create a shoulder and waist strap for playing off a stand.
I am quite proud. I haven't used it in a show yet like the large atabaque I made, but it is coming up soon.
These photos are In construction order.
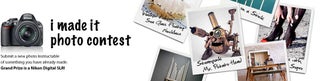
Participated in the
I Made It Photo Contest