Introduction: Mokume Gane Silver & Copper Heart Pendant
This Instructable will explain how i made a silver and copper Mokume Gane billet and shaped it into a pendant. It is not an easy project, but i did my best to keep it as simple and affordable as possible, should anyone get inspired to try it out.
Feel like stepping up your jewelry game? Do you already know how to solder precious metals and shaping jewelry, but feel like you are ready for the next step? Mokume Gane might be the answer! Mokume Gane (wood grain metal) is a very old Japanese way of creating intricate seemingly impossible patterns in metals. It is similar to making damascus steel, and the process is basically to layer up different metals, bond them together either by soldering or by diffusion bonding (very difficult) into what's called a billet, and then shaping and cutting said billet to reveal the patterns. I highly recommend a Google image search, it is absolutely amazing what the masters of the art can create.
I am by no means a master at this. I am not even a professional jeweler, but i managed to pull it off so it is not impossible, just a bit difficult. If you've never worked with silver or jewelry in this sense before, I'd recommend at least learning how to solder first, it will give great insight in the processes I will be using. For tutorials on soldering, I suggest MrBalleng here on instructables, or Mr. Soham Harrison on Youtube, both have excellent tutorials that helped me a lot.
Enough talk, lets get started!
Step 1: Materials and Tools
Since we're making a silver and copper pendant, we need silver and copper. I know those are expensive, but to lift your projects up a notch, sometimes small investments must be made. The amount of silver i used was not that bad really, it cost me about 40$.
Here's the full list
Materials
- Silver sheet, dimensions depend on how large you want your piece. I had 5 silver layers 30x12mm. Thickness should be less than 1mm.
- Copper sheet, again the size depends on the piece. Just make sure they are the same size as the silver, and that you have an extra copper layer.
- Silver solder, hard and soft
- Silver wire 1mm
- Flux for soldering
Tools
- Furnace (Nothing fancy, I'll elaborate shortly)
- Blowtorches (A large one for the furnace, and pencil torch for soldering)
- Steel (preferably stainless) plates, at least 4mm thick, and large enough to cover the layers plus at least 15mm on either end
- Soldering station
- Anvil or heavy piece of steel that can be used as an anvil and a polished hammer
- Citric acid (Can be found as drain cleaner or food grade powder)
(Update 14-02-16 - I found out that warm dissolved pool cleaner (sodium bisulfate) can be used instead of citric acid)
- A selection of metal files, both large and needle files
- 400, 600 and 1200 grit sandpaper
- Buffering wheel
- Dremel with a 1mm drill, and optional diamond core drills
- Pliers and a vice
- Bit of scrap plywood
Most of this I already had lying around, and some things i improvised.
The size of the silver and copper sheets are not very important, but without proper equipment i wouldn't recommend larger than 40x20ish mm. I am showing one example of how to use the Mokume Gane billet, but there are tons of ways to use it. You can make just about any kind of jewelry if you have the skills. The most popular is flattened Guri Bori (I'll explain towards the end) and rings.
Step 2: The Furnace
Don't be scared off because you need a furnace, you can make one suitable for this project costing next to nothing.
I am not going to spend too much time explaining how to make the furnace, instead I'll give credit to NighthawkInLight who made an excellent video showing how. I made it exactly as he showed, and it worked like a charm.
https://www.instructables.com/id/How-to-Make-a-Sou...
Basically you line the walls of a soup can with plaster of paris mixed 50/50 with sand, and make a hole for the blowtorch. To get it hot enough though, you need to make a "door", so you can contain the heat. Simply put some of the mix onto the lid that comes off the can, and use it to close the furnace. Make sure the can is big enough to fit the billet (with pressure plates) in with a little room to spare.
You also need to make a small "shelf" for the billet to sit on, to make sure it heats as evenly as possible. I just rolled up some wiremesh, and put it at the bottom of the furnace.
Step 3: Silver and Copper Sheets
Unfortunately i didn't have enough actual silver sheet, but i had some 4mm wide strips, that i soldered into sheets.
Of course it would be easier with normal sheets, but you need to solder no matter what.
To make the billet, you squish the layered stack between two pressure plates, and apply heat. If there's solder present, it will flow before the silver melts and thus bond the copper and silver together. To make sure there's enough solder, it's a good idea to presolder the silver sheets. To do this you clean the silver sheet, flux it and place some bits of solder on the surface. Then you heat up the silver until the solder flows and becomes somewhat level. Make sure to use hard solder! It doesn't have to be that pretty or even cover the entire surface, it just needs to be fairly flat. You don't need to use a whole lot, just cover about 25% of the surface.
To make my strips into sheets I cut the strips to length and soldered them side by side. While i was at it, i used the opportunity to pull some of the solder onto the surface. Make sure you presolder both sides of the silver.
The copper sheets doesn't need any particular preparation, besides a thorough cleaning explained in the next step.
Step 4: Cleaning the Metals
Cleaning the metals is very important, and you need to do this immediately before firing the billet. They must be as clean as possible when the go in the furnace, preferably not even a fingerprint on them.
The silver will be quite ugly after soldering. The excess flux can be dissolved in a solution of lukewarm citric acid (which is a substitute for a professional pickling solution)(Update 14-02-16 - you can use dissolved and heated pool cleaner (sodium bisulfate) instead of citric acid). If it doesn't get it all you can scrub it with a coarse sponge soaked in the citric acid.
Depending on how your copper sheets look, i recommend lightly sanding them to clean the surface from oxides. Don't leave too deep scratches, use 400-600 grit sandpaper.
Before placing them in the pressure plates, wash them with soap and try to only touch the edges after the wash.
Step 5: Pressure Plates
You need two pressure plates to sandwich the billet. I used some 4mm normal steel, but it would have been better with 5-8mm stainless steel.
Cut the steel into two pieces at least 15mm longer than the sheets. The reason for the extra length is that you need to drill holes for bolts that provides the pressure on the billet. I only had two bolts, but I'd recommend having four. I used M6 grade 8.8 bolts.
Make sure to clean the surface well, I sanded mine on a disc sander until they were shiny all over. You don't need to polish them just clean them.
To drill the holes, i suggest layering the plates, and drilling both at the same time. This makes sure the holes are aligned.
Step 6: Placing the Layers Between the Pressure Plates
When everything is ready and the sheets are freshly washed, it's time to place them in the pressure plates.
The reason you wash the sheets with soap is that oil will hinder adhesion between the layers. This can be used to our advantage though, since we don't want the billet to stick to the steel. Place a drop of sewing machine oil on both steel plates and run a finger over it to spread it evenly.
Place the bolts in the lower plate pointing upwards (I had a washer under the bolt), and start layering up the billet. I started and ended with a sacrificial layer of copper, that i would file away afterwards, because i didn't know how the solder would act in contact with the oil, if it could affect the adhesion to the layer opposite side. I had 6 layers of copper, and 5 layers of silver.
When the stack is in place, make sure the layers are aligned as straight as possible before putting the top plate on. Carefully screw on some nuts (i used some washers here as well), making sure not to shift the layers. Tighten them enough that the stack stays in place, and them place the whole thing in a vice. Tighten it around the pressure plates and re-tighten the bolts. You don't need to kill it (when using the solder method, if you try diffusion bonding use as much pressure as humanly possible) but make it fairly tight.
Finally ready for the oven!
Step 7: Firing the Billet
Time to turn up the heat. Put the blowtorch in the furnace, and light it up. Put the door in front of the opening and wait a few minutes for it to heat up before placing the billet in there. It's going to take some time to heat all that metal up, so place the door in front and check in on it every few minutes. We're aiming to reach a temperature hot enough that the solder flows, but not hot enough that the silver melts. When you can see the steel start to glow a dull red I recommend taking the door off and replacing it with another blowtorch. This makes it easier to see when the solder flows. The difference in temperature between the solder flowing to the silver melting is about 50°C, so you need to be careful when you get close.
At some point it will look like the billet is "sweating". This means the solder is flowing and the layers are bonding. When you see the sweat you can turn off the torches and quench the whole thing in water. With a little luck and proper preparation your billet is done by now!
Step 8: Cleaning the Billet
When everything is cooled down, open the pressure plates and remove the billet. It will look very ugly and burned, but a lot of that can be cleaned away in the citric acid. The edges will be ugly, so file those down to reveal the layers. Congratulations, you've made Mokume Gane!
Now the real fun begins. From here there's a plethora of options you can do with the billet. Something fun to do is to hammer it into a rod, twist it and split it down the middle. This will make really interesting patterns and can be used to make rings for example. Another option is to roll it flat into a sheet.
I decided to do something different, and kept the layers intact. This was so that i could make a kind of topographic map of a heart (I have a friend who is a topographical engineer, this is a gift for her for valentines day). The next step is about how I shaped my billet, but when you have a billet sky's the limit for what to do with it.
Step 9: Shaping the Heart Pendant, Forging
I had my mind set on a heart shaped pendant from the beginning, and here's how i made it.
First i cut a square piece of the billet with a Dremel cutting tool. This left a big chunk of the billet i will be using for another piece later. The billet was too thick for a pendant so i had to reduce the thickness to about half. I did this by whacking it with a hammer on a steel block. Plain and simple. The hammer was polished on a disc sander so it would leave as few marks as possible on the surface. When you reach about 30% reduction (no matter how you shape the billet, if you draw it, roll it, hammer it ect.) it needs to be annealed to soften it again. When you are hammering it you work harden it, so to soften it up you need to heat it up to a dull red and quench it in water. Don't superheat it, it only needs a slight red glow.
When I reached the thickness i wanted, I used my computer to draw a heart just small enough to fit on the now flat square. Then i placed a piece of paper on the screen and (very!) lightly traced the outline of the heart. Be careful not to damage your screen!
Cut the heart out and glue it to the billet. I used a thin film of wood glue. Make sure there's metal all the way around the outline, you don't want to fall short after you start shaping.
Step 10: Shaping the Billet, Subtractive Shaping
Fair disclaimer, when you use power tools on such small stuff, you need to work very carefully, because in a split second you can ruin the whole thing.
I rough shaped the corners on a disc sander, semi fine shaped it with a dremel, and fine tuned the outline with files. I started with the outline, before rounding over the edges. As you can see in the photos, I am holding it in an improvised ring clamp. This is simply two pieces of plywood with aligned holes and a bolt through it. This is your best friend when filing, because it makes handling the piece a hundred times easier, and also protects your fingers when the piece starts heating up.
When the outline is done, it's a good idea to drill the hole for the jump ring. Punch a mark in the center, and drill down far enough that the hole goes through the part that will be the heart. This is much easier to do now when the surface is flat, and not later when it's curved.
When the hole is drilled, start rounding it over to really reveal the pattern. I filed off the top and bottom sacrificial copper layers, but to my delight I saw that the hammering had dented the layers and some of the copper remained in the middle. This is the wonderful thing about Mokume Gane, you can never really predict the pattern, it will always be different.
When everything is filed and the shape is good, start sanding the surface. Go through 400, 600 and 1200 grit and finally the buffering wheel.
After a thorough cleaning you can solder a jump ring on. Place the ring in the hole and solder it to the piece, this time using (very important!) soft solder. You use soft solder because the layers are held together with hard solder, so you must stay below the melting point of the hard solder. This is definitely a difficult step! After soldering, the piece is ugly again and needs a dip in the citric acid (or professional pickle) and a good cleaning. Maybe you also need to buff it up again.
Step 11: DONE!
Your piece of Mokume Gane jewelery is done! Don't worry if the metals don't have much contrast after polishing, after a few days the copper will have oxidized and the colors will pop out. You can also experiment with different patinas, and if you want a professional one, look up Baldwins Patina from RioGrande.
Next step from here is to advance to the even more difficult diffusion bonding, but that is still beyond me. Mokume Gane can also be done with many other metals like brass, bronze, gold, platinum, palladium, nickel silver, even titanium. If it has caught your interest, look up James Binion, Chriss Ploff and Steve Midget. The latter has published a book about the craft which goes into way more detail than me.
Another way you can use the billet, is to drill into it, file patterns, make holes and waves with burrs in the surface, and then hammer it flat again. This will make very interesting patterns as well. The remainder of my billet will be patterned like this.
Final note on this project. Since silver is more noble in the galvanic series than copper, galvanic corrosion can occur between these metals. If the jewelery is often wet or exposed to sweat the copper will eventually start to show signs of corrosion. The rate of corrosion is highly dependent of the circumstances, but a pendant like this will easily make it decades before corrosion sets in. A ring won't last as long, unless you use noble metals in the same galvanic state. Copper may also color the skin a little, but a pendant like this will be moving around so often it will be minimal.
Happy Mokume Ganeing!
Step 12: Bonus Step
I only used about half of my billet for the heart, so here's what i did with the rest.
With different drills, files and burrs i made some contour in the surface of the billet. This revealed the layers, just like it did with the heart. Then with a hammer, i spent hours working it down to a rod, twisted it and hammered it flat. After a bit of filing, i had a bar of patterned Mokume Gane. I think I'll make this into a ring later.
I have entered this Instructable in the Jewelery contest, if you think i deserve a vote i would greatly appreciate it.
Feel free to ask me anything, i may not have all the answer right away but I will be happy to help any way i can.
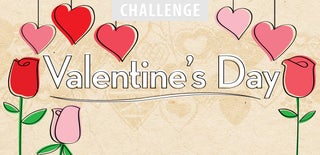
Runner Up in the
Valentine's Day Challenge 2016
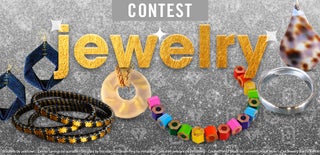
Second Prize in the
Jewelry Contest
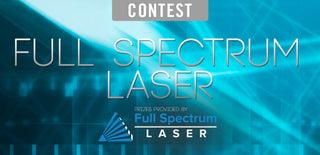
Participated in the
Full Spectrum Laser Contest 2016