Introduction: OpenLH: Open Liquid-Handling System for Creative Experimentation With Biology
We are proud to be presenting this work at the International Conference on Tangible, Embedded and Embodied Interaction (TEI 2019). Tempe, Arizona, USA | March 17-20.
All assembly files and guides are available here.
Latest code version is available on GitHub
Building/built one? Write us at info@milab.idc.ac.il! We would love to know, support, and even feature your work on our website.
Why did we build this?
Liquid handling robots are robots that can move liquids with high accuracy allowing to conduct high throughput experiments such as large scale screenings, bioprinting and execution of different protocols in molecular microbiology without a human hand, most liquid handling platforms are limited to standard protocols.
The OpenLH is based on an open source robotic arm (uArm Swift Pro) and allows creative exploration. With the decrease in cost of accurate robotic arms we wanted to create a liquid handling robot that will be easy to assemble, made by available components, will be as accurate as gold standard and will cost just around 1000$. In addition the OpenLH is extendable, meaning more features can be added such as a camera for image analysis and real time decision making or setting the arm on a linear actuator for a wider range. In order to control the arm we made a simple blockly interface and a picture to print interface block for bioprinting images.
We wanted to build a tool that would be used by students, bioartists, biohackers and community biology labs around the world.
We hope more innovation can emerge using the OpenLH in low resource settings.
Step 1: Materials
Step 2: The OpenLH Has 3 Main Parts
1. The pipetting end effector.
2. A uArm Swift Pro base
3. A linear actuator operated syringe pump.
* uArm Swift Pro can also be used as a laser engraver, 3d Printer, and more as seen here
Step 3: How to Build the End Effector
1. Dismantle an old pipette and keep just the main shaft.
We used a CAPP ecopipette as it has an aluminum shaft and "O rings" making it air tight. (A-C)
Other pipettes could probably work.
2. 3D Print the parts using PLA and assemble (1-6)
Step 4: Making a Syringe Pump
1. Use a linear actuator Open Builds.
2. Connect 3d printed PLA adapters.
3. Insert a 1 ml syringe .
4. connect the syringe to the end effector with a flexible tube.
Step 5: Setting Up!
Secure all parts to a designated area of work
You can connect the uArm directly to your bench or in your biological hood.
Install python and blockly interfaces:
Python interface #### How to use the python interface? 0. Make sure to do `pip install -r requierments.txt` before starting 1. You can use the library inside pyuf, is our modification for the version 1.0 of the uArm library. 2. For examples you can see some scripts inside the **scripts** folder. #### How to use the printing example? 1. Take a **.png** of the example you would like to print. 2. Run `./convert.sh your_pic.png` and adapt respectevely the path in `test_print.py` to use `your_pic.png.coords` 3. Run `python test_print.py` with the robot connected
### Blockly interface 1. Make sure that you did `pip install -r requierments.txt` before starting. 2. Run `python app.py` this will open the web server that displays the blockly 3. In a different console run `python listener.py` which will be receiving the commands to send to the robot. 4. Now you can use the blockly from the link displayed after running `python app.py`
Step 6: Program Arm With Blockly
Serial dilutions are done by liquid handlers saving time and effort for their human operators.
Using a simple loop to move from different XYZ coordinates and handling liquids with the E variable a simple liquid handling experiment can be programmed and executed by the OpenLH.
Step 7: Print Microorganisms With Pic to Print Block
Using the bit to print block you can upload a picture and have the OpenLH print it.
Define starting point, tip location, bio-ink location and deposition point.
Step 8: Effective Liquid Handling
The OpenLH is surprisingly accurate and has an average error of 0.15 microliter.
Step 9: Some Future Thoughts
1. We hope many people use our tool and conduct experiments they couldn't do otherwise.
So If you do use our system please send your results to info@milab.idc.ac.il
2. We are adding an OpenMV camera for smart colony picking.
3. We are also exploring adding UV for cross linking of polymers.
4. We propose extending the reach with a slider as described by https://www.instructables.com/id/How-to-Combine-UA...
In addition the uArm is extendable by many other sensors that can be useful, if you have ideas let us know !
Hope you enjoyed our first instructable!
The media innovation lab (miLAB) team.
“I make mistakes growing up. I’m not perfect; I’m not a robot.”
— Justin Bieber
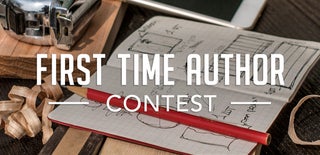
Participated in the
First Time Author