Introduction: PLYWOOD JEWELERY? You'll Be Amazed at the Unique Beauty of Common Plywood.
Everyone who has worked with plywood has spent a lot of time finding ways to hide the edges. I Found a way to showcase the inside of plywood and its hidden beauty! I've always cheered on the underdog so now's my chance to promote the major flaw of plywood.
Two words that have never been used in the same sentence are plywood and jewelery. The idea of making jewelery out of plywood is so unheard of that I needed to try it. I googled plywood jewelery and only found some shapes laser cut out of thin plywood and put on a chain for a necklace. I wanted to use the inside of plywood as the focal point. To my surprise the results far exceeded my expectations! Now whenever I see plywood I'm looking at the edges to see the hidden beauty.
After making the pieces shown, my mind is seeing many other possibilities. Share any ideas you have to use plywood for jewelery.
This instructable will be entered in 3 contests; jewelery, plywood and Valentine. Vote for this if you think merits your vote.
I would like to sell these, does anyone have any suggestions that they have used?
Thanks,
Ron
Step 1: Things Needed
1) Plywood of your choice
2) 20 gauge beading wire
3) Necklace and earings of your choice.
4) Spray polyurethane and stain of your choice.
5) Woodworkers glue, I used
Tools:
Table saw, band saw, drill, router, various clamps and sandpaper.
Tools for the jewelery part :
round nose pliers, flat pliers & wire cutters.
Step 2: Search Thru Your Plywood for a Sheet With Even and Contrasting Layers
I looked for plywood with the most layers to start with. The best I found in my shop was baltic birch and oak plywood. The baltic birch has exterior grade glue used to hold the layers together, not sure about the oak. I chose to use the baltic birch. The 1/2" thick seemed the most likely so I could make a pattern small enough for jewelery.
After some experimenting with plywood with fewer layers, it will work as long as it has minimal voids in the layers.
Plywood is graded for the external layer and not necessarily for the core qualities. A good rule to follow is the more layers or the mor expensive the better the core will be.
Step 3: Cut Into Smaller Pieces
1) Made a pile of pieces to create a few paterns to see how they looked.
2) Cut them twice as wide as the thickness. To do that used 2 pieces of the plywood between the saw blade and the fence. Cut several strips. Then cut the strips into equal length pieces 3 1/4" long. I had no reason for the length, just random. A longer length would make it easier to work with later on.
Step 4: Create a Pattern and Glue
1) I made 2 patterns, one was 4 pieces stacked on top of each other. The other is a stair step pattern.
2) Laying out the stairstep pattern, I wanted about a 4" square. When I put them together I realized it was nearly impossible to get that many pieces together, so I decided on a 2" square.
3) Arrange the pieces in the pattern and clamp them in place before applying any glue. This will make it easier to clamp after the glue is applied. Use plenty of clamps! I found I needed some 1/4" plywood slightly smaller than the sides to hold all the pieces together.
4) Assemble the pieces in the order you want them, then glue them together 1 at a time. Pay special attention to have 100% glue coverage an all surfaces. I used a foam brush to evenly distribute the glue. Take your time building the blocks
4) Cover the outside of the blocks with waxed paper to keep the glue off your clamps. Clamp all around, slowly and evenly tighten the clamps. You may need to loosen some clamps to keep the block square and the ends even.
5) Let the glue dry overnight. When you remove the clamps clean up the glue on all sides. I used a stationary belt sander.
6) Notice the pattern of some light and some dark pieces. I didn't notice that untill after the clamps were removed. All the blocks were cut from the same edge of the same sheet of plywood!
Step 5: Cut Slices Off of the Patterned Block
1) Cut off about 1/8" thick slices. This is a dangerous process since small parts make it easy to get fingers close to the cutting blade, and the density of plywood changes within each sheet so extra care is a must! If the slice catches or cracks the slice will be destroyed. I used a band saw with a custom fixture (a 2x4 with a "V" cut into it)to make it safer to cut and keep my fingers away from the blade.
2) Cut out the shape you want, I used a heart because it's almost Valentines day.
Step 6: 3D Heart
1) Start with a 3x3x3/4" block.
2) Mark cut lines on the block. Drill a 1/16" hole for mounting.
3) Cut shape on a scroll saw or band saw. Again be careful!
4) Sand to desigred shape use a rotary sanding tool like a dremell to cut down on sanding time.
Step 7: Heart Shaped Slices
Here is an easy way to make a bunch of nice looking hearts.
1) Use a 12" length of 3/4" baltic birch plywood.
2) Rround the end using a 3/8 radii router bit on a router table.
3) Cut at 45 deg as shown. Cut into 2 pieces 6" long.
4) Tape the pieces together. add glue. Be sure the glue is spread even and 100% coverage. I used a foam brush.
5) Fold and clamp. Wipe off as much of the glue squeze out before it dries. The glue will be hard to get off after it dries because the dried glue will be harder than the plywood. Let dry overnight.
6) Cut into slices about 1/8" thick. Ued a band saw. Be careful, keep fingers away from any power tools blade!
7) Round all edges with sandpaper, use progressively finer grits to 220 grit.
8) Drill a 1/16" hole to attach.
Step 8: Apply Finish
I tried several different stains to get the best look, with mixed results. Since the wood grain and density changes within plywood there was no finish that always worked better. I liked either no stain or a light stain the best. Then spray with a satin polyurethine finish. After several coats of polyurethane the surface will be rough. This is the wood fibers raising up, sand lighty with fine sandpaper 220 grit. Apply more coats of polyurathine and resand as needed.
Step 9: Turning the Finished Shapes Into Fine Jewelery
Using 20 gauge beading wire, Make a U shape and thread it through the heart. Using round nose pliers and flat pliers wind one end of the wire around the other 3 or 4 times. Straighten the long wire and form a loop using round nose pliers about 1/2" from the heart. Cut off any excess wire. Leave the loop open. Run a necklace or earing into the loop and close.
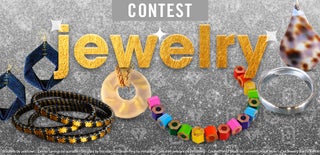
Participated in the
Jewelry Contest
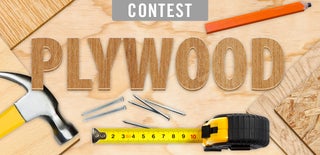
Participated in the
Plywood Contest
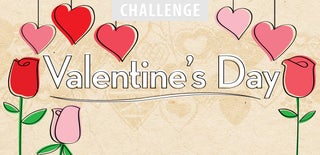
Participated in the
Valentine's Day Challenge 2016