Introduction: Reading Lamp From Used Palette Straps and LED
This is how I made an "industrial looking", variable position table lamp powered by 12V LEDs, using only basic tools and some scraps.
Step 1: Intro to Palette Belts
On my way home I pass a dump yard where I couldn't help noticing a pile of palette straps. for people not familiar with it, palette strap is the plastic belt used to hold goods together on a pallet (shown image is from internet). They feature a good strength but are flexible. I wanted make some use of this cool looking stuff and all of sudden this Idea struck in. Flexibility of the strap can be utilized in place of a flexible (Swivel) coupling and we might be able to apply some structural engineering concepts to stabilize and strengthen required areas. The resulting idea - an articulated robot arm! Well that's the first Idea hit me but as a trial I will settle down with a "variable position reading lamp". Await for the robot arm ;)
Step 2: Supplies
I managed to find some strong palette straps about 20mm*1mm. Ordinary staples were the choice of fastening. base of the lamp was made out of a piece of plank from a palette. Cutting straps could be done with a paper cutting knife. for measuring and inscribing I used appropriate tools.
Step 3: More About Fastening
While stapler works on these, please note that the strength of stationary grade staples might not be enough to penetrate through more than two layers of these straps. so in such cases I manually bent couple of heavy staples and attached with the help of pliers. To drill holes I simply used a pointed tip soldering iron. If you see success with other fasteners such as rivets etc, please share in comments.
Step 4: Design the Structure
Like I mentioned earlier the straps are very flexible. So all the places you need rigidity requires strengthening. First and foremost thing is to get the concept on paper. Then identify the places you need flexibility. My design would have a central flexible area to give adjustment to light position. So both the ends needed to be rigid. I got my inspiration by studying roof trusses and tall towers. I wanted my design to look bit industrial so it helped.
Step 5: Bending the Straps
The straps can be bent fairly easily. For accurate sharp angled bends I used a set square t scribe the guide line. Then made the line little deeper with the scriber(shown in image 1) or the paper cutter. Then placed the line along a sharp edge of the table and bent.
I suggest bending a little more than you need so when attaching the structure will take shape better.
If you want a more precise piece, I suggest drawing a 1:1 scale model on paper and bend your pieces against it. I was too lazy to do that :)
Try to use a strap without cutting. It will reduce the time and the structure will be much more stable. When designing, keep this aspect in mind.
Step 6: Position Control
I selected very simple belt adjustment like mechanism. I do not think much explanation is needed. Holes were made with a soldering iron.
Please note: for areas you need your structure to bend, make sure there is only 1 strap undergo bending. You cannot have two or more parallel straps rigidly fastened in areas needed bending. If you try to do this it will distort the structure. If you can't figure out why, leave a comment so I'll try to explain.
Step 7: Fixing the Base
I used a piece of palette wood for the base. Drilled two holes intersecting each other at right angles (one at top and one at side) so the power line to lights can be drawn through it. After sanding and finishing the base, the structure was pivoted at only one point so it is swivel upon the base. Used a 0.75 Tintack along with a washer (made from a small piece of palette strap) to get this done. Structure itself was lightweight so tintack was enough.
Step 8: Lights and Power Line
Once fixed it turns out just the way I wanted. I have noticed that rigid parts are pretty amazingly strong. If designed properly one should be able to use this concept for other applications such as structures for furniture.
I am not going to go in to details about lights and power as there are so many possibilities. In this project I settled myself with a12v LED strip came from vehicle accessories store. It came with a double sided tape which became handy. The power wire was drawn along one stem of the structure and glued it on. Used tapes to hold the wire in place until glue gets cured. Used a 12V Ac/DC adaptor to power it up and that's it. Of course you can add switches, dimmers and other gimmicks if you like. Total cost was about 800 rupees (approx 6$).
P.S. Sorry about the low quality pics. This is a simple step so I do not think it makes any harm.
Step 9: Power Up!
Simple as that! Once the glue is cured small pieces of insulating tape will be taken away. Notice how the power wire go through the base. Shown images are the two extremes of the light position. Amount of light is more than enough to read.
This Contraption however has a flaw. That is, if you notice there are no supporting members in the mid-span of the structure (purposely avoided to accommodate bending). This makes it wiggle for some time after adjusting the position (or when subjected to any other impact/force). It quickly settles but still is a flaw. There are few remedies you can try such as reducing the span, adding floating members etc, please do not forget share with the community if you try.
Took Less than 5 hours at it. Thank you for reading. Hope you'd grab a point or two for your next project.
P.S. English is not my mother tongue so please bear with me if I made any mistake in composing this.
Cheers!
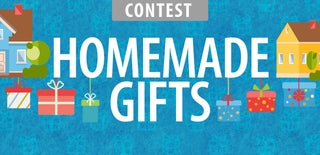
Participated in the
Homemade Gifts Contest 2016
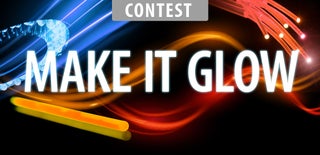
Participated in the
Make it Glow Contest 2016