Introduction: Scrap 2x4 to Diddley Bow
Awkward confession time-- I love to make things out of junk. One of my favorite phrases is "You'll never guess what I found at the dump!" As you can imagine, its a real problem sometimes. But it comes from a good place. I see value in things in which other people maybe don't see value. And thats the core of this "Before & After" creation. This is the story of how a scrap piece of gnarly 2x4 became a gnarly Diddley Bow.
(or a cigar box style one string guitar, depending on who you ask.)
Step 1: Discover an Awesome Piece of Architectural History.
So I have this old piece of 2x4. I don't know exactly where it came from, but its spectacular. Even more so than your average piece of junk lumber. Its full of holes. Its gashed. It has a weird angle cut off one end. Its been attacked with a claw hammer. Its extremely weathered. I'm sure with a little planing this board could look almost as good as new, but I wanted to make something that preserved the crusty coolness of the board.
Step 2: Contemplate...
What to do with such a magnificent piece of scrap as this??
Thankfully, I spend an inordinate amount of time looking through other people's Instructable creations, and a few weeks ago, I saw -BALES- Instructable entitled "The Diddley Bow," in which he re-creates a fascinating piece of musical history with quality and precision. Because of that instructable I had been listening to some YouTube diddly bow blues. And while quality and precision aren't my style, a diddley bow totally is. Hence my decision that this delectable arboreal masterpiece must become a Diddley Bow!
Step 3: Make a Plan-- Sort Of.
A diddley bow of the style that I want to make needs basically a neck and a box. I'm not particularly musical, so I didn't have any super-specific requirements on size or anything, but I have two absolute rules--
1. The beat up exterior of the 2x4 will be a part of the finished product.
and
2. The ONLY wood used in this project will be this single scrap of 2x4. period.
Step 4: Cut the Neck.
I set my table saw for a one inch cut, and cut down 3 feet of the board, then made a cross cut. (I should have just cut the full length of the board then chop sawed it to length, but i wasn't sure what my next step would be yet. After I decided, my next step was to cut off the rest of the 1 inch section.)
Step 5: Slice Up the Rest of the Board.
Minus the one-inch strip i had cut for the neck of the diddley bow, I could now slice all the way through the remaining height of the 2x4 with my table saw. So I set my table saw fence for somewhere between a 1/4 and 3/8-inch cut, and sliced the 2x4 into 4 usable pieces with one very thin piece remaining. To preserve the exterior sides of the board, I cut the outside edges first to ensure that my remainder piece would be from the middle and not from one of the exterior sides. My plan is to cut and glue these slices together to make the box end of the diddley bow.
So now I have a 3-foot neck piece, 4 slices of about 3/8-inch width and 2 3/4-inch height, one extra-thin slice, and the remainder of the neck piece, appx. 1 3/4 x 1 x maybe 12. And all my fingers. So far, so good.
Step 6: Trim Some Edges.
If I'm going to glue this thing together, then I have to have some decently straight edges. Both sides of interior pieces have to have straight edges, but i can leave ragged edges on the outside. So back to the table saw to take off a blade width for good joining edges. Only off one edge of the gnarly pieces though.
Step 7: A Word About Safety.
Back in high school, we had a shop teacher who cut off three of his fingers while giving a safety demonstration on the first day of class. After he got them sewed back on and was mostly back to normal, the art teacher made fun of him for years. For YEARS.
Watch out for art teachers. They can be awful.
Step 8: Make a Box!
ok, now to make these slices of woody wonder into a box...
How big of a box? I say 12 inches long because-- well, just because. And I say 4 slices wide because-- again just because.
But how to cut four pieces into exactly the same length?? If only I had recently torn apart an old shelf and made it into a winged table for my chop saw... Oh. I guess i DID :)
(man I love to make things out of junk!)
So I layed out my first slice for a 12 inch cut, clamped it to my table, lined up the next three pieces to perfection-ish, and cut! These will be my top pieces. Then I did the same thing for the bottom pieces.
Step 9: Make the Neck a Part of the Box.
I'm worried that my Diddley bow isn't going to be super-strong because of the cracked up pieces of exterior wood. But I need it to be able to withstand the tension of the string. And I hate to hide that weathered neck inside of the box part of the Diddley Bow... Solution-- Make the neck a part of the box! I can totally do that, I just have to make a joining edge along 12 inches of each side of the neck piece.
That turned out to be a bit more complicated than I thought. For the first side i just set the table saw fence to the right distance to take off a saw blades width off the edge. no problem there.
But for the other side, I couldn't do that. The fact that I had just cut off a small section of the edge on one side meant that I could not use that side a a guide against the saw fence to do the same on the other side. My solution was to place a 1x2 scrap next to the fence, then set the fence so that the 1x2 was super-close to the blade, then use the 1x2 as the guide to trim a saw blades width off the neck. Make sense?
I probably could have just set my fence that close to the blade, but that didn't seem like a great idea.
Step 10: Problem.
If I'm making the neck a part of the top of the box, then I need a piece of equal width for the bottom of the box...
Remember that extra length of neck piece that I cut off in step 4? Its exactly the same width as the neck piece. so I just need to trim the edges and then slice off the exterior edge to the same width as my other slices, and it will be fine.
Another problem. I has a cut through it already. Oh well, we can make that work.
Ok, now we have all the pieces for the top and bottom of the Diddley Bow, with an integrated neck.
Time for some glueing!!
Step 11: Glue Up the Top and Bottom.
I figured out very quickly that trying to clamp these boards and then keep them from bowing was going to be more trouble that it was worth. But it also meant that I was going to have to use some patience and glue things together one piece at a time. But at least I get to go inside and take over my kids craft table for this step, because its way too cold in the garage for glue...
First I glued the top slices to each other, then I glued them to the neck. In order to glue them to the neck, I had to first clean up the edge left from a partial table saw cut. Then, I used shims to create a platform so the slices would set flush with the top of the neck.
On the bottom, I followed basically the same steps, only I didn't need the shims because all the pieces are the same height.
Step 12: Now for Some Sides...
To finish the box, I need some sides. In order to represent the awesomeness of the original board, I'm keeping the pieces from each original side together. I left all the outside edges unfinished. so for the sideboards I will cut lengths of the corresponding side board, then trim both edges for gluing. These edges will be glued so that the cut edges won't be seen.
Then for the front side and back side, I will use internal slices.
Step 13: That Pesky Neck.
I need to notch the front side and back side slices to accommodate the neck. No problem. It just so happens that my favorite tool in the whole world is the jig saw...
BUT WAIT!!! I love the jigsaw. Deeply. Almost oddly. But I think I can get a better result here from the table saw...
So Instead I set my saw blade to the appropriate height, cut the outside edges first, then cut out the inside blade width by blade width. Repeat that for both the front side and back side.
Now back inside for more glue.
Step 14: More Glue.
I flipped the top side/neck side of the box upside down, and glued on the front side and back side, using the other side pieces as guides to line them up.
Then, I glued on the sides, making very certain that they match the exterior slices they were being glued to. The two sides of the original 2x4 were weathered very differently, so that was important to me.
Step 15: Another Problem.
Now that I've got the sides glued up, I'm starting to think about gluing on the back of the box. But I've got two problems.
1. Its more sturdy than I thought it might be, but I'm still just a little worried about structural integrity.
2. If I decide to drill some extra holes for sound, or succumb to the pressure of my guitar playing buddies and put in a pickup, I'm gonna need to get back inside this thing. But Elmer says that his glue dries stronger than wood...
Solution-- I need to add some supports and screw on the back of the box instead of glueing it.
Step 16: Back to the Left-over Pile.
I want some supports, but I'm only going to use whatever I've got left of this 2x4...
Remember that left-over from the original neck cut in step 4? At this point, its been trimmed for good edges, and had its cool exterior sliced off. But it should still work for some internal supports. I'm thinking one in each corner and one on each side of the neck.
So I cut those from that left-over piece and glued them in. I intentionally cut them a tiny bit short to help the box seal up well.
Step 17: Screw on the Back.
After the glue dried, I found some screws from an old project, pre-drilled holes through the lid and into the internal supports, and then screwed on the lid. I used my drill, but i set it on 1 or 2 so as not to crack and crush the weathered lumber slices.
Step 18: Diddley Bow Body Is Complete!!
Its a box! With an awkwardly long handle. Now it looks like I'm gonna need to put a string on it.
But before I do, appreciate the coolness of this 2x4. Notice the nail holes that are represented in each layer through the board, but all side by side in the diddley bow. Cool stuff I think. Please feel free to comment if you think I should drill some holes for sound resonance. I'm still deciding on that one.
Step 19: Hope Rises.
So I need a wire. Let it be known, this diddley bow will NOT be strung with a guitar string. The original diddley bows were basically built from junk by impoverished and oppressed people who refused to let their spirits be quelled and invented an entire genre of music in the process. I have a ton of respect for that. I did some research and discovered that the best wire for the original diddley bows was the wire that held the straw onto a store-bought broom. I don't have any of that.
Are you thinking what I'm thinking???? Sounds like its time for a trip to the dump!!!!
Step 20: Hope Fades.
So I strolled through my shed on my way to water the dog. And what do I spy half buried in dirt in the corner but this tangled up mass of wire. Now I've got wire! But I don't get to go to the dump. Darn dog.
I still need something metal to hold up the wire off the box... something like the seat clamp from a 1954 Schwinn Panther! Man, I'm really not going to get to go to the dump for this one.
Step 21: String It.
There is an old angled nail hole at the end of the neck of the diddley bow. We're totally gonna have to use that. I think thats where the tuner is supposed to go, but we'll put that on the other end. I pushed a drill bit through the hole to clean it out a bit, then pushed through my wire. And to serve as an anchor, I twisted the wire around the nut that came with the afore mentioned seat clamp. Also, I pre-drilled and screwed in an old flathead screw to run the wire over.
Now, to the other side...
I remembered seeing a screw hook out in the shed, so I decided to use that for a tuner.
A note about the shed--no pictures of the shed will be used in this or any instructable for the safety of the internet. I briefly showed my neighbor the inside of the shed last summer. They are moving now. Suffice it to say that I have some awesome stuff in there waiting to be created with, and that the 2x4, wire, and hook used for this diddley bow were all only about 4 feet apart in there, even though I discovered them at different times during the build. I love that shed :)
So I screwed on the seat clamp, pre-drilled and slightly screwed in the hook, then wrapped the wire around the hook and turned it until music started happening! NOW its a diddley bow!
Step 22: Get Bluesy.
Finished! I called my musical buddy to ask him what key I should try to tune this thing to for the blues (he said D. i think.) Then I got on youtube and found a d tuner for a guitar and got pretty close. Then i started playing.
For a pick I use one of the washers from the seat clamp. For a slide, I use my pocket knife. So far, no splinters!(note, you can't use fingers to play notes because without frets they absorb the vibration from the string.) My son plays it with a little metal rod like a percussion instrument.
The diddley bow turned out to have an awesome, tinny sound and pretty good volume. It can be hung on the wall through the nut used to anchor the wire at the end of the neck. Its great for decoration and for playing. All the wood is from that one 2x4, and everything else was stuff I had laying around. (Admission-- I bought the glue). Tools used were a table saw, chop saw, and cordless drill.
Now I just need to learn to play the "momma needs a digital camera blues." hint.
And thats how this old 2x4 became a diddley bow.
Thanks for reading. Go build something :)
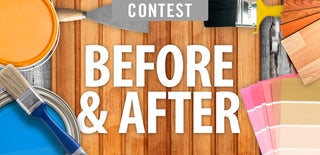
Participated in the
Before and After Contest 2016