Introduction: Simple and Durable Hydroxy Gas Generator
This instructable is a description of how I made my fifth hydroxy gas generator. Hydroxy gas has been an evolving science for me as I have learned what works, and what doesn't, what you need on a generator, and what you really don't, and that you shouldn't ignite a milk jug full of this stuff at 10:00 PM in the middle of your neighborhood, or you will have some explaining to do. My goal with this generator was to make a device that quickly separates water into hydrogen and oxygen gasses, can be made without advanced tools and is as tough as nails, so that I can throw this thing in my trunk and set it up at a friends house without worrying about spilling caustic fluid, or starting anything on fire. So let's get started.
Step 1: Build a Container
Containing the generator, bubbler, and power components in one tough and organized place is a must for a durable setup. I chose to make my own box from cedar wood because it is rot resistant, looks really cool, and smells nice. In order to begin making the box you will need to decide its final dimensions, and in order to do that, you will need to skip ahead and find your stainless steel carriage bolt. It is important to have the bolt at this stage because this will determine the final height of your box. It is also important to add the length of your gas output connecter to the length of the carriage bolt to determine the height of your box. I didn't do this and ended up having to cut down my connecter. Here is a list of supplies and tools I used for this step.
Supplies:
- 2 Cedar Boards 1.5 in wide x 1 in thick x 8 ft long
- Titebond III Wood Glue
- Wire Nails
- Hinges
- Latch
- Paint
- Painter's Tape
Tools:
- Drill Press
- Drill Bits
- Hammer
- Table Saw
- Rubber Band
- Clamps
- Chop Saw
- Rubber Bands
- File
- Sandpaper
The first thing that I did was to cut down my cedar boards into 16 pieces that were each 8 inches long. I cut 45 degree angles into 16 of them being very precise with this step. I took these pieces and glued them together to form squares. I didn't have a band clamp, and so I made do with rubber bands. These worked super well for me and after the squares had dried, I took them over to the drill press to pre-drill two holes at each of the joints. After pre-drilling, I knocked some nails into these joints and sanded, filed, and planed them all to something of the same size. Next I used the table saw to rip one board to half of its width and I made another mini square with this one. This was to get the box to an acceptable height for the generator. Using my table saw I then ripped down a couple more boards in half for the bottom of my box. I glued all around the bottom of one frame and using a lot of clamps and weights, left the glue to dry. Once the glue was dry, I put nails thorough these strips.
Next, I trimmed the bottom of the box and glued all of the square frames together, using clamps to hold them in place. Once they were dry, I heavily sanded the whole box. Next I scrounged around and found a nice pine board which I cut to make a square lid. It doesn't match the cedar, but I like the nice color contrast and it doesn't bother me. I sanded it down and clamped it in place while I attached hinges to the box. Clamping it while I did this allowed for near perfect hinge movement. Next I fastened the receiving part of the latch to a scrap piece of wood and I mounted the locking part on the lid of my box. I glued and clamped this scrap piece of wood in the right place by locking the lock while the glue dried. Then I went back and put some nails into this scrap piece.
After this, I thought that the box needed some pizazz, so I printed off a raindrop picture from Google Images, and after carefully cutting it out, I used painters tape to secure it to the lid of my box. I then painted the outline with royal blue oil-based paint, and I let it dry.
And then, the box was done.
Step 2: Build the Generator
Now it's time to get down to business and make the generator itself. My design is a negative electrode made from a modified stainless steel water bottle and a positive electrode made from the bolt, some nuts, washers and three shot glasses. The electrodes are held in place with square pieces of cutting board with circular ridges cut into them. The upper square has a hole for a cork that is for easy filling and emptying of water. The system for collecting the gas consists of a robust connector screwed into the top square, a small check valve to prevent siphoning and a bubble counter that I found online. Here is the list of supplies and tools that I used for this step.
Supplies:
- Stainless Steel Carriage Bolt
- Stainless Steel Nuts
- Stainless Steel Locking Nuts
- Stainless Steel Washers
- Stainless Steel Water Bottle
- Stainless Steel Shot Glasses
- Clear Plastic Water Bottle
- Cutting Board
- Tubing Connector
- Check Valve
- Tubing
- Bubble Counter
- Thread Tape
- Rubber Stopper
- Silicone
Tools:
- Drill Press
- Chop Saw
- Circle Cutter
- Hacksaw
- Ruler
- Fine Point Sharpie
- Masking Tape
- File
- Clamps
- Crescent Wrench
- Pinpoint Torch
- Pliers
- Sandpaper
- Drill Bits
- Crescent Wrench
The first step in building the generator is cutting out the squares of cutting board. The size of the squares is determined by the diameter of water bottle that you are using for your outer casing. I used a hacksaw and I cleaned up the edges of the squares with a file and my pocket knife.
Next I cut my clear plastic water bottle. The length of this water bottle is determined by the length of your carriage bolt and the thickness of your two cutting board squares, as well as the length of the bolt that will go on the bottom of the generator and hold it all together. I used a chop saw to slice cleanly and evenly thorough the bottle.
Next I made the negative electrode. This was one of the most difficult parts of the whole project. I have attached a diagram that I drew to help you get an idea of the angles and measurements of the cuts. I used a sharpie to make marks and masking tape to help me make the cuts straight. Once the bottle was cut to size, and the strange tab on top was cut correctly, my neighbor loaned me his propane torch and I used a pair of pliers to bend this tab into a quarter inch tube. I went thorough all of this trouble to make the final product more air tight. After this I used a scrap block of wood cut to precisely fit inside my bottle, to support the bottle while I made indentions and drilled a set of nine holes in my tube. These allow gas made on the outside of the tube flow to the inside, they allow electric current to reach the outside of the tube, and they look cool.
Next I made small markings on my shot glasses with a sharpie in the exact middle and using my drill press, not turned on, and a nail in its jaws, I made indentions in the shot glasses. Next I drilled thorough the indentions with a small drill bit in my drill press, and then a bigger bit, and then finally the 9/16 bit.
Next I drilled holes in my plastic squares. The top square got four holes and two ridges. A hole in the center for the square part of the carriage bolt to fit snugly into. A hole for the circular part of the negative electrode to slide into. A hole for the cork. And finally a hole for the gas output tubing connecter to screw into. The two ridges were made using a circle cutter and a drill press. The two ridges are for the positive electrode and the outer casing to slide into for a solid overall build.
Step 3: Assemble the Generator
The next thing I did was to sand the electrodes in a + pattern with 100 grit sandpaper. I sanded the inside and outside of my negative electrode water bottle and my positive electrode shot glasses. I also sanded the outside of my bolts. They will not contribute much surface area, but they are still part of the positive electrode.
Next I filled the small tube on the negative electrode with silicone and I screwed in and sealed the gas connector with silicone.
After these had dried, I put on some gloves and using oil defeating soap, I washed all of the metal electrodes very thoroughly and then I rinsed them off thoroughly with distilled water. For the most part I did not touch the electrodes past this point with my bare hands.
Next I assembled the whole thing. I began by putting on gloves and sliding the cutting board square onto the bolt and then using the square part of the carriage bolt and two crescent wrenches to screw on the first locking nut on tightly. I generously applied silicone inside of and around this joint. If I had been thinking, I would have screwed the other locking nut on at this point as well. But alas, I was not and I was later forced to thread two normal bolts onto the bolt ahead of the locking nut so that I could thread it on without breaking the silicone seal of the top locking nut. Locking nuts are hard to screw on.
The purpose of the second locking nut is to hold the shot glasses in place with a very small gap that allows for gas to escape. This will require some tinkering to screw it on just far enough. After this, I slid a shot glass on, followed by four washers and a regular nut. I repeated this until I had a third shot glass without any washers or nuts behind it. Then I put the negative electrode into place and heavily siliconed around where the tube pokes thorough the top square. Finally, I put a bead of silicone into the outer groves of both squares I pushed the outer casing firmly into the grove of the top square. Then I added the bottom plate and after a heavy coat of silicone around the hole in it, I added some epoxy as a makeshift thread locker and I screwed on the final bolt. After some finishing touches of silicone around the union of the outer casing and the squares, I set it down and let it dry for a solid 24 hours.
Step 4: Conditioning
Once the generator dried, I filled it up with distilled water and rinsed it out. If I did it again, I would have measured the water that came out so as to provide a precise measurement for the water that I would pour in with electrolyte. I put thread tape on the threads of the bubbler and filled it up with distilled water. I then cut pieces of tubing and attached the bubbler and a length of tubing off of the bubbler to the generator. I used 20 ml of Sodium Hydroxide (lye) to 3 cups of distilled water. I added the lye to the water slowly, stirring continuously. This solution was poured into the generator and once the power was hooked up, with the negative to the water bottle, and the positive to the carriage bolt, and the first bubbles of hydroxy gas churned thorough the system.
I ran the system for 30+ hours and changed out the fluid four times and the batteries five times. I changed out the fluid of my generator when I could see that it had a rusty color to it, as seen in the above photo, or when it had a significant amount of rust flakes in it. The conditioning made an obvious impact on the speed of my generator, that is, it got faster each time that I changed out the fluid. I knew that I had finished conditioning and could install the generator when the water remained clean for the duration of the batteries' life.
Step 5: Electrical
Electrical is my weak side, and so please take this advice with a grain of salt and a fire extinguisher. During the early stages of conditioning, you may need to use a higher voltage setup in order to obtain decent gas rates. Once I had conditioned my cell for awhile, however, I was able to use an ideal setup of 4 D batteries. The hydroxy community says that 2 volts is the target for your generator, but I am fine running 3 volts in mine. In order to achieve this setup, I used 4 D batteries. Two are wired in series with each other. The other two are also wired in series with each other. These two sets are wired in parallel with each other. This setup gives 3 volts while doubling the amperage output of power. I used a solid switch which I bought from Amazon.com for authoritative control of my system.
Step 6: Putting It All Together
Now I assembled everything. I began by cutting angled pieces of wood and gluing them to the side of the box to create a solid locking system to hold the generator in place. Then I wrapped the upper two triangular pieces with grip tape. This helped to secure the generator into the box snugly. Next, I used a hacksaw to cut apart the mounting piece that came with my bubbler. I then smoothed out the ridges in the plastic with a file, and drilled a hole thorough the piece. After shortening a nail and mixing up some epoxy, I glued and nailed this mounting piece to the wall of my generator. Next I used a soldering iron and heat shrink tubing to assemble the electrical battery boxes. I cut some wire and wrapped it around one of the switch terminals using heat shrink tubing to secure it and I attached my battery packs to the switch. Next I mixed up some more epoxy and glued the switch into place in the corner of my box. I then used some stainless steel screws to secure my battery boxes to the walls of my box. The wires were kept tidy with the help of a cable tie and a staple.
Next, I connected the negative wire to the water bottle with a piece of heat shrink tubing and a zip tie, and I connected the positive wire to the carriage bolt with a magnet. This setup allows me to easily take the wires off of the generator for filling it with fluid, and for more room in the box while I replace the batteries. I then cut small pieces of tubing and connected the generator and the bubbler with the check valve in between. Finally, I installed fresh batteries and a length of tubing to the bubbler outlet, and I mixed up a fresh batch of electrolyte fluid and poured it into the generator body.
And then it was all done.
Step 7: Conclusion
This instructable, like all instructables, is not free of errors.
RECALLS :
- I didn't account for the expansion of the battery packs when batteries are installed. I should have installed each of the battery packs with some space in between.
- The box wasn't quite big enough. I should have made it 6 3/4 inches wide on the inside, and 7 1/2 inch tall on the inside as well. As it is, everything is a bit cramped.
- I should have used a more robust sealant on the generator body. My silicone is holding up fine, however, I anticipate some trouble in the future.
Thanks for viewing!
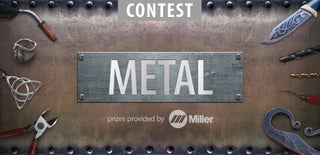
Participated in the
Metal Contest 2016