Introduction: Solitaire Ring With Accent Stones
Here's how to make a solitaire style ring that features accent stones down the sides of the ring shank. This is a great project for someone who has made some simple rings and is looking to step up a bit and maybe add a little more sophisticated stone setting techniques into the mix.
Let's get started!
Step 1: Tools and Materials
I covered in great detail most all of the tools that jewelers use in this instructable so please refer to that for learning about all of the tools and how they are used. Reading through that instructable first will also explain a lot of the terminology used. If there are ever any questions about tools or procedures please don't hesitate to ask!
There are a couple of tools used in the making of this ring that aren't in the mentioned instructable, most notably the jeweler's torch. My torch of choice is the Hoke brand. I've been using one of these torches for over twenty years at my work and it's been great. For gas I use a mix of Oxygen and natural gas. The Oxygen regulator is set to 35-40 psi and the natural gas is pumped straight into the building at approximately 5 psi. Another good setup is the Smith Little Torch and that's what I have at home since I use an Oxy/Propane setup there. The Little Torch is a bit smaller and lighter weight than the Hoke torch and the hoses are a bit smaller and more flexible. While this ring is made from 18K yellow Gold with a Platinum head you could just as easily make it from Sterling Silver (or even Platinum.) A couple of really good sources for jewelry metals and solder are Rio Grande and Hoover and Strong. Both are great companies with an excellent selection of materials.
Since this ring involves soldering there are three items that will come in handy- soldering flux, pickling compound and boric acid.
Soldering flux is used by brushing a small amount on a joint that is to be soldered. Flux helps clean the metal and provide for good solder adhesion. I keep flux in an old fingernail polish jar (with an appropriate bench monster on top!)
Pickling compound is used to clean metals of firescale after soldering. Some people heat this in a small crockpot but I've never found that necessary.
Boric acid is mixed with denatured alcohol (1 part boric to 3 parts alcohol) and this is brushed on to any metals before applying flux and soldering. This helps clean the metal before soldering and helps prevent firescale.
Step 2: Cleaning Up Castings
In the case of this particular ring, the ring shank and head were created as 3d models and the ring shank was cast in 18k yellow Gold and the head was cast in 95/5 Platinum Ruthenium. Since those materials are pretty pricey if you're just starting out you can buy premade ring shanks and cast heads directly from suppliers- this is also a great option if you don't have access to casting equipment.
There are an enormous variety of rings shanks and heads available form the previously mentioned suppliers RioGrande and Hoover and Strong. Otto Frei is also a good source. The style of ring shank used here is a cathedral shank. The head/setting used is called a basket head. With a cathedral style ring shank you want to pick one that has fairly thick shoulders as that will allow enough depth for setting stones down the side of the ring shank. A four prong basket head is probably the easiest style head to set a round or oval shaped stone into as they tend to have a little more room for stones that require greater depth to set- most colored stones will have greater depth than a Diamond as they tend to have a bit of an acorn shape to the underside of the stone. A four prong head will also allow for a much easier fit with a ring shank as there is more room between the prongs compared to a six or eight prong head.
Most premade settings are pretty clean and have a decent finish but since this ring and head were cast from 3d models they required a bit of clean up before they could be soldered together.
I first sand the surface of the ring shank using a sanding stick- this will remove the majority of the rough surface texture left from the casting process. Next I flatten the sides of the ring using a split lap. A split lap has slots cut in the lapping disc that allows you to see through it as it spins. A polishing compound is applied the the underside of the felt lap and it flattens and polishes the sides of the ring shank as the shank is pressed against the lap. The ring shank can get pretty hot when doing this so sometimes it is pressed to the lap using a small piece of leather.
Once the sides of the ring look good the remainder of the ring shank is polished using tripoli polishing compound and large buff on the outer surface of the ring and a small rotary tool brush for the detail areas.
The Platinum head is smoothed using a small brown rubber wheel in a rotary tool, followed a greenie wheel and then Platinum polishing compound with a small wheel brush. The brown wheel does a good job of smoothing the casting while the greenie wheel gives it a bit of a pre polish before going to polishing compounds.
At this point in time we're not yet going for a super mirror like finish, rather just a nice luster to get everything looking nice before soldering.
Step 3: Soldering the Head
The first step in soldering the head to the ring shank is getting a proper fit. This can be a bit tricky and requires a fair bit of patience! A head that is soldered in poorly will really show when you go to set the stone later so it is absolutely worth taking your time to get it right as it can be darn near impossible to correct later.
The head in this ring is soldered to both the shoulders on the sides of the ring as well as to the bridge that goes underneath the head- this gives it a good solid connection the the ring shank. I begin by trimming the shoulders of the ring shank to fit the upper support wires of the basket head using a small ball burr. I want the wires of the basket head to rest in the grooves but in the ring shank shoulders. I always check to make sure the head will sit level as I trim the shoulders.
Once I know the head will set level and straight I hold the head to the ring shank using locking "head and shank" tweezers. These special tweezers are designed specifically to hold a head in place during soldering. I then coat everything with a boric acid mix and light it on fire- the alcohol will burn off and leave a white film behind that will help protect the ring during soldering.
Now I cut up tiny chips of hard solder and ball them up with the torch. Next coat the areas to be soldered with a bit of flux and position the tiny balls of solder to those areas using flux. The flux will help hold the solder balls in place. Now solder the joints. The torch method I use is to hold the ring/tweezers in one hand and the torch in the other while heating the metal on the opposite side of the solder. The reasoning behind this is that you have a lot more control over where the heat is going when holding the item to be soldered in your hand vs. placing on a bench top- it will also heat up quicker and more evenly and it's easier to see where you are applying heat. You always want the solder to flow to the heat source. If you apply heat directly to the solder the solder will quickly melt but it will have a difficult time forming a good bond with the metal and you will get a cold/incomplete solder joint and the head can easily be broken off the ring shank (which is real bummer when you lose a nice stone!)
Once your soldered joints look good soak the ring in a pickling solution for a few minutes to clean off all of the boric acid/flux residue. If you are soldering a white Gold head or Platinum head to a Gold ring shank you can go ahead and quench the ring right after soldering- this will clean it a bit faster and will anneal the head, making stone setting easier. If you are using Sterling Silver do not quench it- let the ring cool and then let it soak for a few minutes in the pickle afterward. Sterling Silver is already pretty soft so if you heat it up and quench it it will be like butter when you go to set the stone in the head and it'll be difficult to get the stone tight in the setting.
After pickling and rinsing with water give the ring another very quick light polish.
Step 4: Setting the Accent Stones
Now comes the fun part- stone setting!
The method shown here is called bead setting. This involves setting each stone into a countersunk hole and then pushing four small beads of metal over the stone to hold it in place. Good lighting and magnification make this much easier!
Typically I want to use Diamond cut stones that are one millimeter smaller in diameter than the width of the ring shank. Diamond cut stones are good for this application as they are cut to specific geometry that makes them easier to set due to overall depth and girdle thickness. You can get most colored small stones in a Diamond cut shape.
Begin by laying out your stones on the shoulders of the ring shank. I position them on the ring shank using a tiny bit of beeswax and then mark the stone positions on the sides of the ring using a fine tip sharpie marker. You want to leave a little bit of space between each stone- remember that since they are being set down into a curved surface the will get closer together as they are set into the ring. Once you are happy with stone positioning, remove each stone and mark a center point for each stone using a small ball burr.
Now drill small holes (I typically use something around a .7mm drill), open them slightly using a small ball burr and then cut seats for the stones using a straight setting burr that matches the stone diameter. To get the stone depth right you just want the top of the stone (called the table) to be flush with the surface of the ring. If it set too high you will have a hard time forming beads over the edges of the stone.
Now take a knife edge graver and cut a border on the outside edges of the stone openings. The grooves should just come to the edges of the stone seats. Next use a round nosed graver or very small ball burr to remove material between the stone openings.
Remove excess metal between the stone openings and the cut border with a small flat graver. Cut small lines between the stone seats with a knife edge graver to create small triangular shaped metal prongs- there are four prongs for each stone seat.
Once the stones are placed in the seats use a small flat graver to push the prongs over the stones. Then use a small beading tool to shape the prongs into a round bead shape. On this ring I left a clean edge on the border but if you want something more decorative you can use a millgrain wheel to create a beaded border. Now lightly go over the stone setting area with a small stainless steel brush with a rotary tool in order to remove any metal burrs that are present and smooth the metal.
Step 5: Setting the Center Stone
Time to set the center stone!
First I trim the prongs slightly as that's where the head casting was sprued. I make sure all prongs are the same height. Then I mark the height of the where I want the stone girdle to sit using dividers- in this cast I want the stone to sit just barely over half way up the height of the prongs.
Using a 90 degree hart burr I cut the seats for the stone, taking care not to cut more than half way through the prong. Now bend back the prongs slightly using chain nose pliers. I bend them just enough to get the stone into position where I can check the fit. In this case the girdle of the stone is a bit thick so I use a tiny ball burr to cut a bit more clearance for the stone girdle. It's best to cut just a little bit at a time and check the stone fit as you go, making sure the stone will sit straight and level.
Once the stone is placed into the notched prongs gently squeeze the prongs together so the top of the prong is just touching the top of the stone. Using chain nose pliers grab prongs in pairs and squeeze them together to tighten the stone. Once the stone is tight file down the height of the prongs and round them off using a small needle file. Use a cup burr to round off the tip of the prongs and polish the prongs using small polishing wheels. Once the center stone is set the ring gets a final high polish with rouge.
After a thorough cleaning the ring is finished- stand back and admire your handiwork!
Hope you found this helpful and as always if you have any questions just ask!
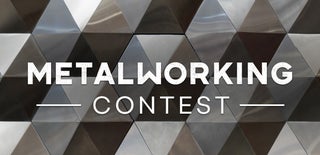
Second Prize in the
Metalworking Contest