Introduction: "The George" Liverpool's Liver Building Clock Replica
Being from Liverpool I am extremely proud of where I'm from and for as long as I can remember I have been fascinated by 1 building in the city, the Royal Liver Building, and specifically it's astonishing clock.
This clock is famous for being the largest in the UK, people always assume the Great Westminster Clock or "Big Ben" is the largest but they are mistaken.
So on the hunt for a project I was inspired by an old round topped coffee table which was set for the tip, in the mindset that this could be put to use somehow I thought "why not build a clock?" I ventured down the way of creating my masterpiece and instantly thought of the great clock I have always known and loved and there began a labour of love with the vision to create my very own replica of my favourite clock.
The coffee table didn't make it, it was far too heavy, but the idea was stuck and I had to move forward.
Supplies
* 3mm MDF Board for the inner detailing of the clock
* 6mm MDF board for the outer detailing of the clock face
* 3mm Spectrum LED Perspex
* 8mm Balsa Planks for the hands
* Steel Seemstress Pins (Box xontains around 1000) to emulate rivots on clock hands.
* MDF Sealer
* Fine sandpaper (240 grit wet n dry did the trick for me)
* MDF Primer Paint (I used white)
* Matt Black Spray Paint (I used Car Paint for its durability in sunlight)
* L shaped plastic Angle for clock surround
* 240gsm Card for Clock Walls
* Wooden blocks (size defined by distance between clock face and back of clock)
* 12mm Dowling for mounting face to back.
* 10M LED Strip (Mine was labelled as yellow but the colour is more Amber / Orange)
* 2 core wire for joining LED strips together
* Push switch (I took my switch from an old torch)
* Soldering Iron
* Hot glue gun and glue sticks.
* Sharp knife for carving with plenty of spare blades (stanley knife, craft knife or the likes)
* Multi Tool (I used my trusty Dremmel) with sanding attachments for carving the hands from Balsa.
* LED Driver (I used a 50W Driver, conditions are different dependent on your LED's power)
* Mains plug & 3 core cable for powering LED Driver.
* Junction boxes / Terminal Blocks
* Contact Adhesive
* Mains Powered, heavy duty clock movement for large clock faces (https://www.agtshop.co.uk/product/5131-high-torque-mains-clock-movement.html)
* Cardboard boxes and bin bags to construct a temporary spray booth - some people have the luxury of a space for spraying in, I didn't and had to do this in the freshly decorated dining room!
* Optional - Local artist to paint a mural on your wall, I was lucky that there is a famous Liverpudlian Artist willing to do this - https://www.paulcurtisartwork.com/
* Laser Cutter - Again I am lucky to have a local community shared workshop that has a fantastic laser - https://doesliverpool.com/
Step 1: Planning
Planning for me was all about getting the detail right. I knew exactly what the clock looked like but I wanted to ensure every bit of detail was as accurate as possible.
This involved looking at images online (we all love google images!), however, none of the images available got close enough for me to see exactly how much detail was involved. For instance, from the ground, the entire face looks as if its all the same level but upon closer inspection I discovered the inner detail of the clock face was actually a thinner material than the outer ring of the face.
The clock hands being made of sheet metal that has been rivitted together so when you actually get close to the hands and see them you can see all of the rivots.
The one thing I was never going to get accurate was the glass that makes up the face of the clock. The real life clock is actually made up of hundreds of individual panes of glass, which over time have had to be replaced through damage, the effect this gives during normal daylight hours are different shades of white glass on the face in between all the detail. At the scale of my clock (it's 35" Diameter) this would have been close to impossible to achieve.
You can't see any of this detail from the ground, and at the time you were not allowed to go up the towers for a closer look (the building now do tours so you can get up close and personal with the clock faces and behind them too - https://rlb360.com/)
I chanced my arm and went to another famous Liverpool building opposite called the Tower Buildings, they very kindly allowed me onto their rooftop and from there I was able to take close up pictures of the actual clock (Sorry I can't post these) and see all the little details that were hidden from the ground.
Step 2: Design
I used Adobe Illustrator to create my design, using my photographs as a guide to get all the dimensions and angles correct.
I was then able to create CAD files for use on the laser which would allow me the most accurate cutting available for the detail I wanted.
Step 3: Laser Time
Importing the files the laser did a wonderful job, separated into 2 files (inners & outers) due to the difference in thickness I needed 2 to solid pieces.
The outer ring of the actual clock is made up of 12 individual pieces, I couldn't achieve this with the laser as I didn't have the brain power to work out how much I would need to resize my design to allow for the kerf of the laser (thickness of the cut and material loss this causes) As much as I tried with individual pieces it would never form a complete circle without gaps so I opted instead to have the laser engrave lines in the face to give the illusion that they are separated pieces.
I also used the laser to cut the circle of LED Perspex but just being a white circle didn't see the point in taking a photo of it!
I am OBSESSED with laser cutting it amazes me hence the amount of images at this step :o)
Step 4: Dry Fit
Before moving on further you want to make sure the pieces fit together, using digital drawings I was confident enough everything would be fine and I didn't need to think of the measure twice cut once rule but it's always better to make sure before you start painting & gluing.
Now the project is really starting to take shape!
Step 5: The Hands
Unfortunately I have no images of this process as it was an extremely dusty process I didn't want any electronics getting clogged up (i'd just got a new phone so was feeling precious of it)
To make the hands I printed out a 2D image of the hands and stuck it to the Balsa wood, I then proceeded to carve the wood by hand with my knife and knock chunks off here and there to create the general base shape. I got the final shape as accurate as I could with the old Dremmel and the sanding heads.
Finished the hands off with 247 seamstress pin heads which create the look of Rivets.
Measured the width of the centre fixing on the clock movement with some digital calipers and drilled the holes in the hands (drill a hole a mm or 2 smaller as the wood is very soft and the drill bit generally moves a bit).
Glued the fixings for the hands into said holes with some strong contact adhesive, covered with some wood sealer and leave to dry for a day.
Now for the most important part, balancing the hands. you cannot simply just make your own clock hands and attach them to a movement. Any clock maker will tell you that a movement is only as good as it's hands and your hands need to be perfectly balanced in order for your movement to work efficiently and stand the test of time (no pun intended)
To do this I hollowed out the backs of the hands to give me somewhere to add weight where it was needed and not add any more bulk to them. I found the point of balance (this is quite difficult) and then just added chunks of solder to the side that needed to have weight added until it sat with a perfect balance.
Once the balance was confirmed by leaving it there for about 10 minutes without it dropping on either side, I melted the solder and poured it into the hollow at the back of the hands and let it set.
Once it had set and cooled I popped the solder out (it doesn't naturally stick to wood) and stuck it in place with some contact adhesive for a permanent fix.
Primed and painted the hands in the same way as everything else with plenty of sanding in between.
The hands are probably both my favourite and least favourite parts as they have the most detail but even after crap loads of sanding and painting you can still see a faint element of the wood grain. Balsa maybe wasn't the material I should have went for but I stuck with it, it's not the end of the world and you can only REALLY tell when you're really close up to them.
Step 6: Paint, Sand, Paint, Repeat.
One of the more tedious tasks but if you want a great finish you have to put the work in.
MDF sealer used so that the board doesn't just suck up all the paint you throw at it, I used a few coats just to make sure even though the tin said 1 coat would be enough. I sanded in between coats too just to keep a good smooth finish.
After the Sealer it's onto the primer coat, the same couple of coats and sanding in between applies to ensure a good finish. I opted for white primer for some reason but in hindsight I probably should have used grey as when applying the final coat of white it was stupid difficult to remember where I had painted and where I hadn't.
It's also difficult to get full coverage with the paint here as the exposed edges also need to be painted but without having splodge marks, I couldn't use a brush because I didn't want brush marks bud I had to use a small brush to touch up areas that the spray just coudn't reach effciently (sharp angles are the killer here)
Once the primer was done I sprayed the whole thing with the white finish coat, masked off the areas to stay white and applied the black paint. Again sand in between and apply a couple of coats.
all this was done in a prefabricated spray booth made up of scrap cardboard boxes and bin bags.
Step 7: Another Dry Fit
Now we're all painted just check everything still fits because you know paint increases thickness - I had to sand down the inners a little here to ensure it got snug as it was a mm or so over what it had been originally and that really did make a difference.
Step 8: No Lighty No Likey!
Continuing to be a stickler for detail, I wanted my version to be as close to the original as possible, this means it needed to light up at night. To me this seemed simple, I then made it more complex and ended up simplifying once again!
LED's were the best option for obvious reasons; high light, low power and no bulk, tick tick tick.
I bought 2 x 5M strips of Amber LED's, they're self adhesive so I was able to place them pretty much wherever I wanted, the hardest part for this was to figure out the spacing of the LED's and also the pattern in which I would lay them (straight lines being the only real option as strips don't bend when they lay flat). Some people mentioned edge lighting from the outside in but as the clock was so large I would never get it bright enough to give an even colour across the whole face. To get the even lighting you have to get the distance of the perspex and the spacing of the light source just right.
After A LOT of testing on this I found the best option for spacing is space between light and face minus 25% so for example if the space between the light source and the face is 10cm the spacing between the strips of LED's needs to be 7.5cm. You can see in the images the way I decided to lay out my strips and this rule applied pretty much across the whole face (there are a couple of areas where strips are a little closer but this was determined by the fact that LED strips can only be cut in certain places and I would rather the strips were slightly too close than too far away.
After sticking the strips down I had the tedious task of soldering away to connect them all up. This was time consuming for me as I decided to test the strips after each solder, I'm not a confident enough solderer to join them all up and test afterwards, it was better for me to take the long road.
Once they were all connected up and working I applied hot glue over the top of every single solder joint just to give me reassurance they were not going to come loose when the clock was placed on the wall.
Now I knew they all worked I had to decide on what was going to turn them on or off, my head was ruling my heart here. My heart was telling me the lights need to come on automatically when it gets dark, just as the real one does, my head was saying just use a switch as then you have control over it.
I followed my heart and bought a light sensor switch, got it all wired up and set in place only to find the area I was hanging my clock was pretty shaded all day and so, the LED's stayed on permanently and so I reverted to my head, having spent out on a light sensor I wasn't keen on spending any more so I took a push switch from an old LED torch (from a christmas cracker no less) and wired that up. I decided to hide it behind the clock walls rather than make a cut out for it, it sits directly underneath the 6 o'clock point and as the wall is flexible (cardboard) you can press it without any fuss and there's no switch extruding from it. The video shows the switch in action, not bad for a Torch that came in a Christmas Cracker!
Step 9: Dry Fit With Lighting
Lights working and face painted I had to check the coverage of the light with the clock temporarily constructed. All was well and I was chuffed to bits I didn't have to take a backwards step to rectify any problems, everything was going to plan.
Step 10: Lining Up the Face With the Back
Obviously joining 2 flat circles together and getting them perfectly in line is quite difficult especially as they need to be mounted separately - the back needs to be screwed to the wall and the front then has to attach on top for obvious reasons and the clock face can only sit one way because the switch is at 6 o'clock and needs to be at the bottom.
I was able to align the 2 pieces using wooden blocks and dowels. the blocks sit on each part 5 on each side and I drilled holes for the dowels so that when putting the face up the dowels provided the alignment, you can see the blocks in place at 12, 2, 4, 8 & 10 o'clock positions as I saw these as the perfect weight bearing positions for a circle and provide an even balance to not put too much strain on any 1 area when hanging on the wall.
Good old contact adhesive stuck everything together.
I took the plunge and screwed the back plate to the wall, plugged it in to make sure the lights were still functional and then placed the front face on top to ensure it lined up and still held firm. It did.
Step 11: Hiding the Wires.
Being mains powered and as I had a rather stunning mural on the wall I didn't want there to be any wires dangling around so I was able to drill a hole directly behind where the clock face would sit and feed this behind down to the plug socket on the left hand side of the wall, being a new build house it was pretty easy to navigate the rear of the dry wall using a long bamboo cane with the cable attached to it to feed it over.
Step 12: The Mural
At the beginning of this project I was just putting a clock on the wall, I hadn't thought about the possibility of a mural to make it look even better.
I was browsing my Twitter feed and stumbled across some work done by Paul Curtis - I already knew about Paul's work in the City of Liverpool and a lot of his work has become quite famous now. The piece I saw on his Twitter account was amazing and so I dropped him a line and asked him for a price to do my wall.
Paul is a real great bloke, he came down and measured up, did some digital mock ups for me and we rolled from there. He didn't tell me at the time but he had no idea why anyone would want a mural of the Liver Building without the Liver Birds included, only at the end of the project did he let me know he was never quite sure exactly what I was trying to achieve and thankfully he was impressed with the outcome.
I'm so pleased I decided to do this, having the clock alone would have been great but having the Mural really sets it off.
Step 13: The End
It took some time to get there but the results for me are exactly what I wanted. I hope you liked my Instructable, maybe you'll feel inspired to do something yourself.
Thanks for reading :o)
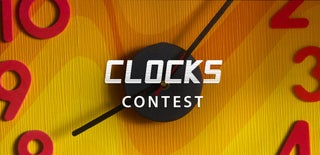
Runner Up in the
Clocks Contest