Introduction: ThunderCats Sword of Omens - Dagger Form
Lion-O, the leader of the ThunderCats, lead his team with a powerful, supernatural weapon - the Sword of Omens. When not wielding the sword in battle, the sword was in a smaller dagger form. You're not new to this info though. You're checking out this instructable because you were/are a fan of the ThunderCats, and what you don't know, but want to know, is how to put together a replica of the dagger carried by Lion-O.
The materials that I used for this project were:
Polystyrene Plastic
MDF
PVC
Expanded PVC
Bondo Body Filler
Milliput
Free Form Air
Spot/Filler Putty
Cyanoacrylate
5 Minute 2 Part Epoxy
Silicone
Polyurethane
Ease Release 200
Aluminum Powder
Primer Paint
Acrylic Paint
Air Brush Paint
Urethane Clear Coat
The tools I used for this project were:
Table Saw
Band Saw
Coping Saw
X-Acto Knife
Clay Sculpting tools
Sandpaper
Sanding Sponges
Airbrush
This materials/tools list is long, but don't be intimidated by it. These items are what I used because I already had them, and am comfortable using them. Substitute any material/tool with one you are more comfortable using. Also silicone and polyurethane aren't necessary if you aren't going to make a mold and copies of your dagger. One other thing, my methods aren't set in stone. Change any technique to one that is better suited to your skills set.
Step 1: Template
I did a Google image search for the Sword of Omens in dagger form, and used it to make my template. A vector template was drawn with Adobe Illustrator. The vector format is scalable, so the template can be changed to a different size without becoming pixelated.
I find it easiest to first create a line down the center of the reference image and draw one half of the template, then copy and flip what I have drawn to the other side, making one completely symmetrical template.
Step 2: Handle Shaping
I began the handle with a polyurethane plastic rod. The rod was made by casting polyurethane into a piece of 2" PVC pipe and letting it cure. The cured piece of polyurethane was put into my lathe and turned to shape, following the layout of my template. I used a small metal ruler and calipers to measure and gauge the correct ring widths and distances on the handle.
The benefit of polyurethane compared to a block of wood is the lack of wood grain. There is a downside though; if a pressure pot isn't used when casting the polyurethane, there will be air pocks in the final piece. To hide them I left the piece on my lathe and used spot putty/filler to fill in the air pocks. Once the putty was cured I turned the lathe on and sanded the putty smooth with a high grit sanding sponge. The last step to hide the air pocks was using filler primer. The role of filler primer is in it's name, it fills in minor scratches. 2-3 coats of filler primer on the piece, then wet sand the primer with a high grit sanding sponge (I use 1000 grit minimum) while the lathe is running.
Step 3: Handle Details
All of the handle details were made of polystyrene plastic. For the butt details, I first made a working paper template and then traced that onto two pieces of polystyrene.
The first piece of polystyrene was adhered to the butt of the handle with cyanoacrylate. The second piece had the middle section cut out so it could be adhered to the sides of the first piece, forming a "plus" shape.
All of the gaps in these pieces were filled in with spot putty. They were then smoothed and rounded off with different grits of sand paper/sponges. I forgot to photo document this step. I also forgot to photo document the curvy detail pieces. They were done the same way as the butt pieces. Paper templates first, transferred onto pieces of polystyrene plastic. I made a center line down both sides of the handle to properly align these pieces. Any gaps were filled in with spot putty.
The holes where the gems would be mounted were first centered and marked, then carefully drilled out with a hand drill.
My last step for the handle was to check for remaining flaws. I put primer paint on it so it would all be the same color. It's easier to spot flaws when everything is the same color. I checked and fixed the flaws, then wet sanded the whole handle for a smooth finish. A wooden dowel was adhered to the top of the handle to form the pour spout in the mold.
Step 4: Dagger Base
The base was cut out of 1/2" MDF. Polystyrene was used for the front and back details, adhered with cyanoacrylate (super glue). 1/8" thick pieces of wood were added to the sides.
I penciled in guides on the bottom of the base to start the "ramp" detailing process. The material used to create the "ramps" was Milliput, which is a two part epoxy clay that cures in about 3 hours depending on room temperature.
A piece of 1/8" thick wood was centered and adhered to the base. I penciled in more guides for the next addition of Milliput. I applied the Milliput and roughly formed it to shape within the guides and let it cure. Once the Milliput was cured, I sanded it to the proper shape. The edges of the Milliput were cut flush with the 1/8" wood using an X-Acto knife.
Step 5: Cross Guards
I used 3/4" MDF for the base of the crossguards construction. After transferring my template onto the MDF, I cut the crossguard shapes out. Next, I drew a taper guide on the top sides of these shapes, and taper-cut the pieces on a band saw.
Polystyrene plastic was used for all of the crossguard details. Both faces of the crossgaurds needed to look the same. To accomplish this, I transferred my template shapes to the polystyrene, then cut them out with an X-Acto knife. I then put one piece on top of the other and held them together while sanding each of the edges with sandpaper and/or files, making the shapes identical to one another. For just a couple of pieces, this method is fine. Considering this project, like most I do, have several detail pieces, a laser cutter would be extremely beneficial. I do not own a laser cutter, so I used the method described here for all of the detail pieces in this build.
The crossguard detail pieces were adhered to the MDF with cyanoacrylate. Once they were all on, I sanded all of their edges flush with one another. Polystyrene sands down very easily, so I used high grit sand paper/sponges leaving minimal scratches in the plastic, and thus, minimal touching up.
Spot putty was used to fill in any voids and uneven joints that I couldn't make flush with one another by sanding.
Step 6: Eye of Thundera
The base of the Eye was made from PVC pipe and polystyrene. The polystyrene was adhered to the inside of the first ring of PVC with cyanoacrylate. The polystyrene was inset enough so that the piece that would become the Eye, would be slightly inset when set on it. The second ring of PVC was added to the polystyrene on the opposite side of the first PVC ring, also inset. I then attached the "Eye base" to it's "cradle". I forgot to document the construction of the "cradle", but it was done similar to the crossguards, and base piece.
I used a strip of faux wood blind to build up the space between the PVC rings. I'm not certain what the material of the faux wood is, but I think it's an expanded PVC, like Sintra.
Polystyrene discs were cut slightly bigger than the PVC rings they would be sitting in, because they would have a bowl shape to them, making their total diameter smaller. To create a dome in the discs, I individually heated them with a heat gun just enough to make the plastic pliable and pressed into the center of the discs with a round object until they cooled. I adhered them to the PVC with cyanoacrylate. The gaps around the outside edge of the domes were filled in with spot filler.
Step 7: Spade Detail
The Spade detail of the Sword of Omens has always been odd to me. It's part of the sword though and must to be made.
The spade shapes were cut out of polystyrene. They were then cut in the middle and adhered to the base.
A center guide was made of polystyrene. This guide is to make sure end product is straight and symmetrical.
The spade was filled in with Milliput. I formed the Milliput close to the desired shape of the spade. Once cured, I sanded it to the final shape.
With the spade finished, I attached the "eyes". The eyes were made of polystyrene.
I primed and wet sanded this piece before adding the texture within the detail areas, because I didn't want the texture to lose any detail.
Step 8: Blade
The base of the blade is polystyrene, cut to the shape of the blade. I used the edge of a faux wood blind, slightly tapered, to make the spine of the blade. The frame of the blade was filled in with Bondo body filler.
The first details of the blade were made with polystyrene. Two pieces were cut out and their ends were glued together making a sleeve that would slide onto the blade, ensuring the two pieces would be properly aligned with one another. Polystyrene triangles were cut out and adhered to the blade. The sleeve was then slid into place, and adhered to the blade. The small gaps were filled in with spot putty. The bigger gaps in between the sleeve and the blade were filled in with Milliput. So that the blade would sit properly on the eye, I used the same PVC pipe that I used to make the eye, and marked the sleeve for cutting. I used a Dremel rotary tool with a sanding drum and sanded this piece to the proper shape.
The textured areas on the dagger body were made with a medium grit sandpaper. The most efficient way to prepare the sandpaper pieces, is to first mark them using their respective polystyrene detail pieces, then cut them out and test fit them before the detail pieces are glued into place.
The blade was primed and wet sanded, then adhered to the body with 5 minute, two part epoxy adhesive. The gap in between the blade and body was filled in with Milliput.
Step 9: Handle Mold Preparation
I rolled out a slab of non-sulfur sculpting clay (the clay must be non sulfur based, or the silicone will not completely cure) big enough for the handle to fit, and have room for registration keys for both the mold and the mold jacket. . Registration keys are a must! Without them, the two sides of a mold/mold jacket, won't line up properly. I put the clay onto a piece of foam board so I could move it around as necessary. I laid the handle on the clay and "traced" it with a sculpting tool. I then dug out the clay within the traced shape. I made the dug out hole slightly smaller than the handle. This made smoothing out the seam line easier, because there were little to no gaps between the clay, and the handle.
After the handle was pressed into the clay, small clay worms were laid where the clay and handle met, then they were smoothed out to fill in the seam line.
When the seam line was finished, I added registration keys to the clay. Small holes were dug out with a clay tool, then smoothed out with the end of a paintbrush. Again, registration keys are a must, as they insure proper alignment of the two mold halves.
Step 10: Handle Mold & Mold Jacket
First, a print coat of silicone. I used Rebound 25 by Smooth-On The print coat(s) capture the detail of the master piece, and help prevent air bubbles from forming in the silicone. I do 1-3 print coats before thickening the silicone for the final brush on coats. This particular silicone needs to set about an hour or less depending on room temperature, and fully cures in about 6 hours.
After the print coats, I put on a few coats of thickened silicone, along with mold to mold jacket registration keys. These registration keys are to insure the mold is properly aligned with it's mold jacket. This silicone was thickened with a thickening additive called Thi-Vex, also a Smooth-On product. Thickening the silicone isn't absolutely necessary, but it will take MUCH longer to build the proper thickness in your silicone without it.
When the silicone was fully cured, the outside edge of the silicone was cut off to make a clean edge all the way around it. I then cut registration keys out of the clay for proper mold jacket alignment, and then the mold jacket material was added. I made the mold jacket out of an epoxy clay called Free Form Air. I usually make fiberglass jackets, but for this project I needed to work inside my house which isn't an option with fiberglass because of the extreme mess and toxic fumes. Free Form Air was a perfect option for me because it's 99% less messy than fiberglass/polyester resin, and has no fumes. Free Form Air is another two part epoxy clay, but much less dense than Milliput. I colored the first side of the mold jacket clay with blue pigment. This made it easier to find the separating seam line between the two halves easier when it was time to crack open the mold jacket for the first time.
After the mold jacket clay of side A was cured, I turned it over and pulled the sculpting clay off of everything and cleaned up the remaining sculpting clay from the seam line. Everything got a coat of Ease Release 200. This is a silicone free lubricant, which prevents side B of the silicone and epoxy clay from sticking to their side A counterparts.
Side B of both the silicone, and mold jacket go through the same processes as their side A counterparts.
The last picture in this step shows the finished mold and mold jacket, along with the handle master.
Step 11: Dagger Body Mold & Mold Jacket
The same exact procedures used to make the handle mold were used to make the dagger body mold.
A thick clay pancake was formed, then the dagger was traced and cut out of it. The dagger body was "planted" into the clay, and a seam line was created, then registration keys added. I did have to make a second level of clay for the blade because of the height difference of the blade compared to the body. Several coats of silicone were applied with registration keys added to the final two coats. The silicone edge was trimmed and registration keys were added to the clay. A clean edge around the mold was cut using an X-Acto knife.
Jacket mold made with Free Form Air.
The last photo in this step shows the first dagger casting, using a cold cast technique, explained in the paint section.
Step 12: Casting
Casting with a new mold is always an experiment. It usually never works just right the first time, so I'll lay out the basics, and leave you to do trial and error and develop your own methods.
Straight forward. The mold needs to be lightly coated with a release agent, or dusted with a powder like baby powder. Using a release agent like Ease Release 200 yields the best result, but makes painting the casting difficult, as the release agent bonds to the casting, and paint doesn't like to stick to to it.
Put the mold/mold jacket together, and hold it together with rubber bands, bungees, straps, etc.
Mix the casting material then pour it into the mold and slush it around inside of the mold. I personally find it best to do more than one pour. The first pour(s) being print coats, using small batches of material.
After the print coats, I mix bigger batches of material, and still slush it around inside of the mold. I do this until the mold is full of material.
Once the mold is full, let it cure for at least the amount of time specified by the manufacturer. Not doing so could result in your cast piece deforming.
Step 13: Assembly
The assembly of the dagger can be done more than one way. I forgot to photo document the process I used, but the following steps are how I did it.
I first drilled a 1/2" hole, a few inches down the center of the handle using a hand drill and 1/2" spade bit.
I cut a 1/4" piece of rebar, to a length of around 6". I put the rebar into the hole I drilled into the handle, and then filled the handle with polyurethane. Before the polyurethane set, I made sure the rebar was as straight and centered in the hole as I could. Once the polyurethane sets, the rebar is locked into place.
Another 1/2" hole was drilled a few inches down the center of the base of the dagger body. I partially filled this hole with polyurethane and put the other end of the rebar in it, obviously the end sticking out of the handle. Before the polyurethane set, I centered the handle with the body of the dagger. Once set, the handle and dagger body were locked together. This method of assembly is not quick, but ensures the handle can't snap off from the body of the dagger.
The acrylic gems were adhered to the handle with cyanoacrylate.
Step 14: Paint
I also did not photo document the steps I used to paint the dagger, but here is how I did it.
First off, the metal look is actually metal - I cold cast this dagger. I'll explain this process. Before I began casting the dagger, I dusted the mold with aluminum powder. The polyurethane bonds to this thin layer of aluminum powder. The surface of the cast piece is buffed with 0000 steel wool, and makes the aluminum powder shine like the metal it is. I prefer this method over a metallic paint, because it doesn't appear to be metal since it really is metal. Also, because it isn't paint, it doesn't require any protective clear coating. The steps of primer paint, metallic paint, and clear coat are all done in one step.
After the piece is buffed with the steel wool, I cover the whole piece with an acrylic black wash. Before it dries, I rub it into all the crevices, and then off of the rest of the surfaces with a rag. This makes the metal look richer. I use this technique even when I've used a metallic paint.
The green textured areas were painted by brush with watered down airbrush paint. Acrylic paint could have been used as well. I didn't paint these areas solid green, but left unpainted spots to achieve a more used/worn look.
The eye was painted with an airbrush and airbrush paints. Off white first, then red faded into the off white, followed by a yellow fading from the off white into the red.
I cut a short piece of pvc from the same piece of pvc I used to make the rings for the Eye of Thundera, and placed it on the Eye of Thundera. This was an easy way to mask off the dagger while clear coating the paint on the Eye of Thundera. Yes, I only clear coated this area, using a urethane clear coat. I didn't clear coat the whole dagger, to keep the metal look more true. I was not worried about the acrylic black wash or green airbrush paint coming off. They aren't on surfaces where paint would easily rub off. Water would make the black and green paint more easily come off, but the dagger would have to be wet for more than a brief moment. This dagger shouldn't be in any water, and if it is, then it means the house has flooded, and the paint on the dagger is the least of worries.
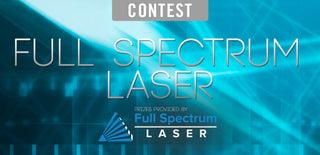
Participated in the
Full Spectrum Laser Contest 2016