Introduction: Animatronic Hand Statue
- Addition to the section on the crank shaft build!
- Addition to the section on the fingers
- addition to the section on tumbling
Originally this was going to be a replica build of the hand and arm displayed in the terminator movies at Skynet. But, then i wanted it to move. I was still going for the look of a statue/display model, but at the same time I wanted it to be interactive. A couple of years back I built a robotic salmon for the local museum complete with infrared camera eye, monitor display and articulating mouth fins and body. All of these could be controlled by the patrons themselves. Interactive art is the new black.
This build does take into account that the builder can weld and has access to a welder. Of course this could all ways be built with using rivets or nut and bolt, but would be need to be thought out a bit more. I'm sure one could use alternate metals too, I used aluminum rod for the fingers and thumb, and the balance out of recycled bits of steel. Total cost for this was about 30$, with the biggest cost being the aluminum 17$. These were scrap, but when buying metal such as this they charge by the pound regardless if it came from there scrap bin. The rest was used up buying washers, odds and ends, air craft cable and the brass connectors.
This instructable has been a while in the making. All though the total combined hours wasn't that great, the space of 30 minute intervals stretched it out over a month. Total time was about 16 man hours.
Last but not least, safety. Working with metal will make you bleed, its gonna happen. Be careful, its one thing to get small cuts from metal (which you will) its another to have a penetrating eye wound from flying disintegrating zip cut discs. Where full face shield masks, ear protection and watch where your body is in relation to killer tools at all times!
Finally, if you do build this, be ready for the "Big bang theory jokes" I would put an actual video of the episode below, but... the powers that be at youtube would frown on that. So... just copy and past the following!
http://www.youtube.com/watch?v=L6Us9jIPwMI
Have a look, and please remember to VOTE and take the time to rate me. Thanks and enjoy!
Here is the hand running on a test motor, a 12 volt automotive motor. This would be much too fast and loud for a permanent display, but still its awesome!
Here it is finished, much slower but I love the articulation.
Step 1: Supplies and Tools
I used:
- 1" aluminum rod, about 1 foot
- 3/4" aluminum rod, about 3 feet
- 1 1/2" x 1/2" steel bar, about 4 feet
- 1/8" steel plate, about 3-4 square feet
- 2" heavy duty washers, 6
- Thin air craft cable, about 4 feet
- 1/4" steel rod, about 3 feet
- 110v barbecue rotisserie motor
- small 3.5v dc wall=wart power supply
- Automotive LED detail light
- 3/8 bolts, connecting nut, washers & acorn nut
- Various small screws, cotter pins, small nails and wire tie down nails
- Silicone tubing, black, about 3 feet
- 110v rated switch
- Shrink tubing or electrical tape
- Patience, about 9 metric tons
Tools used:
- 110v wirefeed welder
- Dremel tool and various bits
- Angle grinder with zip-cuts, grinder wheels and flap discs for aluminum and different ones for steel
- Hammer
- Chisel
- Wire stripper
- Rock tumbler, with grits, bb's and turtle wax
- Drill and a variety of size drill bits
- Tabletop clamp
- Variety of small hand tools, clamps vise-grips etc...
- lots of safety gear, glasses, flame resistant clothing, thick leather gloves, full face shield and ear protection.
- A fire extinguisher isn't a bad idea as well. Not that I needed it, but...
- Band saw
- Drill press - oh please Santa!
- http://www.sears.com/shc/s/p_10153_12605_00922900000P
- Bench grinder
Step 2: Fingers and a Thumb
- Follow the pictures along and you will get the basic idea. Fingers were made with 3/4" aluminum rod, and the thumb was made with 1" rod. Finger tips need a section on which you will attach your ligaments, its the piece that kinda looks like a nail. It is cut out with dremel cutting discs or if you are feeling adventurous, full size aluminum zip cuts.
- Shaping is done by shaving off sections one at a time with cutting discs, then shaped with a drum sander. Rough bits that rotary tools can't get at are chiseled out.
- Joints are achieved by making finger joints in the aluminum rod, one end gets a notch, while the other end gets the sides shaved down to fit the next notched joint.
- 2 joints are fit together and clamped in a table top vise and drilled through to accept a hinge pin.
- The joints will need to be taken apart many times and trimmed so that they move very freely, a little side play is fine.
- Temporary pins are inserted, nails work fine. They will be welded at the end as putting this together requires some stages to be taken apart a bit.
Step 3: Palm
- The palm was rather simple, lay the fingers down on paper, and trace out the palm.
- Then lay pieces of metal over the life sized drawing and cut to fit.
- Hold them in place with magnets and start welding
- grind the edges smooth and its good to go!
- also took this time to bore out the holes in the bottom for the cable guides.
Step 4: Rough Tunning
- At this point I layed it all out to see how I was going to trim the fingers to match the posts on the palm.
- I notched the fingers, and drilled hinge pin holes for them.
- Used some nails as temporary hinge pins
- Inserted some tubing into the guide holes for the fit.
- Trimmed the fingers some more, and notched the front of posts, to clear the arc of the finger sweep.
Step 5: Tendons
- Welded on some tips, resulted in weak cables, snapped with a little tug
- Went with crimping on brass terminals, worked awesome.
- Drilled a hole in the tips of each finger to accept the brass tip, but not all the way through as to have it slip out all the way.
Step 6: Ligaments
- Posts were welded on to the back of the palm at each finger.
- Silicone tubing was stretched onto the posts and finger tips, you have to play with the length. Too short and the motor will have to work to hard, too long and you will have floppy fingers.
- Problem with using round silicone hose is that it tends to roll as its stretched. So I drilled 2 holes on the back each finger and inserted a trimmed wire nail hoop thing... sorry not sure of the real name. Hammered in with a dab of epoxy, they seem pretty strong.
Step 7: Tumbler
- Ah yes, almost forgot this step. Polish those aluminum fingers with a rock tumbler
- Toss them all into your tumbler with 200 grit for 12 hours, then 500 grit for 12 hours and they come out looking like they have been sand blasted. All the edges are smooth, but dark gray.
- Here is the tricky part, wash them off and add 500 bb's along with a tablespoon or two of car wax.
- Turn it on and walk away for a week
- Wash them off, and look at the glory that beholds you. They have that touch a million times look. And, when they brush against each other in your hand they almost make a singing vibration, its quite odd. They even seem harder some how.... Sorry there are no pics, my SD card got messed up at this point.
Step 8: Shenanigans
aw, intermission. The hand at this point sat in our back proch for about 2 weeks, where any yahoo could play with it!
Step 9: Push Rods
- Rods are simple, buck off a piece of 1/4" rod about 4" long.
- grind 1 flat edge on one end, the other end gets 2 flat edges ground
- on the 2 edge side, this is where you weld on the washers
- the other end can have a hole drilled through
Step 10: Arm Bones
Arm bones were simply left over long piece of metal bar that i used on the making of the palm. Cut them to your desired length and weld them to the palm. Just make sure to make it the same width to fit your crank shaft!
Step 11: Crank Shaft
- First Look at the pictures, welding this up did drive me a little batty, but if you have a game plan it goes quite well. Had the whole thing don in 25 minutes. The most important picture is the welding diagram that I did with plane old windows paint. Check it out!
- The fingers movement is determined by how far the cable has to be pulled to make it move the desired distance.
- Go through each finger, and measure the distance pulled. Mine were about an inch, So your washer has to be at least 1 1\2" across.
- I went with over sized 2" washers, its easier and it helps guide the push rods. 4 of them will receive 2 hole and 2 will receive 1 hole. A single piece of rod goes through each hole and welded in place. Then they are stacked, fitting onto its neighbors hole.
- Before this though you slip on your push rod. and weld in place. Build up one layer at a time, the pictures will help.
- The axle ends were 3/8" bolts welded onto fender washers. These were easier to center.
- If you wish, email me a request for more detailed instructions as this is a build unto its own.
Step 12: More Push Rods
These push rods are more or less the same as the others, just a little longer. Hole are drilled on either side, to accept a hinge pin and the air craft cable.
Step 13: Guides
Spent for ever making the guide for the push rods, welding thin stainless tubing is evil. in the end the tolerances were to tight!!!! so found some desk drawer channel steal and tacked them together. This allowed the rods to move smoothly!
Step 14: Motor Coupling
- The coupling is simply a metal rod connector doodad thingy. Yep, awesome when I'm trying to sound technical.
- Just thread it over your 3/8 crank shaft axle, and drill a hole through it all.
- Weld it down tight. The other end is open and will connect to the motor.
Step 15: Base
The base is made of 1/8" plate steel. This is some real thick sheet metal. However your going to build it, just treat it like origami and score before folding. I scored it with a zip-cut in an angle grinder! metal bends much easier this way, doing away with that whole foundry thing!
Remember though, measure twice, cut once!!! Because I did not...
In the following pics, the leds power supply is now in the way of the base, hence the odd perforated metal cover on the side. it works with the whole scheme and all but it was not intentional.
Once you have your basic box built as per the pictures, you can cut your holes for the arm bones and the motor. Drill any holes you may want for lighting, and weld it together.
Step 16: Motor Mount
- My motors receiving end is a square hole. So I took another 3/8 bolt and carved the head into a square. I screwed it on to the hands crank shaft mount and drilled through the two of them and locked it with a cotter pin.
- The motor mount was another piece of plate steel that was bent cut to fit against the motor.
- Holes were drilled to fit the motors mounting holes
- a slot was made so that I could slip in the motor with out rubbing against the motors axle point.
- Then it welded to the base
- finally the motor was slipped in and bolted down.
Step 17: Shiny Lights
- This part was a bit of a cheat, considering my last instructable was an LED interactive light table.
- I used a leftover LED detail light used in automotive. I have seen these at car discount bins for less then 2 dollars for a 4 pack. the beauty of these is that they are all ready fitted with a resistor for 12 volts.
- The LED's just had to be taken apart to get at the good bits, you will see in the pictures
- My motor has a pigtailed electrical plug on it, so I just grabbed a wall-wart type power supply, this one rated at 4.5 volts and wired it on. Dead simple
- Plug it into the motors spare receptacle and the lighting was done.
Step 18: Wire It Up
Something like this does not need to much explanation.
Sever the cord on the motor, leaving 6-8 inches to give you space to work.
Slip the plug end through a hole drilled in the back of the base.
Reconnect on of the wires together and tape
hook the other 2 up to your switch.
Plug into the wall and say aaaaaaaaaaaaaaaah, nice.
Step 19: Final
- When all the stages are done, its time to tie it all together.
- Add washers as spacers between the fingers in prep for the next step
- All of those hinge pins will get loose over time, so weld them together. This is where I was stumped for a bit. The fingers being made out of aluminum i thought would be damaged by the heat, not so!. I simply slipped a steal nail through the hinge hole, and briefly touched the end of the nail with welding tip, and it instantly melts and balls forming a melted rivet of sorts.
- Go through the whole hand and weld any other pins you may have missed
- Wipe off any slag and sand lightly.
- Plug it in and wait for the Big Bang Theory comments to start!

First Prize in the
What Can You Do with a Dremel Tool?
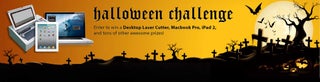
Finalist in the
Halloween Decorations Challenge

Second Prize in the
Kinetic Sculpture Design Contest

Participated in the
Epilog Challenge

Participated in the
Craftsman Tools Contest