Introduction: 3D Printed BATON - 100% 3D Printed - Prints in ONE PRINT - ALREADY ASSEMBLED - SINGLE EXTRUDER - NO SUPPORTS
THIS BATON WILL PRINT IN ONE PRINT, WITH A SINGLE EXTRUDER, AND WITH NO SUPPORTS OR RAFT... MOST PRINTERS WILL BE ABLE TO PRINT IT PRETTY EASILY
Here is a video of me explaining the Baton:
OVERVIEW:
This is a baton that I designed after gaining inspiration from a previous part that I designed for my AWESOME 3D printing enclosure (You can check it out here: LINK TO ENCLOSURE INSTRUCTABLE )....
I came up with the original concept to be used as a slide out support for an acrylic hatch I made on the enclosure ( LINK TO SLIDE'S THINGIVERSE )... After coming up with that sliding concept which I designed in a way that it prints in one print, already assembled, I thought this would make for an awesome Baton / Lightsaber design - so I did that... And it turn out pretty cool...
This shouldn't be a long Instructable, however, I felt I needed to make one for this print due to the fact it is a very complex part and requires some configuration on your printer to get it to print right...
This is a long print... Account for 12-18 hours for printing - depending on how fast you go and your configurations.
Here is a link to the Baton's Thingiverse page where you can find the STL's needed to print it:
Step 1: Step 1: Getting and Setting Up the Print Files
Above are a couple of pictures and two graphical representations of the two parts / prints that come with the baton... First is the baton itself... It prints just like that in one print, already assembled - no supports or rafts - on a single extruder...
The other is of an option backstop / spacer / locking end that you can print with the baton... This part has an outer thread so that it screws directly into the back of the baton... The layers will space out the shafts to give the baton a more aesthetic, tapering look... Lastly, there is a free running screw through the middle that has a hex bolt on the bottom and threaded on top so it can be threaded into the bottom of the middle shaft of the baton, thus locking everything in place... This stops the baton from flying open when you don't want it to...
Step 2: Step 2: Preparing for Printing
As you can see in the pictures above, this is an extremely complicated design with very little margin for error - which is why I made this Instructable - so you can successfully print the baton with little issue...
Here's the thingiverse page again where you can find the STLs: http://www.thingiverse.com/thing:748660
Just for reference, every shaft / shell in the design there is only a 0.5mm spacing between them... Needless to say, this can easily weld itself to the other shells during the print and you'll waste all that time - this step is here to avoid that...
I do not recommend using a dual extruder for this, I did mine on a single extruder... I don't like dual extruders for this print because they tend to be messier and there is a lot more room for error in regard to the other extruder resting with filament in it, eg. bleeding, melting existing filament, stopping between extruder shifts, and needing to use purge walls - which will take a very long time... Do it with a single extruder... If you only have a dual extruding machine - only use one extruder and turn the other off...
First filament.... You can print this in PLA, however, ABS is a stronger filament and will be better overall - but it's ultimately up to you and what you have available... Nylon is the strongest popular filament on the market (in terms of tensile strength). However, nylon has warping issues (worse than ABS) and any warp will ruin the print... I haven't personally tried nylon, however, with the right configuration - it could work (theoretically)... So if you're willing to do that - feel free... Please tell me the result though - I would love to see if it works... PET could also be a good filaments for this, but I haven't tried that either... Stay away from the carbon fiber filament though, you would think it would be strong - however - I tried it, and it failed miserably - it snapped like a stale bread stick within the first whack...
The most important things for this print are speed, infill, shells, and heat... You have to get these 4 things perfect for this to work right...
Speed: You should print this guy kinda slow and allow your printer to make good, controlled movements around the shells... I recommend between 40-60mm/s overall... To be more specific, I recommend, FIRST LAYER - around 20mm/s... OUTLINES - around 30-40mm/s... and INFILL around 40-60mm/s...
Infill: This is really only important for strength... You don't need full 100% infill, you can go for it, but I wouldn't recommend that due to the fact that when filaments cool down, they tend to expand, and if they expand too much - you'll have problems with the shells sticking to each other and the baton not sliding correctly... So I recommend printing with at least 50% infill, but no more that 90%... But 100% infill could work, I just haven't tried it yet due to the fact it will take a very long time, use a lot of filament, and thus be devastating if it fails...
Shells: Print this guy with 2 shells... No more, no less... The infill is high anyway, so number of shells shouldn't matter much...
Heat: This one is important... Whatever filament you decide to use, be sure to print on the low end of its range... For example, PLA is typically 190-230C... Print it around 200-210C... Same concept for ABS and other filaments...
Layer Height: Doesn't really matter... I printed mine at 0.3mm (300 micron)... But you can do yours at any one you want... I recommend at least 0.3mm for the sake of time... But if you want high detail, feel free to print at 0.1mm - It's going to take at least 24 hours though, be prepared for that...
Step 3: Step 3: Trial Run - HIGHLY RECOMMENDED
This step, I want you to do a quick trial run with the filament and printer you intend on using to print the real thing...
Set up your slicer with the recommended settings listed in Step 2...
What you can do for this step though, to save time, is lower the infill to like 20-30%... HOWEVER, keep speed, shells, and temp at the same parameters you intend on printing with as these are the most important factors....
What you need to do now, and I know it's a hard thing to do - but it will be worth it in the end... You need to either cut the model in your slicer or cancel the print right around 35mm high (the two pictures above is what it should look like)... It will be a wasted print and about 2-3 hours, however, it will tell you if the print is going to work for you... The most important and most troublesome parts of the print all happen in the first 35mm... This is where the stoppers, sliders, and everything else are printed and these are the parts with the most detail and least room for error... If, after you stop at around 35mm, all the shells are free and slide out and move around - you're good to go - PRINT THE WHOLE THING... If not, you're going to need to play a little more with your speed, shells, heat and infill and try again until it does work...
If everything is successful in your trial run - go ahead and print the entire thing... It should be an near guarantee to work now.
AS I SAID BEFORE, THIS IS A LONG PRINT AND WILL TAKE AT LEAST 12 HOURS TO PRINT IF PRINTED RIGHT...
Step 4: Step 4: Multi-coloring (optional)
This step is going to explain how to do multi-coloring like the pictures you see above...
I said this in a previous step, but I'm going to say it again because it's important... I do not recommend using a dual extruder for this, I did mine on a single extruder... I don't like dual extruders for this print because they tend to be messier and there is a lot more room for error with the other extruder resting with filament in it... eg. bleeding, melting existing filament, stopping between extruder shifts, and needing to use purge walls - which will take a very long time... Do it with a single extruder... If you only have a dual extruding machine - only use one extruder and turn the other off...
What you need to do is start with one filament for the bottom... Then Z stop the printer at approximately 17-20mm and change the filament to the color you want next... Then at approximately 115-117mm Z stop the printer and change filaments again to whatever you want on the top... Pretty simple, I found this method works best...
I HOPE YOU ENJOYED THIS INSTRUCTABLE AND I HOPE YOU ENJOY THE BATON!!!! THANK YOU!!!!
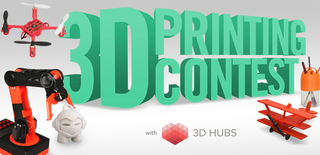
Participated in the
3D Printing Contest