Introduction: All About Coin Rings! Make Your Own!
Since the first time I saw a coin turned into a ring I knew I wanted to try making them too! Here are some example of what I've been able to achieve so far:
Step 1: Some Video Reference
I also made some video about this subject on my YouTube channel:
The first one explain shortly how I used to make coin ring back when I started without any specific tool apart from a ring mandrel.
In the second video I used some other tools like a punch and die set I made in order to get consistent and centered holes in coins (but we'll talk better about that deeper into this instructables)!
Step 2: Entry Level: Essential Tools
Like some other hobbies you don't really need a whole lot of tools to make your first and very own coin ring, sure expensive tools will make your life easier and may ensure higher production, but not much is strictley needed to start!
Absolutely necessary stuff:
- Ring mandrel:
We are going to shape our ring on this cone like tool so it needs to be made of an hard and sturdy material like stainless steel. I bought mine on ebay for less than 20€ but you can also have it made at a local machinist shop or by a friend with a metal lathe! If you want to go the second way I'll leave you here a quick 3D model of my ring mandrel for reference. This shouldn't cost you much as it's a very easy shape to turn.
- Mallet:
To force the ring into his shape we need to use a relatively soft mallet (or hammer however you want to call it). I've tried some different kind of mallet and the one that I like the most is an HDPE plastic mallet I made myself, but also other rubber like mallet works fine. The point is that it has to be softer than the coin's metal you are going to work so that you don't damage your surface. Here is the video where I made my HDPE mallet if you are interested in making it: HDPE Mallet Video - Blow torch:
Needed to anneal the metal when it gets hard
Other common tools:
- Drill/drill press:
To make a hole into the coin. A cheap punch and die set works even better!
- Some kind of center finding tool or jig:
Finding the exact center of the coin is crucial, when I started I made a very simple plexiglass center finder (just a bunch of concentric circle scribed on a thin plexiglass piece) but there are many other way that will give the same result. Just take your time and do your best to find the exact center
- PVC pipe:
To help at the beginning of the folding process. I use one of 25mm outer diameter and 2mm thick wall. - Rotary tool and bits:
To clean, grind and polish. Very handy tool to have :)
Step 3: Entry Level: the Process
Check photos for most steps:
- Find a coin that will look nice as a ring! :')
- Make sure the metal is suitable: heat up the coin to red with a blow torch to see if it melts down and check it with a magnet to see if it's magnetic, many magnetic coin will be too hard to work. Otherwise search the coin name on google and see what's metal the coin is composed, if it's aluminum it will melt down and if it's steel it will be very hard to work. Examples I tried: 100 lire 1990 (stainless steel) and 5 mils 1972 (aluminum).
An easy metal to work is copper. - Find the center of the coin.
- Punch or drill an appropriate hole according to your ring mandrel, mine start at 11.5mm so I make a 12 mm hole.
- Place the coin on top of the mandrel and start folding with the pvc pipe, the face that you want on the outside of the ring must be facing up. You can secure the mandrel in some way to help you in this process.
- Anneal the coin. Annealing means making the metal softer and it's achieved by heating and cooling the metal. Most metals apart from tool steels can be quenched in water to cool off and they won't harden.
- Drive the coin down the mandrel while keeping it perpendicular to the mandrel itself. It will start to feel hard after a while meaning that the metal is getting harder.
- Anneal again.
- Work the coin into a cone shape with the mallet until you reach a point where it doesn't bend much anymore.
- Anneal. You can't anneal too many time! :)
- Put the coin in the mandrel upside down and work the other way closing the cone shape to a cylinder.
- Refine the two sides with sandpaper or with a grinding stone on a bench grinder or on a rotary tool untill the two sides are parallel to eachother. Here many problems can occure if the hole wasn't centered enough as the side might be not paraller and you will need to grind off a lot of material.
- Remove any sharp corners (with sandpaper, rotary tool or deburring tool) and polish the ring up to your liking. To do so I use a fine polishing compound and a cotton buffing weel on the rotary tool, but you can make it look just as shiny by working by hands with metal polishing product on a rag.
Step 4: Intermediate: More Tools
Here I'll list and explain more tools for the coin ring maker. The order goes for what I think it makes the best difference for the price:
- Self centering
punch and die set
:This simple tool made a tremendous improvement in the quality of my rings. Once folded there is no need to flatten the sides of the ring anymore therefore the eventual reeded edge of the coin can be preserved. Moreover is much quicker than drilling and overhall has halved the time it took me to complete a ring. This is the punch and die I made myself on my metal lathe, it's a pretty easy project that any machinist can make quickly. You can ask a local machinist to make one of these, it can't cost much! I include a 3d model made in fusion360 for measurements and a link here to the video where I make it: DIY Punch And Die Set
- Doming block:
Another inexpensive tool I bough on ebay for 20€. with this one you can achieve two "important" goals:
1) Take off the slight cone shape your ring will have out of the ring mandrel for a perfect straight look
2) Shape the ring to a "fat tire" look by pressing the ring into the doming block further down.
This tool can also be used to make the initial fold on the coin by pressing it into the doming block with a ball bearing sphere.
The only problem with the doming block is that another tool is almost absolutlety need to use it proprely: an arbor press. - Arbor press:
Awesome and versatile tool, I got mine used near by where I live for 30€. It wasn't in perfect shape but I love to restore old tools so I went ahead and did a full restoration transofming it into the tool that I now love :) I went as far as making a new HDPE handle for it, similar as I made my mallet, here is a link to that video if you are interested! Arbor Press Handle HDPE
Step 5: Pro Level Tools: Stuff That I Don't Even Own
Next up some expensive gear:
- Ring stretcher:
Considered by many a must it's as expensive as useful. Quality one can cost up to 400€ but it's a good investment if you want to mass produce and sell your creations. This will speed up your process by a lot since you don't need to hammer down your ring into a coin anymore. After the initial fold you can place the coin into the stretcher and voilà you a have a ring (more or less). Also most of stretcher have a built in reducer that can be used as a doming block plus arbor press combo.
- Proper press:
Air or jack press that will output much greater force than an arbor press. Punching holes will be easy with one of these!
Reduction dies - swedish wrap:
With these set you can jump into newer techniques of coin ring making, allowing you to produce very tall flat sided rings and to reduce huge coins into wearable rings. All this will come very pricy but again a good machinist can make set like this if you happend to know one :) I won't write much about these since I never tried them. Down a pic of how they work.
- Powder coating:
Another new trend, the design of the coin is accentuated by coloring the low portion of the coin. This process consist in powder coating all the finished ring and then cleaning up and polishing the high spots creating an high contrast effect in the finished item.
Step 6: Conclusion
I always have a ton of fun making this rings! <3 The last photos will be a comparsion between a couple of my first coin against more recent ones. As now I have made 20-25 rings so I would say the learning curve isn't too bad!
I hope you enjoyed this instructables and found something interesting!
See you on the next one :)
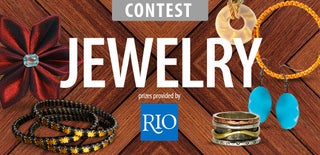
First Prize in the
Jewelry Contest 2017