Introduction: Blade of Woe // Skyrim
My absolute favorite Skyrim quest to play is the Dark Brotherhood. There's no better family than a group of cut throat assassins, AM I RIGHT? (awkward silence from my disappointed parents).
Anyways, everything about the Dark Brotherhood I love unconditionally (minus SPOILERS that betrayal part). After you complete this quest line you get a sweet dagger. Now I, being the geek that I am, decided that for Metacon, I would be an assassin from the Dark Brotherhood, so obviously I would need this legendary blade, to compliment my shroud.
This build took way more time than I expected it to (I went to great lengths to make sure I made everything as perfect as I could), a little over a month I believe. It would have only cost about $10 to make, but I decided to make castings out of resin which pretty much broke the bank. I, however do not regret this. It adds a nice weight to the blade (the original weighed about 3 ounces, while the castings weigh about 11 to 12 ounces) making it feel like a real blade, and it's more durable, so I can't break it too easily. I'm not gonna lie, I'm super pleased with how it came out, and the extra time and money was definitely worth it.
Step 1: Materials
- Paper
- Cereal box (or a thin cardboard)
- Expanding foam
- Spackling Paste or wood filler (I used about 8 ounces)
- Sandpaper (100, 180,220 grit)
- Wood glue
- Apoxie sculpt (or a clay like material)
- Rubber gloves (I used a ridiculous amount to keep almost every material I used off my hands)
- Epoxy glue / super glue / rubber cement
- Resporator Mask
- Marker
For mold making:
- foam core
- silicone
- resin ( I got mine here )
- clay
- hot glue
- matte clear spray paint
- nitrile gloves
Painting
- Acrylic paint ( black, silver, white, burnt umber )
- Brushes
- Silver Rub and Buff
- Leather for wrapping. I got mine from this shop
- Matte clear spray paint
- 2 part epoxy ( I used 6 minute )
I decided to make a mold of mine.
Step 2: Source Material / Other Tutorials
I know before I start a project, I do the most research I can. Obviously before I decided to attempt this I did some research. I have some source pictures above and if you wish to look at other ways people made the blade check out some of these beautiful tutorials :)
http://daniel-abreu.deviantart.com/art/WIP-Blade-o...
http://daniel-abreu.deviantart.com/art/WIP-Blade-o...
Step 3: Pattern
First I printed off a picture of the Blade in the size that I wanted. Tip to tale it was about 18 inches long. I taped it to a cereal box and cut out two copies. My cereal box was not long enough to encompass my Blade, so I cut it out in two parts and glued them together adding a few cardboard supports to stabilize.
I did not glue my two cardboard blades together. It was easier to sand in the later steps when I had one sided pieces.
Step 4: Foam
I used the same technique I used on my Loki helmet. First I covered my card board in expanding foam. Then I cut away the parts of the foam I didn't need. I wanted my blade to be quite slender, so I cut away almost all of the foam with a serrated knife.
I cut out the outline first following the cardboard outline. I then trimmed the thickness of the blade down to about a half an inch (per blade).
I was a bit disappointed because the foam had air pockets in all the places I didn't want. I took out my spackling paste and filled in the whole thing. I put a very generous amount on it.
Step 5: Sanding. Oh the Sanding
I sanded the blades with 100 grit sandpaper. The great thing about spackling paste is that is easily sand able, lightweight, yet quite sturdy. Also if you get frustrated from all the sanding and punch a wall. You got a big jug of paste you can fix the wall with.
After the first round of sanding, I made sure that the spackling paste didn't over flow on the sides of the cardboard (see pic 4). I trimmed away all the excess. I also cut away pieces from the blade, and sculpted into a more blade shape.
Then I put another layer of spackling paste on the blade, and sanded that down. It is very important to sand the edges of the blade really well, so when you attach them together the blade is sharp and pointy. I also made sure to wear a respirator mask, so I didn't inhale the dust.
Sanding sucks, but the more time you put in during the process, the more beautiful it will be. This step is very important to make you're blade look authentic, and if you cut corners in the beginning, you end up correcting them later on. Something that would have took 5 minutes to fix, ends up taking an hour (or more) to fix in the long run.
Step 6: Gluing the Sides Together
First scored the cardboard, then I coated both sides in contact cement. It didn't stick together that well. Maybe it was because the cement was old, it was 25 degrees outside (rather warm for a MN winter lol), or my inexperience, but I ended up using epoxy to keep the sides together.
My two blades with slightly bowed so when I glued them together some of the spackling paste began to crack. I filled those parts in later on with more spackling paste and a few coats of wood glue.
Usually I would have used hot glue, but hot glue is bulky and would have made the seam more apparent. Super glue probably would have worked the best, but I couldn't find any, so I used what I had.
I trimmed the excess on the blade off. Then I covered the seam in spackling paste, sanded that down. Next I coated it in watered down wood glue (1 to 1 ratio).I prefer wood glue to Elmer's glue because it's less water soluble and sandable. Mod Podge is also a good alternative, but it's not sandable either, and one time when I used it, a bunch of bubbles appeared on my prop a day later, so I kept my distance and used wood glue. However the wood glue I used was not water proof, so I actually ended up coating the whole thing in resin and sanding that down, later on.
I was really happy with how it looked at this point. The thing I've learned about making costumes is that even if things look like they won't turn out, with a little elbow grease that will. So don't worry!
Step 7: Details
This was the part that really took a long time (other than sanding of course). I used apoxie sculpt to first build up the handle on one side of the blade. To get it smooth(ish), I wet my fingers and rubbed them over the details. Then I let it cure for 24 hours. The great thing about apoxie sculpt is that it doesn't shrink or crack, and it's sandable. However it can be difficult to work with, so I did all the sculpting little by little. After 24 hours I did the other side of the handle let that cure, and then sanded the crap out it.
Next I went on to do some finer detail. To make the design I rolled out the sculpt into very thin rolls and then put it where I wanted it. This was quite a frustrating process because it wouldn't always stick to blade. I had previously debated using paper clay for this part, but paper clay, while it sticks really nicely to wood glue, it doesn't blend back into itself that easily (maybe it was the brand I'd used in the past idk), so it would have been hard to smooth it onto the blade.
To make the details precise I used some tools I ordered online. You could probably use a tooth pick or something to define edges and that would work just as well. This was my first time sculpting such tiny details with apoxie sculpt and man, was it difficult. If you guys have any tips on working with this stuff that you'd like to share, please comment or message me.
Step 8: Details (part 2)
To get the details to look the same on both sides of the blade. I coated the details in blue washable marker, then I quickly rubbed a piece of paper over the raised details. This gave me a mirror of features. Next I took an exacto knife and cut the lines. I made sure to do it dashes so the paper didn't fall apart. Then I took a pencil, lined the paper up, and traced through the thin lines I had cut.
I rolled out the apoxie sculpt and put the sculpt over the lines I had just drawn. Because symmetry is hard. I ended up with a 'sisters not twins' scenario on the details.
I also built up some of the edges and then sanded them down so they looked sharper. I sculpted the rib things on the blade then copied it to the other side.
I realized that the wood glue I had coated the blade in was not water proof (neither was the spackling paste). I didn't know if that would be a problem with the silicone, so I made a split decision and coated it in resin. This added another day to my project, but I'm quite glad I did it. For one it strengthened the blade, but it also made it water proof. It took awhile to sand down, and reaffirm the details. If you do this method, I would suggest coating your blade in resin, then doing the detail work.
I cannot stress enough how important it is to detail the blade slowly. I did one half of the hilt details, waited 24 hours than did the other side, waited 24 hours built up the edges sanded them down., added the lines on the blade to one side, waited 24 hours, did the lines on the other side. It took a long time, but it allowed me to slowly build up the features of the blade without ruining other details I made. It took about 6 days to do all the details.
Step 9: Beginning of the Mold
I decided to make a two part mold of my blade, so I had a sturdy copy that lasted a long time. I drew an outline on newspaper around my blade, then cut it out of foam core. I took clay and flattened it out along my blade. I smoothed the clay out, and made sure everything was level. To get the excess clay off of the dagger, I used a ridiculous amount of wet q tips, and swatched them over the dagger.
Next I cut off the excess clay with a butter knife then cut out strips of foam core. Since I wanted to save silicone, the shape of the mold was a little weird, and I had to measure out the individual pieces for the wall. I hot glued them in place, then went over the edges with hot glue to seal it in, so the silicone wouldn't drip out. I pushed the clay to edges of the foam core, and made sure everything was sealed and secure.
To make some recognition points, I took the end of a paintbrush dipped in water and made little holes around the blade, except at the butt of the blade (I later cut a pore spout here).
Step 10: Pouring the Mold
To make this mold I used three Oomoo 30 silicone sets in total (1.5 sets per side). I sprayed my blade in matte clear spray paint as a release. This was not really useful in this step, because the only thing silicone sticks to is silicone, but I wanted to be safe. I mixed 1.5 sets of silicone with a paint stir stick for about a minute, then I slowly poured it over the blade.
I read somewhere that pouring it slowly helps keep air bubbles out of the mold, so be careful with this step it will help you later on.
When the silicone had cured, I broke the foam core off of the mold, and flipped the mold over. I took all the clay out of the mold and sponged off the residue.
You're not supposed to take the object you're casting out of the mold at this point, but my silicone was not actually flat. It was slanted in a weird way which dislodged the tip of my blade ( I later realized my blade curved to one side, that's why this happened), and I couldn't fix the mold without recasting, so I paid for that later by having to sand down my cast blades more.
Step 11: More Mold Making
I actually reused the foam core I had used previously for the mold wall. I simply just glued the wall back together, sprayed it with matte clear spray paint (as a mold release) before pouring the rest of my silicon in slowly (1.5 kits of silicone, roughly a quart and a half, I believe). After it had cured I carefully pulled the two sides apart.
I wiped down the clay bits I had missed, and removed my blade from the mold. At the butt of the handle where I didn't put recognition points, I cut a crude hole (my exacto knife was dull).
Step 12: Casting
First I cut out two foam core boards (actually 4, check out the note on the photo). I wrapped rubber bands around the mold. This keeps the mold secure and tightly pressed together, without disrupting the mold. If you put the rubber bands over the silicone without foam core, it would pinch the mold.
I decided to pour my resin in batches. I wore nitrile gloves. After mixing together the two parts of the resin, I poured it into the hole I had made at the butt of the handle. This filled my mold about 1/3 of the way. I swirled my mold around to make sure I got resin every where ( I think it also releases air bubbles ). Then I mixed another batch of resin (I didn't wait for it to cure) poured that in, swirled, and repeated the process until the resin was filled to the top of the mold.
I waited for all of it to cure (my resin only took about 20 minutes to fully cure), Then I took off the rubber bands and the foam core. I carefully separated the silicone. I should note I did not use a release. I did not have one on hand, but I heard that it lengthens the life of a mold, so I'll be investing in one soon.
Also a worthy note to add: My resin cured with an exothermic reaction (it released heat). I learned later on that you want the casting to cool down before you remove the casting. If it's still hot, it sometimes take pieces of the silicone with in when you remove it from the mold. This obviously damages the mold, so learn from my mistakes.
I had a little over flow which I trimmed away. Some of the resin did not fill out certain parts of my mold (see notes on pic), but this was the first casting, so I wasn't worried. I used apoxie sculpt to fill in these parts because I didn't want to trash the casting, but I also wanted it to look complete.
I apologize for not having more pictures on this part. I didn't want to get resin on my camera.
Step 13: You Thought There Would Be No More Sanding
I sanded everything with 100 grid sand paper. To see the imperfections I fixed, check out the notes on the pics above.
Step 14: Painting and Leather Wrapping
To paint this blade, I started out with a wash of silver and white and a little blue to make a base color. I let it dry on a drawer thing that I kept my paint brushes in. I then coated the whole thing in silver paint.
My favorite part of any project is the weathering. Weathering really brings a whole piece together, makes it look realistic, and hides some of the flaws you might have made. Humans like to make patterns when detailing, but the earth's natural wear and tear, rarely does so. To make the blade look realistic, I scuffed a wash of black paint over places where grim would naturally appear, and wiped it away with a napkin. This leaves the raised details shiny, and the indented bits, dirty. I also went over it with a wash of burnt umber. They I lightly brushed the raised details with silver Rub and Buff.
I sealed it with a clear matte spray paint.
I bought some 2 oz leather on Ebay, and cut that into 1 cm strips. I used 2 part Epoxy to attach one end of the leather to the handle, then I just wrapped it up, and used Epoxy to glue the end of the leather to the handle.
Step 15: Sweet Mother, Sweet Mother...
It's funny how a build that was supposed to take only a week or two, ended up consuming my whole February and half of March. Even though my blade did not come out perfect, I was ridiculously proud of making my first silicone mold, and trying new techniques in prop making in always good to broaden the horizons.
If you have any ideas for what I should build next, or have any questions about this build, feel free to contact me via the comments or a direct message.
For other Skyrim builds see how I made the Wabbajack, Glass Helmet, and Helm of Yngol.
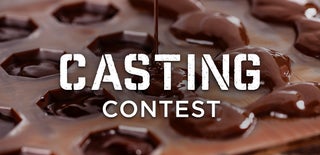
First Prize in the
Casting Contest