Introduction: Build a Warped Box!
Do you have a problem misplacing your miscellaneous items? Car keys, wallet, watches, or loved ones?
Well I have a solution for you...make a Warped Box! No it isn't a Tardis, no you can't pull a lamp or coat rack out of it, and no it is not actually warped. However, it is a stunning box that will catch your eye and remind you that your keys are in it!
This Instructable will guide you through my journey making this box in my high school wood shop class. You can follow along and make one for yourself, or sit back and enjoy the process of making this unique checkerboard pattern.
Step 1: Materials and Tools
Materials (rough cut sizes):
- 3/4" x 7" x 26" mahogany (sides of box)
- 3/4" x 7" x 26" oak (sides of box)
- 1/2" x 1" x 2" mahogany (handle)
- 3/8" x 1/2" x 25" oak (top frame)
- 1/8" x 6" x 10" plywood (bottom and splines)
Tools that I used:
As always, use wear safety goggles and use safety precautions when working with machinery.
- Table saw
- Miter saw
- Band saw
- Surface planer
- Hand sander
- Tri square
- Double sided tape
- Scroll saw
- Router table
- Belt sander
- Drum sander
- Bar clamps
- Pipe clamps
- Strap clamps
These are tools that I used, but if you don't have access to all of them don't be discouraged. Some of these tools such as the drum sander were just for convenience and could easily be substituted with a file or sandpaper. The following are the barebones necessities for this project:
- Table saw or circular saw
- Bandsaw or scroll saw
- Surface planer or portable belt sander or hand plane or router sled
- Bar clamps or pipe clamps
As you can see, this list is pretty short and lenient. You'll notice each bullet point lists several machines that can perform similar tasks. You'll need something that can: cut angles, rip, or crosscut; cut curves; plane a face; and apply pressure. Even if you have limited tools, try giving this project a shot! What's the worst that might happen? A warped box?!
Step 2: Brainstorm and Design
The Back Story
For my high school wood shop course, I was tasked with making a small wooden box. I wanted my box to be something unique. I considered making one with a built in wooden combination lock door or one that had an organic shape to it or one with a secret compartment.
However, I stumbled upon Peter Brown's Drunken Cutting Board and all those other ideas were left on the back burner. He designed a cutting board with a checkerboard pattern but cut each line with a different curve (see thumbnail above). This gave the surface an optical illusion look where part of the board was bulging out or twisted. I figured I could take the "drunken" checkerboard pattern and form the sides of my box with that. To take it a step further, I wanted the wavy pattern to flow seamlessly across all four sides of the box so that no "square" would be adjacent to another "square" of the same color. This would be achieved using 45° case miter joints and some careful planning.
I decided to make my box 6" x 6" x 6" because that's a nice number to use. That size also gave me room for a 4x4 checkerboard pattern which was plenty of pattern to play around with.
I'll explain making parts of the pattern and box in more detail, but here is a basic overview so you get the gist of it: (The following list #'s do not match up exactly with the steps in this Instructables but they both are the same chronologically)
- Start with two contrasting color boards of the same dimensions and stack them on top of each other using double sided tape.
- Mark the curves flowing lengthwise along the top board with a template.
- Use a bandsaw to cut the curves through both boards.
- Now you should have strips of both boards and each strip should have an identical pair of the opposite color.
- Reassemble the boards but switch every other strip with the identical pair of the other color. Doing so will create a striped wavy pattern so every dark wave of wood is adjacent to a light strip of wood and visa versa..
- Glue and clamp the strips together in this new configuration to form the boards, letting it dry 24 hours.
- Smooth the boards on the surface planer.
- Stack and double sided tape the boards together again, making sure they are in the same orientation so that the waves of the top board match with the waves on the bottom board.
- Now repeat the process of cutting the curves on the bandsaw.
- Again reassemble the boards and swapping every other piece with its twin. This should form the "warped" checkerboard patterned boards which we desire.
- Now that we have two patterned boards, we will cut two sides from each board, and a top from one the remaining.
- Using 45° miter joints and splines we will assemble the sides.
- Then comes decorative trim along the top of the box and a nifty handle.
- Finally sand and finish with oil and polyurethane.
(If this didn't make sense for you, check out Peter Brown's Drunken Cutting Board video from 0:45-1:24 minutes.)
Step 3: Creating the Templates
Although the wavy pattern could be cut free hand on the bandsaw, such as with the drunken cutting board that was not ideal for this project. The contrasting color "squares" on the edges of the sides need to be at a set interval so that each wave will flow seamlessly to the next side until it reached all the way around the box.
Thus, I used a template to ensure the waves were the same distance apart every 6 1/4" (the width of my box is 6" but the 1/4" takes into account the kerf of the bandsaw and table saw). For my template, I printed out sine and cosine waves with different amplitudes and periods from Desmos, a graphing utility, for a variety of different templates. You can print out the image of the graph above on regular 8 1/2" x 11" paper to give you the same templates that I used.
I also made a full scale drawing of three sides and experimented with the different templates until I found a pattern that I liked. I cut this pattern out and used it as a reference when I marked the pattern on the board in the next step.
Some of you might be wondering why I'm going through all this effort to make the waves flow around the corners if I'm just using 45° miters and the pattern would flow anyways since I'm cutting from a continuous board. It is entirely possible to go the route of not planning check points to space the curves, instead, you could free hand the curves. It would give the box an even crazier look, but some planning is still involved if all four sides were to line up. It's up to you whether or not you want to stick with the tried and true or you want to warp off into your own dimension.
Step 4: Cutting the Horizontal Waves
Okay! We're finally at the fun part: cutting the pattern. First, you're going to want to make sure your mahogany and oak boards are exact same length and width. Then use four strips of double sided tape placed parallel to the width of the board to sandwich the mahogany and oak boards together.
Now we want to mark the check points the waves will pass through every 6". Pick one end of the board and mark the end grain so you can identify it later. Starting 1/8" from the end of the board, mark lines perpendicular to the length of the board every 6 1/4" (the extra 1/4" takes account for the band saw and table saw kerf). Then, 1/4" from the bottom edge, divide the vertical lines into 1 1/2" segments. This will give you even spacing between curves.
Now, use the templates to create three waves parallel with the length of the board. Be sure the waves pass through the points you just marked.
Once you are satisfied with the design, trace along the waves, cutting through both boards simultaneously with a band saw on top of the template lines. Keep the cut as smooth as possible since we will not sand the curves. If possible, use a fine band saw blade with a thin kerf.
Now you should have strips of both boards and each strip should have an identical pair of the opposite color.
Next, remove the double sided tape and reassemble the two boards. Alternate every other strip with its pair of the other color. Now you should two boards with a striped wavy pattern as shown in the picture above.
Glue each patterned board together. Use at least 3 bar clamps for each board. Make sure the curves fit together snuggly and that there are no gaps. Wipe off excess glue and set to dry 24 hours.
Step 5: Cutting the Vertical Waves
After drying, remove the clamps and surface plane both sides of the boards down until they are flat (Do not plan them down to 1/2" yet).
Now we are about to repeat the process of cutting the waves, but this time running vertically. Start by using double sided tape parallel to the length of the boards, to sandwich the boards together. Make sure the boards are stacked in exactly the same orientation. (If you were to see through the top board, the pattern would match the bottom board)
Before using the band saw, remove 1/8" from the ends of the board on a miter saw to square the boards. Again, draw lines across the board every 6 1/4" (these should be where lines ran before you planed them)
Between those lines, evenly space 3 vertical waves about every 1 1/2" using the templates.
Just like for the horizontal waves, cut them out on the band saw. NOTICE: Do not cut along the straight 6" line markers. This is where we will separate the sides later on the table saw.
Repeat the process of alternating the waves and glue them up again.
Step 6: Cutting the Sides and Miter Joint
After letting the glue set 24 hours, plane the boards down to 1/2".
Then rip the boards 6" wide on the table saw by removing 1/4" from the thinner wave on one side and 3/4" from the thicker wave on the other edge.
Cut the boards into 6" lengths along the lines that you previously used as check points. Since these lines were long planed away, use a ruler to find where the spacing between the waves is 1 1/2" and ah-ha! You found the line.
You should have 8 pieces total and select the 4 that make the best horizontal continuous wave pattern.
Mark the 4 you have selected so you can identify the orientation they go together by labeling their edges A,B,C, and D.
Now angle the table saw blade to 45° to the left and using the fence as a guide, cut the miters on the end grain of the 4 sides. Be sure to keep the sides 6" long, only angling the side, not shortening it.
Once all four sides are done, cut an 1/8" wide spline, 3/16" deep, down the length of each 45° miter. In order to get the spline perpendicular to the miter, simply angle the table saw blade 45° to the right and use the fence asa guide. Use a scrap piece to test the blade height and distance from the fence.
Then, cut four 3/8" x 6" splines from 1/8" plywood on the table saw.
Test fit the box together making sure the splines and groove fit together easily.
Step 7: Cutting the Groove and Bottom
Step 8: Making the Top
For the top, cut a leftover piece of the warped pattern to a 4 15/16" square so it is just large enough to fit inside the box.
Then, cut a 1/8" deep groove along the perimeter 1/8" from the edge of the top piece with the table saw using a 1/8" blade.
For the decorative frame of the lid, use 3/8" x 3/8" x 25" oak and cut a 1/8" deep groove along the center of a side of the oak.
Cut the oak with 45° miters so that it forms a trapezoid shape with the groove running along the shorter side. The short side of the trapezoid should be 4 15/16" long.
Cut four 45° mitered 1/4" wide spines from the 1/8" plywood to fit in the grooves of the patterned piece and oak frame.
Dry fit the top, splines, and oak and glue together.
After dry, add four 6" long 1/8" decorative mahogany strips along the edge of the oak frame by using 45° miters.
Step 9: Sanding
At this point, the box is almost done. All we are missing is the handle and a nice coat of oil.
Sand all surfaces with 150 grit and then 220 grit sand paper. Sand with the grain when ever possible.
Step 10: Making the Handle
The handle is based off the outline of the greek symbol pi which is a reappearing theme in this box (as already seen with the sine and cosine waves).
Use a router table with 1/2" round over bit to cut a groove along both sides of the 1/2" x 1" strip of mahogany.
From this, cut a nice looking wave/pi shape on the scroll saw.
Use a drum sander, spindle sander, and files to get a more rounded shape.
Glue the handle to the center of the top of the box using super glue and tape it down to secure it.
Step 11: Applying Finish
Clean the box of as much dust as possible. For this step, work in a well ventilated and particle free area. Wear gloves and don't breathe in the fumes.
Apply the oil of your choice with a clean rag. I used boiled linseed oil. Allow the oil to soak into the wood for a few minutes before wiping off excess oil and setting it to dry for 24 hours.
To protect the box, I used 2 coats of wipe on polyurethane sanding with 500 grit sandpaper in between coats (letting each coat dry for 24 hours first).
Finally, I used touch-up wax filler sticks to fill in any gaps in the spline joints visible from the top and buffed it with a rag.
Step 12: Congrats You Made It!
Thanks for sticking with me to the final step! I hope you enjoyed this instructable and are inspired to try it for yourself. If you make one, post a picture in the comments, I'd love to see it.
Please tell me what you think of it or if you have any questions in the comments!
This is my first instructable, and I had a lot of fun putting this together. I look forward to making many more!
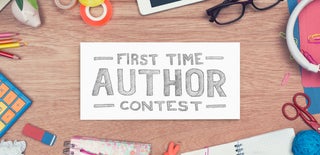
Second Prize in the
First Time Author Contest 2018
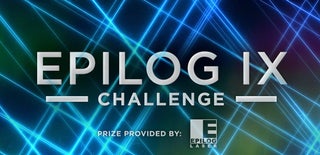
Participated in the
Epilog Challenge 9