Introduction: Mid-Century Modern Lounge Chair
This project was also part of my school wood working class. I wanted a furniture project that would really mean something to me. Hmmm...what could be more meaningful than a chair that I sit in 24/7?! What about a chair with a really cool design? So I began to look for some inspirational chair designs, and I stumbled across Shaun Boyd's Mid-Century Modern Lounge Chair. It was a stunning piece, as are all the projects on his channel. I knew this was the project for me, but since there were no available plans, I made my own. (Update: Shaun now has plans available on his website).
In this Instructable, I'll take you through my build process start to finish!
I hope you enjoy!
Step 1: Materials and Tools
Materials
- 5/4" x 7 1/4" x 8' oak
- 3/4" x 7 1/4" x 12' oak
- 19" x 21" Seat Cushion
- Pillow (I bought mine from Costco)
- Wood Screws
Dowels
Tools
Below is a list of tools that I used. Other tools may be used as a substitute. As always, use proper safety precautions when working with machinery.
- Miter Saw
- Table Saw
- Band Saw
- Spindle Sander
- Hand Sander
- Dowelling Jig
- Plug cutter
- Portable Belt Sander
- Portable Router
- Hand Screw Clamps
- Bar Clamps
- Wood Glue
- Double Sided Tape
- Ruler
Step 2: Designing
Using images from Shaun Boyd's chair, I began making some sketches and full size drawings of how I wanted my chair to look. While I'm sure its not an exact replica, I think I did a pretty good job of capturing the unique style of the chair.
For convenience, I converted my full scale drawings to CAD drawings which can be found as a STEP file below. This is helpful to visualize the chair more. I also added details like dowels, tongue and groove joints, and screws. I tried to make everything as accurate as I could. Also, I made full scale PDF drawings, also available below. Note: these are large documents and need to be printed on a large 44" x 34" paper or collated on several 8.5" x 11" sheets to be full scale. See this guide on how to "tile" documents across multiple sheets of paper.
Step 3: Prototype
(Building a prototype is optional, but it could save you from avoidable mistakes on the actual build!)
The prototype was quick and cheap since I used some cheap 3/4" painted pine and scrap plywood. I also didn't bother constructing the "L" frame and seat stretchers. I constructed the legs using the same process I detailed later in this instructable and used them as templates for the actual legs.
Step 4: Leg Stock
The legs and armrest are made from 5/4" oak. The leg assembly has three parts: the front leg, armrest, and back leg. I was able to get two of each part from a 7 1/4" wide board, so I only used 3 sections of 5/4" board. I cut out the 3 sections from an 8' long board and then traced the leg parts using the prototype legs. I made sure to trace with the straight side of the leg along the edge of the board (this is a reference surface for that miter saw). Then I rough cut all the leg parts on the band saw.
Now, I used double sided tape to stick the pairs of identical parts together. I made all the angled cuts on the miter saw, cutting both pieces at once. This ensured that both sets of legs would be identical.
Step 5: Leg Assembly
On each mitered joint, I marked the position of the dowels, making sure the line met up with the other half of the joint. Then I used a 3/8" drill bit and a doweling jig to drill out the holes for the dowels. I set the depth of each hole to a little more than half the length of the dowel.
I dry fit each joint and once I was sure the holes lined up, I could prepare to glue the leg parts together. I tightened hand screw clamps parallel to the face of each joint. These would act as cleats to give me something to clamp onto when gluing the joint. Next, I spread wood glue on all the faces of the joint and pulled it all together with 4 bar clamps per joint. I wiped away any glue squeeze-out using a wet rag.
Step 6: Final Leg Shape
Once the legs were dry, I used double sided tape to stick both sets of legs together. I used the spindle sander and and hand-held belt sander get the parts to final size. Another method would have been to use a pattern bit on a router to get the legs to get an exact match of the prototype template.
Step 7: Back and Seat
All the seat components are formed from 3/4" x 7 1/4" oak. First, I cut out all the sections of board I would need.
Next, using a dado stack, I formed 1/4" x 1/2" tongues on both sides of the stock that would make the vertical pieces. Then, I ripped three vertical stretchers from each 7 1/4" wide board.
I also ripped the horizontal stretchers on the table saw. Then, I cut grooves in the horizontal stretchers using the dado stack and a feather board.
Once I had checked that the frame fit together, I sanded the sides of all the stretchers with 220 grit sand paper because they would be harder to access later. I also cut ten 1" spacers to get the proper interval on the stretchers.
Next, I glued both the frame for the seat and the frame for the seat back. I used 4 bar clamps per glue-up to apply even pressure on the horizontal pieces.
Once dry, used a 1/4" round over on the portable router to smooth the horizontal stretchers of both frames. Finally, I sanded everything with 150 and 220 grit sand paper.
Step 8: "L" Bracket
Two obtuse "L" shaped brackets would be used to connect the seat to the seat back. These were rough cut on the band saw from the same 3/4" oak boards.
I used the same process as when making the legs: double sided taping them together, cutting the angles on the miter saw, drilling the dowel holes, and glue it together.
After each "L" was dry, I added a 1/4" round over with a portable router and then sanded everything to 220.
Next, I outlined where the seat and back would get screwed into the bracket. I drilled ten pilot holes with a drill bit just smaller than the threads of the wood screw into one bracket. Then I stacked the brackets and transferred the pilot holes to the other bracket.
Step 9: Seat Assembly
The seat assembly is a two person job since there are many parts to line up. The seat assembly was glued up without screws. The screws would be added later to give structural support.
First, I glued both frames to one L bracket and let it dry for about 10 minutes. Then I clamped the second L bracket on and let the whole assembly dry 24 hours.
Next, I extended the pilot holes into the seat frame (the length of the screw) to prevent the oak from cracking. Also, I used a counter sink so the screw heads sit about an 1/8" below the surface of the "L" bracket. After screwing in all the wood screws, I plugged and glued all the screw holes with oak plugs and sanded them flush. I made sure to orient the grain of the plugs parallel to the grain of the surrounding wood. Some of the grain on the plugs matched the wood so well that it was hard to tell there was even a plug there.
Step 10: Chair Assembly
Before attaching the legs, I rounded over all the sharp edges on the router and then sanded with 220.
Then I glued one chair leg to the seat assembly, making sure that the legs were attached at the correct position and angle. After about 10 minutes I glued on the second leg and made sure it was in the same position as the first.
While the glue was drying, I glued some small wood rectangles into the grooves of the horizontal stretchers of the seat. These hid the groove completely and will prevent any dust from collecting in the groove.
After 24 hours, I drilled pilot holes, countersunk, and screwed in some 2" deck nails where the legs were glued to the seat assembly. The screws penetrated all the way into the seat frame. This helps prevent sheer forces weakening the glue joint. I also hid these screws with matching oak plugs.
Step 11: Finishing
To prepare the chair for finishing, I sanded any imperfections and wiped all the dust off with a rag.
Then I applied a coat of boiled linseed oil and wiped away any excess.
After letting the oil soak in for 24 hours, I put on a coat of polyurethane and sanded with 500 grit sand paper.
Step 12: Woodburning
For a final touch, I wood burned my name into the back of the chair with a fine tipped wood burner. This now makes the chair an official family heirloom!
Step 13: Add Cushions
Lastly, add cushions, sit back, and relax!
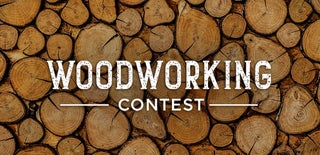
First Prize in the
Woodworking Contest