Introduction: Building a Yew Coffee Table
I decided that I was going to build a coffee table as I have been doing a bit of woodwork for the past year, mainly jewelry boxes and some basic shelves, and thought this would be a good project to further my skills. I had originally envisaged the table being made from waney edge pippy oak, as I had made a couple of shelves out of this wood, but having looked on the internet to price my project up I noticed a page called selected woods.....there I saw some lovely yew boards which would be great to make an unusual piece out of. I had not come across yew before so looked around on the internet for ideas for my coffee table as the boards came with waney (natural) edges and had quite a few splits and cracks. It looked like the best way to deal with the cracks would be to fill the bigger ones with resin or something similar just to stabalise the large top. I decided to make the four legs out of one board and use the other board for two bottom shelves. To join the legs to the table top I will be using mortise and tenon joints and attach the bottom shelves to the legs with pegged through tenons. Hopefully this will give enough lateral stability to resist racking forces and create a not very wobbly table.
Materials
For the table top I used a 940mm x 400mm x 50mm single piece of yew
For the legs I used a single 200mm x 1680mm x 27mm board cut into four
For the lower shelves I used a single 150mm x 2080mm x 25mm board cut in to two.
Wood glue
Epoxy resin to fill the cracks
Tools
Table saw
Router + straight bit
Clamps
Chisels
Hammer
Safety glass
Ear defenders
Step 1: Legs
My first step was to deal with the legs. I took my board I selected for the legs and cut it in to four equal sections on the table saw. As the wood is waney edged you have no straight edge to reference to as you normally would with regular timber boards. I therefore marked the cut positions on the board beforehand and orientated it in line with the saw blade. I do have a crosscut sled with integral clamp slots so this made this step pretty easy and safe too.
The next step was to cut the mortises in to the underside of the table top board with a hand held router. As the board was not square and the ends not parallel I marked the first set of leg mortises parallel to one end and the other set parallel to the first ones, this would at least make all the legs square and parallel which would help with bottom shelves later on.
I had originally intended to cut the mortises using a chisel but after cutting part of one there was just too much movement due to the cracks throughout the board which created quite a bit of breakout, so i moved to using the router instead. This did mean that the width of the mortises was set to the width of the chisel so I would have to route in two passes as my chisel was wider than my straight router bit. I used a clamp as a straight edge for my router to follow and marked the position of the base for the start and end points of each slot. For each slot I only cut around 3-5mm depth at a time so to not stress the router bit, each slot was finished to around 25mm deep, I then cut the ends square with a mortise chisel.
Next step was to cut the tenons to the top of the legs. I used my router now mounted in to a table with a fence set to cut the very end of the board to set the bit height correctly. To do this I set the height to less than it needed to be and cut both sides of the board, tested the final width in the mortise and gradually increased the height until the tenon gave a tight fit. Once the height was set it was just a case of cutting the rest of the tenon by adjusting the fence to the correct position to give me a 25mm deep tenon.
As I was using a through mortise and tenon for the shelves I cut a slot 100mm by 25mm around 300mm up from the bottom of the legs. I used the same router and chisel technique as I did for table top but went all the way through. Just make sure you have a waste piece underneath, I used a thin bit of ply, maybe too thin as I did go a little deep for one slot and routed a bit of my workbench!
Step 2: Table Top
As the top came as one large slab it inevitability had a few cracks and splits in that I needed to sort out. Having done a bit of research I ended up with two possible solutions, using epoxy to fill the cracks or using dovetail splines to prevent the cracks from enlarging. In the end I decided that I would use both, the splines for my main structural repair and some epoxy to level out/fill the cracks (I have kids and they tend to fill cracks up with food and small lego pieces). I also like to do new things and hadn't even come across dovetail splines before; plus I liked the look of them and enhanced the rustic look of the table.
A bandsaw would probably be the easiest and quickest way of cutting the splines as you need nice straight edges, but as I don't have one I used a saw and chisel. I determined the size of the splines by looking at my scrap wood, I found a length of square section walnut which looked like a good width and cut it in to 75mm lengths. I marked the half way point of the pieces and then drew on the lines from the corners to the centreline at an angle of 8 degrees using a dovetail marker. Having got the outline I sawed down the centreline to the end of the dovetails and then pared from the edges to the bottom of the saw cut with a chisel. As the splines were so thick I sawed each one in two.
I layed out the splines along the crack to find a good position for each of them and marked out each with a pencil followed by scoring the lines with a knife. The knife lines will give a nice accurate guide for the chisel later on. I also marked the top of the spline and above the outline so I didn't got the orientation mixed up. Most of the spline hole was removed with a router, just plunging lots of holes one after another, which gave my hole a good flat base. I then removed the rest of the wood with a chisel using the scored line as a guide. The trick is too make the hole slightly undersized and gradually increase the size constantly checking the fit. My first one was okay but my second and third were much better, I was pleased anyway as it was the first time I had made them.
After I had the splines completed I filled the major cracks in with a two part epoxy adhesive, dripping it in with a nail as to not make too much mess. Before it cured completely I removed a large part of the overspill with a chisel followed by sanding once it had set solid. The end result wasn't too bad, I did have a large hole to fill adjacent to the end spline when a chunk of wood popped out when I was chiselling and the epoxy took on a green colour, unusual, but I can live with it.
The top just needed to be sanded and finished, so I used a random orbital sander with 80 grit followed by 120, 180, 240 and 320 grits to get a nice smooth finish. I used two coats of Liberon Black Bison Wax to finish the majority of the top and some danish oil to finish the bark bits that weren't loose and looked like they might not fall off, here's hoping anyway.
Step 3: Shelves
Having taken care of the legs next came the shelves. I had bought a 2050mm long natural edge board which would be just long enough for a shelf for each set of legs. I cut the board in two lengths of 950mm each (the same length as my top) with a hand saw which left me with a piece around 150mm long which would do for the pegs.
As the boards are natural edged you have to be a little carefull marking out the tenons as they will not be central to board. I layed the shelf board on the underside of the top and positioned it how I wanted it, I then inserted one of the legs in to the top so I could transfer the position of the leg slot on to the shelf board. I then cut the shoulders off the end of the board to make a 100mm wide and 75mm long tenon, giving me around 50mm beyond the outside face of the leg. Having cut one side I put the shelf through the leg and marked out the opposite tenon using the other leg as a guide. It was just a matter of cutting and a bit of fine tuning, followed by the other shelf.
Step 4: Cut Through Mortises in Wrong Place First
OK so the main photos are of the steps to make the through mortises. Unfortunately I marked the holes out in the same position as the legs and did not realise until I had cut all four holes and put the legs and shelves together, so I have left the photos for these as they show the steps I used to make the holes. After doing this wrong I filled the holes with wood and recut them the correct place.
My first step was to cut the pegs which I made out of a left over section from one of the boards. I marked a line on my crosscut sled to give me a good angle and used this as a reference point for all my pegs for a bit of consistency. I determined how far down I wanted the pegs to lie and marked the top and bottom of the shelves on the pegs, giving me the top and bottom dimensions of the mortise.
After marking the top of the mortise on the board I marked another line a few millimetres in from that so I could use a router to remove most of the bulk from the vertical section of the hole. To form the angled part of the mortise I cut an additional piece of wood to the same angle as the pegs and used this as a guide. I used a mortise chisel to cut this angle and to clean up the rest of the sides.
Step 5: Assemble
Having corrected my mortises I only needed to sand and wax as I did for the top. Once the I had completed the finish I dry fit all of the table and was pretty happy with the outcome so took apart, applied glue took the leg/top joint and fit it all back together.
After a couple of days one of my boys spilled a little water on the top and it marked it somewhat so i guess the wax finish is not particularly suitable or I've not put enough on? So I am now thinking of removing the wax finish and apply something else instead. Any suggestions are welcome. I am looking at keeping the wood as natural as possible, I have some danish oil and some finishing oil so one of them might do.
All in all I am happy with my first attempt at a table, and although there are a few things I would change/do better/do differently, I guess this is how we learn and improve
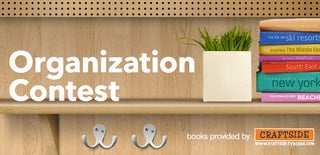
Participated in the
Organization Contest