Introduction: CNC Laser Cut Crawling Robot 6 Bar Mechanism UW Platteville
In this Instructable, we will show you how we made a crawling robot using a 6 bar mechanism and CNC laser cutting. This project was inspired by our Mechanisms and Machines class at UW Platteville, where we learned about different types of bar mechanisms and how they can be used to create various motions. We aimed to make a robot that could mimic the crawling motion of a bug using a single power source and basic bar mechanisms. We hope that by following the steps on how we made our 6-bar crawling robot you can more easily make your own!
Supplies
To complete this amazing project you will need everyday craft tools and the following:
- A 6V DC motor
- A battery and a switch
- Wood bars of different lengths and angles
- Metal bars of different lengths and angles
- Screws, nuts, washers, and spacers of different sizes
- A set screw for the motor shaft
- Hot glue
- Rubber bands
- Access to a CNC laser cutter
- Access to a 3D printer
- Fusion 360 software
- Access to Excel or another sheets software
Step 1: Research 4 and 6 Bar Mechanisms
You will need to know what you are working with before we start making. Before we started designing our robot, we did some research on 4 and 6 bar mechanisms to understand how they work. A 4-bar mechanism is the simplest closed-chain movable linkage, consisting of four links connected by four joints. A 6-bar mechanism is a more complex linkage, consisting of six links and seven joints. There are different types of 4 and 6 bar mechanisms, depending on the configurations of the joints and the links.
Some of the things we learned from our research are:
- A 4-bar mechanism can have different types of motion, such as crank-rocker, double-crank, double-rocker, parallelogram, and trapezium.
- A 6-bar mechanism can have different topologies, such as Watt and Stephenson. A Watt topology has two 4 bar loops, while a Stephenson topology has one 4 bar loop and one 5 bar loop.
- A 6-bar mechanism can have more degrees of freedom than a 4-bar mechanism, meaning it can have more possible motions and configurations.
- A 6-bar mechanism can also have more complex and interesting coupler curves, which are the paths traced by the points on the coupler link.
We decided to use a 6-bar mechanism for our robot, because we thought it represents the crawling motion the best. We also liked the idea of using two 4 bar mechanisms joined by a coupler, because it seemed simpler and more intuitive than using a 5-bar loop.
In making your crawling robot, you can use any number of 4 or 6 bar mechanisms, but a quick return 4-bar mechanism is the easiest option that still mimics a crawling motion.
Step 2: Design the 6 Bar Mechanism
After we decided on using a 6-bar mechanism, we started sketching the mechanism in Fusion 360. We used the dimensions of the 4-bar mechanisms that we learned in class, and modified them to fit our design. We also made sure that the mechanism had a single degree of freedom, meaning it could only move in one way.
We settled on a 6-bar mechanism that was joined on the crank of two 4-bar mechanisms. This design, we felt, best resembled the crawling motion because of the two output bars mimicked the feet best. The input link was connected to a motor, which provided the power source for the robot. The output links were connected to the ratcheting wheels, which were made ensure movement in only one direction. The coupler link was connected to the body, which was 3D printed in one big piece to provide support and structure.
We recommend that you also make a sketch in Fusion 360 to understand the characteristics and motion of the mechanism that you decide on. By tweaking the values of the lengths of the bars you are able to attain a variety of unique motions.
Step 3: Make the Parts in Fusion 360
After we sketched the main body part in Solidworks, as was the requirement for the course, we made the rest of the parts in Fusion 360 because that is the software I am most familiar with. Fusion 360 is a cloud-based 3D modeling software that allows us to create and modify 3D designs, as well as prepare them for CNC laser cutting and 3D printing. It is free under the educational license and it is a very powerful and useful tool to learn as an engineer.
We used Fusion 360 to design the following parts:
- The ratcheting mechanism, which were 3D printed and had a curved shape to fit the output links and provide traction.
- The motor mount, which was 3D printed and had a hole to fit the motor and a slot to fit the drive shaft which powered the input link.
- The links, which was made of wood and had holes to fit the coupler link and the motor mount.
- The drive gears, which were 3D printed in PLA to power the drive shaft.
We cannot highly recommend enough the importance of designing tolerances in your robot! If you are not familiar with the term “Tolerance,” there are many great resources online that can give an exact definition and why it is so important. A brief short cut recommendation for tolerance, is if you are confused with tolerances to design 2 or 3 millimeters spacing between each part. This will help you so much when you move to the assembly step.
Step 4: CNC Laser Cut and 3D Print the Parts
After we made the parts in Fusion 360, we exported the bars as DXF files for CNC laser cutting and STL files for 3D printing. CNC stands for computer numerical control, which means that the machine follows a set of instructions from a computer to perform a specific task. This tasks is usually a subtractive method of manufacturing, or a method that cuts material away in the process. Laser cutting is a CNC subtractive process that uses a focused laser beam to cut or engrave materials with high precision and accuracy. 3D printing takes this same technology in CNC machinery but the 3D printers build upon the material it makes, thus it is an additive manufacturing method
We used our college’s CNC laser cutter to cut the bars of the both sides of the mechanism, the motor mount, the body, and the eyes. We used wood for the bars, the motor mount, and the body, and acrylic for the eyes. We chose these materials because they are easy to cut, lightweight, and durable.
We also used our college’s 3D printer to print the body, gears, motor mount, and ratchet mechanism. We chose PLA for these prints because it the most abundant material and it is easy to print with. We also chose 3D printing because it allows us to create complex shapes that are difficult to cut with a laser cutter.
We highly encourage any maker attempting this project to expect that parts will not fit entirely
Step 5: Assemble the Robot
After we CNC laser cut and 3D printed the parts, we assembled the robot using screws, nuts, washers, and lots of hot glue. We followed these steps to assemble the robot:
- We attached the motor to the motor mount using screws and nuts.
- We attached the input link to the motor shaft using hot glue. Later we machined a shaft key because hot glue is not sufficient.
- We attached the crank link to the input link using a little shaft, a washer, and hot glue.
- We attached the coupler link to the crank link and the rocker link using a little shaft, a washer, and hot glue.
- We attached the output link to the rocker link and the other output link using a little shaft, a washer, and hot glue.
- We attached the other rocker link to the output link and the other coupler link using a little shaft, a washer, and hot glue.
- We attached the other crank link to the coupler link and the other input link using little shaft, a washer, and hot glue.
- We attached the other input link to the other motor mount using little shaft, a washer, and hot glue.
- We attached the motor mount to the body using a designed press fit and hot glue.
- We attached the wheels to the output links using a long shaft, many washers, and hot glue.
- We attached the ratchet mechanism to the shaft using hot glue.
With this we had a very awesome crawling robot! But it fell apart immediately after we put it together. We recommend to start to feel comfortable taking your machine a part and putting back together again a great number of times. This is often required when making a new robot design for the first time.
Step 6: Test the Robot
After we assembled the robot, we tested it by connecting the motor to a battery and a switch. We observed how the robot moved and how the 6 bar mechanism worked. We also measured the speed and the distance of the robot.
We found that the robot did not work as expected at first, because we did not consider the tolerances, the elastic deformation of the materials, and the difficulty of assembly. We learned that these factors can affect the performance and the accuracy of the mechanism, and that we need to account for them in our design and fabrication.
We made some adjustments and improvements to our robot, such as:
- We added many more spacers and washers to reduce the friction and the gaps between the links.
- We replaced the drive shaft with a shaft that we keyed ourselves to increase the strength of the connection of the gears to the motor.
- We adjusted the angles and the lengths of the links to optimize the crawling motion and the coupler curve.
- We added some rubber bands to the wheels to increase traction.
After we made these changes, we tested the robot again and found that it worked much better. It was able to crawl smoothly and steadily on different surfaces, such as thin carpet and tile. It also had a more realistic and fluid motion, resembling a bug.
We measured the speed and the distance of the robot using a tap measure and a ruler. We found that the robot could crawl 10 feet in 1 minute and 46.03 seconds. Which means it traveled an average of approximately 4.9 miles per hour.
We recommend you go wild in assembling your robot, maybe give it googly eyes for it to see better 😊. Or even try a bug shell, make your machine unique and yours!
Step 7: Reflect on the Project
After we analyzed the data and completed the project, we reflected on what we did and what we learned. We also thought about what we would do differently and what we would improve in the future. Here are some of our reflections:
- We enjoyed working on this project, because it was fun and challenging. We learned a lot about 4 and 6 bar mechanisms, CNC laser cutting, 3D printing, and Fusion 360. We also learned a lot about the design and fabrication process, such as sketching, modeling, cutting, printing, assembling, testing, tolerances, measuring, and analyzing.
- We faced some difficulties and challenges in this project, such as choosing the right mechanism, finding the right materials, adjusting the tolerances, fixing the deformation, and optimizing the motion. We overcame these challenges by doing research, making changes, and trying different solutions through rapid prototyping.
- We would change some aspects of our project, such as the method we used to attach our CNC laser cut bars to our motor. We used hot glue, which was not very secure and stable. We shifted to a keyed drive shaft, which was more reliable and precise.
This is what we completed for this project, but you do not have to stop there. You could also add some sensors and a microcontroller to your robot, which would allow you to control and program the robot remotely. Let your imagination run wild!
In this Instructable, we showed you how we made a CNC laser cut crawling robot using a 6-bar mechanism. We hope you enjoyed reading our project and learned something new. We also hope you are inspired to make your own robot using bar mechanisms and CNC laser cutting. Thank you for your attention and happy making!
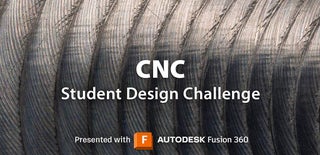
Participated in the
CNC Student Design Challenge