Introduction: Cardboard Mini Locker
I teach high school pre-engineering and manufacturing classes (i.e. shop class). At the end of my Intro to Manufacturing 1 class the students are assigned a design project in which they have to design a product that can be assembled without the use of any mechanical or adhesive fastening. After the students choose an idea to work on they must sketch out their plans, model the parts using a CAD software, create a mock-up out of cardboard using our laser engraver, and finally produce the final product out of plywood or MDF using our CNC router. The initial step of thinking of an idea that they want to build is the hardest part for many of my students. I am creating this Instructable as an example for my students to showcase the steps of our project and what can be created with the amazing technology and equipment that they have available to them at our school.
Students at this point in my class will have prior knowledge of how to use Autodesk Inventor, how to create oblique, isometric and multi-view drawings, and will have used our laser engraver for a smaller project.
Skills used and developed during project
- Problem Solving
- Measurement
- Sketching
- CAD
- Laser Engraver operation
Side note: Because I am writing this targeting my students there will be steps or parts of steps that you can skip if you are just doing this project for yourself. For example, my students only have 15-ish class periods to complete this entire project, while also working on other smaller assignments, so I make them have multiple ideas to work off of in case their first idea doesn't work or is too time consuming.
Step 1: Equipment and Material List
-Pencil and Paper
-Computer/Laptop
-CAD software (We use Autodesk Inventor)
-Cardboard
-Dial Caliper
-Laser Engraver
Step 2: Brainstorming/Research and Concept Sketches
Our goal is to come up with three or four ideas for products that you want to build. The sky is the limit at this point! Do not get hung up on how difficult you think your idea will be to accomplish, how you will design the product to fit together, or if an idea has been done before. We just want to get ideas down on paper first. If you're having difficulty coming up with any ideas at all here are a few things for you to think about to hopefully help get those creative juices flowing:
1. What do you do for fun? What are your hobbies?
-Can you think of anything to build related to that?
2. Is there someone you could make something for?
-A parent/guardian, friend, girlfriend/boyfriend, grandparent, teacher/mentor, or someone in need?
3. Is there something that bugs you in your daily life that you could build something to help with that?
-No place to hang your hats? Video game controllers always falling off the coffee table? Your dog is to old to jump up onto your couch to snuggle?!
4. If the questions above did not help search the internet for keywords/phrases like "CNC router projects", "flat pack furniture", or "3D buildable puzzle".
Once you find an idea you like create a quick concept sketch of that product and give the overall dimensions of height, width, and depth you would like the final product to be. Your goal should be to have three to four concept sketches with overall dimensions. We want to have more than one idea to work with in case we can't figure out how to design our original idea in a way to make it work in the time constraints of our project.
You can see my three concept sketches above. I chose the Mini-Locker because I had one as a kid and thought it would be fun to make and display on my desk!
Step 3: Sketch Individual Components
Great! You have chosen an idea and are ready to start planning your product. You need to start thinking of how this idea can actually be made. Below are some questions to think about as you begin this step:
-How many parts will you need?
-What type of joint are you going to use to hold your product together?
-Research wood joints if you are unsure
-Box Joints
-Mortise and tenon
-Dove tails
-etc.
-What thickness of material will you need and use?
-Use a dial caliper to measure the thickness of the cardboard you will be using.
After you have answered those questions start creating multi-view sketches for each of your parts. Remember if you need two of the exact same part for your final product only create one sketch for that part.. The sketches should be dimensioned enough that you can create accurate 3D models for each part in the next step. These multi-view sketches do not have to be perfect but they should be neat enough to use as a guide in our next step. I highly recommend using a straight edge when working on your sketches!
Above you can see the dimensioned sketches I created for each part of my Mini-Locker.
Step 4: Create Model in CAD Software
Idea chosen! Sketched plans made! Now it is time to create each one of your parts using CAD software. From these 3D models we will export the faces of each part so that we can then cut them out of cardboard to make our mock-up. I used Autodesk Inventor to create the six parts for the Mini-Locker. Things to keep in mind when you are working on your 3D Models:
-Keep it simple, don't try to figure out how to use some obscure tool/command inside the software stick with what you already know. Remember we have time constraints with this project.
-Pattern repeated elements instead of drawing each one.
-The thickness of your material will play a factor in your design.
Above you can see some pictures of my Autodesk Inventor models. I assembled the parts together to test to see if my joints would align. As you will see in Step 6 I did not get that portion of my models right on the first attempt.
Step 5: Laser Cut Parts
Warning: Lots of steps ahead!
To use our 3D models of each part from Inventor we need to export them to a usable file format for our laser engraver. We are going to export our files to the .dxf format. To do this follow the steps below or view the steps in the images above.
1. With your part file open in Inventor move your cursor over the face of the part that needs to be cut out and left click to select that face. The face should highlight a red or blue color.
2. Now, right click on that face and choose the "Export Face As" option
3. In the "Save Copy As" window that opens, type a name for your part in the "File Name" text box and make sure the file type is set as .dxf in the "Save as type:" text box.
4. Click save
5. Repeat steps 1 through 4 until all of your parts are saved as .dxf files
Now that we have our parts as .dxf files we can import them into our software for our laser engraver which is called CorelDraw. To accomplish this follow the steps below or view the steps int he images above.
1. Open a new file in CorelDraw
2. Right Click on the screen and select the "Import" option from the menu that opens.
3. In the "Import" window that opens select one of your .dxf files to import.
4. After you select your .dxf file an "Import AutoCAD File" window will open. Make sure the scaling is set to 1:1 and then select the "Ok" button.
5. Finally after clicking the "Ok" button simply click the "Enter" key on your keyboard to import your part into the center of our laser engravers cutting area work space.
Now onto the fun part! Follow the steps below or in the images above to use the laser engraver to cut your parts out of cardboard.
1. Repeat the steps to import your .dxf files until the cut area of your laser engraver is full or until you have cut out all of your parts.
2. We need our parts to be cut lines which means they need to be red. In the upper right side of your screen there should be three squares of color (Black, Red, and Blue). Highlight all of the lines of the parts that you want to cut and then move your cursor over the red square and right click.
3. Once all of your lines are red we are ready to cut. Towards the top of your screen click on the print icon.
4. In the "Print" window that opens select the "Preferences" button which will allow us to select the material we are working with.
5. In the Material Database window that opens. Select the Mat Board (ours does not have cardboard in the library) material and then enter your material thickness in the bottom left of the window. After you have done that select the "Ok" button on your Material Database window and then again on your Print window.
6. Finally we can open our laser engraver command window. Our parts should show on the screen and be ready to by laser cut. Turn on the laser engraver and wait for the Play button to turn green. Turn on your fume extractor and watch your parts be cut.
Side Note: Don't be too alarmed if your cardboard bursts into flames. It happens occasionally when we cut too close to the edge of the cardboard. As long as you have your fume extractor on it will stay contained. If needed a wet towel can be used to stamp out the embers to return things to normal.
Step 6: Test Mock-up and Redesign
Attempt 1 (Red and Gold not assembled)
As you can see in the images my first attempt (The image of the pieces not assembled that are gold and red) that my locker did not go as planned! I initially thought our scrap cardboard was close to 1/8" thickness when actually the cardboard I grabbed was closer to 1/4" thick. I made the mistake of cutting twice and measuring once but that is why we test our designs with cardboard first.
Attempt 2 (Green and Red version)
The second attempt went much better as you can see from the completed locker that is green and red in the image above. I was using scrap cardboard we had spray painted on top of which gave the mock-ups a neat look.
Attempt 3 (Red and gold assembled version with handle)
I wanted my locker door to actually be attached and open somewhat. I redesigned a third time and attached the door to the front part of the locker and changed the square hole to something different that I could attach a simple handle as well. (If I was going to continue on to make this product out of plywood I would find a different way to attach the door.)
Not all of the parts were perfectly cut out. In trying to place as many parts as I could on a sheet of cardboard certain pieces of my parts were cut off or made too short. If that happens with yours as well don't worry as we will fix that in the next step.
Step 7: Assemble Final Product (or Final Mock Up)
Time to assemble the final product or the final mock up if you want to continue on to build a more sturdier version! This time when you laser cut your parts you need to make sure that they all get cut out completely. Do not try to cram all of your parts on one sheet of cardboard unless you can safely do so without accidentally cutting off connecting points.
You can see my finished version of my Mini-Locker in the pictures above.
I've included the .dxf files if you would just like to make one of these Mini-Lockers yourself. I believe the spacing for the joints on those is around 1/4". I've also included the .ipt files if you would like to edit this model in a 3D format for your own needs.
Step 8: Display (or Create Final Product Out of Wood!)
Display your creation and take pride in the quality of your work! You just learned, used, and further developed skills that allowed you to think of an idea and work your way through the process of actually making that idea come to life!
If you do go on to create a sturdier version out another material I recommend keeping your cardboard version and displaying them side by side. People often like seeing the steps in your process and it gives you an excuse to brag about the sweet technical know-how skills you have!
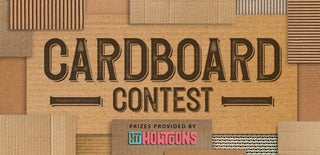
Participated in the
Cardboard Contest 2017