Introduction: Chainmail Rings the Easy Way
Before I say anything else I would like to apologies for the extremely bad video quality. The reason for the bad quality is the fact that the videos was made back in 2002 (a time where recording digital video was still a new thing and most camera was only able to record 30 sec at a time). At that time I was into making chainmail and plate armour and thought that I would make a tutorial. The tutorial was never made but when I found this page and saw some of the other chainmail tutorials I thought that I would share some of my techniques.
A chainmail has a lot of rings and therefore you want to spend the smallest amount of time on each ring.
Just to give you a reference I made a chainmail with 13000 rings. The assembly time was 24 hours which is equal to 6,6 sec per ring. The preparation of the rings is not a part of the 24 hours. I did not time how long this took.
Also note that the wire I used was galvanised wire fence with a diameter of 2mm and 1,6mm. I have never tried anything else so I can not guarantee that it will work with other kinds of wire.
Step 1: Making the Coils
When making coils almost all tutorials suggest to make some kind of winding stand and then control the wire with one hand while the other hand turns the rod either manually or with a drill. This way is slow and if you try to do it fast you will either burn your hand or destroy the glove your are wearing. Also it is difficult to control the wire.
I used this method for a while but then came up with something much much better but still very simple. It is so simple that the pictures really don't need any explanation. I cut the wire into length before winding it but if you are able to have the wire on some kind of spool it would be even better.
Step 2: Peparing Rings
Before cutting the rings you have to pull the coil so that the finished ring is open and ready to go.
To cut the rings I use a knipex mini bolt cutters like this one: Knipex bolt cutters
Step 3: Closing and Putting Rings Together
I will not go into detail about how to make the 4 in 1 pattern but I will talk about how I think you should connect and close them.
After you have made the first 3 rows you then make one row at a time like I show in the video. This way you only have to connect the new ring with two rings at a time. In the video I only have a small section of mail. You should be working on a piece at least 50 cm wide.
And now to the real revolution - The way you close the rings. Some people suggest to hold the ring with two pliers - one on each side of the opening and then force the two ends together. This method sucks for several reasons all related to the force required.
- Your hands and fingers will be abused and you will get blisters.
- If the pliers accidentally slip you will move the rings you already put together having to realign them before you can continue.
The way you should do it is like I do it in the video. You hold the ring with one pliers and with the other you press the two ends together and then align them by giving the pliers a small twist.
Step 4: Pliers
The pliers I use are simple pliers found in any hardware store.
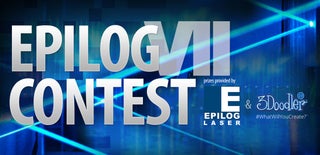
Participated in the
Epilog Contest VII